Introduction: How NOT to Make a River Table (For Your Chair!)
Everybody loves epoxy river tables, right?! We tried to make one and it turns out we have no idea what we're doing...but even though things kept going wrong at almost every step we managed to fight to the end and it came out AWESOME. :)
Our projects tend to start as one idea and end up becoming something slightly different by the time we're done...this project is a great example of that. So, this is how NOT to build a river table!
We recommend watching the video above and following along with the written steps!
Also, please let us know what you might have done differently in the comments. :)
Step 1: Getting Started With Our Material: Australian Red Cedar
To make the "river" we need a live edge, which is when the edge of a piece of wood still has it's natural shape and hasn't been cut off. So we picked up a piece of Australian Red Cedar with an awesome live edge. It's a hard-wood in the mahogany family so it has a really nice deep red heartwood and bright yellow sapwood.
Although it's pretty, we had some big issues with wood movement due to it likely being dried too quickly...but we'll get to that later.
We only needed the live-edge for this project and not the entire board so we marked a line using a straight-edge of where to cut. We weren't 100% sure how much material we needed at this point because too much planning isn't always our thing, so we left plenty of extra room.
Next, we ripped off the live-edge at the band-saw. If you look at the back of the board in the band-saw picture, you can see it flexed open about 1/2" as we ripped it. 1/2" of flex over 48" is MASSIVE. This is a great example of why doing initial rips at the band-saw is a smart idea, if you have the means to. If this had been done at the table-saw, all of that flex would be up against the blade and it creates a potentially dangerous situation.
The flex is (typically) due to something called "case hardening", which basically means the board wasn't dried in the best way for woodworking. When you rip it down the middle, all of the tension is released and it turns your flat board into a potato chip.
Lastly, we're going to make the "river" from the live-edges of the two halves put together so we cross-cut it in half at the bench. You could use any saw for this, just need to turn one board into two boards.
Tip: If you have the means to, using a band-saw for your rough "rips" is a safer option than using a table saw. Not to mention the kerf of the blade is smaller so you're saving more material! We still use the table saw later when cutting to final size, but rough ripping is always done on the band saw.
Step 2: Milling and Prepping the Wood
Next, we milled the wood to get it flat and straight. In the several minutes between ripping the live-edge off and moving to the jointer, the board had already moved a LOT due to all the released tension. It was relatively straight when we bought it and turned into a potato chip shape pretty quick once we began milling.
It took a lot more passes than normal at the jointer to get it flat, which resulted in the boards being quite a bit thinner than anticipated. This wood movement issue would continue to mess with us throughout the whole project...
After fighting with it for a bit, we got things looking nice and flat and straight. The ideal thing would have been to let it sit a few days (or longer) to finish it's initial movement and then repeat the milling process. This gives the wood enough time to come into equilibrium before actually starting the project. This way it would have moved a lot less later on. Hindsight, etc. etc.
A quick pass at the table-saw took care of the extra material we didn't need. Since this is a final size and we'd already released the initial tensions over at the band-saw, it was fine to make the cuts on the table-saw. That being said, you could still easily do it on a band-saw or circular-saw since it isn't critical that it's straight for this project.
Tip: Wood moves! Even long after it's been "dry", any cutting or milling can expose moisture to the wood and release internal tension. For best results, when you bring home a new piece of wood, give it some time to acclimate to your shop environment. If you need to mill it and remove a lot of material, the best way to do that is to mill it, let it rest a few days, then mill it some more, to let it acclimate slowly. Otherwise, it can continue to move throughout your project and mess things up.
Step 3: Finalizing Our 'River Banks'
Jaimie spent a little time trying to find the ideal river shape and then she marked out our final length. This is another thing that we could have probably planned better to save a little material but it wasn't a big deal.
We cross-cut the pieces to final length at the table-saw. This would be easy enough to cut at a miter saw or with a circular saw as well. This is just the fastest way for us to do it. We wanted the ends to be square to the back edge which would make it easier when we build the form for pouring the epoxy.
The live edge was free of bark but still had a lot of fibrous material on it so we used 'dragon skin' which is like a metal sandpaper to scrub it off. Worked perfectly. Jaimie used to use the dragon skin stuff a lot when she worked in Visual FX and we had some from her days of building monsters and costumes and stuff.
