Introduction: How to Build an Extreme Fishing Gaff
So you finally went and did it… you broke your fishing rod. Your buddies told you to relax and take it slow but no, you couldn’t let the big one get away and you snapped the rod in two. Now the fish is gone and you have two pieces of a fishing rod. You can stick a metal rod or other type of dowel in it, but you would lose its natural flexibility rendering it unfishable. Or maybe you had a lot of good memories with that old rod your father gave you, but is no longer fishable. Well, I have the solution for you. It will let you keep that fishing rod around for many more years of EXTREME fishing service…build a fishing gaff!
As an avid angler, I like to target larger game. And hooking up a big fish is only a fish story if you can’t land it. This instructable will guide you in your endeavor to building an extreme tool that is both extremely reliable and great looking. On top of making this an extreme tool, all of my projects are done with saving money in mind. A comparable Aftco Gaff with foam grips and not customized can run in excess of $80 plus shipping. This gaff build cost a total of $20 granted you have a broken or trashed fishing rod and some basic tools.
Tool Used:
1. Dremel (or hacksaw)
2. Dremel 420 Cutting Wheel
3. Dremel Polishing Wheel (elbow grease)
4. Hobby Knife
5. Flat Head Screwdriver
6. 100 Grit Sandpaper
7. Vice
8. Drill (with 1/4" drill bit)
9. Ruler or tape measure
10. Dremel Grinding Wheel (grinding stone)
11. Permanent Marker
12. Needle (or something else that is small enough to scratch away paint)
Materials List:
1. Rod Blank (salvaged)
2. Tarred Cord ($11 for 1lb of size 18)
3. 3 inch Gaff Hook (salvaged but can be purchased for ~$8)
4. Black Spray Paint (left over from bike project)
5. 2 part epoxy (dollar store happens to have some decent stuff)
6. Super Glue (8 for $1)
7. FlexCoat Rod Finish ($6/leftover from another project)
8. Masking Tape (dollar store)
Step 1: Strip the Rod Down to a Blank
After inspecting the rod blank and its components, I decided I was going to keep the reel seat, both lock nuts, and the butt cap. The nuts were going to be used as decorative accents, the reel seat would give us a break in the monotony of the grip as well as providing a Daiwa emblem, and the butt cap would keep the blank from loosing integrity from being banged around (not to mention mine had a cool D on the bottom… score!).
With a sharp blade, begin to strip the guides off of the blank. Do so by sticking the blade parallel to the blank underneath the guide feet and cutting down enough to expose [the guide feet]. Once you do so, the guide will become loose and you can simply pull it off. Repeat the process for the rest of the guides.
I kept the under wrap since it had a coat of varnish on it and would provide some decoration. NOTE: If you have a rod that has been exposed to the elements and has a weathered look, the section of the blank that is covered with the under wrap will be a different color, so it is best to keep the under wrap.
To remove the tip top, try a firm twist and pull. If that doesn’t work, you can heat the tip with a torch or lighter to melt the glue used on the tip top and pull it off with a pair of pliers. Some companies will use a heavy epoxy, if this is the case cut off the tip with a Dremel.
To remove the broken part of the reel seat I used a flat head screwdriver and simply pried it off. It was in bad enough shape that a harsh wind would have probably blown it off. Normally I would use the Dremel to score it deep enough to cut through without damaging the other components and pry it off with a flat head screwdriver. Score the other part of the reel seat and remove.
In the middle of a hot barracuda bite, I find there is not enough time to wash off the slime from your hands in between fish, so we are going to be removing the EVA Foam grip, which I find becomes too slippery with ‘cuda slime. Some companies use glue that will soften with heat, and if you want to salvage the foam you can boil a big pot of water and dip the foam in it once it boils. I simply cut the foam grip with a sharp blade and pulled it all off. Once the foam was off the rod, I used 100 grit sandpaper and sanded off the bits of foam and glue that were still stuck to ensure the grips would lay even.
Using the Dremel with a polishing wheel I polished the irrelevant information off of the blank but stopped short and kept the brand and series names. I use a lot of their fishing gear so I thought it to be a good idea to sport my one of a kind Daiwa Sealine fishing gaff. I then removed the tarred cord that was on the blank (boat rail guard) as it was worn and wouldn’t match the new tarred cord I was going to use for the grip. A blade under the first wrap was enough to make quick work of the existing cord. I then cleaned the reel seat with the Dremel and a polishing wheel.
Step 2: Prepping the Blank for the Gaff Hook
In this project I was going to be using a 3 inch gaff hook. The hook was salvaged from a gaff that failed and came with a straight shank, the kind used in the mass produced stock found in stores. While the hooks themselves are of great quality, these gaffs are simply not built to handle the abuse. Attaching a straight shank to a gaff is not very difficult, and provides a decent bond. But I’m not looking for a DECENT bond; I am looking to build a gaff that can pass the “Dave Test” (more on this later).
I used a vice to bend the last 1/4 inch of the shank at a 90 degree angle, and kept tightening the vice on the 1/4 inch part to get two flat sides. At this point I realized the tip of the fishing rod was too thin to support having a hole drilled on the side of it, so I cut off a section of it (about 15inches from the top) until the walls of the fishing rod were at a thickness I was comfortable with.
