Introduction: How to Make Four (Awesome) Wooden Swords From a Single 2X4
Ever since I was a kid, I've always liked toy swords. When I was younger my parents once bought me a "Roman Gladiator" set that was made out of hollow plastic. It was highly decorative, but not very durable. I think it took me about 15 minutes to break it. (Sad face.) Of course, back then, parents were different than they are now.
Dad: "You broke it already?!"
Me (blubbering): "Ye-eah-ah-ah"
Dad: "I told you not to hit stuff with it."
Me (blubbering, still): "Bu-uh-uh-ut, it's a sword! You're a-sposta hi-i-it things with it."
Dad: "Well, it's not a sword anymore. It's pieces of a sword. Maybe I'll fix it later."
He did. He slid a piece of wood inside the hollow part of the sword and secured it with some screws. "My God, this man is a GENIUS! Is there anything he can't do?!" I thought to myself. "He made it STRONGER!" I spent many happy days wandering around the house banging it on things I wasn't supposed to. As I did, I thought to myself: Why didn't they make the toy out of wood in the first place?
Little did I know.
Now, I'm a grown up (on paper) *and* I have tools. So... WOODEN SWORDS IT SHALL BE FOR ME AND MY CHILD!
(Huzzah!)
Step 1: Get the Necessary Tools and Materials Together!
What I started with were the best quality 2X4s I could find at the local "big box" hardware store. For this particular project, untreated pine was used. I wanted to make good length, two-handed swords for myself and my kid to play with. That meant I had to buy 10 foot long 2X4s, rather than the less expensive 8 foot 2X4s. I think the difference in price is about $2 per board. (No biggie.)
Before we get into the the good stuff, it's probably best to provide you with a list of the tools and supplies I used for this particular build. They were:
- Table Saw
Note: I used a crosscut sled during this build. You can do the job without one, but having a sled makes several of the steps a whole lot easier. Sleds are usually something you have to build for yourself. If you would like to build one for your particular table saw, I recommend you check out this instructable posted by KentM.
- 9" Band Saw
- A wood lathe capable of handling 46" long stock
Note: I understand a lot of people won't have this particular tool in their arsenal. That makes this one of those instructables where you can think to yourself "Darn it! If I don't have that tool, I can't do this project! Not true! Get creative. You can achieve great results from careful carving, leather wrapping, or using a router. The lathe is only used to establish the *look* I was going for on the grip.
- A Small Combination Square
- Hand Drill
- Random Orbital Sander
- A Handsaw with a very narrow Kerf
- A Miter Saw
Of course there are other things that most every shop will have. Painters tape. Pencil. Calipers. That kind of stuff.
Step 2: Let's Name the Parts of the Sword, So You Know What I'm Talking About As I Describe Them.
Picture is pretty self explanatory. For this build, I'm not doing anything "super fancy" with the blade. No edges. No central ridge. No fuller. They aren't necessary. They might LOOK cool, but here's the thing: They make the sword weaker.
What we used on this build was pine. Pine is soft. It's also relatively light. When you bang these swords on things, they are GOING to dent. The thinner you make the blade, the more likely that they will splinter. If these were to be made of a denser wood (like Hickory) you could have a ball with making the blade look amazing and probably be okay.
Also... The point of the fuller on a sword blade was to reduce the weight of the blade by removing unnecessary material. It also served as a structural component to the sword. We're not worried about that.
Step 3: Cut the 2X4 Into the Appropriately Sized Chunks.
Cutting to length:
Take your raw 2X4 over to the miter saw and give yourself board lengths as follows:
- Two lengths of 46" (which will be used to make the grip and the blade)
- Two lengths of ~8" (which will be used to make the cross guard and the rain guard)
Save your scraps so that you can later cut out the pommels.
Cutting to thickness:
Use table saw to rip the lengths of 2X4 down to 1 1/2" x 1 1/2" blanks.
Marking up the blanks.
Take a look at your blanks. Inspect thoroughly for splits in the wood, chips, problematic knots, etc. Then get out your pencil.
I wanted my swords to be two-handed, so I needed to measure off enough space that both my hands could fit. I knew I was going to be using my lathe, so some of the wood near the bottom of the grip was going to have to be sacrificed. Here were my measurements from base of the sword to the tip of the sword:
- 1" from base (cutoff portion)
- 10" for the handle
- 1 1/2" for the cross guard
- Whatever is left becomes the blade length.
(Carry all your marks all the way around the blank, so that it's marked on all sides)
Then you have to decide how thick you want the blade to be. I wanted them to be strong, so I went with 1/2". You can go thinner than that... but it won't be as durable.
I made "X" marks on the ends of each blank to make it easy to align my lathe spindles. The more precise you are with this, the more perfectly centered the grip will be.
Step 4: Turn the Grips
I happened to have a grip I had made for another project, which gave me the look and thickness I wanted for my swords. I took measurements off of it using my calipers and got to turning. With freshly sharpened knives it took about 45 minutes to make all four grips.
Now, the nice thing about using a lathe is that it (pretty much automatically) allows for you to find the dead center of whatever piece of stock you're working on. That's information we're going to need to know when it comes time for us to attach our pommel, toward the end of the build. Unfortunately, the part of the stock that has lathe marks on it is going to have to be cut off (for aesthetic reasons), so we have to carry those marks all the way through. The easiest way to do that is to use the spindle mark as a guide, and to drill down into the base of the grip. Make sure you go deep enough that when you cut the base off, the hole will still be there.
Once you've drilled all of them, take the blanks to the miter saw and cut them off.
Step 5: Rip the Blades Down to the Appropriate Thickness
There are a bunch of different ways to handle this part of the job. Some would say that the easiest and cleanest is to use your band saw. Those people are probably correct... However! My band saw blade was dull at the time... so I used my table saw.
