Introduction: How to Make a Knife - the Newbie Guide.
Okay, this is my first attempt at making a knife and it was more of a trial run to get the hang of the process. I thought I would publish this instructable all the same as there may be other novices out there that want to give it a go and are not sure where to start - and since I have researched the topic quite thoroughly and now successfully made a knife myself, I may be able to provide some sort of insight.
It is worth mentioning that this knife isn't heat treated in any way as it is made from 304 grade steel, which doesn't take well to heat treatment and needs to be done professionally. I will be posting a series of instructables later on in which I will be using steel that is more generally used in knife blades - and I will TRY and heat treat the blade.
Step 1: Step 1: Materials You Will Need.
- Metal - Preferably flat bar as it won't need as much shaping. I used 304 grade steel, but as this knife isn't going to be for heavy use, any steel will do.
- Wood - Preferably a hardwood as it is easier to work with (IMO) and will result in a sturdier handle. A wood with a unique colour or grain will also look better once finished. If you want a really unique and beautiful looking handle then try and obtain a sample of wood with either a burr (burl) or a spalted finish. Admittedly, the wood I used was from a dead tree in my neighbour's garden, so I have no idea what it is, but it seems tough enough and was nice to work with.
- Aluminium rod 3mm (1/8") diameter - This is to partially hold the pieces of handle to the blade. You can use brass, nickel or steel rod instead, but I like the silver finish the aluminium gives and since it is a soft metal it is easier to work with. This can be bought off of eBay for about 99p for 6 inches worth.
- Wood stain, wax, or oil - This is to finish the handle once the knife is made, it is not essential but will bring out the grain of the wood a bit more and make the handle look much nicer. I used Danish oil which actually stabilises the wood slightly and gives a great finish.
- WD40 - This is used to buff the end piece.
- Cyanoacrylate (SuperGlue) - This is to fill in any remaining pores in the wood and give a mild sheen or high-gloss finish to the handle.
Step 2: Step 2: Tools/ Equipment You Will Need.
- Grinding wheel - I found it easiest to use a bench grinder to rough out the blade's shape and edge.
- Angle grinder with sanding and grinding wheels - This is essential as it significantly reduces the time spent sanding and polishing in comparison to doing it by hand. It is also used in one of the first steps to grind the shape of the blade out.
- Goggles - For obvious reasons; I actually got a shard of metal in my eye and it hurt like hell.
- Face mask - Same as above, I didn't use one for a majority of this instructable and was also in a fairly confined space, the result was me coughing my guts up and suffering a sore throat over the following few days. Some woods will actually contain all sorts of nasty things, from mould spores to mites or disease riddled sections of wood, so a mask is a really good idea.
- Wood saw - This is to cut the handle, a powered saw would also be good but some bits I preferred to do by hand.
- Hacksaw - This is for cutting the metal to a rough shape, I used a reciprocating saw to save time and effort but for some bits it would be preferable to have greater control over when cutting.
- Ball-pein hammer - This, for those that don't know, is similar to a regular claw-hammer only with a rounded 'ball-pein' in place of the claw. This is to flare the heads of the pins going through the handle so that they hold the handle together.
- Vice - Clamps will also do, but a vice is always a workshop essential for holding work pieces in.
- Anvil - Seems a little bit unusual but it essential to have a hard metal surface to use when fixing the handle together. I don't actually have an anvil, I used the flat metal surface at the back of my bench vice, but an anvil is perfectly suited for this step.
- Drill - This is to drill the pin holes in the metal and handle.
- 3mm & 4mm Metal drill bits - These are for drilling the metal and wood also, the sizes will be covered briefly later.
- Countersink - To countersink the drilled holes in the wood.
- Belt sander - Not essential, but much easier if you have one.
- Epoxy resin - Or a similar very high-strength adhesive. It seems epoxy is the preferred and recommended glue though as it can be easily sanded and polished once fully cured. Do not buy the rapid set form of this, it does not dry as hard and also gives you less time to work with at a crucial stage.
- Polishing wheel - This will be used when finishing the blade and handle after is all put together and sanded down in order to give a nice smooth, slightly shiney finish. It is only really needed for woods and metals, but I suppose it could polish up plastics too.
- Centre punch - This is to dent the metal prior to drilling a hole, it will prevent the drill bit from slipping and keep it exactly where you need it.
- Double-sided sticky tape - This is useful to hold work pieces in place on a worktop without putting them in a vice, this is also not essential but proved useful to me.
- G-Clamp - One or two small G-clamps will be very handy when assembling the handle.
- Sand paper - Grits needed: 80, 120, 240, 320, 400, 600, 1200. Wet and dry paper would probably be best.
- Dremel - Not entirely necessary but makes a lot of the end steps much easier.
