Introduction: How to Create a Large 3D Printer Using a Smaller 3D Printer - "Project Locus"
From those that own 3D printers, to those who simply are just curious about their capabilities, one topic that comes up rather frequently is the idea of "Printing another 3D Printer". Now this may not be 100% possible when considering components such as the electronics, however, nearly every 3D printer today in the open source community utilizes to some degree, 3D printed parts in it's construction. From fan mounts to spool holders, a person can spend a few minutes searching the web, and likely find a suitable design to use on their own printer. This has proved to be very useful, especially for those who love to build, modify, and design their own machines.
I had went in half and half on a Prusa i2 machine with my roommate late last year. Knowing we would not be living together this coming school year, we were faced with a predicament I'll refer to as "who's going to keep the printer". Given this situation, I proposed an idea. If we could agree on a value for what the printer was worth, I would accept half of the current resell value and put that towards building a new printer. The deal was made under the condition that we continued to share the printer for the remaining 3 months of the lease. With a mere 3 months to build a printer from scratch, it was time to get to the grind; do lots of research, design like crazy, and more importantly, PRINT LIKE CRAZY.
My main goals for the printer were:
- $600 budget
- As close to a cubic foot of built volume as possible
- Precision equal to, or better than the Prusa i2
- Bowden extruder setup to remove weight from carriage area, allowing more speed, less moving mass, and possibly better accuracy
- Ability to print PLA and ABS
As soon as I stepped my feet into the market of ordering parts, I began realizing that this was not going to be the same as building a printer similar to the Prusa. Although my budget was somewhat on the smaller side (College student), the overwhelming drive to build and create made me think a little harder.
The two main costs of the printer (which had alternative options) were the aluminum extrusions and the heatbed. After looking into homemade heatbeds, I had decided the price difference was very marginal, and not worth the time, effort, and risk. The aluminum extrusions would be what would make this that much more interesting. To build a simple cube which matched my desired built volume, while still allowing room for component mounting, would cost me at least $100 (USD). This was just a rough idea of what I thought I would need to create solid corners and overall a rigid frame for this somewhat large printer. That's when I began experimenting with how to make a cheaper, cost effective, proof of concept, printed PLA extrusions frame.
The printer was unnamed throughout the entire design and build process, more because I wasn't sure what exactly it would look or be like. The "P.L." on some parts, stands for "Project Locus" (as well as my initials). The mathematical definition of Locus is as follows;
"A curve or other figure formed by all the points satisfying a particular equation of the relation between coordinates, or by a point, line, or surface moving according to mathematically defined conditions."
-source: dictionary.reference.com
-------------------------------------------------------------
This printer works using a belt routing technique more formally known as "CoreXY". There are alternative ways to use this technique in a system other than the way I do, however the main issue for those using it is how the belts will cross at a certain point (although there's phyisically only one belt). If you're interested in learning more about CoreXY, there's a small, but helpful website you can visit here: http://corexy.com/index.html
------------------------------------------------------------
Note to the builder:
I will try my best to be as thorough in the assembly and details as possible, however, it is assumed that to construct this printer the person(s) involved have at least an intermediate level of overall skill levels. Basic power tools will likely be needed (drills, angle grinders to cut and chamfer threaded rods, etc). I have included many pictures and CAD illustrations to aid in the assembly process, these will be the key elements to follow for a successful build. The ability to interpret the information provided, as well as simple troubleshooting skills will prove to be handy. The main hardware used consists of 10-24 machine screws, which will need to be cut to length by hand (takes a few seconds per screw) with the use of a standard wire cutter with machine bolt cutting capabilities. These cutters can be found at the hardware store for between $5 and $25 depending on the quality of the tool. I recommend purchasing one that is at least middle of the line considering there are a lot of bolts to be cut. These work by shearing the bolt, and I have found that the nicer tools are far less likely to leave a rough edge at the end of the bolt thread.
Q: I'm going to print these parts on my current printer, how big should it be able to print to fit even the largest parts?
A: All of the printed parts used on this printer were created using a prusa i2 style machine with a build volume of 185mm x 185mm x 85mm (x,y,z). The extrusion pieces are to be printed vertically, and these are 80mm tall each. I typically printed 6 at a time.
**Please Note** As with many how-to write-ups, further revising and additional details can always be added to make it that much better. As time allows, I will continue working on it to try my best and revise lists and overall information. There's a lot to cover, please use the pictures and illustrations to your advantage as I believe those provide the best guide anyway. I highly recommend reading through the entire guide first, and downloading/taking notes as you go. There may be small details which are better picked up by a thorough read before beginning the build process.
Step 1: Gather and Print Parts
Time to buy some parts, and of course print some parts, print some more parts, and finally, print a few more parts. (I will post .stl files on the pages related to the parts being assembled). Once doing lots of brainstorming and sketching during class (whoops), I decided I wanted to use common parts, and build the printer around those. Here's a parts list to get started. I'll try to list everything here, however I may forget some things. Each step contains details regarding hardware involved as well.
----------------------------------------------------------------------------------------------
-(5) Nema 17 Motors (2 for X-Y motion, 1 for extruder, 2 for Z-axis)
- E3D V6 Hot End
- 5mm bore, 17 tooth GT2 Belt Pulleys. These are to be used on the X-Y motors
- Bowden Tube for 1.75mm filament (2mm I.D., 4mm O.D.). I recommend buying at least a few feet and cutting to length
- Ramps 1.4 / Mega 2560 (this will serve as the main control board for the printer)
-(3) Endstops (X,Y,Z). The parts designed on this printer are for use with optical endstops.
