Introduction: How to Paint a Car Like a Boss (and You Don't Need a Spray Booth)
I have been building this hot-rod for the past 8 or 9 years. I had the picture in my head of what I wanted it to look like and it is almost there now! You can see here pictures from the day I bought the death trap rust bucket donor car (the powder blue thing) that belonged on a scrap heap, some of the early transformation pics (the powder blue thing missing some bits and sporting rust), to when I tore the body off the chassis, all the way to now.
I've already written an Instructable about the chassis restoration and making the engine look the mutt's nuts. This car was absolute junk, major structural parts were made of newspaper coated in body filler, rot was creeping everywhere, I had to cut out and replace more steel than I left behind. But rather than scrap it, I have given it love and attention, given it a roof chop (that is lowering the roofline, by a few inches, to make it look lower and meaner), built a new engine, done a full chassis restoration, a full body restoration, and made a LOT of trick parts. There is not a single part of this car you can look at without seeing something I have restored, modified or made new.
In this Instructable, I am going to talk about paint. Actually, I am going to level with you, this Instructable mostly is a thinly veiled gratuitous brag. I mean, look at it! LOOK AT IT! LOOK. AT. IT.
JUST.
LOOK.
AT.
IT.
Right, lets chat paint, paint prep, and doing things the right way. We will touch on welding, and cover brazing, using epoxy filler, fibreglass filler, primer, sanding and laying paint.
This Instructable is aimed at people who have some experience at DIY restorations and want to attempt something bigger. This is the second time this car has been repainted, the first time I did it outdoors under a gazebo in my yard.
The second time, I had access to a better indoor work area for the parts I did, and a professional on hand for advice, teaching and help. But the principles are the same, and you can achieve great results provided you give it care, attention and time.
I owe a huge debt of gratitude to Paul Weeding and LVH Engines and Restos for all he has done here.
Supplies
LOOK AT IT! LOOOOOOK AT IT!!!
Body work on cars car be as hard or as easy as you like. On this website alone you will see everything from skim, hit and hope patch jobs right through to professional nut n bolt restorations.
This one falls into the latter category. This is the sort of thing that requires time, blood, sweat, tears, some specialist tools and a LOT of patience. You WILL make mistakes, and WILL have to redo parts of it. It is all part of the learning curve. I am going to talk you through how this was done, but I will talk about alternatives you could do along the way.
Tools, consumables and materials that were needed for this:
- Dual Action (DA) Sander
- MIG welder (a gas MIG welder using a CO2 / Argon mix and 0.6mm wire is my personal weapon of choice here)
- A decent auto-darkening welding mask (anything less will just make your life way harder than it needs to be)
- Angle grinder with slitting discs, grinding discs and sanding pads
- Oxy turbo set (a mini gas torch, using oxygen and map gas)
- Welding goggles
- Welding apron
- Welding gauntlets
- Hand sanding blocks (a selection of these is very handy for getting contours right)
- Various grades of abrasive paper for your DA and sanding blocks - wet and dry, grades 80 right through to 2000 or even 3000.
- Cutting compound
- Polisher and a selection of polishing mops (don't use polisher attachments for drills etc, use a dedicated polisher otherwise you will risk burning through your paint or contamination from your tool)
- Primer spray gun
- Top feed spray gun with a selection of nozzles
- Compressor adequate to feed the spray guns - You can use aerosol cans here instead if you are doing a small job.
- Assorted wire brushes for the drill and grinder
- Fine body filler
- Fibreglass body filler
- Scotchbright abrasive pads
- Epoxy primer
- 2 pack automotive paint
- 2 pack clearcoat
Some notes on all this.
The paint is not nice stuff. If you do not have an extraction system, don't use 2 pack. Use cellulose or something a bit safer. Your paint shop will be able to advise.
This time, it was painted in a dedicated booth for painting, with extraction, filters, and some decent equipment. That said, you can achieve a lot in a yard with a small compressor and a spray gun, which I talk about in Step 8.
On the subject of sandpaper, the grits and what they should be used for.
40 to 80 Grit – This grade is coarse, and will leave behind visible marks. It is for when you need to remove a lot of hard material, and not at all recommended for use on paint unless you are removing it completely. use this for shaping body filler, sanding down brazing work etc.
120 to 180 Grit – This grade is for flattening out scratches left by coarser grades, feathering edges of body filler, and rust removal.
320 to 400 – Now we are getting to finer grades. It can be used for keying a surface before laying down primer, sanding out scratches, rough primer sanding, and final body filler sanding.
600 to 800 Grit – This range is for sanding out imperfections in primer, and keying primer ready for paint. You should start at lower grits and work your way up to this when preparing a surface for paint.
1000 to 1200 Grit – Blemishes in our base coat and sanding out runs is what this range is for. When you are into this range, you should always be wet sanding, never dry sanding.