I measured the length of the hook and marked where I would be drilling a hole through a part of the blank. Using a 1/4 inch drill bit I drilled a hole just enough to get through the first part of the blank. I marked an angle with a sharpie and used the Dremel to cut it out on the opposite side of the aforementioned hole. This angle will allow the tarred cord to slowly reduce circumference and give a cleaner finish. A quick coat of black spray paint around the gaff shank would ensure that if there were any gaps while wrapping they would be less visible. A coat of flat black on the reel seat gave it a clean look that would blend well with the tarred cord (oops! forgot to take a picture at this stage!) . I plugged the large hole with wax and slapped a coat of quick drying glue on top to prevent any water from going into the blank.
Step 3: Wrapping the Grip
In order to wrap the cord without having visible knots on the grip, I wrapped the cord underneath itself. This process was used throughout the entire build and is illustrated in the first image. In order to end the wrap underneath itself you have to lay down a loop 5-6 wraps before finishing and pull the tag end underneath the wraps, clipping any excess tag as close as possible to the grip(illustrated in the second image).
I started by using masking tape as a shim for one of the reel seat nuts and glued it in place at the bottom by the butt cap. I then began wrapping by holding 1 inch of the cord parallel to the blank. I wrapped the cord 5 times over itself to have it hold itself onto the blank. I then pulled it tight and pushed it down to the butt of the blank. I continued to wrap the cord on the blank. Pull tight and push down every 5 turns to ensure a tight wrap. Once I wrapped up to where I wanted (up by the second reel seat nut) I cut the cord about 3 inches longer than needed and pulled the tag under itself. I tightened it by turning it with my hand and pulling on the tag end. I then clipped off the excess as close to the blank as possible and dropped a bead of super glue on the end. I repeated the process above the reel seat, and followed it to just about an inch below the Daiwa sign.
Once the grip was done, it was time to add the gaff hook.
Step 4: The Gaff Hook
A very similar process was used for the gaff hook. I first placed the gaff hook in its final place and noticed it was not lying flat and tried to roll. I took out the Dremel with the grinding wheel and grinded away on the contact areas until it sat on the blank evenly.
I cleaned off the hook with denatured alcohol to remove oils and small debris. I scraped off some of the paint on the blank with a knife and also cleaned it with denatured alcohol to ensure a solid bond. After letting them dry I used a 2 part contact cement to affix the gaff hook in place and seal up the hole I drilled for it. I let it cure for 4 hours and, instead of waiting for spray paint to dry, I painted the gaff hook with a sharpie to avoid any of the bright metal to shine through the cord. Then I wrapped the gaff hook.
I began wrapping the hook from the top. Running a length of cord along the side, parallel to the blank and gaff shank, I wrapped it 5 turns and tightened like before. I carefully followed up the bevel to ensure there were no gaps and tightened down every 2 wraps and periodically placed a drop of super glue on the blank. Once I finished wrapping the gaff hook to the blank I gave it 6 more wraps and threaded the cord under itself like before. I then clipped the cord and dropped a bead of super glue.
Step 5: The Dave Test
…Attaching a straight shank to a gaff is not too hard, and provides a decent bond. But I’m not looking for a DECENT bond; I am looking to build a gaff that can pass the “Dave Test”…
I’ve seen it happen to others and has happened to me in the past… You hook into a monster fish, fight it for what seems like an eternity, and finally manage to get it tired enough to come boat side to sink in your machine made gaff. YAY!!!! You start to pull up on the gaff to collect your prize only to have the catch of a lifetime give its last attempt at escape. That’s when you hear a crack as the machine made gaff gets light. The hook broke off and now the fish is back in the water. You’re left with a very mad fish swimming away with your gaff hook on its back… leader, rod, and reel still attached. If you are lucky, you managed to snap off the line and not lose more gear. But in the end, it sucks to be you!
The Dave Test is here to help you avoid that situation using a very simple approach. The ingredients needed are your freshly built gaff, some nylon straps, and Dave… I’m Dave. Using nylon straps I tie two knots onto the gaff, one by the hook and one by the grip. I go out back to my shed, hang the gaff from a rafter, pull on it?… no, HANG ON IT! Tipping the scale at 250+ if the gaff can hold me, it’s good to catch a sea monster! Assuming you’ve passed the Dave Test, it’s time to finish it up!
Step 6: Turkâs Head Knots and Other Details
As a statement of my success I scribed my team name above the Daiwa logo and signed and dated the gaff underneath.
Using a needle I scratched off the paint from the Daiwa logo on the reel seat which gave it a nice accent.
With a two part rod wrapping finish (Flex Coat) I coated the Daiwa logo, my team name, and the painted and scratched reel seat. The end product yielded a beautiful in its own right, remarkably durable fishing gaff capable of handling the most extreme of fishing excursions.
I've yet to catch something worthy of using the new gaff. But here's the one I made for my buddy in action.
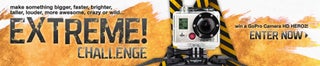
Participated in the
EXTREME! Challenge