Introduction: House Metalwork Main Door
I have DIY concept, as a way of being all the time, in anything. I am an old subscriber of this website as others, never ever did an instructable, but when i saw this metal contest it gave me a click - why not to do it? One of the last Projects I did was fun and it held me. Finally because I believe the problem it motivated me to do it, could be shared for many of you, why not ? Would like also to say that the door was made not to be an instructable, so it can be not so well documented in photos, but I will try to complement with drawings. Finally as English is not my main language, sorry for any language kicks.
In my house for many years I had a tipish wood old style main door, it was a nice door. Issue was that, through the years it required to many maintenance and if in the summer, door was dry and opening smoothly, on winter time, door grows up with the humidity and rain and some times I was "looking" to my self kicking the door to open. Because through the seasons was increasing and decreasing size each year maintnance was harder. This spring I decide that it was enough.
Did a research and asked for several quotations and end up realizing that from pvc to alluminium, all most everything is standarized style, looking the same, i could chose the door frame similar in basicaly all the materials and then I could choose a panel for the door, with more glass , less glass, having just very few italian supliers working the panel area. Second research was to draw the door and ask for quotations, overall on the first choise price was between 2500€-5000€, second was going high behond the 5000€.
I decided Bruno: “DO IT YOURSELF”, and started projecting a new door.
Remark: some times you may think that requesting quotations, digging on the diferent choises/ solutions can be a waste of time, my experience is that the exchange of knowlegment between a supplier and the buyer that wants to know more then the information presented on a brochure can be so, so reach, that when I finished this step with all the information collected, it gave me a base to start this project believing much more in the final result.
Step 1: Goals & Cost
GOALS:
- Final product could not sensitive to the weather cast, ending up with the door kicks to open;
- Because we didn't had on the old door a mail box, goal was to make a embebed mail box on the door frame;
- Optimize materials in stock, reducing the much possible the diferente iron tube shapes/sizes;
- Continue to have a natural light getting inside throught the door;
- Robust and safe; Style, mixing a "clean" contemporany and old fashion door look;
- With the money savings, doing the door myself, I would like also to solve a problem that we have in house that is never know where the door keys are, so I installed a access control system.
FINAL COST
Door total cost was 600€-700€
Access control system – 70€?
Step 2: Drawing and Projecting the Door
Measurement collection is a crucial point, in old house constructions the frames and measurements are not always the same, I chose to consider the smaller measures and work on them giving a 1cm margin of error on the measurement.
In order to prevent theft through the slot, I chose to make a Z-joint with a 6mm spacing between fixed and movable element. In the fixed part all around that spacing I applied a plastic profile that would serve insulation/ seal, stop/ cushion and finally prevent any object from entering the slot and can reach the door latch.
All elements where glass exists, in order to allow maintenance, I used a removable structure that easily allows them to remove the glasses and or clean.
All glasses used are double glazing, allowing for greater thermal insulation.
In order to get an old dash for the door I used an aluminum cast grid instead of iron cast to don't make the door heavier.
Step 3: Materials Used
Iron
Iron Tube
6 Centimeters round tube for the handle2x6 Centimeters
1,5x3 Centimeters
1,5x2 Centimeters
2x2 Centimeters
Iron Bar
1x1 Centimeters
1mm iron plate
Aluminium - Used a Aluminium Cast panel 1meter x 62 centimeters double-sided or double face, today I would have used a single-sided panel, since the interior of the house, by using frosted glass, we does not take advantage of the interior face/side, simultaneously would make the grid thinner and lighter.
Supplier Link - Alluminium Cast Supplier
Glass
Double glazing, filled with argon gas according to the necessary measures
Hardware
All the hardware for the door, cylinder, electric door lock, ...
Step 4: Hands on the Job - Frame
I started by welding the structure, to minimize bends I made welders of about 3-4 centimeters with intervals of about 40 centimeters and crossed or alternating welding between the front and back face, would allow a much smaller bending, robust and a work with much cleaner edges.
In the cast aluminum panel, I split it into three equal parts (two parts for the movable element and one for the fixed part of the door) so as to join the two aluminum elements I made a low temperature aluminum brazing here you will easily find a good tutorial, like This. Finish all to minimize welding aluminium joints. Lastly,In the resulting parts, I applied a U-rail all around, shaping a rectangle.
Attachments
Step 5: Applying the Sheet Metal to the Structure
The 1 mm metal plate was not welded to the structure, but was glued, this is a technique that I learned from contact with locksmiths years ago and which I tried to learn more. This bonding process, compared to (thin) sheet welding, has the following advantages:
- being an easy technique in relation to the welding process which in the thin sheet is thorough and requires a lot of technique and equipment knowledge;
- Leave no mark on the plate;
- It is a clean process
For this I used a high quality single component adhesive sealant with high adhesive strength and initial tack. It is based on MS-Polymer®, chemically neutral and fully elastic. Sealant aplied is from Soudal but any adhesive based on MS-Polymer will work - Soudaseal HT - Technical Data.
Workflow:
Thoroughly clean the surface of the elements to be glued with thinner;
Finish with brushing with a wire brush (this is very important for good adhesion to the surface) brushing should be done on both parts to bond the plate and structure;
Apply double-sided adhesive tape throughout the structure and whenever the structure to be bonded allows not only to hold both parts during the curing process but also to ensure that the thickness of the adhesive to be applied is not thin. more. Never use files or angle grinder to clean surfaces and never, never use clamps to glue the parts;
- wait 24h for the curing process to end;
To save on the cost of sheet metal instead of using several plates and having a lot of waste, I opted, in the narrowest parts, to apply iron plate strips to the width instead of single plate (it becomes more evident the savings in the upper window, where I had to mend all joints with two components mastik for metalwork.
In the application of sheet metal and because I did not know the bend on the struture , i rather prefer to have a margin of error of a few millimeters more on final measurements. At the end it was a harder work on the finishing of the edges and aligning joints, but endlessly, was without a doubt the best solution.
For the door Handle I used a round tube cutted in 45º and welded, I used some plate to weld and fill the holes in the ends. To finish I drilled and made a thread to apply threaded baron that went through the door and was fixed inside the door. The handle is an easily removable element if you need to touch up the paint as it is the most used area.
The slots and holes for applying electric locks and locks, as for the mail box folding struture because they are difficult to explain, I will try to complement this subjects with good photographic documentation in the last step.
Step 6: Ending the Iron Work & Painting
Opening the holes for the glass it was made with a angle grinder.
In this last step, the most laborious was undoubtedly to rectify the joints / spacings between the moving and the fixed part, so that they were equal and parallel.
All grooves/holes for application of glass and grilles were made before gluing.
In Painting it was applied normal procedure a synthetic primer and later synthetic ink. In my case I chose to place the two faces of the door with different colors, gray forge on the outside and inside to reflect more light a matt white ink.
Step 7: Photos, Details of the Final Result
I was not sure but decided to post more photos of the final job, it can clarify the steps over the workflow
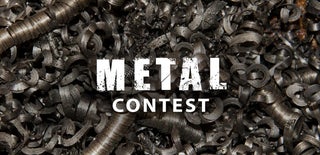
Participated in the
Metal Contest