Introduction: How to Cut Dovetails by Hand - No Jigs
Dovetails have an air of mystery about them. They're aesthetically pleasing and revered over who can cut them the cleanest and whether or not they are machined or done by hand. A lot of folks even have bragging rights over using jigs or doing it free hand (I'm one of those folks).
To be quite honest, it's only in the past fifty years or so that dovetails have become more of an aesthetic option. Dovetails for generations were done for speed and strength, not for looks. This joint is not only mechanically strong in and of itself, but bears a ton of edge to edge glue surface that allows for great strength.
I do want to be clear about one thing before you dive into this article: the end result is really what matters. Whether you use jigs or not, whether you clear waste with a router, chisel, or a coping saw, whatever it is that you do to dovetail, the end result is ALL that matters.
With all that being said, free hand dovetailing does create some advantages. You can adjust your ratio and your tails at will. You can vary the size of your tails and pins on the fly. You can do things that just aren't available with a router jig or other more automated tool. Furthermore, you really get to develop your hand tool skills and get the quality muscle memory and feel for sawing, chiseling, and assembly. In my opinion, there are few better tests of hand tool skills than free hand cutting dovetails. So if you're up for a challenge, challenge yourself.
Supplies
Mandatory Dovetailing Supplies:
Dovetail Saw (Western Backsaw or Japanese Pull Saw)
Dividers (Two is optional, which I prefer)
Marking Gauge (Two marking gauges is helpful at times too and also optional)
Coping or Fret Saw
Sharp Chisels
Something to Knock said Sharp Chisels
Marking Knife or Sharp Blade (Razor Blade or Box Cutter Works)
Optional Dovetailing Supplies:
Layout Board (I use the bench hook of my shooting board)
Low Angle Jack Plane and Low Angle Block Plane
Medium or Fine File or Rasp (A knife file is amazing without teeth on the edge. I don't own one yet but it's on the wish list.)
Painters Tape
Dovetail Marker or Sliding Bevel Gauge
Paraffin Wax (Great for saws... I actually even use mine on the fret saw... and plane soles)
Step 1: Laying Out Tails
In my opinion, laying out dovetails is if not the most crucial step, a very close second. First of all, your tail board is the one that doesn't have the half pins on the ends. You cut those off. This board will be hugged so to speak by your pin board and be pushed into that board's sockets.
A good foundation is key so start with square and surfaced stock. Most folks will finish plane these down by hand which is what I do as well. I start with the tail boards first and I want to figure out how big I want the half pins to be. As mentioned, those are the little guys on the left and right ends of your end grain. Once I establish that, I use the divider to indent on either side. I prefer little bitty pins but my marking knife is a bit thick so I try to keep my pins at about 3/4 inch at it's widest point. If you have a thinner blade, you can certainly go smaller. Just keep in mind you'll have to saw and chisel these out as well.
With my other set of dividers, I’m going to walk across the width of the board twice for two tails. The idea here is that I want the distance between my half pin mark and the end of my divider off the board to be about one full pin. Once I get that right, I’m going to indent across the board one way starting from my first half pin, and then walk it back the other way from the opposing half pin indent.
With the marking knife, I put the knife point in the indent and then slide the square up to it and strike the line. I then go back and trace them in with a pencil so I can see them better. I've made a habit of sliding my measuring device up to my marking device, whether it a knife, scratch awl, or a pencil because it ensures accuracy. This is something you can take with you to other projects that don't involve dovetails.
The marking gauge will set the base lines for your pins and tails so since we’re doing tails first, I’ll set the marking gauge off my pin boards and strike the base line on all four sides of the tail board and both ends.
If you don’t have a dovetail marker you can use a bevel gauge as an alternative. I use the Rob Cosman marker and it’s got two ratios on it, one for soft and the other for hard wood. Again, slide the marker up to your pencil which is nesting in your marking knife line, then strike your line. Then I go ahead and mark out waste with an X. You can mark it out however you like. Just make sure it's marked.
Step 2: Sawing Your Tails
Before sawing, I hit the saw plate with some paraffin wax. You can get a lifetime supply of this stuff at your local Walmart for about three dollars and it it’s great for planes and saws alike. It helps reduce friction and the wax doesn't affect your material at all.
My sawing technique still needs plenty of work but I start by putting my thumbnail in the marking knife line and setting the saw kerf into what will be the waste. My thumbnail acts as a fence for the saw plate and allows for me to stay just off my line and just perfectly into my waste. I also do some little tiny back and forth strokes to make sure that the saw is started before I get into full push strokes. Loose grip and more of an across instead of a downward motion help immensely.
You want to saw down to your baseline, but keep an eye on the back of your board to make sure you don’t cross accidentally on the other side. I’m also right handed and prefer to only cut the right sided lines so I’ll flip the board and come from the other side to complete the tails. Slower deliberate cuts will serve your well and allow the saw to take more material with each stroke.
You may notice that I'm clamping two boards in the vise at once. I'm clamping both the tail boards, and I'll do the same with the pin boards, in an effort to keep the vise from racking. This makes sure that even on this crappy, rickety, hand me down bench, my work is secure in the vise.
I don’t remember where I learned this little trick with the chisel, but I shimmy off my base line for the half pins, and then chop down to create a kerf track to saw out the half pins. This allows me to rest the saw right into the void in an effort to stay away from the base line and keep square at the base of the half pin. I then take a chisel to pare down to the line. I find it easier to slice across the end grain instead of coming perpendicular into it, a common practice with chisels but it still needs mentioning.
Then onto the fret saw. As I said earlier, a fret saw will allow you to get extremely close to the baseline. I still have a bad habit of tilting my saw so that the cut is higher on the back side of the cut. However, that’s certainly better than being too low and crossing your baseline, which is largely unforgiveable.