- Gloss brush - This is to coat the handle in oil if treating the wood, a brush with finer fibres seems to give more even penetration.
- Pack of disposable artists brushes - This is for the superglue coating at the end. It is easier to use a disposable brush, throw it away and then use another disposable brush afterward than it is to clean a brush properly between every coat.
Step 3: Step 3: Design Your Knife.
First thing you will need to do is come up with a rough idea of what your blade will look like. It doesn't have to be to scale, just sketch a few ideas and decide on one of them according to the following criteria:
- How good it looks - Pointless making a crappy looking knife.
- What it will be used for - If you need it for hacking shrubbery then it's not feasible to use a tiny little knife. Similarly, if it is to be used as a fishing knife then you don't want to design a whacking great machete/ hatchet.
- Materials required for design, and what is available to you - I only had thin steel available to me, so the knife I made has a slimmer, less elaborate design than some of my original sketches.
- Practicality of design - If the design had wildly eccentric curves, cut-outs and pointed sections then it isn't really going to be useful in any real-life scenario.
- Ease of construction - The more extravagant the design, generally, the harder it is to make.
Really think about the design, incorporate features that you think will be useful; for example, a thumb guard, a serrated edge, whether it will be curved or straight, the materials for the handle etc.
Once you have decided on the design you will be using, draw it again, but more to scale so that you can get a real idea of the size and shape of the finished product.
Once you have this, you need to transfer the design to your metal, unfortunately I did not photograph this, but you will see my rough metal design in Step 4. I simply copied my design from the paper to the metal but some may want to cut their design out and stick it to the metal itself - whatever you find easiest.
Step 4: Step 4: Cut Out the Blade.
To cut the metal I used a reciprocating saw to get as close as possible to the sketch outline - but you can use a hacksaw or bench saw of some description - and then I used an angle grinder to grind the rest of the way down to meet the lines I had drawn.
Take your time with this or you could cut/ grind too far and have to start all over again. It is also an idea to enlarge your design by 1mm or 2 in each direction to give you some extra material to play with later on - you may decide to accentuate the curves of blade, or that you need a thicker/ thinner section, the extra material will allow for this.
Step 5: Step 5: Give the Blade an Edge.
First, draw the extent of the edge onto the metal - one thing I have found out during my extensive research prior to making this knife, is not to bring the edge further than halfway across the width of the blade, preferably not much more than a third of the way, as this significantly reduces the blades strength(and does something else that I can't remember but is equally as serious). This point seems to be thoroughly reiterated across a majority of the knife making, blacksmithing, and metal working forums and sites, so I would not take the warning lightly.
Once you have your edge drawn onto the metal though, it is time to grind that edge into fruition. Use a bench mounted grinding wheel for this because it is so much easier than any alternative I can think of. You could use an angle grinder or sander of some sort but this will take about 7 million times longer. Some people even prefer to do this entirely by hand, using a double-edge file, but I can imagine that would take days.
Bench grinders usually have two wheels on them, a rough abrasive and medium abrasive, use the rough wheel to get as close to the line as possible and then use the medium finish wheel to go over the edge, neaten and refine it. You will want to go along doing either side of the blade evenly - so go along one side of the edge, then flip the knife round and do the other side - this will help you keep the sides even and the cutting edge centred.
You should now have something that vaguely resembles a knife. The blades edge will most likely not be razor sharp at the moment but it will sharpened slightly later on, and once the entire knife is finished, you will need to get the edge you want using an oil stone.
At this point you will also need to drill the holes in the handle; use a 3mm drill bit for the pin holes and a 4mm drill bit for the lanyard tube hole(keyring hole) - if you are making use of such features.
Step 6: Step 6: Make It Shine.
To get a nice even, shiney finish across the entire knife, you need to sand it using a variation of grits - ranging from 80 all the way to 320+.
I started by sticking the knife to the worktop with some double-sided sticky tape and going over the flat of the knife with the angle grinder and a sanding wheel. I started at an 80 grit to remove the worst of the scale from the metal and worked my way up: 80 - 120 - 240 - 320 - 400. I didn't bother sanding the handle section any higher than a 120 grit because when it comes to assembling the handle, you will need to scratch up the surface of the metal tang handle section so that the epoxy has something to key into.
After you have smoothed the knife body you will need to place the knife into a vice - using padding on the jaws to prevent denting of the metal - and repeat the above process for the blades edge. Once you have sanded the edge to an even level, you will need to decide on the blade angle:
The blade angle your knife will require will be dependent upon its purpose; Machete's, sharp hatchets and other tools used for chopping will use an angle of about 22 - 30 degrees half-bevel for durability, but this won't slice very well; 17 - 22 degree angles tend to be that used for kitchen knives, they are fairly durable but also fairly sharp; 10 - 17 degree blade angles are still used for knives but generally limited to flesh slicing knives such as those used by butchers or fishermen, but at these angles the blade cannot be used for chopping; under a 10 degree blade angle is reserved for razor blade straight edges where they are subject to very little abuse and can therefore maintain their edge with little damage. All the above angles are measured from the centre-line of the blade to one outside edge angle; so for example, the 22 - 30 degree category is only taking into consideration half of the blade bevel(sliced down the middle), so the actual total angle of the blade edge would be 44 - 60 degrees.
