Introduction: How to Make a Concrete Countertop for Your Sink
Making a concrete sink is easy, and fairly inexpensive. Most of the materials for making the mold can be found as scrap pieces from old furniture. This project can be done under 100$, and is worth every dollar because it will make you feel REALLY good about yourself every time you use it.
Step 1: Taking Mesurements
First I removed everything from atop your old sink countertop, along with faucets and drain stopper. Then I used some tracing paper, and, Indiana Jones style, rubbed the outlines of all the holes. After doing this, I "expanded" the holes by just a hair (1/16th on an inch) on my drawing, to make sure that everything fits into the holes (yet still get covered up by the hardware removed), and i wouldn't have to do any concrete grinding after it's all poured. Many sources like CHENG Concrete and Expressions-LTD sell rubber plugs to me these holes even more effortlessly.
I then cut out all of the holes from my template and cut up some wood to make the mold. It is recommended that you use smooth surfaced material to make your mold, mine had a little texture in it to help me replicate a wood finish on my final product. I then sealed the corners with some caulk. The height of my new countertop was 2" as recommended as the minimum on the concrete I used. I had then traced all other markings from my template to the bottom of the wood, so I could add my mold forms for all my holes.
(I was making two sink countertops, in case I didn't like the first one, that's why there are two molds)
I then cut out all of the holes from my template and cut up some wood to make the mold. It is recommended that you use smooth surfaced material to make your mold, mine had a little texture in it to help me replicate a wood finish on my final product. I then sealed the corners with some caulk. The height of my new countertop was 2" as recommended as the minimum on the concrete I used. I had then traced all other markings from my template to the bottom of the wood, so I could add my mold forms for all my holes.
(I was making two sink countertops, in case I didn't like the first one, that's why there are two molds)
Step 2: Adding Mold Forms
It doesn't matter what material you use for the forms so long as it is strong enough to keep the concrete away from those areas. CHENG CONCRETE and Expressions LTD sell rubber mold forms that will definitely save time on convenience.
I used some dowel stock with tape on it for the faucet holes, a CRAZY glue stick shell for the stopper hole, and some foam I found across the street from a gallery show. I cut the foam with a paper clip, i kept reheating over fire. These mold can be done more precisely, however going into this i knew that the lips on my bath sink hardware were forgiving enough to cover all the rough edges.
I used some dowel stock with tape on it for the faucet holes, a CRAZY glue stick shell for the stopper hole, and some foam I found across the street from a gallery show. I cut the foam with a paper clip, i kept reheating over fire. These mold can be done more precisely, however going into this i knew that the lips on my bath sink hardware were forgiving enough to cover all the rough edges.
Step 3: Reinforcing Skeleton
Because the concrete layer will be so thin, I decided to put some steel rods in it, that I tied together with steel wire, all of which were gathered from different building sites garbage piles.
Step 4: Buying Concrete, and Pouring
After some research I decided to go with the Quikrete 5000 concrete mix. It holds up when poured in 2" or more, dries relatively fast and seems to be what professionals mostly use for interior applications such as this. I followed the instructions on the bag, and the mixed turned out fairly nice. However I applied a little more water later, which I don't regret doing. To pour two of these molds and a 5-10 pound lifting weight for my girlfriend, I used up all of the 80 pound bag.
After every mold is poured, it is important to remove the bubbles from the mixture. I used a sander with no sanding pad on it, and applied it's vibrations to the perimeter of mold multiple times around.
After every mold is poured, it is important to remove the bubbles from the mixture. I used a sander with no sanding pad on it, and applied it's vibrations to the perimeter of mold multiple times around.
Step 5: Leaving the Project to Dry
After I poured the concrete, I applied moisture onto the concrete and sealed it into a plastic tarp to prevent moisture from escaping. I left the mold this way for 13 days, applying a couple of sprays of water on each mold every other day during these two weeks.
Step 6: Filling in Imperfections With Concrete Slurry and Sanding
Concrete slurry is easy to make and is inexpensive. I gathered up whatever remaining concrete powder (which i seethed), about one and a half or two cups, and mixed it with a CAPFUL of concrete bonding mix (11 dollars for a gallon at Home Depot) and some water. Goal was to make it similar in consistency to a soft serve ice cream. After that I just put on my surgical gloves and massaged this mix into any bubble holes I saw.
