Introduction: How to Make 400Watt Brushless Mini Sumo
This instructable is 18+ category in contest and will show you how to make a Mini sumo using brushless motors and brushless ESC's:
First of all, this project was a true challenge for me to fit all componenets in 10x10 cm projection area and not exceeding the 500gr weight limit. Because of its speed and power I call it Mach 1.0, pretty cool name huh? :)
Weight is an another issue when it comes to mini-sumo's. Every component used in project are precisley weighed before adding them to bot.
There is no gearbox on motors unlike nearly all of the entarants in robot contests do. That makes this bot unique and extraordinary.
Anyway this is enough for praising part, let's get it started.
For more info you can take a look at my blog: www.ceyhunderinbogaz.com
First of all, this project was a true challenge for me to fit all componenets in 10x10 cm projection area and not exceeding the 500gr weight limit. Because of its speed and power I call it Mach 1.0, pretty cool name huh? :)
Weight is an another issue when it comes to mini-sumo's. Every component used in project are precisley weighed before adding them to bot.
There is no gearbox on motors unlike nearly all of the entarants in robot contests do. That makes this bot unique and extraordinary.
Anyway this is enough for praising part, let's get it started.
For more info you can take a look at my blog: www.ceyhunderinbogaz.com
Step 1: Parts and Tools
Making the bot was easy, hardest part was finding the money and time for this project.
When it comes to Brushless technology, you need a thick wallet with nice green papers in it.
Luckily our Chinese friends working hard to make this parts cheaper every day.
PARTS:
2x Turnigy 35AMP CAR ESC
2x NTM 910KV outrunner Brushless motor
1x Turnigy Nano-tech 1300mAh 25-50c Li-po
1x Arduino Duemilanove
1x Laser cutted Bot frame
2x Ultrasonic Sensors for opponent sensing
2x QRD1114 contrast sensors
Total cost is approximately 150$
When it comes to Brushless technology, you need a thick wallet with nice green papers in it.
Luckily our Chinese friends working hard to make this parts cheaper every day.
PARTS:
2x Turnigy 35AMP CAR ESC
2x NTM 910KV outrunner Brushless motor
1x Turnigy Nano-tech 1300mAh 25-50c Li-po
1x Arduino Duemilanove
1x Laser cutted Bot frame
2x Ultrasonic Sensors for opponent sensing
2x QRD1114 contrast sensors
Total cost is approximately 150$
Step 2: Making the Frame
For this step, you got to have access to a laser cutter. You can find corel draw files which will be needed for laser cutting.
In first version of the bot, it was made from balsa to ensure lightness. But while testing the bot using 4-channel remote controller, the destruction happened in seconds and motors was flying in the air :). So if you don't know how to reinforce frame using fibreglass don't use this method
For motor mounts you are going to need a L-shaped aluminum profile. This things are easily available in Karakoy if you are living in Istanbul.
Cut the L-profiles about 5cm long and then mark the drilling points using motor mounts, then drill the holes with a 3mm drill bit.
After mounting motors on the profile, this mark holes using profiles and drill both profile and acrylic glass.
In first version of the bot, it was made from balsa to ensure lightness. But while testing the bot using 4-channel remote controller, the destruction happened in seconds and motors was flying in the air :). So if you don't know how to reinforce frame using fibreglass don't use this method
For motor mounts you are going to need a L-shaped aluminum profile. This things are easily available in Karakoy if you are living in Istanbul.
Cut the L-profiles about 5cm long and then mark the drilling points using motor mounts, then drill the holes with a 3mm drill bit.
After mounting motors on the profile, this mark holes using profiles and drill both profile and acrylic glass.
Step 3: Making the Tires for Direct Driven Motors
In first run I used anti slip mats from 3M and 1 directly glued them onto the motors.
For a normal bot the idea should work fine( The traction is the best amongst all other materials, cause it is made to be ANTI SLIP!)