1500 to 2000 Grit – This range is for removing scratches and runs in the clear coat and finishing coats, before you start polishing. You should DEFINITELY be wet sanding whenever using this grade, otherwise your paper will just clog up. Once you are sanding clear coats, you do not want dust hanging around to ruin your finish.
Step 1: The Tear Down
In my chassis restoration Instructable, I tore the car to pieces after realising she was held together with little more than rust, hopes and dreams and happy thoughts. I built the car, drove it twice, and tore it to pieces again because it just was not right. I was not at all happy with it, there were still major structural issues and rust everywhere.
Many of the welding-related things I talk about there are absolutely valid here. It is worth a flick through. Note, the welding technique differs for bodywork to structural stuff.
When I dug around on this body, it turned out to be just as bad as the chassis for rot and rust. I won't get bogged down too much in the welding but I will talk about some of it in the next step.
The point of this part is that you need to be brutal and look very hard at the vehicle. Be ruthless, dig at every rust bubble and blemish. Hell, get the shell media blasted if you fancy making yourself cry.
An assessment of this body shell revealed a requirement for some serious open-wallet surgery.
The sills (the bottom of the body), much of the rear arches, one of the front arches, both B pillars (B pillar is where the door bolts to the car) all needed a lot of attention (read: Replacement). The glass had to come out of the body (I disposed of the old rubbers, I am not going to reuse them), doors off, bonnet off, the rule was this: If it comes off, then take it off.
This is the point of no return, there is no going back from here. Strap on your red sparkly shoes, because after this, you are not going to be in Kansas any more, Dorothy.
Step 2: Hit It With the Fizzy Stick!
As I said, I am not going to go into depth about the welding, purely because I have already done that in another Instructable and it would make this one way to long and heavy. There was a LOT of welding needed.
But to touch on one example, to give a flavour of the pain I had to endure, the front right quarter panel (or whatever you call it in your Country) was pretty shot. I attempted a repair on the lip by cutting out the upper portion, and welding in new along the crease, but after doing this (and making a damned fine job of it, I might add!) we realised that it had sustained impact damage at the bottom sometime in it's life, so we ended up opting to cut the whole panel out and replace it. LIKE I SAID IN THE LAST STEP, LOOK CLOSELY AT THE WHOLE CAR!!! Not looking closely and just jumping in meat a whole 3 days of work wasted. Throwing a repair I was proud of on the scrap heap was not a good day.
To remove a panel on a vehicle, you need to firstly look at the replacement panels that are available. Buy the very best you can afford, you really do get what you pay for and an extra $100 on a quality pressing can save you days of fettling around later, or worse a result that you are not happy with. Find the best quality steel you can. There's a reason cheap repair panels are cheap - they do not last.
If no panels are available, you will have to either find a donor vehicle (I got several parts off other vehicles here - the chassis framehead, the roof is made from the roof of three different vehicles, parts of the doors, were all from donor vehicles and welded in). For some parts, you can make your own panels. I made several panels of my own here from sheet steel. That topic is worthy of another Instructable of it's own.
Look carefully at where you will make your cuts and plan them well. In this example, the factory spot welds were drilled out carefully and a slitting disc used to free what was left off. I would advise cutting out less than you need to, and then regularly offering up the new panel and trimming the target area to fit. You can also cut the replacement panel to suit if needed.
The fuel filler flap is on this side, but since my bonkers hotrod has a wooden barrel poking through the bonnet as a fuel tank, I do not need the filler flap.
This involved cutting out the pressing where the filler flap would go, and welding a patch over where it was. You could just weld a patch over the hole, but that is a bit lazy and leaves you with random bits of steel kicking around that you don't need, and would make the area under the bonnet look less tidy. Because it was redundant, it was removed.
I am going to assume you know how to use a welder here. If you do not, this is NOT the time to learn, but by all means use some scrap metal and try these tips out.
Clean the metal to be welded thoroughly using a flapwheel or wire brush in your angle grinder. Go gently, don't press down on the grinder, let the grinder do the work. Less is more, take your time! Watch for the metal getting too hot, if it even starts to glow, STOP!!!!!
Welding bodywork requires a different technique to welding thicker steel. You are going to select a fairly high power setting (practice on some scrap steel to find the sweet spot for your welder). Rather than welding a bead, you are going to hit it with a very short, sharp, zap to tack it until your tacks meet here. You need it so that if you linger for any length of time, you will blow a hole in the steel. Normally, when this happens you would turn the heat down so you can lay a bead. But not here... The reason for this is you want a very good, deep penetration full weld, and you do not want to heat the surrounding metal up. You need to keep the heat very, very localised for this technique to work, otherwise you will see a lot of warping on your panel.