-(13) 608 Bearings
-(4) 624 Bearings for belt tensioners located in the X-Y belt path
-GT2 Belt, I recommend buying a 2m roll and cutting it once installed. You'll use most of it.
-8mm Smooth Rod, you'll need (8) pieces in (457.2mm) lengths. There will be 4 required for the z axis (heatbed guides), and 4 for the top X-Y assembly.
-8mm x 1.25 Threaded Rod, you'll need (2) pieces in (457.2mm) length. These will serve as the Z-axis "lifting screws".
-LCD Screen w/SD (Optional, but recommended.) Allows you to run the printer without a computer dedicated to the printer. I used the 12864 LCD which was included with my ramps 1.4 and endstop kit.
-Computer PSU adapted for the 12v sources (don't cheap out here, my Diablotek 475W died quickly). I recommend the Sentey 725W. Alternatively, you can buy a 12VDC power supply which doesn't need configuring.
-12x12" Heatbed with a heatbed relay (the heatbed will draw around 20 amps alone)
-(3) 40mm Fans, 1 for hotend, 2 for Ramps board, if using an additional fan for "bridging" and/or an external heatbed relay cooling fan; purchase 5/4 fans instead of 3.
-(11) LM8UU Bearings, 3 for hotend/x-axis, 4 for y-axis, 4 for z-axis
- 10-24 countersunk machine screws. You'll need to cut these manually to length, unless you can manage to find some in sizes around 6mm (0.25" in length). I suggest buying screws in the 1-3" length, and using a wirestripper/bolt cutter to manually cut screws to length. Please see the picture included for the bolt style and tool I am referring to.
-5/16"-18 Threaded Rod, see the step "Assemble the Frame" for lengths
-5/16" washers - buy a bag of 100
-5/16"-18 hex nuts (Usually you can buy bags of 100 for a few bucks, I'd pick up two bags to start.)
-1/4"-20 Threaded Rod, see the step "Assemble the Frame" for lengths
-1/4" washers (buy a bag of 50)
-1/4"-20 hex nuts, buy a bag of 50
- (2) 5mm to 8mm coupling, used to connect the z-axis Nema 17 motors to the 8mm threaded rod
-3D printer to print parts, or an outside printing service such as 3dhubs.
-(5) spools of PLA filament if printing parts on your own.
-ABS filament (only the hotend parts are highly recommended to print in PLA, the heatbed components are highly recommended, but not necessary).
-12" x 12" Cork Sheet, can be found at hardware store or office supply store, look near where the bulletin boards are sold.
-Heatbed screws (3mm x 35mm), matching washers (12) and (4) 3mm nuts.
-Heatbed springs (something similar to a 7mm O.D., ~20mm in length), these will go under the corners of the heatbed.
- Springs for heatbed frame assembly connection at Z-axis. These should be roughly 30mm in length, with a 9-10mm inner diameter. The coil section will be around 1mm in diameter (pretty standard). These will mount inside of the z-axis threaded rod brackets, and serve to maintain a preload on the upper and lower 8mm nuts.
-Super Glue for mating surfaces between frame extrusion sections
- LED wiring, get the 4 wire rolls, you should be good with a 15 or 20 foot roll of it. This runs ~$10.
- #8 and #6 machine screws, in 1" and 1/2" length. A pack of 100 of each size bolt, with matching washers and nuts should do the trick. I bought two of the same assortment of small machine screws for $5 which included these sizes.
- 11.75" x 11.75" x 1/8" glass sheet for heatbed
- 12" x 12" sheet of kapton tape (optional, for heatbed)
- Binder clips for heatbed, these will secure the glass on top as well as the cork on the underside of the heatbed. The binder clips I am referring to can be found at any office supply store.
- Large compression spring to aid in keeping the hotend wiring and bowden tube from interfering with the X-Y Gantry. (roughly 1" in diameter, 1 foot long).
------------------------------
It is important to note that depending on hardware available, mostly all of these components which I'm listing as 5/16" rod, can utilize 8mm hardware instead if cheaper/preferred (Frame braces, belt crossing axis bolts, X-Y gantry bearing bolts, etc). The reason I used 5/16" is due to supply constraints, as well as extreme price differences if I were to order 8mm hardware and threaded rod online.
------------------------------
In an effort to save money, I made the decision to print parts such as the frame extrusions. However, this obviously had a direct effect on the amount of PLA used. This is where the foam filling comes in. If you wish, you can certainly print all of these parts at 100% infill, or, you can do it in a similar fashion as I did.
The foam I used can be found at several hardware stores from what i've noticed. It's generally used as a crack sealer/gap filler, and has pretty decent properties as far as expansion and overall hardness when cured. One thing to note is the flammable warning label. This means that I do not recommend using this on any parts exposed to hot temperatures (Hot End and Heatbed Primarily). I have included a picture of the foam I picked out, I was able to get by with a mere two cans when building the whole printer, which set me back $5 total for the two cans.
Attached as image files, are tabulated lists of Parts to be printed, Rod Lengths to be cut, as well as recommended infill and whether or not to fill with foam.
Step 2: Begin Filling Parts With Foam (Optional)
If you choose to do the foam filling, this is your page. The general idea I used for this was to drill a hole in the part once printed, making sure that wherever I drilled the hole would be concealed once assembled. This was rather easy, one general pattern to notice is that brackets which will mate up to the frame typically have a flat surface. Given that there are usually at least two of these types of parts on the printer, I would drill the hole on the "backside" (surface mounting plane), fill with foam, and somehow clamp the parts together. I used a range of 2mm - 3mm drill bits depending on the part. The extrusions are the only ones where you'll want one of the smaller bits since you'll be drilling into the end of the extrusion.