The angle I used was somewhere around the 17 degree angle(34 total angle), as I will be using this knife for general purpose cutting, but also wanted to keep it quite close to a gutting knife. I will try and maintain a 17 degree angle(34 total angle) when finally sharpening on an oil stone, and then see how this fairs against day-to-day use - I can always blunt or sharpen the blade slightly later on.
Step 7: Step 7: Making the Handle Scales.
The handle scales are the two sections of handle fixed to either side of the metal on a full-tang knife configuration.
The scales are shaped from a block, or branch in my case, of wood. It is better to use a hardwood with a tight grain for strength, comfort and durability. A coloured wood with a unique grain would make the nicest looking handle, but it is all about preference. A lot of people like making handles from woods such as: Zebrawood, Bocote, Cocobolo, Ebony, Koa, Lignum Vitae, Purpleheart, Bois D'arc (Osage Orange) etc. It is worth taking some time to choose your wood as each has its pro's and con's, I just used the wood available to me at the time.
Blocks of wood can be bought on knife making sites, or alternatively you can buy chopping board samples from kitchen stores for a couple of quid, and these are often quite beautiful hard woods. Another alternative is to cut a branch off of a tree like I did, but this does mean you will have to completely dry it out and you will also need to use some sort of wood treatment in the end. Trees can also contain all sorts of mould spores, or similar, making them hazardous to inhale - so this option is only really a last resort is you haven't any decent wood about.
To get started, you will need to cut your block/branch section of wood in half length-ways so that you have two identical and opposing halves. You then need to roughly draw around your knife handle tang, but enlarging it slightly, onto both wood scales. Cut the scales right down as close as possible to the handle outline but make sure you leave enough space to sand it to the desired shape. Place the tang back onto both sections of wood and mark the drill hole points.
Carefully drill the marked points with the 4mm drill bit and then ensure that all the holes line up as required. You will then need to countersink the drilled holes on the outer-side of each scale. This is so that when you place the Aluminium pins through the entire handle - wooden scales, tang and all - you can mushroom both ends of the pins, holding the handle together, without splitting the wood.
Finally, sand the inner faces of the scales so that they are flush and smooth, this will remove the drawing of the tang position but it should no longer be need as you have already drilled the pin holes.
I have included a diagram labelled with the names of each section of a full-tang knife, this should help you keep track of what is being referring to throughout this instructable, if you don't know already.
I do not own the rights to the labelled diagram of a full-tang knife, all rights are reserved by the original author.
Step 8: Step 8: Whack It Together.
The first thing you will need to do is place all three sections of the knife together as they would go when assembled, and mark the aluminium rod about 5 or 6mm longer than the complete width of the handle. Cut the appropriate number of sections of rod with a hacksaw and then, one by one, place them into a drill chuck and use the drill to chamfer their edges ever so slightly on a piece of sanding paper. To clarify, you will need to place the aluminium rod section into the drill chuck and tighten it, you will then need to hold the drill at roughly a 45 degree angle and use the drill to spin the aluminium rod in a regular clock-wise direction as if drilling, whilst holding the tip of the rod on a piece of sand paper - this will remove any burrs on the ends of the metal rod from cutting it, and will also make it easier to push through the handle section. Do this for each end of all aluminium pins.
The section of the metal tang that will be in between the wooden scales will need to be scratched up a bit before you glue it all together; the rough surface of the metal will act as a key for the epoxy to adhere to. To create the 'key' in the tang, stick the entire metal section to the worktop with double-sided sticky tape and rough up the surface with the coarsest sandpaper you have. Scratch it in different directions until you can feel the small abrasions in the metal with your finger - don't scratch it to the point that it alters the thickness of the tang! Now wipe off any metal dust so as to make sure it doesn't affect adhesion.
Once you have all of the components needed for the knife it is just a matter of assembly. Lay the scales on the worktop, inside facing up, and grab your epoxy resin. You want to use a moderate amount of epoxy, the excess can always be wiped off when the knife is assembled. The epoxy resin will come in two syringes that are attached to each other, one is the epoxy resin itself, and the other syringe contains some sort of hardening agent. Once you have applied the adhesive to both scales, making sure you have placed a small amount in each pin hole, you need to thoroughly mix the two liquids together for about 30 seconds. This mixing process is very important as it will define the strength of the cured epoxy resin, it will also alter the curing time, so ensure the two liquids are thoroughly mixed.