You are aiming for good penetration. The steel should be discoloured, the weld clean, and neat. If you have a snotty looking weld, your settings are not correct or your steel is still contaminated with something. You cannot rely on being able to rework the welds here, you have one shot to get it right before you get into trouble. Rewelding will just distort your metal.
Once you have the settings dialled in on scrap steel of the same thickness, you can brave the bodywork.
- Tack the fresh steel in place, using welding magnets and being very careful to keep everything aligned. Your tacks should each be a very short, sharp hit. A fraction of a second is all it should take with the trigger pulled. Adjust the fit with light taps and pushing as you go.
- Once your tacks are in, wait for the metal to cool.
- Now, you are going to hit each of your tacks with another one right next to it, a good sharp whack, so that the next tack joins the first one. Use a small hammer to keep things aligned.
- Rinse, and repeat!
It is painstaking, and if you rush it and don't let the metal cool, it will warp and distort. Having an air line handy to blow air at the metal to cool it off. You can also use a piece of flattened copper pipe as a heatsink behind your weld.
Once your welds are done, go very very gently with the flapwheel to flat the welds back to the level of the bodywork. You really, really have to be careful here not to make the metal too thin otherwise it will crack and buckle. You are ONLY interested in removing the high spots of your welds, you are NOT trying to flatten the whole area to make it look nice.
Once this was done, the new wing was stitched to the car using rows of spot welds along the seam.
- To spot weld, drill holes in the overlap of the two panels, about an inch apart.
- Clean the area well with a flapwheel.
- Clamp the new panel to the old panel.
- Fill each hole you made with your welder, ensuring the two panels fuse properly.
- If you blow a hole, DO NOT try to fill it with the welder. Just move on past it. If the hole is huge, you will have to cut it out and start again. Using a copper "spoon" (a piece of copper hammered flat) behind the weld will help you a lot here to stop you making holes.
The point here is sometimes it is easier and better to just cut a panel out than it is to try and repair it or skim over it with filler or fibreglass. Welding in fresh panels is a skill, and there is a reason why it costs money to have this done. But of all the methods for restoring a vehicle, it is the gold standard.
I have included a selection of pictures of other areas that needed welding to really show you how far I had to go with this, and why this definitely qualifies as "trash to treasure". The car was a real mess.
Step 3: Filling and Blending - Brazing
Here we are, getting into the real fiddly bits.
So, you have welded the panel in. Now what? Well... There are lots of options available to make it look pretty. If you are a super pro, with superpowers far beyond mine, you won't need to do any of this because you will have welded like a boss and it will be perfect.
But what if you don't live in a make believe land where things like physics and metallurgy get in the way?
There will be a noticeable imperfection where you welded. In this example, the area over the filler flap that was deleted, as well as the area around the swage line at the top of the wing where it joins the windscreen scuttle, were deformed and warped a little. (A swage line is a crease in the bodywork, usually for aesthetic purposes. They make a very handy place to start and end repairs too, as you can hide your seam in there).
Lets start with brazing. This is the addition of brass as a filler material, and is great for seams where there needs to be a little strength, where seam welding would risk warping the area badly (in this example, the swage line is a hard one to weld and because it is so prominent, the eye will be drawn to any imperfections there). Smearing epoxy over the area would likely cause the repair to crack further down the line, so brazing was the chosen method.
Brazing is difficult. You need to practice. But done correctly, you will find the brass bonds to the steel nicely, and creates a seam that will not rot, won't crack, sands down well and readily accepts paint - it will NOT react with your paint like some fillers will. Some naysayers will claim that brazing cracks or causes problems. the very same can be said of epoxy used indiscriminately and poorly. Don't listen to them. It is an old skill, an old school way of doing things, but it is worth learning to do.
The method is fairly simple, but mastering the technique takes time.
For this you will need:
- Your oxy torch
- Flux coated brass brazing rods
- A wet cloth
- Eye protection (welding goggles)
- Welding gauntlets
- Clean the area well with a wire brush, and then wipe down with thinners. Make sure the surrounding area is free of paint, grease and contamination. Once done with your thinners, put the lid back on and put them away, WELL away from where you are working. Same goes for the cloth you used. Let the metal dry off and the thinners evaporate before moving on.
- The goal is to heat the parent metal (the steel) to a temperature that will melt the brass. You are not going to melt the brass with your flame.
- Light your torch, and make a small blue flame by tweaking your controls.
- Heat the general area with the torch to a dull red.
- Now, increase your oxygen flow. You are looking for a bright blue, almost white, flame.
- Heat a small patch at one end of the joint to around 900*C - use the colour chart I have included here. KEEP THE TORCH MOVING! Do not concentrate on one tiny spot. You are looking for a salmon to dark orange colour on the steel here.
- You need to be swift on this stage. Touch the brass rod onto the joint, keeping the torch moving on the surrounding area to keep the temperature up. The brass will melt quickly, and flow into the joint. Do NOT try to melt the brass with the torch! The technique is a lot like soldering. You will see it flow nicely as a liquid, and stop flowing where it meets cooler steel.
