Introduction: How to Build an Accurate Mechanical Model of the Solar System
Hello, I'm Khush, I am an A-level Student studying Product Design in the UK and this is my final project at school. It would be amazing if you could leave a comment for my coursework. For students studying Product Design for their A-levels, you have to make a final year project for the coursework. Most students my year decided to make a piece of furniture or something similar, I personally thought that would be as fun to make so I looked on this website to help inspire me on what to make. I came across a few models similar to this and they gave me the inspiration to take this on as my product. Here are some links to some of the models which had inspired me:
https://www.instructables.com/id/How-to-Build-a-Pr...
https://www.instructables.com/id/8-Planet-Motorize...
https://www.instructables.com/id/Solar-System-Orre...
All of these are incredible Instructables to read so I recommend checking them out. I would like to state that although these were my inspirations, I have made my own gearing ratios and design. I will make sure to include a link to the CAD parts. Each step of the production is from my record of manufacture so I apologise for any parts hard to read.
Some of the key features include:
- The revolutions of all the planets are accurate to 99.3%
- The planet sizes are scaled to S'= Ln((S/10^3)/2)*10 in mm
- The radii of the orbits of the planets are scaled to D'= Log(D)*150 in mm
- It is motorized with the orbit of Earth taking 30 seconds
Step 1: The Materials and Equipment
I am lucky to go to a school with a thriving DT department so I had access to professional equipment.
Materials:
- Casting Aluminium
- 10mm Aluminium tube (300)
- 8mm Mild Steel bar (330)
- 5mm Black Acrylic sheet (600 x 300)
- 8mm Frosted Acrylic sheet (600 x 300)
- 5mm Brass bar (1.1m)
- 3mm Silver Steel bar (120mm)
- https://www.amazon.co.uk/Reversible-Reduction-Elec...
- https://www.amazon.co.uk/gp/product/B0746CK175/ref...
- https://www.amazon.co.uk/gp/product/B07CWLGNJ5/ref...
- https://www.amazon.co.uk/Toggle-Switch-SODIAL-Posi...
- Spade connectors
- Solder
- https://www.shapeways.com/product/KEE55AKJW/solar-...
- https://www.amazon.co.uk/Crystal-Photography-Lensb...
Equipment:
- Metal Lathe
- Milling machine
- Belt sander
- Laser cutter
- Hack Saw
- Wire stripper and crimping tool
- Soldering Iron
- Sand casting equipment
- Scribe
Step 2: The Gear Ratios
To do the gear ratios, I started off by finding the orbital period of each planet in Earth years and use this as a basis to create 'desired' ratios between the each of the consecutive planets. After this, I used trial and error to find teeth numbers for each of the gears to get them as close to the desired ratios as possible. I also used trial and error for scaling the distances and the planets.
Step 3: Laser Cutting the Gears
Process:
For the arms, I decided to spray the frosted acrylic black so I could laser engrave the design on it and it would have a good aesthetic appeal. To do this, I wiped down the acrylic piece with a cloth to remove dust, I put it under the extractor fan in a well-ventilated room. I applied my first coat of the black spray paint. I allowed that to dry and applied my second layer making sure each layer was thin and covered the whole area. The strokes on the second layer were perpendicular to the first to get the best coverage. I applied 4 coats and allowed each to dry. Between drying times I designed the gears and arms on the computer. When creating the gear ratios I had to use trial and error to get the ratio as close to the real ratio as possible and used the toolbox to create the gears with a right number of teeth. Using smart dimension was very useful as I was allowed to create perfect measurements. All the gears were mated on SolidWorks with the correct ratios and worked together perfectly. This means the gears I had designed were perfect for the product as long as the friction on the pivots were at the minimum. I took the bearing sizes and central shaft into consideration and made the holes accordingly. I converted all of my gears to a 600mm by 300mm working drawing scaled 1:1. I ordered all the parts and saved it as a .dxf drawing. Then on techsoft, I imported the drawings from the .dxf file and did my final edits. I used the letter tool to number each gear. The first number represents which planet it moves from the outer planets to the inner planets. The second number represents the number in the gear train. On techsoft, all I had left to do was the numbering so this means I had fewer uncertainties when doing the measuring as the smart dimension tool is only on SolidWorks. I saved all my parts onto a USB and took it to the laptop for the laser cutter and got it cut out. Although creating the gears took over 2 hours, converting it to techsoft only took a few seconds. This was also true when doing the arms for each planet as this was created the same way on SolidWorks and converted to techsoft. When laser cutting the gears, the time taken for the total sheet to be cut was 41 minutes to do and the arms took 32 minutes to do. Although the arm file was smaller than the gear file, I cut the arms out on 9mm frosted acrylic while the gears were cut on 5mm black acrylic.