But for a beast like this with 18000rpm the problem is it is not durable enough with brushless motors.
So I decided to use another material called EVA. I don't know what does it mean but it is more like a super computer name :)
Cut a piece of EVA to wrap it around the motor. After measuring tire piece, use 5-minute epoxy to glue it around the motor.
These tires are very durable if you used epoxy glue. Traction is not good as Anti-slip mats but enough for killing some bots in the ring :)
For a normal bot the idea should work fine( The traction is the best amongst all other materials, cause it is made to be ANTI SLIP!)
But for a beast like this with 18000rpm the problem is it is not durable enough with brushless motors.
So I decided to use another material called EVA. I don't know what does it mean but it is more like a super computer name :)
Cut a piece of EVA to wrap it around the motor. After measuring tire piece, use 5-minute epoxy to glue it around the motor.
These tires are very durable if you used epoxy glue. Traction is not good as Anti-slip mats but enough for killing some bots in the ring :)
Step 4: Placing Components
The rectangle in the middle of the chassis is used for placing the ESC, just behind these two esc's it is possible to mount Li-Po
using cable ties. Same goes for the arduino too. I didn't have time to o make a special place for it, just use cable ties to secure it onto battery.
Ultrasonic sensors are placed onto a laser cutted plexiglass and the plexi is glued onto the chassis.
Photos must give a clue about placing.
using cable ties. Same goes for the arduino too. I didn't have time to o make a special place for it, just use cable ties to secure it onto battery.
Ultrasonic sensors are placed onto a laser cutted plexiglass and the plexi is glued onto the chassis.
Photos must give a clue about placing.
Step 5: Contrast Sensors
As many robot hobbyist use cny-70's, be different and buy some qrd114 for better sensing and better daylight filter.
There is 2 little rectangles on the chassis for qrd1114 sensors. They will fit very well in place but you can also add some glue on it to make sure it is safe.
Connect the sensors according to the schema.
There is 2 little rectangles on the chassis for qrd1114 sensors. They will fit very well in place but you can also add some glue on it to make sure it is safe.
Connect the sensors according to the schema.
Step 6: How to Control ESC With Arduino
With built in functions of arduino, It is a piece of cake to control ESC's.
Basically ESC are designed to work with remote controllers using PPM protocol. PPM protocol is a pwm wave at 50hz frequency.
By changing the duty cycle of this Pwm wave, different speeds and directions are achieved.
There is a picture below to make it understand how PPM works.
Arduino can generate servo signals with servo function.
This function sets the angle of servo with values 0 to 180
This angle information interpreted in ESC as:
Degree 0............90.............180
Speed -%100...........%0............+%100 (- and + shows the direction of motor)
Basically ESC are designed to work with remote controllers using PPM protocol. PPM protocol is a pwm wave at 50hz frequency.
By changing the duty cycle of this Pwm wave, different speeds and directions are achieved.
There is a picture below to make it understand how PPM works.
Arduino can generate servo signals with servo function.
This function sets the angle of servo with values 0 to 180
This angle information interpreted in ESC as:
Degree 0............90.............180
Speed -%100...........%0............+%100 (- and + shows the direction of motor)
Step 7: Make You Own Algorithm
Sorry about not publishing the source code but it is very easy to implement sumo algorithm.
You have everything to start knocking your opponents.
Thanks for reading, more to come at www.ceyhunderinbogaz.com
You have everything to start knocking your opponents.
Thanks for reading, more to come at www.ceyhunderinbogaz.com
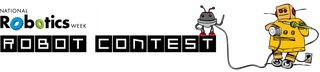
Finalist in the
National Robotics Week Robot Contest
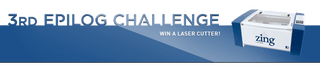
Participated in the
3rd Epilog Challenge
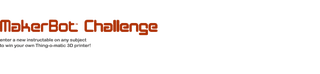
Participated in the
MakerBot Challenge