Introduction: How to Repair a Snapped/Cracked PCB (Circuit Board)
In this Instructable I hope to show you how to fix any broken PCB's you may have as this is often seen as something that can't be repaired and can contribute to a large amount of E-waste each year. For this example I will repairing a broken Sony Walkman that has had the PCB snap in half in three seperate places. This tutorial is for single sided PCB's with tracks on only one side, double sided PCB repairs are possible but a slightly harder to repair due to having to repeat the process on both sides. This guide is made for someone with some prior experience with soldering but can be learnt.
*this is a guide for low voltage electronics and how you use this is up to you*
Supplies
Tools required
- Soldering iron
- Idealy a fine soldering tip
- small file or sandpaper
- Exacto knife or similar sharp blade
- Multimeter
Parts required
- Solder paste (leaded will be easier to use but might be slightly more expensive and associated health risks)
- Loctite 435 instant adhesive (or similar form of superglue)
- standard guage wire - guage (thickness) will dpened on the size of the tracks that need repairing
- Solder - the higher the quality the easier the repair will be, can be leaded or unleaded
- Schematics for the PCB - This is not necessary but comes in very helpful when reparing complex breaks. The best place to find schematics for consumer electronics is service manuals that can be found for free on the internet and will often contain detailed schematics.
Step 1: Practice Makes Perfect
This step is not necressary but can help you with this repair if you have never done it before. This can be quite time consuming as you are effectively repeating the process twice. However, if the circuit board you intend on repairing is valuable then doing a practice could save you damaging the important board if you make any mistakes. You don't have to do a full repair, you could just practice soldering or gluing them together, what parts you practice are up to you.
- Try to find an scrap/permenantly broken circuit board - ideally one with similarly sized tracks to the one you intend to repair.
- Then make a small controlled break in the circuit board.
- Repeat the next steps in this instructables and test the board with a multimeter to see if your test repair worked.
- you are now ready to do your repair
Step 2: Locating the Break and Bonding the PCB
- Your first step will be to locate the break in the PCB and make sure the break is as clean as possible - this makes bridging the tracks and bonding it back together much easier.
- Once you have located the break apply a thin bead of super glue and hold the PCB for a minute or two to allow the glue to dry slightly, wiping away any excess from the side of the PCB that has tracks on it. - this is mistake I made, I didn't wipe away enough of the glue and this meant I had to file/sand some away before I could solder the tracks.
- Leave the glue to dry for a minimum of two hours before soldering.
Step 3: Preparing the Surface of the PCB and Soldering
- You will first want to remove any left over superglue that might be on the surface of the PCB, do this using a exacto knife or similar to gently scrape away any excess superglue.
- Then remove the top solder proof protective layer of the pcb with the knife to expose the bare copper tracks to solder to.
Method 1 - small gaps - I used on the area highlighted in BLUE (on the schematic photo)
.Method 1 - the simplest is simply bridging gaps with just solder or solder paste, this can only be done on the smallest of gaps or the solder will simply ball up and not join the tracks correctly.
- Apply a small amount of solder paste to the tracks, about 0.5 mm thick with a knife or something similar.
- Heat the solder paste with the soldering iron, the paste should join the tracks together if the gap is smal enough, if the solder does not you will have to resort to Method 2.
Method 2 - large gaps - I used on the areas highlighted in RED (on the schematic photo)
.Method 2 - more complex but will produce a stronger, more secure bond and is able to bridge large breaks in the track.
- You might need to scrape back some more of the pcb to expose some more copper this allows the wire to be soldered to a larger area of the pcb, making a better connection and much easier to solder.
- cut a thin strand of wire that is the correct diameter relative to the track width - a neat trick is to use multi-strand wire and then break it up into its thinner strands and use them as they can be very thin individually.
- Next place the wire onto the broken track and then hold it in place with solder paste, this is useful as it keeps the wire secure until the solder is melted and secure.
Method 3 - bridginging heavily damaged or small tracks (photo with yellow bridging wire and yellow line in schematic)
.Method 3 - the most bulky form of repair as it requires large wires to be soldered on the PCB.
- Follow the damaged tracks to nearest available solder point, making sure not to skip components. You can follow the tracks by eye or using a schematic.
- Ideally use the smallest guage possible, as this will be easier to solder to the PCB.
- Tin the end of the wire with some solder.
- Solder one end of the wire to one of the components on the broken track and then solder the other end to another component on the other side of the broken track, making sure no components are being skipped when this is done to ensure the circuit is not changed.
Step 4: Testing the Repaired Tracks
Before plugging in the device it is best to test the repaired tracks to make sure there is good continuity between tracks. You will need a multimeter and a schematic of the ciruit will help as this allows points to test the continuity to be found easily. (However, a schematic is not necessary, read on)
Set the multimeter to continuity test mode. (often represented by a diode symbol)
If you have the schematic locate points on the PCB where you can test the continuitity and go through each repaired track making sure there are no bad joints with no join.
If you can't find a schematic follow the traces on the board and test that way instead, this can be hard to do on certain boards but is definetly possible, shining a bright light under the board is often a good way of doing this as it highlights the tracks well.
Step 5: The Finished Product
Once you have tested the PCB try the device and you should have a fixed pcb with full functionality. A video of the now repaired walkman is attatched. Hope this Instructable was helpful and helped you repair your PCB.
I would also like to thank my design technician for assisting me with some of the fine soldering and giving me advice with certain areas of the project.
Trouble shooting: Remember if the device is only partially working but you have repaired all the tracks there is chance there are other issues with circuit that could have been damaged when the PCB snapped e.g components coming off.
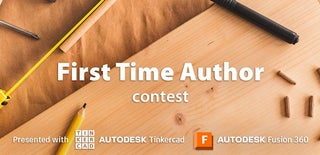
Participated in the
First Time Author