Alternatives:
The gear would have been near impossible to do by hand, even with a template but this would have taken a huge amount of time and the accuracy needed would not be sufficient as a laser cutter has. The arms could have also been possible to do by hand but laser cutting them meant I could do a cool space design.
Attachments
Step 4: Creating a Mould for Sand Casting
Process:
I made a Solidworks design to see how layering triangle pieces of 12mm MDF would go together and what the lengths for each triangle would be. I used these lengths to knock up another CAD design on techsoft for the laser cutter. The black lines were used to cut and these pieces were sent off to the laser cutter. Once this laser cutter cut the pieces, I used dowel and PVA glue to attach the pieces together. This was much easier as all I had left to do was sand all the edges down to the same angle to create a slope as I used the belt sander. This made this process much quicker and the mould was shaped within 2 hours. After this, I used a sanding block to curve the edges so it would be easier to sand cast and sandpaper with increasing grits to smooth down all the surfaces. After smooth, I applied a layer of varnish as it is resistant to moisture from the sand in sand casting and dried it with a blow dryer. I applied 2 more layers to each face and using high grit sandpaper, remove the paint brush marks.
Alternatives:
A good alternative would be 3D printing the base out of ABS and sanding down the edges to remove the plastic lines however this was not possible as our 3D printer at school did not print sizes of this magnitude.
Step 5: Sand Casting
Process:
To make the aluminium base, I brought out the sandbox and the 2 halves of the sand holder. Firstly, I put the bottom half of the sand holder (the drag) upside down and then I put my base in the middle and sprinkled parting powder all over the bottom plank of wood and my base. Then I used a brush to make sure the parting powder was laid evenly. After that, I used a sieve to sprinkle sand a layer of sand on top of the mould and around the box. I compressed the top of the mould and around the edge with my fingers. After that, I had to carry on adding heaps of sand compressing it after every layer with a mallet by pounding it until the sand wouldn’t move anymore. I carried on doing that until the sand was heaped over the top. Using a flat metal bar, I levelled off the sand in drag then slowly lifted it up (making sure no sand falls out (it shouldn’t if the sand is compressed enough)) and flipped it over.Then I put the second half of the sand holder (the cope), stick the mould for the runner and riser near the base mould on opposite sides in the sand and sprinkle more parting powder on top. I brushed the parting powder evenly on the mould and the sand again. After this, I sprinkled and compressed more of the sand into the cope around. I carried on adding sand as well as pushing the sand together. After I had filled the drag and cope completely I took out the riser and runner, lifted the top and put it on its side on the side. After that I drilled a small pilot hole into the base making sure to keep my hand as steady as possible and tightened a long screw into the base, I pulled out the screw and the mould out together carefully and put it aside just in case a problem arose when pouring aluminium in and needing to restart this process again. I used a trowel to create a path from the motor holder mould cavity to the runner & riser holes and I used a paintbrush to take out loose sand and put the top half back on. The DT technician then poured molten aluminium into through the runner and into the cavity until you could see the aluminium come out on the other side in the riser. To finish off, we waited for it to cool (about 2 hours), took it out, cut off the excess aluminium with a hacksaw. To clean up the edges, I used emery cloth to smooth the edges a little bit and polished it with wet and dry paper to make it very smooth.
Alternatives:
Instead of sand casting the aluminium base, I could have used a CNC mill along with a large block of aluminium to get a smoother finished product however this would have lead to too much waste making it unsuitable for higher scaled of manufacture and the school doesn’t actually have a CNC mill. Alternate materials include copper, brass or bronze for a cool golden or orangey colour however these metals have a very high melting point compared to aluminium.