Along with the foam, 1/4" threaded rod is used through the center of the extrusions. The foam adds a significant amount of stiffness to the extrusion piece, while the threaded rod will hold the pieces together. In addition to simply holding the extrusion sections together, the threaded rods are also in compression. This further stiffens the assembly and increases the overall strength of the printer when done correctly.
**I would like to mention that this foam should be used in a well-ventilated area, and is very sticky and hard to wash of of your hands. In other words, I recommend wearing some sort of latex gloves while doing this step**
-------------------------------------
For the extrusions, I bought a cheap wood clamp from the hardware store and was able to do 12 at a time. If you haven't cut the 1/4" rod yet, don't. To keep the extrusions nice and straight while keeping the clamp compressed on them, I ran a 1/4" through the centers. Once the foam dries in a day, you can easily pull the parts off this rod, and use it again to fill more extrusions, and eventually in the finished product. Wahh-lah, a tool and a final product (score!). Since I bought my rods in 3ft lengths, I stacked 12 (12*80mm tall = 960mm long = 37.795"). This is important because the rod should not be sticking out the end when clamping, you want the force to be only on the extrusions, leaving the rod's function to be simply keeping the inner extrusion holes concentric. You may use more 1/4" rods as shown, clamped to the outside, to help prevent bowing when compressing the extrusions.
**An alternative option to the wood clamp (for the extrusions) is to pass the 1/4" rod through the center, making sure that the rod length is longer than the total extrusion stacked length, place a washer and a nut on each side, and tighten. These do not need to be super tight, snug will do the trick. Depending on your infill %, there is a risk of breaking them under too much force.**
I drilled 4 holes in one side of each extrusion for the foam. I then would inject a small amount, wait, and inject some more. Once you experiment a little you'll get a feel for it. The idea is to drill all 4 holes on one side, that way when mated to cure, the foam has nowhere to go besides expand inside, and increase the rigidity of the part. Having so many extrusions to do, with 4 holes each, this was a good excuse to make a simple tool to aid in efficiency of the process.
--------------------------------------
To create the nozzle special filler nozzle (optional, but saves a considerable amount of time), download the .stl files and assemble as shown (I used super glue). The special nozzle acts as a 4 way splitter; simply attach the can's included injection straw into the inlet of the nozzle, mate to the extrusion, and fill with foam.
I recommend creating a few of the nozzles because the foam can be troublesome to clean out and reuse another day, that is said under the assumption that you're not filling all of the extrusions at the same time.
The parts required to print and make one nozzle are:
- (1) foamfillertool.stl
- (1) foamfinenozzle.stl
- (4) foamfiltertab.stl
The foam I used can be found at several hardware stores from what i've noticed. It's generally used as a crack sealer/gap filler, and has pretty decent properties as far as expansion and overall hardness when cured. One thing to note is the flammable warning label. This means that I do not recommend using this on any parts exposed to hot temperatures (Hot End and Heatbed Primarily). Here is the foam I picked out, I only used two cans when building the whole printer, which set me back $5 total for the two cans.
Step 3: Assemble the Frame
Now that you have your extrusions printed, and your 1/4" threaded rods cut to length, it's time to assemble the frame.
-To create the basic cube structure, you'll need to make 12 of the frame sides. Each frame side is made up of (6) sections of the extruded profile. The 6 pieces consist of (4) "Extrusion_Main" pieces, along with (2) "Extrusion_w_insert" pieces. Please refer to the pictures included in this step to ensure the correct ordering of the parts.
-If you used foam in the extrusions, now is the time to clean up any of the residual foam before putting these pieces together. Alternatively, you could use a power washer once assembled (which works very well).
- To create a side, you'll need the 1/4" threaded rod, two washers, and two 1/4" nuts. You'll also need some sort of wrench, pliers, or socket to tighten the hardware mentioned. For a standard 1/4" nut, you'll need a 7/16" socket or wrench.
-Begin by placing a nut and washer as shown in the picture, on one end of the rod. The nut should have thread engagement, however the closer to the end, the better. Now, begin stacking the extrusions. I recommend putting a thin layer of super glue in between the sections as you continue to add extrusion pieces. This will help the not only the strength of the sides, but more importantly, this helps ensure that the pieces will remain co-planar with each other.
-Once you've stacked all 6 in the correct order (see picture), place the other 1/4" washer and nut on the free end. Now, tighten the nut until it is snug.
-Lay the assembly on a flat surface, and tighten both nuts at the same time. It will help if you can hold the assembly to the surface so that the sections to not twist when tightening the nuts. These nuts should not be much more than "snug". If you happened to use a high infill % on the extrusion pieces, you are able to tighten the nuts slightly more than snug.
It is important to note that overtightening these main inner rods can not only crack the extrusions, but it can also cause the sections to become bowed. This is why I recommend that you tighten the nuts to "snug", followed by an additional 1/2" turn on each end.
----------------------------------------
-The Corner pieces are to be assembled once all of the sides are complete. The corner pieces assemble as shown in the diagram, and are designed to work with 10-24 x 0.75" Counter Sunk Machine screws. You will need (9) screws and nuts for each corner, and if preferred, you can secure the frame sections even more using the inner holes provided.
