Introduction: How to Restore a Band Saw
Howdy, i'm Dave from Parts and Restoration and today, were gonna fully restore an old band saw! LETS GET TO IT!!
Step 1: ACQUIRE a BAND SAW
To restore a band saw, you first need a band saw worth restoring! Chances are, sombody in a 10 mile radius of you is selling one! Keep an eye to Facebook Marketplace, LetGo, Craigslist, and eBay. Also, machinery auctions (bidspotter.com) and estate sales (auctionzip.com) are great places to find quality used machinery!
Things to look for:
-CAST IRON! Old machines were built well! They were made with heavy castings that cut down on vibration and flexibility! Old castings are smooth, they were cast in clay, modern castings are made with sand and are rough. avoid modern
-Big Heavy Table - Also cast iron, you want the band saw table to be ground flat and made of cast iron. For me, a band saw with a stamped or light weight table is trash.
-Signs of AGE - If its made primarily with plastic, avoid it. Get something made well back when old tools were made with the workman in mind, not with SHAREHOLDERS in mind!
Step 2: Take Your Machine Apart!
This is the fun part! Its gonna get dirty so do this somewhere like a garage or outside. Band saws hold TONS of sawdust inside their wheel guards. If you are lucky enough to find a band saw with a metal cutting gear reduction, you will find TONS of oil and grease inside too!
*VERY IMPORTANT* I would highly recommend video taping yourself disassembling your machine with your cell phones camera. This will come in handy later when you cant remember where some random grub screw was supposed to go!
Keep your parts organized! Keep parts from each sub assembly in a separate box or container. You don't want your screws getting mixed up! Take photos of complicated parts before you disassemble them so you know what they looked like before you started fiddling with them.
Magnetic parts holders are great for keeping track of small screws and parts as long as they are ferrous metals (steel).
Step 3: Determine What Needs to Be Replaced
Chances are, an old machine may be missing parts or have broken pieces from its years of service. Check out www.vintagemachinery.org and search for your band saw by manufacturer to find reprinted PDF manuals and parts lists of common old machines. Ebay is a good source for replacement parts (though they are expensive) and local used machinery dealers may have parts for vintage machinery in stock.
Band saws have some consumable parts in them as well. Check the following:
Bandsaw Tires - The rubber "tires" are the surface of the wheel the saw blade rides on. The old rubber tires may be dry rotted and if so, consider replacing them
Bearings - The wheels have bearings pressed into them. Additionally, bandsaws use ball bearings to help guide the saw blade as well. If they dont spin freely, now is the time to replace them. Industrial suppliers like Granger and local Bearing Distributors can help you replace your bearings if you bring them the originals
Blade Blocks - The band saw blade is guided by metal "blade blocks" that keep the blade straight while you cut. These wear out. A modern blade block called "Cool Blocks" are made of a fiberous material and they are excellent!
The Motor - How does it sound? Does the shaft and pulley spin freely? Its it under powered (some old machines often didnt come with a motor, the buyer supplied whatever motor he had, or could afford)
The Blade - Buy some new blades!
Step 4: CLEAN EVERYTHING
Time to strap on some kitchen gloves and get dirty!
First things first, safety. PPE (personal protective equipment) it essential! Protect you eyes with ANZI approved safety glasses and consider lab style goggles if splash is a concern. Wear gloves when using chemicals. Hospital style gloves are great, and wear chemical resistant gloves when using paint stripper. Respiratory protection is important when sanding or other processes that create dust. PROTECT YOUR BODY!
Step 1. Remove DRY Dirt and Debris First!
Band saws hold TONS of saw dust inside the wheel guards. Be sure to remove all the dry debris out of the machine first before applying any wet cleaning chemicals. Vacuums or air blowers are great ways to remove this stuff. If you don't have a good shop vac or a compressor air gun, PC duster works well too.
Step 2. Cleaning and De-greasing:
I am a huge fan of Krud Kutter for degreasing old machinery although any de greaser will work! Spray on your de greaser and use scrub brushes to work it down into the surfaces. Large faced brushes work well for open, flat surfaces and small brushes (old toothbrushs work great) are excellent for complicated surfaces to get into the nooks and crannys. This step can take a while!
For large parts, especially really nasty ones, put the part in a big plastic tote and pour some de greaser in the bottom and scrub away!
For small parts, place them in a jar or pot of de greaser and allow them to soak. Later, scrub them clean with a small brush.
Once each part is clean de greased, wipe them with warm water to get the de greaser off and pat dry.
Step 5: To Repaint or Not to Repaint?
Right now, you should be staring at a huge pile of squeaky clean cast and machined band saw parts. Years of cigarette tar, saw dust, oil, grease and dirt are a distant memory. Now is the time to ask yourself a few questions. How do your parts look? Are they rusty? Is the paint flaking? Do repairs need to be made? Do you like the color?
If your machine was just dirty, but is in great shape, skip ahead to Step 9 - Reassembly.
Here are my thoughts. You've come this far. If the machine was in great shape, you probably wouldn't be reading this instructable!