Step 6: Milling
Process:
With my casted piece, the bottom was still very rough, to fix this, I put it in the milling machine table vice and secured it on the milling machine bed. I wound down the ‘z-axis’ handle to just above the piece and wound the ‘x-axis’ so the piece was to the right of the mill bit. I turned on the machine and turned the ‘y-axis ‘ wheel up and down to draw a line into the metal piece, I adjusted the ‘x-axis’ wheel for the next turn and went back and forth with the ‘y-axis’ handle. I repeated this process until I had gone over the whole top. I turned the ‘z-axis’ wheel one fraction of a turn and repeated the milling process and I did this until the whole bottom was level. When the base became level, this made it easier to belt sand the edges to the same correct angle as I did with the mould but this time to remove all the imperfections in the casting process.
After this was done, all I had left was to mark out where the holes would be in the motor holder for the motor and the bar. To do this, I used a ruler and tri-square to bisect all the edges to find the centre, I had to do this on both sides as one side would hold the central shaft and the other side would have to enclose the motor. I scraped the lines on with a scribe and centre punched each intersection for the holes. I aligned the milling machine to the centre of the clamped casted piece and turned on the machine, I used a 20mm bit for a clearance hole for the motor and a 10mm bit for the central shaft. I wound the ‘z-axis’ wheel about 25 complete turns slowly to create a hole which was 25mm deep for the motor and about 15 complete turns for the central shaft. To connect these holes, I milled an 8mm hole for the spindle of the motor to go through safely.
To mill the flats for the connecting shafts, I put the full length of the steel bar into the collet and tightened that to the collet block, this was tightened to the table vice on the milling machine bed. Using the handles, the piece was moved to just touch the mill on the end and the handle on the ‘x-axis’ was set to zero, this ensured exactly 5 mm was cut from the end of the bar. I wound the ‘z-axis’ spindle down to be just above the curved surface, 5 mm in from the end. I turned on the milling machine and went back and forth on the ‘y-axis’ wheel and then turned the ‘z-axis’ handle 1 fraction, I repeated this process 5 times and turned off the milling machine, used a micrometre to check the thickness and then one of the gears with the flat holes to test it, if the bar did not fit in the hole, I milled down the flat in small increments to a point where the gear perfectly slid onto the bar. I took out the bar from the collet and cut off 15mm from the end with a hacksaw. With the cut piece with the flat on one side, I tighten the piece with the rough end facing out in the collet. I brought the mill to just touch the rough end and turned the machine on, I went back and forth in the ‘y-axis’ while adjusting the ‘x-axis’ in small amounts until this side was flat. I repeated the process of milling the flat on this piece and then did this whole process again eight times for each of the connecting pieces. To mill the long flat on the central shaft, I could not use a collet block so I used the table vice along with parallels to keep it level. However, the main process of milling the flat was identical as I went up in small amounts to the point where one of the gear holders fit. The process of milling the flats took 1 and a half hours while the process of milling the motor holder took 1 hour.
Alternatives:
For the base, I could have done it completely by laser cutting layers of acrylic and attaching them together instead of casting then milling all the holes in the correct places. This may have been more useful for holding each part together as the laser cutter could account for the spaces however, the colour would not have a metallic theme or a flat edge in this way.
Step 7: Drilling
Process:
For the 8mm driving bar that goes through the central shaft with the flat on one end, I marked out the centre of the other end with a centre punch and ruler. I measured the spindle of the motor to find the size of the hole needed for the motor to fit into the driving bar. I put the bar into the lathe with the marked outside about 50mm away from the chuck of the main stock. On the tailstock, I tightened the drill chuck in with a 4mm drill bit. After this was all secure I turned the tailstock wheel to bring it closer to the steel bar and turned on the lathe. With my bar spinning, I wound the drill bit into the end of the bar up to 15mm and brought it back out. I put the motor spindle in the hole of the bar to check if the hole was perfect just in case and it was. Then, using a ruler and centre punch again, I marked out a hole for an M4 grub screw to go in to hold the motor in place. I put the bar in a V-block and secured the V-block to the table vice on the pillar drill. I put a 1/8th drill bit into the chuck of the pillar drill and tightened. The school did not have a 3.2mm drill bit for tapping M4 holes so this was the closest I could get. I turned on the pillar drill and drilled down straight into the bar to the point where I could see the bit in the hole created on the lathe directly before the bit got to the other side. I put the motor in and secured it with a grub screw in place.