-The outer slots will be used on the top gantry, so it is important to not use these holes on the top corner.
--------------------------------------
The purpose of the "extrusions with a chunk missing", a.k.a extrusion_w_insert.stl is to provide an easy way for nut insertion when mounting any components. Even if you have the printer entirely assembled, it's likely that you'll only have to remove one or two things out of the way to place a nut in the frame wherever desired.
-------------------------------------
General assembly of the components is shown in the picture above. Notice the cross sectional view of the frame and bracket assembly. These extrusions work in a similar manner to traditional frame extrusions, however the cost of a single machine threaded nut is far cheaper than the specialty inserts used with aluminum extrusions.
-----------------------------------
The file named "alumex_midspcer_8mm" will be used in the z-axis crossbar braces. One of these is required per side, for a total of two parts per entire printer assembly.
Step 4: Assemble the Hotend
The hotend carriage consists of two main pieces (.stl files are provided). The main bracket houses all of the bearings, and secures half of the hotend.
The hotend is essentially "sandwiched" between the two halves when fully assembled.
The belts clamp onto this assembly using a total of (4) "gt2_belt_clamp" pieces. There is also room to mount a 40mm fan using convienient zip tie locations in line with the bolt holes.
--------------------------------
Hardware required for these components are:
- (3) LM8UU Bearings
-(4) zip ties, for 40mm fan mounting
- (2) 10-24 counter sunk machine screws, with one nut each. These are the 2 lower "sandwich" bolts which hold the case half together.
- (2) #8 x 1" machine screws, with one nut each. These are the 2 upper case half bolts.
- (8) #6 x 1/2" machine screws, with one nut each. These screws are used for the belt clamps located on the top of the assembly.
Step 5: Assemble the Top X-Y Gantry (Hotend, Belt Tensioners, Belt Crossover, Etc)
The Hotend assembly (previous step) will be placed inside of this subassembly known as the X-Y Gantry. Helpful belt routing images related to the belt crossover piece can also be found in this step.
-------------------------------------
The belt tensioners allow slack to be removed from the top belt, since the use of spring style belt tensioners will not work. The standard "spring style" tensioners will not work because of the total distance the belt travels through its maximum motion moves.
The tensioners require (2) 624 bearings per side, for a total of (4) 624 bearings. The screws used are #8 x 1" screws, with a total of (8) #6 washers per tensioner.
- One washer between the bolt head and bracket
- One washer between the nut and the bracket
- Two washers on each side of the stacked bearings to ensure the bearings spin freely, without getting caught on the bracket itself.
-----------------------------------------
The belt crossover bracket requires:
- (4) 608 bearings, which will be stacked in a similar fashion to that of the belt tensioners. However, only one washer will be placed on the outside end of each bearings outermost surface.
- (2) 5/16" or 8mm bolts, 2.5" long.
- (8) total 5/16" or 8mm washers
- (2) 5/16" or 8mm nuts
---------------------------------------------
Connecting the hotend to the GT2 Belt:
- (4) GT2 Belt clamps
- (4) #6 x 1/2" screws
- (4) #6 hex nuts
------------------------------------------
The side slider blocks will run on the 8mm smooth rod for Y motion, and require:
- (2) LM8UU Bearings, fastened using zip ties, (per side)
- (2) 5/16" x 2.5" bolts and hardware (nuts and washers)
- (2) 608 bearings for the belt to ride on
- (4) belt guides, these are essentially tapered washers. They mount above and below the bearings as shown.
- (1) Two-hole washer piece for above the 608 bearings
----------------------------------------
The Front Corner (Multi Brackets), mount a few components. These mount to the corners, and contain the components and illustrated in the picture. The rear brackets mount as shown and simply clamp the 8mm smooth rod.
- (2) 608 bearings (per side)
- (4) belt guide washers
- (1) two-hole washer plate
- (1) bearing tower (these are side dependent, along with each of the corner brackets)
- (2) 5/16" x 2.5" bolts and hardware, these serve as the bearing axis
- (5) 10-24 machine screws cut to length, used to clamp 8mm rods and secure bracket to frame. One of the mounting holes for a screw to pass through is located under where the bearing tower will mount on.
---------------------------------------
The "Bowden_tube_riser" part is designed to give you a place to attach the bowden tube and hotend wiring to. When used with some wire looms, and a large compression spring to run the wires through (roughly 1" in diameter by 1 ft long seems to work), this will keep the bowden tube and wiring bundle from interfering with the X-Y Gantry throughout the motions of the print.
---------------------------------------
The "bridgingfanmount.stl" is optional, but highly recommended as it improves the overall printing capability (particularly with bridging). The mounting is shown in the images, and no additional hardware is required besides the fan. This mount utilizes a standard 40mm CPU fan. To wire this up on a ramps board, you'll want to connect the positive and negative wires to their respective D9 connector locations. From there, the speed and overall utilization of the fan can be controlled using the board and slicing software.
Attachments
t_gantry_bearing_tower_l.stl
t_gantry_bearing_tower_r.stl
t_gantry_beartower_washer.stl
t_gantry_multi_l.stl
t_gantry_multi_r.stl
belt_crossing_bracket.stl
belt_tensioner.stl
bowden_tube_riser_guide.stl
t_gantry_8mm_clamp_l.stl
t_gantry_8mm_clamp_r.stl
xy_gantry_slider_washer.stl
xy_gantry_slider_block.stl
beltguides608.stl
bridgingfanmount.stl
Step 6: X-Y Motor Mounting
The X-Y motors are mounted as shown in the diagrams above, .stl files are also included. These will need to be printed with support, recommended infill % can be found in the tables found in previous steps. The motors used are the standard Nema 17 motors, and are fastened to the bracket using M3 hardware via the top 4 mounting holes.