Sanding was the worst part of the job. Unless you have a polishing grinder/grinder, you will have to spend a lot of time sanding this by hand. Professionals go through a whole set of grits from 100 to 3000, while I just used the ones I had at home. I had an 80 to finish up the roughness of the mold corners, 120, 220, 400, 800. I spend about 30/40 minutes using each one, and was very happy with the result, minus the fact that I had to often change the sanding paper, and throw it away as concrete was clogging it up very quickly. I think if I ever do this again when I move out of this apartment, I will invest 70-100$ or whatever it costs into a set of diamond polishing pads.
(Picture shows unsanded block as it came out of the mold. It shows the water runs in the concrete because i was diluting the mix with water a bit too much, when I should have been more patient. This has worked out for me however, because it looks like wood grain, for which i was shooting for, as you will see in the next step.)
Sanding was the worst part of the job. Unless you have a polishing grinder/grinder, you will have to spend a lot of time sanding this by hand. Professionals go through a whole set of grits from 100 to 3000, while I just used the ones I had at home. I had an 80 to finish up the roughness of the mold corners, 120, 220, 400, 800. I spend about 30/40 minutes using each one, and was very happy with the result, minus the fact that I had to often change the sanding paper, and throw it away as concrete was clogging it up very quickly. I think if I ever do this again when I move out of this apartment, I will invest 70-100$ or whatever it costs into a set of diamond polishing pads.
(Picture shows unsanded block as it came out of the mold. It shows the water runs in the concrete because i was diluting the mix with water a bit too much, when I should have been more patient. This has worked out for me however, because it looks like wood grain, for which i was shooting for, as you will see in the next step.)
Step 7: Staining, Sealing, Waxing
This was the most fun part.
I ordered two acid stain samples (4oz) from Expressions-LTD and a sealant (16oz). Be prepared to pay a lot for shipping on the stain as it is a hazardous material. The price for shipping these three tiny bottles came out more than the 30 dollars that I spent on the products - 34 DOLLARS.
I then ordered concrete countertop wax from CHENG Concrete for 20 dollars total.
I cleaned the surface with water and a rag and waited a day.
I applied the light stain with a fairly dry synthetic artist brush in tiger stripes to imitate the grain. I did this a couple of times, with no wiping of excess or anything (there was no excess). Then I did the same with the darker stain. After that I diluted some amonia in water and wiped down the surface multiple times with a rag dipped in the solution. When no stain was getting picked up by the rag, I did it a couple more times and left to dry for a day. Next day I rolled the sealant on 3 times in very thin coats, with no time intervals in between. Let dry for 3 days afterward. After it was dry I applied CHENG countertop wax with a rag, and buffed it with a glass cleaning cloth I had laying around. A day after, I unmounted the old sink top, put the new on it, and connected all the plumbing. Below is the example of the difference.
I rate this project as time consuming, slightly expensive, but EXTREMELY rewarding. Every time I get up, hating to go to work, and I see the sink, it really boosts my mood!
Good luck and have fun!
I ordered two acid stain samples (4oz) from Expressions-LTD and a sealant (16oz). Be prepared to pay a lot for shipping on the stain as it is a hazardous material. The price for shipping these three tiny bottles came out more than the 30 dollars that I spent on the products - 34 DOLLARS.
I then ordered concrete countertop wax from CHENG Concrete for 20 dollars total.
I cleaned the surface with water and a rag and waited a day.
I applied the light stain with a fairly dry synthetic artist brush in tiger stripes to imitate the grain. I did this a couple of times, with no wiping of excess or anything (there was no excess). Then I did the same with the darker stain. After that I diluted some amonia in water and wiped down the surface multiple times with a rag dipped in the solution. When no stain was getting picked up by the rag, I did it a couple more times and left to dry for a day. Next day I rolled the sealant on 3 times in very thin coats, with no time intervals in between. Let dry for 3 days afterward. After it was dry I applied CHENG countertop wax with a rag, and buffed it with a glass cleaning cloth I had laying around. A day after, I unmounted the old sink top, put the new on it, and connected all the plumbing. Below is the example of the difference.
I rate this project as time consuming, slightly expensive, but EXTREMELY rewarding. Every time I get up, hating to go to work, and I see the sink, it really boosts my mood!
Good luck and have fun!
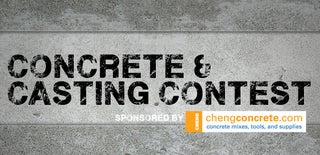
Participated in the
Concrete and Casting Contest