Introduction: How to Break Down a Full Sheet of Plywood
A full-size sheet of plywood is 8 feet long by 4 feet wide, which can be difficult for one person to manipulate on a table saw (unless you are fortunate enough to have a really large infeed/outfeed table setup!) If your project is small enough, you can buy pre-cut half-sheets (4 feet by 4 feet) or even quarter-sheets (2 feet by 4 feet) that are easier to wrangle, but this won't work if you have dimensions greater than 4 feet long. This instructable details a method for using a hand-held circular saw to break the full sheet down into pieces that will be easier to use on your table saw.
The general idea is to use a frame of sacrificial wood to raise your plywood off the floor enough that a circular saw cuts through without hitting the floor. My father taught me this and I understand many others -- especially home workshop people who have limited space -- do so as well.
This is entered in the Woodworking Challenge as a Skills entry. :)
The general idea is to use a frame of sacrificial wood to raise your plywood off the floor enough that a circular saw cuts through without hitting the floor. My father taught me this and I understand many others -- especially home workshop people who have limited space -- do so as well.
This is entered in the Woodworking Challenge as a Skills entry. :)
Step 1: Making the Cutting Frames
Materials:
(10x) approximately 4-foot lengths of cheap wood. If you're buying new, 2x4 studs are the way to go. I built mine from 3/4" MDF because I had a lot left over from the construction of our house.
Drywall screws of appropriate length
Tools:
saw
cordless drill with driver bit
These are just simple wood frames, approximately 4-feet square on each side and as deep as the board's dimensions allow. So if you're using 2x4's, it should be 4 inches deep (i.e., set the 2x4's on edge relative to the floor when putting the frame together). I also recommend a mid-way support piece, as shown in the first picture below. Put them together with drywall screws but make sure to keep the screws at least 1-inch away from the top of the frame (where the plywood will lie). The reason is that when you're cutting the blade will bite into your frames a little, so you don't want it hitting a screw!
If it's a little flimsy (as mine was) use some scrap pieces to reinforce the corners on the bottom.
You need to build two of these frames. Put together end-to-end, you have a support for a full 8-foot-long sheet of plywood. Some people build a single 8-by-4 frame, which is fine, too. I split it into two frames to make them easier to carry and store.
If I were building another set of frames, I would make them a little smaller than 4-feet square, say, 44" on a side. This would make it a little easier to clamp the straight-edge when cutting.
(10x) approximately 4-foot lengths of cheap wood. If you're buying new, 2x4 studs are the way to go. I built mine from 3/4" MDF because I had a lot left over from the construction of our house.
Drywall screws of appropriate length
Tools:
saw
cordless drill with driver bit
These are just simple wood frames, approximately 4-feet square on each side and as deep as the board's dimensions allow. So if you're using 2x4's, it should be 4 inches deep (i.e., set the 2x4's on edge relative to the floor when putting the frame together). I also recommend a mid-way support piece, as shown in the first picture below. Put them together with drywall screws but make sure to keep the screws at least 1-inch away from the top of the frame (where the plywood will lie). The reason is that when you're cutting the blade will bite into your frames a little, so you don't want it hitting a screw!
If it's a little flimsy (as mine was) use some scrap pieces to reinforce the corners on the bottom.
You need to build two of these frames. Put together end-to-end, you have a support for a full 8-foot-long sheet of plywood. Some people build a single 8-by-4 frame, which is fine, too. I split it into two frames to make them easier to carry and store.
If I were building another set of frames, I would make them a little smaller than 4-feet square, say, 44" on a side. This would make it a little easier to clamp the straight-edge when cutting.
Step 2: Tools
Circular Saw (aka "Skilsaw")
Saw guide, at least 96 inches long (Home Depot/Lowe's sell a 2-piece saw guide, with clamps, for about $20).
tape measure
drywall square (optional, but makes the job much easier)
I also recommend buying a "panel carry handle" for moving your plywood.
Saw guide, at least 96 inches long (Home Depot/Lowe's sell a 2-piece saw guide, with clamps, for about $20).
tape measure
drywall square (optional, but makes the job much easier)
I also recommend buying a "panel carry handle" for moving your plywood.
Step 3: Mark Your Cut Line
First, decide from where on the plywood you want to measure your cut lines. For a given plywood sheet, the squareness of corners and the straightness of edges may be in question, so check each corner with a square and each edge with a straightedge (I like using a 2-foot level for the latter). Do not assume the factory got it right! When I make assumptions like that I tend to ruin a $50 piece of wood. :)
Hopefully you can find two adjacent edges that are acceptably straight and have a good 90-degree angle between them. Start your measurements from this corner. I'm assuming for this example you need a full-length cut (a rip down the 8-foot length of the sheet).
Measure from the corner to your cut line and mark with a pencil. Do the same thing on the other end of the sheet, establishing two points for your cut line.
Use a drywall square to draw your cut line across the whole sheet. You'll have to draw half coming from one side and half coming from the other. Don't be surprised if they don't match up! Just adjust so that the line is consistent with your "good" corner.
Hopefully you can find two adjacent edges that are acceptably straight and have a good 90-degree angle between them. Start your measurements from this corner. I'm assuming for this example you need a full-length cut (a rip down the 8-foot length of the sheet).