- Using your wet cloth, damp down the area regularly to pull away the heat. You need to control the temperature, as soon as you see the metal go to a bright orange, cool it off with the cloth immediately. Keep using the cloth to suck the heat out of the metal not immediately around the joint.
Some very important safety tips here.
- Make sure your gas bottles are not between you and your escape route.
- Make sure there are no combustibles nearby. Thinners, cloths, carboard, anything that could catch fire.
- Make sure that there is nothing on the vehicle near the area you are working that could catch fire.
- Have a, appropriate fire extinguisher nearby (powder is the weapon of choice for me)
- Wear welding gauntlets, goggles, and preferably a leather metalworking apron.
- When wetting down the area with your wet cloth, remember that water loves to soak up heat. If you get your gauntlets wet, they will NOT protect you from the heat. Whenever you use the wet cloth, take care to not wet your gauntlets.
Done correctly, brazing will not warp the surrounding metal, and will need little by way of attention afterwards. You may need to sand it, and add a thin skim of epoxy to get it perfect, but the brass will sand nicely and blend very well.
Brazing is also very handy for repairing pinholes and other imperfections in sheet steel. It holds pressure very well, does not make a porous joint, and will not rust.
Step 4: Filling and Blending - Epoxy
Many people will slate epoxy filler. It has a reputation as a bodge tool - an unfair reputation in my opinion.
Used correctly, it is a useful weapon in your arsenal. Many people will just indiscriminately smear it over some rust in the hope that this will magically fix the problem. This is absolutely the wrong thing to do! I have seen some seriously unsafe repairs made using this stuff - it should never, ever be used to bridge holes or make structural repairs.
Body filler is exactly that - filler. It is designed to fill dips and skim over properly made repairs.
Look at the first picture here, at the area that had the patch welded in - the welds were noticeable. This is an area that is ideally suited to this type of filling. Large area, solid metal, clean, not rot. Perfect!
How would one correctly use filler?
Firstly, the area must be absolutely free of rust. Totally, 100% free. There are rust stabiliser products out there, but I don't trust them. Or, more accurately, I don't trust anyone (myself included) to use them effectively enough for them to be effective as a long term solution.
Filler can be applied direct to steel, over fibreglass, or over a primed surface. In this example, it was applied direct to steel.
You will need:
- Filler
- Hardener
- Spreader or pallet knife
- A mixing pad or a suitable mixing surface
- A can of black spray paint
- Sandpaper
- Assorted sanding blocks
Sand the area with coarse sandpaper to key the surface and give the filler something to bond to.
Mix up a golf ball sized lump of filler with a pea sized blob of hardener on a suitable surface (I use pads of special paper for this, but really any clean surface free of contamination will do, just make sure it is something disposable) using your filler spreader / pallet knife. Keep mixing until it is all one uniform colour.
Spread a layer of filler over the area to be filled (as per the second pic). Work the filler into the metal, pressing down hard to really squash it into the metal. Spread it over the whole area to be filled and well into the surrounding areas. Try to smooth it with the filler tool but don't worry about trying to make it perfect yet. Just make sure you have good, even coverage and no huge snots or beads anywhere. Leave it to go off (go hard and dry). Don't try to sand while it is still tacky, you will ruin it.
Once it has hardened, sand it back with progressively finer papers to about 500 grit.
Your sanding technique is important here, and there are a few ways to tackle it. It is better to do it by hand rather than using the DA for smaller areas.
Try to use a circular motion.
Use a sanding pad that closely matches the contour you are working on. DO NOT just hold the paper in your hand unless there is no other way to do it - your hand will create high spots in the sandpaper which WILL transfer into the work.
Go steady, less is more here.
Do not concentrate in just one area. Make very large sweeps with your paper so as to blend the area nicely.
Regularly run your hand over the area in all directions. You are NOT admiring the smoothness, you are looking for high and low spots. Some will be fore subtle. Follow the contours of the bodywork and check very regularly as you sand.
There is a good chance you will need to apply more filler. This is because some of your spots will be level and good, but some will have been sanded too far.
Rinse and repeat until you are happy.
Once you think you are happy, dust a very fine coat of black paint over the ahead (called a ghost coat). You are NOT trying to paint it black, just a fine dusting is all that is needed.
When you run your fine sandpaper over the area on a sanding block, you will see areas of black that get left behind. These are your low spots. It is a handy tool for highlighting where you have sanded too much, or not enough.
Be patient. You will sand away more filler than you leave behind by the time you are done. It is a wasteful process, but worth it for a great finish.
You can see in the second to last pic just how far the filler area is in relation to where the original patch was welded. The thickness of filler is miniscule in places, but this was what was required to bring the area in nicely.