Step 3: Chopping Tail Waste and Laying Out Pins
Start chiseling out your waste. Sneak up on your baseline, go halfway down, and then flip your board and work from the other side. I also chop a bit of a vee into the waste area. Essentially, if you're looking into your waste from one face across to the other, you want the remaining area to be shaped like a bit of a distended "M" with the peaks of the M being the baselines. This will allow your tails and pins to settle all the way to the baseline. A lot of folks tend to leave a little hump or obsess over getting it dead flat on the baseline. Protect your baseline, but the material between the baselines is largely irrelevant.
I clean up all my tails with the chisel just to get rid of some of the saw marks and make everything look a little smoother before transferring to the pin board. I mark the pin board off the tail board with the marking gauge. However, I’m only striking lines on the faces of the pin board, not the whole way around. I then go ahead and tape off the ends of the pin board before transferring the layout of the tails onto the pin board. I use my shooting board as a layout board and that helps keep everything stable when marking. Once again, I’m striking these layout lines with a marking knife.
Once the lines are cut, I’ll peel out the waste areas so that the blue clearly delineates what I’m keeping and whats my waste.
Step 4: Sawing Pins and Chopping Pin Waste
Back to sawing. The face lines on pins go straight down so sawing plumb is key. I am not the best at sawing plumb. However, if you are going to get stray, just don’t cross your layout lines into your pin, drift into your waste area instead. Because of my technique and my extreme right handedness, most of my error tends to lean in the same direction. I would say that if you are going to have some mistakes that are fixable, at least be consistent with the mistake so that the technique to remedy is consistent as well.
After the fret saw, it’s chopping out the remaining waste, much like you did on the tails. I like to start on the narrow side of the pin first with a chisel close to the width of the socket. Once again take light passes working up until your base line and undercut the socket as previously described, the elongated "M" is a good visualization. Then when you flip it, angle the chisel to try to avoid bruising the pins. Using a smaller chisel there helps as well.
When it comes to paring pins, one thing to note here is that I should probably be taking a lighter pass with the chisel. I was really living dangerously with my layout lines for the pins and the last thing you want to do is cross those on your pins because that’s how you end up with gaps during the fit.
Step 5: Test Fitting and Glue Up
Test fitting is extremely important when it comes to dovetailing. If it doesn't fit off the saw, diagnosing your problem areas is just as important as being good at trimming down your components. I line the pieces up starting from what will be the base of my box and then analyze whether the fit is loose or tight toward the front or the back and try and identify where material needs to be removed. If I've brought the material on the pin board down to the layout lines, I'll start working on the tails a touch to further clean them up. Be patient and be deliberate.
For the love of God DO NOT force boards together. Smashing them with a joiners mallet to get them to fit is only going to encourage splits and catastrophe. If it doesn't fit smoothly, take them apart and work the problem areas again. A little snug isn't a problem, but too snug will cause a split, likely down your pin board.
After everything is cut and fit, I like to give everything a light planing before glue up. Don’t go too heavy here and make sure to keep everything flat and square. I’m using a fifty degree iron for the rosewood which is prone to tear out and that also works plenty fine on the mahogany.
For the glue up itself, I really focus on the pin boards. I apply glue to what will be the three covered sides of the pin, spread, and fit. It's a good idea to have all your corners labeled, "A" tail end to "A" pin end, and so on and so forth. In more complicated glue ups, I've even drawn an arrow to figure out which way is up as you can get pretty bogged down trying to orient everything. I throw a couple clamps on after the glue is dry and don't apply a lot of force through the clamp. I'll also go and clean up squeeze out with a wet rag.
Low angle block plane to flush up the proud pins and tails and then a bit of collected sawdust over the top of some glue rubbed into the gaps to fill everything nicely.
Step 6: Some Troubleshooting and Review
If you don't clean up your tails well, sometimes you can see a bit of a squirrley line on your finished product. I will always fill in the gap with sawdust from the wood species of whatever the exposed end grain is. So since I'm working with two species here, where there's rosewood end grain exposed, I use that sawdust. Where there's mahogany sawdust showing, I use that species sawdust.
If you have a gap that is about a 32nd or an inch or smaller, you can sometimes solve the problem with strategic planing. Plane with a low angle plane or even a smoother from the outside of your end grain toward the problem area. What you're aiming for is to blow out the back of the end grain into the gap to bridge the gap so to speak. If you're lucky and you're doing this before the glue is fully cured, you might get away purely with that. If the glue is already cured, just add a little more glue and sawdust over that and a light sand should clean that up nicely.
DO NOT use thin CA glue on end grain for dovetails. No matter what you do, and I have literally tried damn near everything, it's practically impossible to get out. It will blend a bit with finish but it won't be perfect, and perfect is what we're going for. If you have to use CA glue to fix blow out or chip out, use a medium or thick, so that it can be blended in appropriately.
Step 7: Celebrate, Rejoice, Practice
You're done! You're killing it. However, what's important to note with dovetails is that practice is incredibly important. I get incredibly lucky the other day and after not having done dovetails for a while managed to bang out a tray with some perfectly serviceable ones. However, if you want to get better, and build that muscle memory, you should be practicing regularly. The most returns you'll get from practice is sawing practice. Practice sawing technique, experiment, and learn.
If you have any dovetail questions, or additional tips and tricks, let me know in the comments below. Be sure to watch the video and subscribe to my channel if you like what I'm pitching. As always have fun and keep making cool stuff!
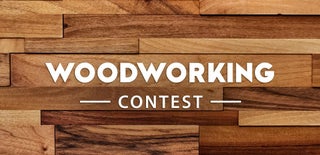
Participated in the
Woodworking Contest