Measure from the corner to your cut line and mark with a pencil. Do the same thing on the other end of the sheet, establishing two points for your cut line.
Use a drywall square to draw your cut line across the whole sheet. You'll have to draw half coming from one side and half coming from the other. Don't be surprised if they don't match up! Just adjust so that the line is consistent with your "good" corner.
Step 4: Set Your Straightedge
Figure out the distance from your saw's blade (the cut line) to where the straightedge should be. There are several methods for this:
-- You could measure it. This works fine for rough cuts but I wouldn't trust it for a finish cut.
-- Use the saw to "nick" the cut line a little then, while holding the saw at the cut line, use a pencil to mark the edge of the saw base (this becomes your straightedge line). The third picture below gives an idea of the geometry. Do this on the far end of the cut line too, but make sure the saw is facing the same direction when marking the straightedge line.
-- When I first bought my saw, I took a piece of scrap wood and made and cut it so that it was exactly the distance between the blade and the saw edge. Very handy! So I use it to set the distance between the cut line and the straight edge.
However you determine this distance, do it on both ends of your cut line. In other words, make sure you measure your straightedge the same distance from the cut line on both ends.
Update 5/28/2012: User UncleBuild reminds me to mention the blade kerf (i.e., the thickness of the blade). This needs to be taken into account when setting your straight edge. The kerf should be entirely on the "waste" side of your cut line. In our example, since I'm measuring from the left side of the board then the blade should cut on the right side of my cut line. My cutting template takes this into account automatically, so I tend to forget. If you don't have a cutting template, just make sure you set the outside edge of the widest blade tooth (which are usually wider than the blade body) on your cut line.
Assuming you are using clamps to hold the straightedge in place, use thin (1/8") pieces of scrap between your clamps and the plywood. This keeps the clamp from damaging the wood.
-- You could measure it. This works fine for rough cuts but I wouldn't trust it for a finish cut.
-- Use the saw to "nick" the cut line a little then, while holding the saw at the cut line, use a pencil to mark the edge of the saw base (this becomes your straightedge line). The third picture below gives an idea of the geometry. Do this on the far end of the cut line too, but make sure the saw is facing the same direction when marking the straightedge line.
-- When I first bought my saw, I took a piece of scrap wood and made and cut it so that it was exactly the distance between the blade and the saw edge. Very handy! So I use it to set the distance between the cut line and the straight edge.
However you determine this distance, do it on both ends of your cut line. In other words, make sure you measure your straightedge the same distance from the cut line on both ends.
Update 5/28/2012: User UncleBuild reminds me to mention the blade kerf (i.e., the thickness of the blade). This needs to be taken into account when setting your straight edge. The kerf should be entirely on the "waste" side of your cut line. In our example, since I'm measuring from the left side of the board then the blade should cut on the right side of my cut line. My cutting template takes this into account automatically, so I tend to forget. If you don't have a cutting template, just make sure you set the outside edge of the widest blade tooth (which are usually wider than the blade body) on your cut line.
Assuming you are using clamps to hold the straightedge in place, use thin (1/8") pieces of scrap between your clamps and the plywood. This keeps the clamp from damaging the wood.
Step 5: Always Wear Protection
Put on a breath mask, ear plugs, and safety goggles!
Step 6: Making the Cut
Set your blade's cut depth to be just slightly (1/8" or so) more than the thickness of the plywood. Enough that it cuts cleanly through the plywood and just a little into your support frame.
Make the cut, keeping the edge of the saw's base against your straightedge.
Make the cut, keeping the edge of the saw's base against your straightedge.
Step 7: Cross-cuts
Okay, you've made that long cut and are ready to trim it to length. Since you've already taken the time to set up, go ahead and do a cross-cut! The 2-piece straightedge is nice for this since you can use half of it when needed.
Step 8: Accuracy of Cut
Some thoughts here:
-- Using this technique, I have achieved straighter, more accurate, cuts than I did with my radial arm saw (which has now been traded in for a better table saw)
-- With a little practice, you can do finish cuts with this technique, however if you trust your table saw more, use this technique to get "close", i.e., set your cut line 1/8" or so greater than the actual dimension, make your rough cut, then clean it up on the table saw once you have a smaller, more maneuverable piece.
-- The straightedge can flex a little in the middle, especially where the two pieces are attached to each other. My father puts a brace here; I'm a bit lazier and I just cut slow and support the straight-edge with my hand as I go along.
-- Using this technique, I have achieved straighter, more accurate, cuts than I did with my radial arm saw (which has now been traded in for a better table saw)
-- With a little practice, you can do finish cuts with this technique, however if you trust your table saw more, use this technique to get "close", i.e., set your cut line 1/8" or so greater than the actual dimension, make your rough cut, then clean it up on the table saw once you have a smaller, more maneuverable piece.
-- The straightedge can flex a little in the middle, especially where the two pieces are attached to each other. My father puts a brace here; I'm a bit lazier and I just cut slow and support the straight-edge with my hand as I go along.
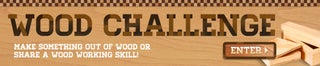
Third Prize in the
Woodworking Challenge