The last pic I have included as a curiosity. You can see how many colours this car has been in the past here. Pretty neat, huh?
Step 5: Just Keep Filling...
Once you have mastered the technique, you just keep going over the whole car.
As you work, you will find more and more areas that need work. Many of these areas will be places you have already done and considered "finished".
It will be a laborious process, and frustrating, and it will take you days, maybe weeks.
Using a DA will help but go easy with it, it is SO easy to over-sand using one of these.
Top tips:
- Keep the work area dry, clean, and free of dust. Clean up regularly.
- Cover any bare metal with paint or epoxy primer, anything to keep the moisture off the metal.
- Make sure your materials are properly mixed every time. If you leave catalyst or hardener unmixed anywhere, it will react with whatever you try to put over it.
- Take your time and be patient. Don't rush any one part of it, take regular breaks from it. A break could be 5 minutes or a fortnight - if your heart is not in it, then stop.
The pictures demonstrate the extents that were gone to for this. You must be ruthless with rust, using a wire brush to really dig out rust and old repairs.
The pics show a few (by no means all!) of the areas that needed attention.
The dash was also grafted in and blended at this point. Yes, it is a solid mahogany dashboard. The plans for this are nothing short of spectacular - there will be an Instructable about this one day.
The green filler is what we call "Hairy bodge" - it is a polyester filler mixed with fibreglass. This stuff is structural FOR A GIVEN VALUE OF "STRUCTURAL" It is not designed for heavy work such as chassis repairs, but it does work for bridging areas that need some strength. In this case, it was used to repair some pinholes around the bonnet lip and add some rigidity to some flimsy steel, and bridge the gap between the car and the mahogany dashboard. Using it is the same as any other filler, except that it needs a layer of fine body filler over it to finish. It will not sand down nicely to a good finish without a top layer of regular filler.
Step 6: Primer Time!
Next up is priming. Give the work area a really, REALLY good clean. You need all the dust out of there, be thorough! Super thorough! An industrial vacuum cleaner will help a lot here.
- Wash the car down with panel wipe. You need to be very meticulous, and make sure that all surfaces are totally free of grease, contamination and dirt. do NOT touch any surface to be painted with bare hands once cleaned.
- Wear surgical gloves.
- Clear everything out of the room that you do not want covered in paint. This stuff will go EVERYWHERE.
- Wear a paper suit, goggles, and an appropriate mask with filters.
- Using the primer gun, the car was coated in a layer of high build epoxy primer.
- Several light coats is the ticket here, to ensure good coverage.
Mix the primer according to the manufacturers instructions, and apply as directed. You can use aerosol cans if you are only doing something small but for a full car I would not recommend this at all.
Test spray on a discreet area, and adjust your air and material flow so that you get good coverage without gacking too much on in a single pass. The primer should look glossy, but not cover the area in a single pass.
A few tips:
- Keep the gun perpendicular to the surface to be painted. Don't be tempted to tilt the gun side to side, always keep the gun at 90* to the surface being painted and follow the curves of the car.
- Don't spray back and forth with the trigger held the whole time. When you sweep from one side to the other (say, left to right), stop the trigger BEFORE you stop the movement. Start the movement in the opposite direction BEFORE you pull the trigger.
- Don't try to "colour in" the vehicle in one go. Work your way around and make several passes, slowly building up the primer.
- Don't panic if you see a run in the paint or a build up in one area. Just leave it and let it dry. do NOT be tempted to touch it or try to rectify it as this stage, you will just make it worse.
- If your primer looks "powdery" and dry, you are either too far away form the target, or your material flow is too low.
- If your primer has creases and wrinkles in it, you are either too close to the target area or your airflow is too high.
- If you are using rattle cans (aerosols), the principle is exactly the same
Let the primer dry properly. Once dry, inspect closely. Sand out and runs gently with 500 grit paper using the same technique as with filler with a sanding pad.
Look for high and low spots over the car with your hands. There is every chance that you will spot things you did not se before at this stage. Apply filler to any areas in need of remedial work, and watch closely for pinholes. These WILL need a skim of filler over them, paint will NOT fill pinholes.
You can see in the last few photos areas that needed more attention. Scratch marks from sandpaper, holes, and issues that needed some remedial work.
The primer will have an "orange peel" texture to it. You need to sand this out.
You can dry sand or wet sand. I would recommend wet sanding be done outside. Whichever method you use, hand sanding is the best way by far. Don't use the DA, you will cut straight through the primer and you will miss a lot of imperfections that you would spot if you were hand sanding.
DRY SANDING
Start in a discreet area to get your eye in.
Using 400 grit, apply gentle pressure with your sanding block.
Let the sandpaper do the work, and sand in a circular sweeping motion. Be very mindful of the contours of the car. Don't sand over edges too much as you will flatten them, so be careful around swage lines and any corners.