- I recommend using 17 tooth, GT2 belt pulleys for these motors, however it is not necessary. A larger gear will allow faster X-Y movement, with a decrease in positional accuracy. A 17 tooth pulley seems to be working great on this printer.
Step 7: Assemble Z-Axis Components
The Z-Axis assembly is rather straightforward, you'll need the following parts (per side):
- (1) 5mm to 8mm Coupling
- (1) Nema 17 Motor
- (1) Lower Z Motor Mount bracket with mounting hardware for bracket
- (1) Upper Z Motor Mount bracket with mounting hardware for brackets and motor
- (1) 8mm x 457.2mm threaded rod
- (2) 8mm x 457.2mm smooth rod
- (4) "z_axis_8mm_clamp.stl" brackets
- (26) 10-24 machine screws (includes those required to mount components to frame)
- (2) "z_axis_crossbar_brace90.stl"
- (4) "z_axis_crossbar_brace_flat.stl"
- z-axis crossbar assembled (includes 1/4" threaded rod through center, secured using extrusions with nut profiles built in on the ends.)
- (1) "z_axis_bearing_guide.stl", houses 608 bearings to ensure the 8mm threaded rod stays in place and concentric with respect to the z-motor. There is room for two of these per side (for a total of 2 per side), however, the top one is a minimum if only using 1 per side.
- (1) 608 bearings, optionally you'll need 2 if you choose to use two of the z_axis_bearing_guides as discussed above,
-------------- Since originally posting this, I have made minor improvements on the Z-Motor bucket pieces. So if you've downloaded these by chance, the updated ones are slightly better. The Upper Z-Motor mount piece is now slotted to help align the motor vertically, and the lower piece will now sit flush on the table.
Attachments
Step 8: Assemble Heatbed Components
UPDATE: 10/18/2015: Another part which is now revised is part of the heatbed mounting system, I have strengthened the LM8UU bearing brackets slightly (although it wasn't crucial), and more importantly I have modified the brackets to house two LM8UU bearings each (versus 1). On top of those two changes, I have also narrowed the width of the bracket to increase clearance between the bed counterweight system weights, and added a mounting place for small bubble levels on each corner. So with that being said, I would recommend printing the new, revised brackets which house two bearings each. The new brackets are "HB_DUAL_LM8UU_BRACKET_MIRRORED.stl" and "HB_DUAL_LM8UU_BRACKET.stl". You will need to print two of each. Bubble levels are optional, but look cool (and of course, serve a purpose).
-The heatbed and components are assembled as shown. Please see the attached table for quantities required of the each component. There are also (3) 5/16" threaded rod sections to be utilized in this step as well. The hardware used in the "Frame" of the heatbed mounting system consists entirely of the 10-24 countersunk machine screws.
-The extrusions used consist of (8) pieces of the "Extrusion_W_nutend". There are no threaded rods through the center of the extrusions in this assembly.
-The extrusions are assembled in a manner shown, where the "nut block" end, faces outwards on the outside pieces, and faces inward on the inside pieces. Please refer to the illustration provided.
-The heatbed is fastened using (4) M3 x 35mm screws, with three washers per corner, and a single nut on the bottom to secure the bolt. The spring is placed between the bed and the bracket. I recommend using a spring which when compressed, measures roughly 20mm.
-The very outside corners of the heatbed system are the brackets which house the LM8UU bearings. These bearings should be placed on the smooth rod during the Z-Axis step, and should be secured in place using two small zip ties once the heatbed is placed inside of the main printer assembly.
- Springs for heatbed frame assembly connection at Z-axis. These should be roughly 30mm in length, with a 9-10mm inner diameter. The coil section will be around 1mm in diameter (pretty standard). These will mount inside of the z-axis threaded rod brackets, and serve to maintain a preload on the upper and lower 8mm nuts.
------------------------------------
- In an effort to help insulate heat on the upper bed surface, I recommend placing a cork sheet on the underside of the bed (12" x 12" sheet with corners cut to clear the springs). Although cork is highly temperature resistant, a sheet of kapton tape stuck to the top side of the cork will improve safety, while also further improving the heat deflection in the upward direction.
------------------------------------
- The heatbed should be covered with a suitable printing surface. I recommend buying a piece of glass (usually $2 or $3 from a hardware store that cuts glass), in the size of 11.75" x 11.75" x 1/8". The reason this isn't 12" x 12" is because of the corner bolt holes being occupied, you'll want the glass to sit flush on the heatbed. To attach the glass, the use of traditional office binder clips works terrific.
----------------------------------
If using an external heatbed relay similar to the one I have used, I recommend mounting it as shown with the included mounting bracket file "heatbed_relay_mount.stl". This allows you to remotely mount the heatbed relay, and keep it cool using a 40mm fan. The fan can be wired directly to the 12v, so that if the printer is on, the relay is being fan-cooled. The mounting bracket also ensures that the contacts on the under-side of the relay are insulated from short circuits (assuming you print this bracket using some sort of plastic).
No additional hardware is necessary besides the fan and a few zip ties. This mount works with the lower 1/4" crossbars which are also used to mount the RAMPS board and the PSU. Please see the attached pictures and .stl file if you choose to go this route.
