Introduction: How to Make a Kitchen Knife for Free!
Are you tired of stamp cut kitchen knifes that go blunt after a little use? have you ever thought I could do better than that? are you a little short on funds, like to recycle or just dont want to spend money on steel? If so, this is the ible for you!
I will show you how to make a decent kitchen knife that can take a beating, hold a good edge and look nice, with the added bonus of being cheap to free and made by you! . So get ready to raid the scrap bin, take a saw for a walk in the woods and ask strangers for favours.
Step 1: Tools and Materials
tools:
Pencil.
sharpie
Ruler
Tri-square.
angle grinder.
bench grinder
belt sander.
wetstone.
sandpaper (every grit you can get your hands on).
a strong epoxy ~(preferably odourless).
Blowtorch, (or an oven hob).
various drillbits and drill.
small files.
a bucket of water
OPTIONAL:
a hammer, an old bike spoke and some pliers.
Materials:
Circular saw blade.
Paper, preferably grid.
brass for the bolster.
Hardwood for the handle, whatever you can get ( I used some hawthorn that has been salted by a tidal surge a few years ago, super dry). Optional secondary wood, I used cocobolo left over from a knife scale my dad broke.
lots of masking tape
Personal protection:
dust mask (as much as you can try, you can't breathe metal dust and sawdust and other fumes)
full face visor,
earbuds
Gloves*
* use gloves at your own discretion, I use gloves rarely but I never use them on the belt sander or bench grinder as it would be worse if they caught up in the machine.
Step 2: Making a Blade
Unfortunately, I did not have the foresight to document the making of the blade, but its pretty straight forward.
first, look at what you can use as material, I had lots of scrap steel lying about but nothing that was fit for purpose. I went to my timber yard to get some bits and bobs and while they were cutting some wood for me, I asked if they had any old sawblades knocking around. As it happened they had a blade that had some chipped teeth and was going in the skip, lucky me!
next look at the blade you want to make, get out a bit of paper and trace the available space and design a blade, WITH TANG, within the confines of that space. Remember, when designing the blade consider function and use as well as how nice it looks. I based my blade from a japanese Deba. I had limited space in the material so I had the Tang come up at a slight angle from the flat of the cutting edge to give more finger clearance. once you have a design, its a good idea to cut it out in cardboard and get an idea of how it feels in the hand.
Next, mark up your design in the material, in my case a piece of circular saw blade, then start cutting.
Cut out the basic lines with the angle grinder, then tidy it up on the bench grinder. Dip the metal in a bucket of water to stop it overheating and ruining the heat treat. DO NOT OVER HEAT, dip it often and make sure the metal doesn't change colour.
Step 3: Adding the Grind
The grind that you choose depends on a few things, what tools you have, what the knife will be used for and what you are comfortable trying.
I chose to do a hollow grind, as I have a bench grinder and thought why the hell not.
the pros of a hollow grind are that it gives a thin edge, allows for easy sharpening and stops vegetables sticking to the knife sides (in theory).
the cons are that it is weaker and less useful for cleaving and takes a while to grind out. Also you need some kind of wheel or convex grinding tool.
other grinds include a convex grind, a strait v grind or a chisel grind (Which the deba traditionally has), whatever works best for you.
Grinding the Edge;
To grind the edge on a bench grinder, I took a piece of scrap wood and clamped it to the rest of the grinder, I used this as a stopper for the blade and adjusted it till I had a grinding angle I liked. Then I just started grinding, swapping sides and eye balling it to make sure it was centred.
Do not put a full edge on at this point or you will regret it when you have to fit the handle.
And remember to dip the piece in water and keep the metal cool, especially when grinding the thin part of the edge as it will heat up quickly.
Optional: at this point I added some slight serrations to the tang to help it stick fast in the handle, and spot it coming loose.
Step 4: Fitting the Handle
Again, this starts with design, choose a handle style that suits the blades style, purpose and fits well in the hand.
I decided to do a 2 wood, hexagonal handle with a slight taper towards the bolster, after looking at lots of pretty Japanese blades on google.
Cut the wood into easy shapes to work with, and leave lots of room, if you have a table saw, band saw or thicknesser (which I do not) you can make these all nice 90 degree corners which will help you in the marking up.
cut a slot in the brass bolster which fits the tang snugly (using a drill bit the same thickness or less than the tang and some small files), then line up the bolster with the next piece of wood that you will be using and mark the hole onto it. I drilled the Cocobolo separately to the hawthorn but you can do it at the same time.
Next I drilled the hole for the tang try and keep it nice and straight or use a pillar drill if you have on (which I do not).
After drilling the hole, I wrapped the blade in a healthy layer of masking tape and heated the tip of the tang till glowing. Carefully, I pushed the tang into the wood to burn a snug fit.
next cover the tang, wood, bolster and any other contacting surfaces in a strong epoxy and assemble.
Cover in clamps and leave to set for a good few hours or overnight if you have the patience.
Step 5: Shaping the Handle
Now we break out the tri-square and the belt sander or file and go to work.
try and square off the wood so that all of the surfaces are flush and aligned. I did this by making a cuboid with the sides running parallel to the blade and all corners at 90 degrees.
Then I measured the ends, cut out paper templates of the octagonal shape I wanted and glued them to the ends, cutting a slot for the tang.
then grind away the excess, making sure that the grind reaches the template on both ends.
You could use the same method for a rounded handle or any thing else you can think of.
Step 6: Sanding and Finishing the Handle
This step is the slowest. break out the sand paper and a scrap of wood. Get a cuppa made and put your feet up.
go through every grit at your disposal, start at the same or one above the grit you used on your sander and work up to the highest you had, I went 60, 80, 100, 120, 180, 240, 400, 600, 800, 1200. Once you are happy or you cant feel your hands, apply the finish of your choice, I used bees wax and turps but pure beeswax, shelac, mineral oil or tun/ linseed oil are all good options.
Step 7: Adding Your Mark (optional But Very Cool)
Take a piece of bike wheel spoke or something similar and hammer the end flat, then using the grinder smooth the sides and faces and tip.
I then fitted a small handle but this can be done with pliers.
heat the tip of the rod and brand the base of the handle with your mark.
leave to cool and then sand and finish.
Step 8: Sharpen Up
very similar to the sanding, its worth putting the kettle on for this, if you left the blade dull it will take a while to put an edge on but it its worth doing by hand.
get the wet stone out
place the blade flat on the surface, with the edge and the spine of the hollow grind in contact with the wetstone,
slide the knife towards the blade, lift and repeat. don't forget to swap sides and when the blade is getting sharp swap to a finer grit.
keep going till it cuts well.
top-tip:
run a marker along the edge before sharpening, this will show you if there are any spots you are missing and how far you are to finishing.
if the blade is not stainless steel, remember to keep it dry, and treat with olive oil now and then to stop it rusting.
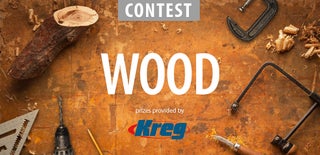
Participated in the
Wood Contest 2016