Stop every few seconds and feel the primer. It will become very smooth very fast.
WET SANDING
As I said this is best done outside. Wet sanding is exactly what it says, sanding with wet paper. The water lubricates the paint and stops the paper from clogging up.
Start with 600 grit for wet sanding.
Using a spray bottle of water, spray the sand paper.
Sand back and forth rather than in a circular motion.
The finish is better with wet sanding than dry sanding. But it makes more mess.
The technique we used before with the black spray paint is excellent for this stage. It will tell you where all the low spots are. Between this and using a bright light to see how the light reflects, you can fettle away to a perfect finish.
Take your time, do not rush. remember you are not just feeling for smooth paint, but for high and low spots and other imperfections too.
This stage is the most critical one. I this stage is done right, your paint will look great. If you do it wrong, you will never get a good finish. When you pay big bucks for a paint job, this is the stage where most of your money goes. it will take you a lot of time, but it is absolutely worth taking the time over.
Step 7: Colour Selection
I mulled over the colour choice a lot.
Something fancy vs something discreet?
Something lairy? Something boring?
It is worth noting at this point that different colours are harder to get a good finish. Black is the WORST colour to make look nice. Dark colours are generally harder than light, and gloss is harder than satin or matte.
Matte white is the easiest colour to make look nice.
Matte colours are very easily damaged though, satin not as much but gloss is the hardest wearing. My advice would be to think long and hard about the finish you want, and the time you have. Multi-stage paint systems such as pearl, candy, crystal etc - basically any of the fancy ones you see on the Discovery Channel where serious men with moustaches make everything look super easy, are a pain to get right and need a LOT of work. By all means attempt them, but I would advise starting with something easier, a single stage gloss paint is best to learn with. Bright red is always fun, and a good starting point as it looks great, hides lots of sins, polishes up really good and is easy to repair.
My car was in a a satin gunmetal grey before I started this restoration, but I wanted a change.
I tried out some "Crystal FX" paint (the copper coloured lined pattern). I thought it looked great! But for a whole car? It may have ben a bit much.
The other main contender was metallic teak brown.
Crystal FX
The method for shooting this was straight forward, but lots of stages and a lot to go wrong.
- To start, the surface is primed.
- Then a coarse metal flake silver is shot (nice and sparkly!)
- Once dry, clearcoat is shot over the metalflake.
- Once the clearcoat is dry, it is flattened back using 1500 grit wet sandpaper - this step is important, as the "Crystal FX" needs a smooth, slightly keyed surface.
- Next, the Crystal FX stuff is sprayed over this. As it dries, it crystalises. The crystals crack, leaving a crusty, scruffy looking surface. It is imperative that you do not touch or disturb the crystals at this stage!
- Mix up some black paint. It has to be very thin, way thinner than you would normally use. Spray a coat over the crystals, and leave it to dry completely.
- Once dry, using scotchbright and lots of water, gently clean the crystals off the paint.
- You will be left with black lines wherever the crystals broke.
- Spray over with clear coat, or if you are like me and want some colour, add candy ink to the clear coat to give it some colour.
While I thought this looked cool, I felt it would be too "busy" for a whole car. I am sure I will use this technique on something, just not a whole car.
Teak Brown Metallic
This paint was a more standard 2-pack automotive car paint, and the technique for using it very standard:
- Prime the surface.
- Paint with metalflake paint (I chose a finer flake for this one).
- Paint over this with the teak top coat
- Clearcoat over the top for the deep shine
- Flat back and polish for the perfect finish
I liked this colour. It looked black until it was in direct light, where the colour would ooze through. the metal flake was only visible in strong light. Subtle, smooth, and suited the look of the car.
I think I made the right choice!
Step 8: No Spray Booth Required
This Instructable has been written after painting the car in a dedicated booth with professional grade equipment.
However, this is not the first time I have painted this car. With help from a very good friend of mine, using exactly the techniques above (albeit without going quite as far), we painted it in a concrete yard under a cheap gazebo with outstanding results.
When she was painted previously, we used gunmetal grey metallic paint with a satin finish. My friend Mikey helped (read: Did most of the work) and I mostly took photos and made coffee.
This was done with nothing more than a couple of cheap spray guns, a bucket of paint and two small portable compressor.
I have also painted panels, and whole cars, using rattle cans (aerosols) as well as enamel paint with rollers. In all cases, the key, the really crucial bit, is the prep. Actually laying the paint, where you see the results, is the easy and fast bit. The work is all in the preparation and attention to detail. Get that right, and your paint will go on just fine and look great. We spent a LONG time on the prep for this. Lots of sanding, filling, sanding some more, primer, sanding, more primer, filler, sanding... it was worth it. Though I only drove it twice after this paint job before finding the issues in the chassis which prompted a full rebuild.