Attachments
Step 9: Assemble Frame Braces
-This step of the assembly is dedicated to the frame braces, which will be the key component in stiffening the frame. I do not recommend skipping making these, as they are cheap to create, and add a great amount of overall strength to the frame.
-I have included rod lengths and pictures illustrating the assembly process.
-The first bracket shown (the one of the four without any text in the image), has two different rod lengths associated with it. The lengths are 210mm and 255mm. The longer length brackets are to be placed on the lower side of the frame on the front and back of the printer assembly.
-These are very straightforward, please see the pictures and rod lengths included for assembly. The .stl files are also included.
Step 10: Assemble Spool Holder
UPDATE: I have revised the spool holder for a much simpler design. I have kept the original design files here in case you prefer that one. The original one is generally speaking, more fancy. However, if swapping filament regularly, the new design beats it. I made the second spool holder version after using my new Rostock Max V2 Printer (where the design inspiration came from).
For the new version, you will still use the same two rods at 45 degree angles, and will need a 10-24 countersunk bolt as used elsewhere in the printer. The length can be anywhere from 1" to 1.5" for it to work. As far as printed parts, the second version utilizes two printed parts as seen in the photograph.
------------------------------------------------------------------------------------------------------
Assembly of the spool holder is rather straight forward, the pictures will illustrate most of what is required. The spool holder assembly requires the following:
- (2) 608 bearings, used in the tapered spool "cone" washers.
- (10) 5/16" nuts and washers
- (2) 5/16" threaded rods, cut to a length of 215mm (8.46"), for the spool holder frame mounting
- (1) 5/16" threaded rod, cut to a length of 170mm (6.69"), for the spool holder axis. Do not be afraid to cut this a little longer, the longer length will help with the variation in spool designs of filament coming from different vendors
The spool holder mounts as shown on the back side of the frame. Once assembled, the spool should be able to spin freely on the bearings. It is okay, and somewhat beneficial, to only tighten all of these nuts finger tight. This allows some freedom of movement when positioning the spool and spool mount assembly.
Step 11: Assemble Extruder
The extruder assembly shown features an easy-access filament section near the motor area. This aids in loading new filament. The bracket also features built-in filament guides, to keep the filament from wandering off of the path. Yet another feature of this, is a unique bowden tube clamping system. The bowden tube is secured in the bracket with the use of the "bowdentubeclamp" .stl file.
The parts and hardware required for this assembly are:
- (1) 608 bearing
- (1) Nema 17 Motor
- (1) bowden bearing I.D. reducer (.stl file)
- (3) 10-24 x 1.5" counter sunk machine screws. Two for the spring clamp, one for the lower pivot arm bolt.
- (2) suitable, small springs for the 10-24 springs listed above. These are used to provide compression between the hobbed gear/filament/bearing, yet also a little bit of forgiveness if needed or in the event of a jam.
- (1) 5mm I.D. Hobbed gear, to be mounted on the Nema 17 motor used
- (4) washers for 10-24 screws
- (3) 10-24 nuts
- (2) #6 x 1/2" machine screws, with one #6 nut per screw
- (1) #8 x 1" machine screw, for bearing axis. This works in conjunction with the bearing i.d. reducer, to effectively allow you to run a ~4mm bolt with the 8mm i.d. bearing (608).
- (2) washers for #8 bolt, along with (2) #8 nuts.
Step 12: Endstops, and Extending Stepper Motor, Endstop, and Heatbed Wiring
The endstops are to be installed in the positions as shown. The endstop mounts are for use with optical endstops, since these are what is included in a lot of Ramps electronics kits (what I bought, along with many others I saw).
-----------------
Extending wires
A downside to having such a large printer is that the electronic component wiring tends to be too short for proper routing of the wires. Fortunately, with the use of some standard 4-wire LED wire and a soldering iron, this isn't much of an issue to overcome. I recommend these wires be extended once the components locations are defined physically. In other words,It is extremely beneficial to have a 20ft length of 4 wire LED wiring on hand, and measure and cut the wires while holding whichever motor or endstop in position. This allows you to decide how you'd like to route the wires, and how much you'll need for the various wires being. As goes with any soldering and extending wires, I highly recommend the use of heatshrink around each individual solder joint, this will help prevent any accidental short circuits between nearby wires and connections.
---------------------
The wires which will need to be extended and routed are:
-The two X-Y motors located on the top, backside of the frame (4 wires each)
- The X,Y, and Z enstops (3 wires each)
- The Hotend wiring (2 wires, use at least 16 gauge wire for this)
- The Hotend Fan (2 wires)
- The Hotend Thermistor (2 wires)
- The Heatbed power wires (2 wires, at least 14 gauge wire here. Only need to extend by ~1 ft)
- The Heatbed thermistor wires (2 wires)
Step 13: Configure Your ATX Power Supply
If you decided to go with an ATX Power supply from a desktop PC, you'll need to do a few simple modifications in order for it to work properly with your printer. These modifications should be done at your own risk, and take note that these may void your warranty on the power supply from the manufacturer.
1.) Find the green (power on) wire in the main 20/24 pin harness, and either place a jumper wire or paper clip from this wire to any black (ground) wire. This is the wire that in a standard computer, tells the PSU to boot up and power on via the button located on the front of the computer case.
2.) Find the yellow (12v +) wires, and black (ground) wires. Now cut 6 of each of them near the connector end so you have plenty of wire to work with. Then, strip off a few mm of the wire insulation to expose the wire core.
