Introduction: How to 3D Print NinjaFlex
This guide aims to highligh Ninjaflex and take you step by step through the decision making to printing using the filament. For novice, this is a great way to get into a new filament but to advance users it will all be very basic stuff and is not the best resource to troubleshoot print settings.
So, for all those who do not know what NinjaFlex is or have not really realize its potential, this guide will show you how! Ninjaflex is a brand sold by ninjatek (https://ninjatek.com/products/filaments/ninjaflex/) and is the most common elastic filament and a good entry level filament to try!
Before we go into settings, we have to make sure this is the right filament for your needed print!
Step 1: Determine If You Need NinjaFlex
Not all applications need NinjaFlex because of its elastic properties can be neutral or even a disadvantages in many cases.
Good Uses
- Tight fits (Phone cases could be printed and really stretch around the case and hold your phone tight)
- Rubbery surfaces (Phone case (makes your phone non slip) and tires for RC cars are good applications)
- Human use item (a wristband or a watch casing can conform to the body when it is flexible rather than stiff)
- Decoration (some things are just fun to play with and looks cooler with the added property of flexibility
Bad Uses
- Anything rigid (if you need rigidity do not use an elastic part obviously)
- strength application (elastic filament have very low strength)
- Cheap parts (looking at the price compare to PLA this is pretty expensive and it takes some work to print so dont waste it on cheap parts)
Step 2: Understand Benefits and Challenges
Now you know what use cases are good, there are some benefits and challenges of the actual printing of this stuff. One benefit is that it is a good gateway into exotic filament and a way to have you experiment with your printer. However, that's about it because this stuff brings a whole lot of challenges to the printing aspect.
It is more expensive and it takes a long long time to print (will go over in settings section) so it may feel like you are banging your head for a lot of the beginning. Also you may need special extruder for this filament because of how elastic it is, printers with bowden printing (where extruder is far from nozzle and it pushes through a long tube) cannot print this filament. So if you can't print with your printer without modification you may have to look online as to how you can modify.
Step 3: Change Settings
Now here is the part you need for setting changes.
1. Slow down speed
Whatever printing speed you have for regular printing, most likely you have to do 1/3 of that and even slower for the first layer to get good adhesion. Starting around 20mm/sec is good and going even slower if you dont see good adhesion results.
2. High temp
A high extruder temp of around 240 C is good and increasing bed level to 70 C will allow it to stick first layer better (feel free to raise it to have better adhesion if it doesnt work at first).
3. Higher Retraction (to stop oozing for looks)
More retraction speed of 30mm/sec and 1.8mm rectraction distance is a good place to start. This setting is useful for only aesthetics.
*These settings in the picture are the most important for a TYPE A PRO printer, your printers may be different but these are the setting that will most affect the success of your part.
Step 4: Do a Test Print
A good way to test the settings is to do a test print and a good test print is benchy! Go to the link (https://www.thingiverse.com/thing:763622) and download the stl to slice. This test print is a good way to test overhangs, curved edge smoothness and sharp geometries.
Step 5: Check Test Print
After printing test your print by looking at it and feeling the surface. The oozing creates the spiderweb which are very hard to get rid of even with dialed up retraction settings so that is normal with bridges. The flexibility should be as advertised and you can squish with your finger!
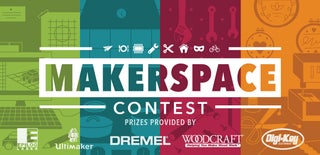
Participated in the
Makerspace Contest 2017