My point is... You do not need professional equipment to get a decent result. You really can achieve this in your yard, under a gazebo, with hobby grade tools. This step is proof!
Step 9: Colour Done!
Anyway... After thoroughly cleaning the spray booth, and the shell, it was time to paint the car. I would strongly recommend you practice on something, an old oil drum is perfect. Get the technique right before attempting a car. But I know you won't. You will go straight into this and hope for the best. That's what I do!
The paint was 2-pack automotive paint. This paint is not safe to use at home in your garage. There are water based paints available, use these if you do not have an extraction system in your garage!
Wear a painting suit, wear a mask, wear eye protection and wear gloves!
Using the top feeder gun, the car was painted first in metallic silver. I have no pics of this, as you really do NOT want to be in and out of a spray booth between coats. Plus the air was very hazy, and not suitable for taking photographs.
The technique is the same as for the primer. Lots of thin coats, keep the gun moving. Don't concentrate on one spot, take long strokes with the gun. To reiterate the points again:
- Keep the gun perpendicular to the surface to be painted. Don't be tempted to tilt the gun side to side, always keep the gun at 90* to the surface being painted and follow the curves of the car.
- Don't spray back and forth with the trigger held the whole time. When you sweep from one side to the other (say, left to right), stop the trigger BEFORE you stop the movement. Start the movement in the opposite direction BEFORE you pull the trigger.
- Don't try to "colour in" the vehicle in one go. Work your way around and make several passes, slowly building up the paint.
- Don't panic if you see a run in the paint or a build up in one area. Just leave it and let it dry. do NOT be tempted to touch it or try to rectify or mess about with it as this stage, you will just make it worse.
- If your paint looks "powdery" and dry, you are either too far away form the target, or your material flow is too low.
- If your paint has creases and wrinkles in it, you are either too close to the target area or your airflow is too high.
Additional points to consider:
- You must match the gun and nozzles to your paint - chat with your paint merchant about this.
- Hold the gun about 30-40cm from your car.
Once done, clean your gun THOROUGHLY. If using metal flake, you need to make sure that every single metal flake is cleaned out. It is better yet to have a separate gun for metal flake, the cost of another gun is less than the value of your time chasing glitter flakes. A single spec of unwanted glitter can ruin a paintjob.
Once the silver has flashed off (the solvents evaporated - the paint will come with instructions on how long to leave between coats and stages) you can hit it with the colour.
Same technique as before, keep the gun moving, lots of very thin coats.
Let the colour dry, but do not leave it too long before the next stage, otherwise the top coat will not bond properly to it. Again, your paint shop will advise on the paint you are using.
Flat the orange-peel in your colour coat by wet sanding with 1000 or even 1500 grit and go VERY gently. Use lots and lots of water. This step will also key the paint nicely really for the top coat. This will be the time that you spot runs and imperfections, and will be your opportunity to put those right. If you see something that is not right, do not ignore it. You WILL regret not fixing it now.
After wet sanding, wash the car thoroughly with soapy water, rinse with fresh water and make sure it is dried THOROUGHLY. Use a chamois leather to get as much as you can off, and if you are in a hurry a hair dryer can help to get the moisture out of hard to reach areas. Leave if for a day or two to make sure it is properly dry.
Some people opt to not flat the colour back. This is fine, as the clearcoat will smooth it out, but you will still be able to see the orange peel texture beneath the clear.
With a thoroughly cleaned gun, it is now time to shoot the clear coat. This will protect the paint, and also give it a very deep shine.
The more coats of clear you give it, the deeper the shine will be but the more the risk that something will go wrong.
Let it flash off and dry between coats, but again do not leave it for too long. The "Flash Time" will be given with the product you use. Some are faster than others. Flashing off simply means allowing the solvents to evaporate.
Once you have shot your clear, leave it to dry for a few days, or even weeks.
Inspect very closely. If you spot any runs, they must be sanded out. Gently wet sand the run using 1000 grit, being very careful not to over sand and cut all the way through the clear coat. You may need to reshoot a layer of clear coat after sanding out your runs, if you sanded too far.
Wet sand the whole car to a high gloss finish with 1500, then 2000, through your grades all the way up to 3000. Each grade will sand out the scratches left by the last one. This job is tedious, laborious, but a great workout and very much worth doing well. Once again, DO NOT USE YOUR HANDS! Use your sanding pads to evenly distribute the pressure on the paper. Definitely do NOT use the DA. You need to be able to see every square inch of the car at this point to get all the blemishes out.
Be EXTREMELY careful on sharp edges and protrusions. It is extremely easy to sand too deeply on these areas. gently, gently, and take your time and avoid applying pressure to protruding areas such as rain scuttles, swage lines, corners etc.