For the legs, I laser cut the three legs using the same technique as before onto 8mm acrylic. I used a combination square to find the angle of each corner of the motor holder and used this to draw my design. After being laser cut, I used a permanent marker to colour the edge for the hole for connecting it to the base. After colouring the edge on the 3 pieces, I used a ruler, scribe and engineers square to work out the centre from the long side. After I marked the centre lines on all the pieces, I put my piece flat on a parallel bar and accounting for the thickness of the parallel and the middle of the width of the acrylic piece (4mm), I used a vernier height gauge to mark the middle of the leg. I put each piece in a vice and centre punched the cross section to get the exact middle of the hole. On the pillar drill table, I set up an angle plate with a G-clamp and then G-clamped the acrylic piece onto the angle plate. I centred this to the drill and tightened a 4mm drill bit into the chuck. I drilled a hole into each of my pieces and then numbered them. To mark out the hole into the motor holder for the legs, I cut about 15mm off a 4mm nail and hardened it to create a punch. To harden it, in the heat treatment area, I turned on the blow torch and heated the nail in a blue flame to cherry red. When the nail started to glow, the technician brought over a little pot of water and with long nose pliers, I picked up the piece and dropped it into the water to cool completely. I lined up a leg to one of the edges on the motor holder and put the punch in. With help from a teacher and the technician, One held the leg and base in place, the other held a scrap piece of metal bar on the punch and I hammered the bar to mark out a hole on the piece, I numbered the leg to the side and repeated for each side. I adjusted the angle of the table of the pillar drill and drilled 1/8th holes in each of the marked holes for the legs. I marked out holes for grub screws to hold the motor in place and drilled 1/8th holes here as well but with the table at 0° for a hole parallel to the bottom of the base.
Alternatives:
I could have drilled a hole for the spindle with a pillar drill but that would have required a much longer time to set up for the same degree of accuracy as the lathe.
Step 8: Turning, Tapping & Threading
Process:
For the holes I drilled into the base for the legs and to hold the motor up, I decided to tap the holes. For this, I started off with an M4 taper tap and tightened it into the tap wrench. I put the piece in a vice and made sure I was tapping perpendicular to the surface of the whole. To tap the holes, I turned the wrench in the hole 360° clockwise and then 180° back anticlockwise. I went back to remove the material out of the hole and forth to make the thread deeper. After I reached the end with the taper tap, I repeated the process with a plug tap to make the thread more defined and so the bolt screwed in tightly. I tapped all the holes I needed to on the base and the hole for the grub screw in the central spindle. After tapping these holes, I used an M4 bolt to check how strong the tap was and to make sure I had not taken away the thread by tapping in the same spot for too long.
After this, I had to make small bolts that I could turn by hand to attach the legs to the base as there was not enough space to use a screwdriver with a regular bolt. To do this I tightened a 10mm diameter bar into the chuck of the metal lathe. I turned on the lathe and using the facing tool, I made the edge flat by turning the forward/back (y-axis) spindle all the way to through the face and back. Then, using the same tool, I turned the y-axis wheel back to the curved surface just touching it and turned the x-axis spindle 15mm down and back. I turned the y-axis wheel in another small increment and repeated the cut with the x-axis wheel. I repeated this process in small measurements to turn the bar down to 4mm in diameter so I could thread it and so it could go in the M4 hole I tapped. After turning the end down, I used a knurling bit to knurl 5mm inwards for the grip so I could tighten the bolt into the base. I took out the aluminium bar and cut off the end with a hacksaw then faced it back off with the lathe and the facing tool again. I repeated this process of creating the bolts 2 more times for each of the legs. For the brass arms, I cut the 5mm bars into each of the specific lengths with the hack saw and turned the ends down the same way with the lathe. Then using a countersink bit, I countersink the end and using a 2mm drill bit, I drilled into the end. The countersink end was to make it easier to hold the planet in place and the hole was so I could put an M2 bolt through the planet and the bar for making the glued joint stronger.