That's about it, you'll have a whole mumbo-jumbo of wires to decide what to do with after that. I chose to neatly zip tie all of the wires, including the main harness with jumper installed, together.
--------------------------------
The wires will connect as follows:
-2 yellow into one socket of ramps board
-2 yellow into other socket of ramps board
-2 ground into one socket of ramps board
-2 ground into other socket of ramps board
-2 yellow into heatbed relay
-2 ground into heatbed relay
------------------------------------
The usage of an ATX power supply for 12v applications has been covered many times in great detail elseware. I recommend searching for guides if you're not familiar, however the details I have provided cover the basics of accomplishing this on your 3D printer.
Step 14: LCD Assembly, Ramps 1.4, and Endstops, Misc. Electronics
Due to the nature of wiring up the RAMPS board, I recommend utilizing one of many detailed guides online. This process is straightforward, and has been covered many of times elseware. I have provided a "truth table" of sorts, which I generated to troubleshoot the wrong motion coming from the CoreXY implementation running Marlin firmware. The "Connector Flipped" category, refers to the particular way I had my motors connected at the time. I should note that again, there is a pattern to the chart, however the orientation I assigned to "flipped" or "not flipped" may not be the same as yours. For reference, at the time of making the chart, I had assigned the left and right motor connectors as "not flipped" when the open end of the connector (the side where you can see the pins through the side), was facing the stepper motor heatsinks.
--------------------------------------------
The LCD Assembly used is the one which was included in my RAMPS kit which I had ordered from eBay. The LCD model number is 12864. The LCD Housing is printed in two parts. This allows you to hide wires inside of the box, and run the wires out the back side to the Ramps board. The two halves can be fastened together using zip ties (which is what I did), or, you could alternatively use m3 x 50mm hardware in the four holes. The screen utilizes a total of 8 spacers to keep it securely in place within the housing.
The "LCD_case_spacer_large" spacers, will go between the main bracket and the backside of the lcd screen (within the housing). The "LCD_case_spacer_small" spacers go between the front LCD case component, and the front of the lcd screen itself.
----------------------------------------------
The switches used are simple 3 wire, 12vdc switches from eBay. These are very easy to find, and can be purchased as a set of 4 for under $5. There is mounting for three switches in the housing, I recommend putting switches in all three, and then deciding how you'd like to make use of these. Some ideas are bed fans, bridging fans, and LED lighting for the printer.
A heatbed relay is required if using a 12" x 12" heatbed with the RAMPS board. This size of heatbed draws far too much amperage for the Ramps board to handle. Don't worry though, the wiring really isn't bad.
The idea behind a relay (in general) is that you're using a lighter duty circuit, to "flip the switch" on the larger circuit. With that being said, we'll apply it to the heatbed.
The heatbed used here draws approximately 20-24 amps during startup. The way this will be safely handled, is by hooking up the ramps heatbed output wires to the heatbed relay input wires. In a traditional setup, this would be the ramps board providing power to the heatbed itself. However, in our case here, the ramps board is simply "flipping the switch" inside of the relay, which in turn, will provide the heatbed with power.
The power for the heatbed will come directly from the power supply. The power supply is to be hooked up to the relay, as well as the heatbed. When the ramps board provides power, the heatbed relay will bridge the gap, connecting your heatbed to the power supply directly.... Pretty cool, right?
Depending on where you purchase the heatbed and relay, the wiring connection names may vary. Although the idea remains the same regarding the overall function, it is best to follow instructions or consult the manufacturer to ensure correct wiring.
-------------------------------------
The "lower frame crossbars" are used along with the 1/4" threaded rod (and hardware) to allow a place to mount electronics such as the power supply and RAMPS board. Please see the attached images for installation illustrations.
---------------------------------
LED Lighting (optional)
Parts Required:
- 12 VDC LED Strip Light, can be found on eBay for around $5 a pair. Commonly used as fog lights on cars, these measure roughly 170mm x 15mm x 3mm.
- (1) "led_mount_base.stl"
- (1) "led_mount_sec.stl"
- (1) #8 x 1" machine bolt
- (1) #8 nut
- (2) #8 washers
The installation is very straightforward, mounting pictures and assembly pictures can be seen in the included photos. For the wiring, I chose to utilize one of the switches (the second one from the top, next to the LCD). I wired through this switch, and to the power supply.
Attachments
lcd_screen_faceplate.stl
lower_frame_crossbar_brkt.stl
psu_mount_plate.stl
ramps_mount_plate.stl
lcd_screen_base.stl
y_endstop_flag.stl
y_endstop_mount.stl
z_endstop_bed_flag.stl
z_endstop_bed_main.stl
z_endstop_mount.stl
x_endstop_flag.stl
x_endstop_mount.stl
lcd_case_spacer_large.stl
lcd_case_spacer_small.stl
led_mount_base.stl
led_mount_sec.stl
Marlin Configuration Project Locus.txt
Step 15: Assemble Your Bed Lift Counter-Weight System (optional)
Due to the large heatbed size and mounting system, there is an undesirable axial load placed on the z-motors. Not only are we trying to save the motors, but being we're using a flexible coupling on the Z-motor, this could be a potential way to end up with some "z-wobble" in your prints. Thankfully, the Nema Motors are pretty tough, but we'll try and take a little stress off their task by adding some counter-weight assemblies. The use of counterweight systems is certainly not new technology. This type of system is used in other mechanical devices such as elevators and lift bridges.
----------------------------------
I was able to weigh my bed, mounting brackets, glass, etc (all of the components which cause downward weight on the motors), and came up with roughly 5.5 lbs total. To counter this weight on the motors, the counter-weight system was designed.