After what seemed like a battle...we had a couple of really nice live-edges!
Tip: If you're not much of a planner, you can always expect to use a little extra material to account for inevitable changes as you dial in your design. Assume there will be mistakes, rewrites, do-overs, and other changes, so make sure to leave yourself enough material for stuff like that!
Step 4: Building the Form and 'Damming the River'
Next up was building the form for the epoxy pour. We decided to use MDF since we had a bunch on hand. We ripped and cut a few pieces down to size.
The purpose of the form is to hold the two river pieces inside and create a space between the live edges that the epoxy will pour into. That meant it had to fit the wood pieces as perfectly as possible to prevent leaks.
We covered the interior faces of the form in packing tape so the epoxy wouldn't stick to it. Packing tape is definitely not a good choice if you're trying to block up a crack or hole in the wood to hold the epoxy in, but it's good if you're just trying to prevent the epoxy from sticking to something else.
To hold the form together we used these Spax MDF screws. No pilot holes required and they hold the MDF good and tight. Also helpful because we could take it back apart later without issue.
The MDF form went together without any issues. Which was great. Because...finally something worked!
Tip: MDF doesn't hold together all that well with "normal" wood screws. If you're making something that you want to stay together but you won't be gluing, these MDF-specific screws work really well!
Step 5: Gluing the Boards Into the Form
The two pieces of wood were hot-glued inside the form on the bottom. This helps them stay put so they don't float up when the epoxy is poured in. This technique didn't work well enough...we still got some leakage underneath that caused a lot of problems later. If we did it again, we'd figure out a better way to hold them down, maybe some clamps?
Hot glue also helped to seal up the ends so epoxy didn't leak onto the outer edges of the boards, which did work.
To figure out how much epoxy we needed to mix, we took an average measurement of the width of the river across the entire length. We overcompensated for the size and ended up making way too much because math is hard...but much better to mix too much than not enough.
Tip: When you're doing an epoxy pour like this, keep your hot glue gun at the ready to spot check any leaks that might happen! You can quickly fill them with glue and stop a major leak.
Step 6: Mixing and Pouring the Epoxy Resin
Epoxy is a two-part mix that uses a Resin and a Hardener. After mixing them together for about 3 minutes in a mixing cup, we split the mix into two separate cups.
Each cup was mixed with a different color using ink dye we got that is specifically for dying resin. One of them we also mixed with some mother of pearl flakes. (Jaimie was super excited about the flakes, they looked awesome.)
The intention here was to mix the two colors during the pour and get a nice mixed effect.
The epoxy pour went really well, everything stayed in the form and it was looking good. The problem is that when we poured the two colors together they just instantly became one color and created no visual effect whatsoever.
Again, if we'd done some tests and planned better we probably could have figured that out ahead of time...
To try to make it look good again we added a bunch more ink dye to the top surface and then mixed it around in a pattern to try to recover.
It actually looked awesome when we left it - sadly it looked nothing like that after it cured.
Tip: Adding the ink dye after the fact did not work at all. Do not do this. :) It would have been better for us to add significantly more ink dye at the mixing stage to get better color, or using an opaque dye and not a transparent dye. Another great tip is to mix the ink dye with the resin before adding the hardener.
Step 7: Fixing Problems With the Epoxy River
When it was cured (~24 hours later) it looked totally different than how we left it. Almost all of the ink had pooled together near the surface and then moved to both of the sides. The mother of pearl flakes had all sank to the bottom and were flat on the surface of the bottom. On top of that, some of the epoxy leaked under the boards so the flakes were actually below the surface of the wood. (Gravity...) AND on top of all that, the wood had kept on moving and twisted back up after milling. The whole thing was totally out of flat again and wobbling all over the place. Not the greatest sequence of events.
With limited options that didn't involve starting over, I had the bright idea to run it through the planer to try and at least get some flat areas to work with. In doing that, the first pass sheered off all of the mother of pearl flakes on the bottom.
(Jaimie was SUPER happy about that. Not my best work.)