It may be that you finish this part and find there is not enough clear coat, or you spot more imperfections or issues. Don't worry, just address the issues as you find them. Be prepared to have to shoot another coat of paint if needed. Do not be disheartened if you "go wrong" here - there is a good chance you will and if you go in prepared you will feel less despondent when it happens.
Things to watch for in these stages:
- "Fish eyes" - these are globs of paint that look like fish eyes. This is usually caused by contamination, such as a droplet of moisture. All you can do is sand it out, and paint again.
- Flecks of dust, or insects - Insects and dust love to land on fresh paint. If you spot one before the paint dries you can carefully try to remove it with a pin. However, you will need to sand and repaint the area. Sometimes, it is better to just leave it in there if it is not too noticeable.
- Reactions - Sometimes, you get reactions in the paint from whatever is underneath it. The paint will go crinkly, not set properly, and just look poor. Incompatible paint systems, or excess hardener or catalyst in the layer below, can cause this. All you can do is let it dry, sand it back, and start again. Sometimes you need to use a sealer to prevent it happening again - talk to your paint shop, they will tell you what you need for the products you are using.
- Orange Peel - Most painted surfaces will have an orange peel look to them as they dry. This is why you polish, you are removing the tiny high spots that cause this effect. Don't panic! It is normal!
Once you have wet sanded, wash the car down well, and thoroughly dry it. Then, following the instructions on the cutting compound, polish your car with your car polisher. Go very easy here too, you do not want to go too far. Different polishing systems have different instructions, so there is no one size fits all advice I can give here. You may need to do the fiddle areas by hand.
If you REALLY want a great finish, use a clay bar or the plethora of other products out there for a gleaming paint job.
Finished!
A few tips:
- Paint all the body panels separately - do the doors, wings, bonnet etc off the car. You will find it much easier this way.
- Do not rush, do not try to colour in the car in one hit. BE PATIENT!
- Do not panic when you see runs. Just ignore them, move on and then go back and sand them out later once the paint is dry. Once the runs are sanded, you may need to paint the area again.
- Where you have sanded out runs, you need to "feather" the edges of the area you sanded. Put simply, you are blending with the surrounding area, so that you do not leave a definite line where you sanded.
- Do not leave it too long between your colour and clear coat. You need to shoot the clear coat before the colour totally goes off and dries, otherwise the clear will not bond and it will, quite literally, fall off. You do not want this. Talk to your paint shop, they will tell you how to use the product you have bought.
- When using the car polisher be careful and use clean mops, dust and debris are you worst enemy here. You can NOT afford any contamination in your polishing mops.
- The same goes for all stages of painting. Cleanliness is next to Godliness. You cannot make your work area too clean and tidy.
So, what is left to do? The wheels are left to paint (they are going to be a bright metallic copper colour), the bonnet, and one of the doors. Then, finish the dash, fit the glass, fit the interior... more Instrucrables to come on this car, for sure!
Major thanks to the boys at LVH Engines and Restos for everything you have done so far to help me with this project!
LOOK AT IT! LOOK. AT. IT.
Step 10: What About the Lumpy Bits?
Some parts of the car would not look good in gloss paint. Either that or they need a harder wearing paint.
The floors, chassis and suspension were painted in a polyurethane paint. This is the stuff that truck bed linings get painted with, it is very tough stuff and it is easily patched up and repaired when it is scratched. It also looks kinda cool and is SUPER easy to use (I may even do an Instructable later with how to use it).
The "luggage area" as it is called on a Bug (the bit under the bonnet) and the front bulkhead are areas that will be subjected to wear and tear.
As such, it makes sense to paint these areas in a very hardwearing paint. My preferred brand is "Raptor", for no other reason than it has dinosaur on the bottle (yes, yes, I am a marketer's dream and a sucker for things like this!).
- Mask off where you don't want the paint (this stuff STICKS!)
- Make sure the area you are painting is clean, free of grease and dry.
- Using the shutz gun (underseal gun) that came with the kit, you mix up the paint with the hardener as directed
- Screw the bottle onto the gun, connect to the compressor, point, and shoot.
- This time, you are going to just colour the car in. No messing about with light coats etc, this stuff will just gack on nice and thick.
Easy peasy!
The texture is a rough one, but looks very nice and presentable.
A pleasant finishing touch!
Step 11: LOOK AT IT!!!!!
LOOK AT IT! JUST LOOK AT IT!!!!
LOOK. AT. IT.
I cannot WAIT to drive it!
Again, massive huge thanks to the boys at LVH Engines and Restos for everything you have done so far to help me with this project! These guys taught me everything I know about restoring cars properly. They did a good chunk of the work on the car ajd helped and taught me as I did the rest.
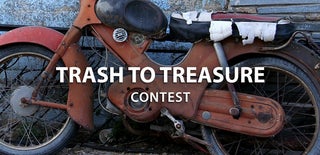
Runner Up in the
Trash to Treasure Contest