The next part was threading the knurled bolts and the brass bars for the planets. The brass bar was to be threaded to M5 and the knurled bolts were to be threaded to M4. The threading process is pretty much identical to the tapping process as it involves turning the wrench 360° clockwise and then 180° anticlockwise. I tightened the M5 die into the die stock and turned the non-countersunk end down to 20mm of the brass bar. I made sure to liberally use grease as brass was quite a stiff metal to thread. I checked the thread with a wing nut but realised the thread was too tight. I tightened the 2 other grub screws on the die stock to make the thread tighter and rethreaded the brass bars to make them a bit looser. I repeated this process with each of the brass bars and then the knurled bolts.
Step 9: The Assembly Part 1- the Fall
Process:
This is one of the last steps I had left to do with my product. I had tapped each hole, I had laser cut each gear and cut the flats where I needed them. To start off, I made the outer gear branches first. To do this, I put one of the 3mm steel pieces with the flats into the centre of a 10mm outer diameter bearing. This bearing fit into the holder for each of the segments of the mechanism, I had 8 of these to do. Using the numbering system I laser engraved onto my gears, I put gears .2 and .3 on either end of flat bar sandwiching the holder in the middle- but not doing it too tight so the gears would spin freely. I used 2 part Araldite to glue the connecting shaft piece to the gears. I did this for each of them and left them overnight to cure.
For the planet, I put an M2 screw in the 2mm hole at the bottom of each planet and using Araldite, I cleanly glued on each of the planets onto the corresponding brass bar and allowed the glue to cure overnight. I removed excess glue with a toothpick and cloth along the side to ensure neatness before the glue was set properly.
For the circuit, I looked up on google how to wire a dpdt switch to reverse a motor and wired it according to the image. I made sure to order a motor to make sure that my power source did not need to be resisted for the motor so my circuit would be very simple. I wired a 12V adapter plug to the switch and connected that to the motor with crocodile clips. I checked the connection and turned the switch on to check the motor turned.
For the central shaft and the base, I again used Araldite to attach these two pieces together and left them to cure along with the outer gear pieces. For the inner gears, I glued .1 and .4 on either side of the planetary arm with Araldite with the 19mm bearing inside and an M10 nut and bolt to line them up and tighten them. The next day, after all these were cured, I started assembly, I pushed the first arm with the gear down all the way to the bottom. The bearing was tight on the central shaft so I had to cut out a piece of cardboard and put that on top of the arm before using a hammer and a scrap piece of pipe to mallet it down to the bottom. I then put the next outer gear mechanism and then the next planetary arm repeating this process over and over again up to the last arm. I attached the legs on with the previously made hand tightening bolts and put the motor in the 8mm steel driving shaft securing it with a grub screw. I used crocodile clips to wire the motor up and put that through the central shaft. On the flat of the driving shaft, I put the primary driving gear on and turned on the motor to see if all the gears turning.
After securing the motor in the base with the 3 grub screws for that and turning on the motor, nothing moved. I took switched the motor off and took off the drive gear to turn the system by hand just to check where the problem would lie. I found that there was too much friction between the inner gears and the central shaft, this may have been because I laser cut the hole in the gears to 10mm and the aluminium bar was slightly bigger or the holes were not lined up correctly when glueing.
This was a huge problem. This meant I had to take it all apart and redo the central mechanism all over again. I pulled off the top gear and the subsequent arms and outer connections, but the gears glued to the bottom arms unstuck. I realised I could not use glue in my mechanism because it did not hold as well as it should have.
Instead of trying to remove every part piece by piece, I salvaged all the parts I did not have to redo leaving only the arms with the gears stuck on the central shaft. I cut up the central shaft so I could take out the bearings and the arms and destroyed the central gears in the process. This meant I had to redo all the central gears and the central shaft again because these were not salvageable.