---------------------------------
The parts you'll need for this system are:
- (8) pieces of 18" long, 1/8" smooth steel rod (cheap hardware stuff works great)
- 14" of 1/4" automotive brake line, You'll need (8) pieces cut into 1.74" lengths (44.2mm)
- 36 steel plates cut to the dimensions provided in the drawing, these serve as the weights. I have also included the .stl file of what the weight plate should look like when done. If drilling holes by hand, this would serve as a great template.
- (16) "bed_lift_cableclamp.stl"
- (4) "bed_lift_pullmount.stl"
- (4) "bed_lift_guidebrkts.stl"
- (4) "bed_weights_shelltop.stl"
- (4) "bed_weights_oshell.stl"
- (4) "bed_lift_pulley.stl"
- (4) zip ties, these will be used to solidify the pulley mounting system by attaching the pulley mount to the frame braces via the bottom hole in the bracket.
- (4) 624 bearings
- (8) #8 x 1" screws with washers and nuts. These are used on the weightblock to hold the wire in place, as well as the pulley bearing axis. I recommend having an additional 8 washers so you can put a washer on the inside of the bracket between the bearing and the inner face of the bracket. This will keep the bearing from rubbing on the bracket.
- Picture hanging wire, youll need at least 12 feet of this. I recommend buying the clear plastic type vs. the steel cable for a more seamless look. Fishing wire may do the trick as well, however the clamping method which holds the wire (and support each weight box) will work better with a good surface to clamp onto.
- (32) #6 x 1/2" screws with washers and nuts. These are used along with the guide flange brackets and provide clamping force on the steel guide rails.
- (8) 10-24 counter sunk machine screws with nuts to secure pulley bracket to frame
---------------------------
1.) To assemble the weight box,
- Cut and Drill your steel weight plates (I recommend looking into local plasma cutting services), or buying a stick of steel that's 1" wide and 0.179" thick (7 gauge), and going from there. Alternatively, you could fill the box with a lot of little steel washers and try to pack them as tight as possible
- Install the brake line sections. The outer and top pieces of the box both have grooves in them to help maintain alignment of the brake lines, as well as the holes in which the steel rods will pass through.
-----------------------------------------
Installing the alignment rods (1/8" steel rods)
- This step is pretty straightforward, follow the pictures and you should be good to go. All of the hardware involved in clamping the rods is #6 hardware.
- I recommend installing the box at this point, and leaving the hanging cable at the box end unattached for the time being.
------------------------------------
Important note about installing the hanging cables. The hanging cable runs down through the center hole of the weight box. From here, it is important to route the wire strategically to maximize friction and minimize clamping force required from the screw and washer assembly. The holes to the left and right of the center "clamping screw" shown in the picture, located on the bottom of the box, are for routing purposes. I recommend running the cable up through one side, past and under the washer, down through the other hole, back under the other washer, and then tucking the cable, or cutting the excess length.
- This same cable wrapping technique applies to the clamp which installs on the bed.
--------------------------------
Setting the cable length
- To accommodate the variance in wire hanging sizes, different cable routings, etc, it is necessary to cut your cables to the correct length. To do this, I recommend the following:
- Install all brackets and hardware off of the printer
- Route cable through pulley assembly, and fasten the pulley assembly to frame using the two screw holes along with a zip tie in the bottom hole (should match up with your frame braces)
- Set your heatbed in it's home (highest) position.
- Hang the weight box as low as you're able to (without it resting on something), and secure using the cable routing techniques discussed.
- I have included a picture to illustrate how I determined where to set the rods in the brackets. Notice how I temporarily mounted the assembly on the outside of the frame, this makes it a lot easier once installing onto the inside of the printer rails. It is also beneficial to use something to rest the weight box on while working with the cable (so it is slack, I used a 2" clamp for this as shown).
----------------------
Finally, it is essential to ensure smooth operation of the weight assembly, and that it will not interfere or hit the heatbed components as it travels through it's min and max positions. This is an important and quick check to prevent any potential of components hanging up during a print larger than 5 (roughly halfway through the z motion when taking into consideration the height of the weighted box as well).
Notice how this system works in the picture where I have disconnected the Z-Axis Motors from the 8mm Threaded rod. As you can see, the bed is "floating" without any sort of support other than the counterweights. This serves as a visual aid to help understand how this system is truly helping. This also makes removing components such as the 8mm threaded rods much easier.
Attachments
Step 16: Print Some Stuff!
Congratulations! You've created your first "Project Locus" Printer build. Now it's time to show off your bigger, 3d printed printer, and put even more meaning behind the idea of a self replicating machine! This printer is not only a proof of concept that you can create a printer of such size while using printed parts, it is also a great showcase piece for the evolution of additive manufacturing and a compliment to the rapid prototyping industry!
Print on, thinkers, tinkerers, makers, fabricators, and everyone else! I look forward to seeing what other additions people will create for and with this newly released printer! I hope you all have enjoyed this build, happy printing!
Thank you for visiting and reading this instructable!
- Pat L.
P.S. I have attached a video as well so you can really see what this printer is capable of thus far. Keep in mind I just finished building this in May 2015, so I'm sure faster speeds will come!.
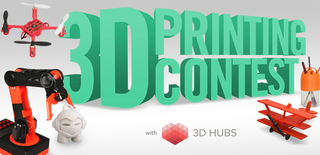
First Prize in the
3D Printing Contest