If the paint is flaking, repaint.
If you hate the color OR would like your saw to match other machinery in your shop, paint it!
If some jerk painted it a stupid color years ago, Paint it!
Over all, if your gonna restore a machine, PAINT IT!
Step 6: Strip the Old Paint
Uh oh! Time to bust out the nastiest chemical in the shop, paint stripper! I prefer Jasco brand paint stripping gel.
Move your parts to a well ventilated area and don your PPE. Minimum requirement for this job are lab goggles, closed toed shoes (yes I wore shop flops for my restoration and it was dumb!), long sleeves and long pants, and chemical resistant gloves. Get a bowl to pour some stripping gel into and a paint brush. Apply a thick coat of stripper to the surfaces. The paint should quickly absorb the stripper and begin to wrinkle. When, after a minute or so, I see dry spots forming where I applied stripper, I apply some more. Let the stripper work for 15-20 minutes or as directed. Using a metal scraper, scrape away the old paint and discard of it right away, it should scrape up easily. Do this until the bulk of the paint is gone. Use chem resistant plastic brushes to scrub away the remaining paint. Remove any remaining stripper with paper towels. Repeat as necessary until all the paint is gone.
To fully remove the stripper, apply denatured alcohol or acetone to the surfaces and wipe clean. Repeat this until your paper towels are coming up clean.
Congratulations! You are the first person to see this machine in the raw in probably 60 years or whenever it was making its way down the production line!
Step 7: Rust Removal
Now that we are down to bare metal, lets get the rust (if any) off! Your options are to use mechanical abrasive methods (best for large parts) or chemical methods (limited to smaller parts usually). For a run down on mechanical rust removal, check out my down and dirty rust removal video
For small parts, there are some great chemical options! Evapo-Rust is an inexpensive and safe rust removal chemical. You soak your rusty parts in a cup of Evapo-Rust and take it out a few hours later. The rust is gone and a black oxide coating is left in its place that can be brushed to a shine with a wire brush or wheel.
For large parts like castings, I recommend using a wire wheel on a grinder (angle or bench) to remove the rust. Sand paper is an effective alternative if you don't own a grinder. Additionally, Evapo-Rust Gel can be painted onto large parts to chemically remove rust without submersion.
Step 8: Prime and Paint
To allow the paint to adhere properly to bare metal, you need to apply primer to your parts.
Step 1. Before applying any primer, be sure to prepare the clean metal surfaces for priming. Wear clean latex hospital gloves and wipe each part of your machine down with acetone. This will remove any oils from the surfaces prior to primer application.
Step 2. Once the surfaces are clean and oil free, use masking tape to cover up any parts you don't want painted. Some examples are the table top, holes for bearings, any mating surfaces, any machined surfaces that will be sliding or bearing on moving parts or places you expect will be oiled or experience wear.
For metal that still has rust pits that you cant remove or that is still corroded, use a spray on rust converting primer. This stuff will chemically halt the corrosion and convert it into a paintable surface. For clean bare metal, use a Self Etching primer. I personally like Rustoleum products.
Step 3. Apply a 2-3 light coats of primer to your parts or follow the instructions on the can.
Step 4. Once the primer is dry, apply your paint! I recommend using the same brand paint and primer to avoid compatibility issues. I painted my bandsaw with Rustoleum Coastal Grey - Satin.
Be sure to consider applying a clear coat to your paint to seal the surface and give it a more durable finish.
Step 9: Reassemble!
Now that everything has received your TLC and been repainted, its time to put your band saw back together!
Here is where that video you made earlier really comes in handy! Work your way back from the end of your video and try to reinstall parts in reverse order.
Hopefully, you kept all of your parts and hardware organized throughout cleaning and painting. If so, you should have no trouble getting everything back together without having any "spare parts" at the end!
Be sure to lubricate moving parts or places where you expect wear might occur (screw threads, moving parts, parts that touch or slider past each other, etc). Refer to www.vintagemachinery.org to find the manual for your saw!
Step 10: Sit Back and Admire!
Congratulations!! You just rebuilt a heritage band saw! Most people would have been satisfied with a piece of cheap junk from China, but not you! You know quality when you see it! You're likely exhausted from this journey. It has been a labor of love bringing this old gal back to life. Take a few minutes to relax and find comfort in knowing that this machine, built so carefully decades ago by American hands, WILL outlive you, and thats a good thing! Thanks to your labor, your children and THEIR children will be able to make whatever they desire on this, what is now a family heirloom tool that you cared about enough to restore! We are but custodians of these beautiful iron beasts! I hope this guide was helpful for you, and congratulations again for your hard work!
Be sure to check out my youtube channel! www.youtube.com/partsrestorationphilly
Check out my daily photos of my workshop happenings on Instagram! www.instagram.com/partsandrestoration
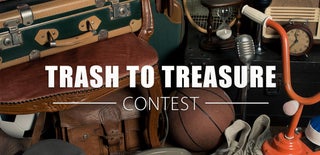
Second Prize in the
Trash to Treasure