Step 10: The Assembly Part 2- the Rise
Process
After the big failure, I started on fixing the gears, to do this I reopened my techsoft design and copied over the central gears to a new file. I increased the diameter of each hole by 0.25mm on all of the parts that were meant to be on the central shaft and put another hole with a 4mm diameter 15mm from the centre for each of the .1 gears and a hole of 3.25mm on each of the .4 gears. I laser cut the new gears out of the 5mm black acrylic used for the other gears. With the arms, I put the bearing in and put one of the new 0.1 gears on one of the sides (it didn't matter which side) and used an M10 nut and bolt to realign them. Put the arm on the machine vice of the pillar drill and drilled a 4mm hole into the arm with the same procedure as my previous step and then with a countersink bit I countersunk the 4mm hole on .1 gears. I tapped the hole 3.25 hole on the .4 gears with an M4 tap and put together the arm pieces with an M4 countersunk bolt. The larger diameter holes for the gears on the central shaft meant that only the bearing would be in contact with the central shaft reducing the friction here by a great amount. I also had to redo the central shaft, to do this, I repeated the milling process on a 10mm bar cut to the correct length with a hacksaw. This process was identical to the milling process described in the previous slides and I glued that to the base with Araldite again after removing the old piece.
I found another problem after doing this. After doing the milling process, the central shaft dented with little notches on the inside so there was resistance with drive bar. To fix this, I put the drive shaft into a hand drill and covered it with diamond lapping paste. I put the base and the central bar upright in a table vice and using the hand drill, I drilled down the diameters of the two shafts so the both became frictionless. The internal diameter of the central shaft increased and the diameter of the drive shaft decreased so there would be less contact. I went through a couple of times to make it perfect and cleaned out all the waste and diamond compound left with a cloth.
I also decided to create 1mm spacers out of HIPS to make sure that the arms were slightly raised above the outer gears so they did not collide. I drew these washers on techsoft and laser cut them as well making sure the internal diameter was 11mm so it did not cause friction with the central shaft. After this, I was ready to rebuild. I resecured the motor onto the drive shaft with a grub screw and then secured motor into the base with the further 3 grub screws. I reattached the legs onto the base in the correct place with the hand tightening bolts. I stacked the first arm with the gear, it slid on tightly but perfectly only on the bearing so it turned freely and I didn’t have to tap that down into place.
To connect to gear 1.1, I pushed down the outer gear connection with gear 1.2 at the bottom and 1.3 at the top. I pushed down Uranus’s arm and repeated with 2.2 gear connection downwards. I made sure to put a washer in between each component. I repeated this process all the way to 8.3 at the top making sure there was no resistance turning the arms all the way along. I put the 8.4 drive gear onto the flat of the drive shaft and wired up my circuit with crocodile wires. I connected the planets bars with the arms with bolts on either side of the threaded part and mounted the sun at the top. I flicked the switch, it worked! There were still a couple of problems so the motor periodically slowed down and sped up but this was fixed by spraying down the gears and the shaft with silicone grease. I flicked the switch the opposite direction and the planets turned anticlockwise as well. This was a proud moment.
I then focused on the circuit. For this, instead of the crocodile clips, I replaced them with wires and spade connectors for the switch and soldering on the motor. For the spade connectors, I stripped the wires and twisted the ends, put them into the spade connectors and using a crimping tool on the red bit. I slid the connectors onto the switch. For soldering, I heated the soldering iron up and melted some solder on the end, I looped the wire into the hole of one of the terminals of the motor and applied the solder. I repeated this for the other terminal also. To connect with the power source, all I had to do was tighten the wire in with the screw. I will show the diagram on the next page. I wrapped some heat shrink around the wires connecting to the motor and using a heat gun, I covered this up. I designed and laser cut a box out of 3mm black acrylic to house the electronics on the side so the switch box would not interfere with the actual product. I cleaned up all my pieces and the production of my orrery was finished.
Step 11: Review
This project was a fantastic challenge to make and I do recommend making a project like this as I had a lot of fun making this. I want to apologise for how long each step is and how it can be difficult to follow at times but feel free to make this project yourself and modify it any way possible. It would also be amazing if you can leave a comment giving some constructive criticism or your thoughts on this for me to use in my coursework. Thank you so much.
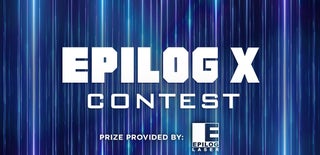
Runner Up in the
Epilog X Contest