After a lot of nonsense, I ended up starting at 80 grit and sanding it all back to as flat as I could. In doing that we took of what was left of the flakes and a lot of the ink that was on the surface. What we ended up with was a turquoise-ish epoxy river. Not at all what we'd planned for but it still looked alright. We started at 80 and sanded up to 320 with the orbital sander.
In the end, we decided to flip it over and use what was originally going to be the bottom as the top, since the flakes were gone and it would hide the weird ink spots on the surface.
Tip: Sanding and polishing epoxy back to a pure, see-through gloss requires a LOT of effort. We purposely stopped at 320 grit because we liked the look. If you're going for a completely transparent look you'll need to wet sand and then use a wax polish....and expect to put in some work.
Step 8: Cutting the Miters for the Waterfall Effect
In a classic "frustrated woodworker" moment, instead of taking a deep breath and figuring out the right solution...we still tried to cut the miters on the table-saw even though the board wasn't perfectly flat. Of course, it moved during the cut and the miters got screwed up.
Two of the miters got cut this way and took a ton of cleanup by hand to be usable. Don't be like us.
For the other two, we have a cross-cut sled with a miter setup so we tried to see if that would help to keep the boards more aligned and it actually helped a lot. We should have just done that from the start. It wouldn't even have taken any more time, we just got into a hurried mood and it ended up costing us a lot of time.
Our first dry fit looked AWESOME but then Jaimie realized our design was flawed and we needed to change it again. On the inside of the chair, we'd forgotten to account for the inner side of the table hitting your leg. We decided to trim the interior side.
Tip: If you're trying to cut nice joinery, you'll have a much easier time working with flat material and not boards that are twisted or cupped. Because our board wasn't flat, there wasn't enough stability to keep it flat on the table while cutting the miters so it moved halfway through the cut, which resulted in a bad joint. Always try to get boards which are as flat and straight as possible to mitigate errors at this point in the process.
Step 9: The Glue Up! Blue Tape and Biscuits
We added biscuits to the miters to help hold them together. This took a little careful planning to make sure they weren't going to cut into the "river" but it went fine here.
The slots were a lot smaller than usual so we had to modify some biscuits to fit. We trimmed off the ends and then cut them in half.
The glue up was completely uneventful, boring, and entirely lacking any excitement. Perfect!
We used regular wood glue, applied it carefully to limit squeeze out, and did not apply any to the epoxy so it would stay (mostly) clear. Blue Tape was used to hold the miters tightly together.
Tip: Use a plastic straw to push through the interior corners and scoop up any glue squeeze out!
Step 10: Surface Prep and Finish
For surface preparation, we used a block plane to chamfer the outer edges. Nothing exciting happened here whatsoever. Nice! On the mitered corners, we used some high grit sandpaper to give it a very slight round so it wasn't sharp. We weren't confident the block plane would cut the epoxy here which is why we used sandpaper.
We raised the wood grain by spraying it with some water and then once it was dry we lightly sanded it one last time with 320-grit sandpaper. After that, we took some hand-plane shavings and rubbed them on the surface to burnish it, which gives us a really great surface ready for finish.
We used a Waterlox finish and applied 4 coats. This gives it a perfect luster and a nice, water-resistant finish so when our 1-year-old spills stuff all over it, it'll be fine.
Tip: Even if you don't like the aesthetic look of chamfered edges, sanding them or taking even a single swipe with a hand plane to 'break' the edges is a good idea. It helps break up the light which gives it a clean look but also the edges won't break off or be too sharp. If you do nothing, they're likely to break at some point. Even a tiny, tiny bit of chamfer is a good idea.
Step 11: The Final Results!
After some serious nonsense, a lot of frustration, and a huge learning curve with figuring out how epoxy resin works...we ended up with a pretty awesome little armchair river table. Not our cleanest or best work, for sure, but we're really happy with it!
Hopefully, this helps somebody out there and you can learn a thing or two from our mistakes and be inspired to try one yourself!
Want to watch the whole video? Check it out here: https://youtu.be/0JSa1SYu7S0
Thanks for reading! Want to see more of our stuff?
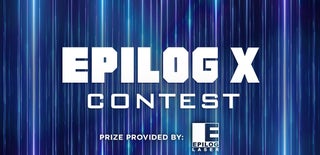
Participated in the
Epilog X Contest