Remember: Our stock is 1 1/2" thick. I want to preserve the center 1/2" of it and get rid of the rest. That meant setting my rip fence on the table saw so that the LEFT edge of the blade follows my line.
Here's the bad part about using a table saw for this: The blade is circular. That means the cut on the underside of the wood is going to go farther than what you see on the top side. Here's the good news! With a 10" table saw blade, that difference between the depth of the cut at the top and the depth of the cut at the bottom is about 1:1, proportional to the thickness of the wood you're cutting. (This is a complicated way of saying that, if you're cutting wood that's 1 1/2" thick on a table saw, the cut on the bottom of the stock is going to be about 1 1/2" farther into the wood than the cut on the top.)
It's the little things that make a plan come together: We already marked the space for the cross guard to be 1 1/2". So, all you have to do is stop cutting when you see your table saw blade hit that mark (like in the picture).
Then all you have to do is finish up your cuts with a hand saw. Make the cuts as flush as you can.
Step 6: Shape the Sword Points
The first step of making the point of the sword is to cut off the portion that's been marred by the lathe spindle. The objective with that is to remove as little material as possible (usually about 3/8").
Once that's done, you have some aesthetic decisions to make. What kind of point do you want your sword to have? For little (really young) kids, a rounded point might be appropriate. My son is almost 12, so he can handle a bit of danger (knock on wood). I opted to go with ~15 degree point.
Mark the blade three inches down from the end. Find the center of the blade. Draw yourself a triangle and make the appropriate cuts.
Once this step is done, you can set the piece off to the side. It's time to start working on the cross guard!
Step 7: Make Your Cross Guards
Creativity can definitely come into play on this part of the build. Your cross guard can look pretty much however you want it to look. I wanted it to be appropriately wide in comparison to the length of the blade, and symmetrical.
Take the pieces of 8" x 1 1/2" x 1 1/2" in stock you made in the earlier step, and find the center. Use your combination square to measure off 3/4" to the left and right of that center mark to account for the way the cross grip will eventually mount to the blade.
Then do whatever you want to do with it.
I used a french curve to make sure that I had a pleasing shape. Then I took it over to the band saw and carved it out. (You could also do it with a jig saw.) I gave the piece a quick sanding to clean up the edges, and then I used it as a template for the other three pieces.
Once they cross guards are all cut out, do yourself a favor: Mark them on the left and right (like I did in the pictures). In a moment, you're going to cut them down the middle.
I don't care how good you are, you will NOT manufacture all of these to be perfect copies of each other without a bunch of tools I didn't list for this build. Marking them keeps you from confusing yourself with mixing and matching.
Set your table saw fence to rip each cross guard down the middle as precisely as possible, making sure to account for the thickness of the table saw blade. My blade kerf is about 1/8". That means the center 1/8" of material is removed as a result of the cut. End result: The assembled cross guard will be 1 3/8" at its thickest point.
Once the cross guard pieces are cut down the middle, I chose to taper the ends. I just built myself a simple 15 degree crosscut jig.
Note: I saved the little pieces that were cut off the cross guard via the jig and used them as my rain guards.
Step 8: Mounting the Cross Guard to the Sword
This step requires more precision than the previous steps. You have to carve out a slot in the cross guard that fits snuggly around the blade. Every one of the blade/cross guard combinations is going to be slightly different, so each one is going to require a little bit of finesse.
Start by marking the center of the cross guard and the flat of the blade. Trace the edges and mark the material you need to remove.
Measure the precise thickness of the blade. In the picture, you'll see that it's *exactly* 5/8". Half of that is 5/16". That means you need to remove 5/16" worth of material from each cross guard piece. The left and right edges of the groove are easy to find. The tough part is getting the cutting depth to be *exactly* right. I recommend using the combination square to set the height of the table saw blade to a teensie bit LESS than 5/16" and gradually increase it until you get it *perfect*.
Once you're done with both sides of the cross guard, marry the pieces up around the blade. Glue it. Clamp it. Let it sit.
While it's drying, figure out what you want to do for a pommel. I chose to cut a circle out of the leftover pieces of 2x4. Once the glue was dry, I drilled out space in the pommel and the grip for for a dowel rod and joined the pieces together.
Step 9: You're Done! Decorate Accordingly!
Shown are the swords with varying levels of decoration. You can leave them plain. You can stain them. You can paint them. I even went out at got some plastic jewels from the local craft store.
Those that are painted are coated in Rustoleum Hammered Finish paint. I find it makes them look more like real metal. Just make sure that if you *do* paint them, you do a clear coat finish (like Modge Podge Hard Coat) to keep them looking good.
Have fun!
Edit: On the unfinished swords, you may have noticed that I drilled a hole through the cross guards and filled it in with a piece of 1/2" dowel. That's a structural thing, but it may not be the kind you're thinking.
It's to make the sword WEAKER.
Like I said, I have an 11 year old son. He's able to handle *some* danger, but he's also big enough that if he really gives something a good whack with this thing it's going to cause some damage. Drilling that dowel and then gluing it into place effectively creates a breaking point in the sword. It takes the 1 1/2" wide by 1/2" thick stick and splits it (structurally) in the middle. I *want* these swords to break if they're not being used in the way I intended for them to be used. That little modification helps to ensure that a toy can't be used as a weapon... or if it *is* used as a weapon, it's only ONCE.
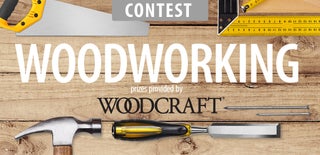
Participated in the
Woodworking Contest 2017