The scales are now ready to be fixed to the the tang; place the two aluminium rods through each hole of one scale whilst it is still laying in the same position, place the metal section of the knife on top using the pins as alignment guides. It should look like the image above, only with a lot more adhesive on it. Place the other scale over the top of the tang, again using the pins for alignment, and firmly press together.
Pick the entire knife assembly up, careful that the pins don't fall out, and lay it on a hard metal surface - such as an anvil or, as I used, the rear section of a bench vice. Using a small G-clamp, hold the scales and tang firmly in position and then place one end of the knife assembly onto the metal surface so that the aluminium pin is resting on the metal. Grab your ball-pein hammer and start striking the head of the pin that is supported underneath by the metal surface and is poking out of the top of the handle. Hit it three or four times, then spin the knife around the hit the other end three or four times. Keep doing this until the aluminium flares out on both sides evenly and the pin is fixed in place. The aluminium should be almost flush with the surrounding wood but not quite - protruding about 1 or 2mm out of the handle. This will be sanded completely flush once the epoxy has dried and the handle is secure. Repeat the above process for all of the handle pins you have, then remove the G-clamp, wrap the entire handle in paper or card and clamp firmly into the bench vice. You will now need to leave the epoxy to fully cure for a minimum of 24 hours - some even say to leave it a week!
Step 9: Step 9: Moulding the Handle.
After the epoxy has fully cured (mine took around 48 hours rather than 24 due to its curing environment), remove the knife from the vice and gently test the strength of the handle, any movement and you'll need more epoxy and then another 24 hours or so for it to fully cure and harden once more.
If the epoxy has fully cured and set solid, and the handle is nice and sturdy, then you can begin to shape your handle. To begin with I laid the angle grinder upside down on the worktop and lightly dragged the handle across it as the sanding disc spun. I only did this to reduce the size of the scales slightly and bring them closer to the tang, a majority of the actual moulding of the handle needs to be done by hand - unfortunately.
To shape the scales to match the tang, I placed the blade in a vice with the blade wrapped in a sponge, and used a dremel to gently sand out the grooves of my handle. Once I had the shape I wanted I began rounding the entire handle, still with the dremel, so that the knife would better fit into my hand.
With the handle completely shaped I began going over what I had already done with a succession of sandpaper grits; starting with the 240 grit and working through with the 320 and finally 400 to get a nice even, smooth handle finish. By the end the handle had an ever so slight sheen to it as if it had been polished slightly - it is now ready for some sort of treating.
Step 10: Step 10: Treating the Wood.
For this step I used Danish oil to treat the wood; I found that it really accentuates the natural colour of the wood and brings out the grain pattern, I didn't want any sort of artificial finish that you get from a dye or stain.
The Danish oil does contain certain preservatives that will prevent the wood from rotting and wearing down over time slightly but it does not completely seal the handle, for this I will be using cyanoacrylate - or super glue as it is commonly known. It may seem strange to use super glue to finish a knife handle but it dries solid and transparent, completely sealing the wood, and it can also be sanded and buffed to a mild sheen or even high polished finish.
To start, wipe off any dust on the handle with a mildly damp rag, let the handle dry completely while you set everything up. Use a Tupperware tub or similar to pour the oil into, and then soak a brush in the oil, leave it in the tub for the time being.
Wrap your knife blade in some sort of tape so that you can hold the knife by the blade without slicing your hand open. Then place the knife, handle first, into the tub of oil and generously smother the oil over the wood. Try and use the brush to rub the oil into the wood before smothering it with yet more oil and repeating. Do this about 5 or 6 times, careful to cover the entire wood surface evenly, and then leave sitting in the oil for 10 minutes or so.
Come back every 10-15 minutes and repeat the above process of lathering the wood handle in oil, working the oil into the wood and then lathering it in oil again - do this anywhere from 5 - 15 times until the wood looks as if it can absorb no more oil. At this point, place the knife back into the vice by the blade, place the tub underneath the handle so that any excess oil can run off into it, and coat the handle one more time. Leave for half an hour to 45 minutes until the oil starts to thicken and go slightly 'tacky', at this point you need to wipe off this tacky oil with a rag and then leave the handle to fully dry over 24 hours.
NOTE: After wiping the tacky excess oil off of the handle, place the rag outside, away from the house, as they have been known to spontaneously combust! I have not experienced this myself but many people in forums and in video tutorials talk about their experience with spontaneously combusting oil rags burning their workshops.
Step 11: Finishing.
Originally I wanted to get a high-gloss finish for the handle, giving the wood a 'wet look'. I used the superglue method; coating the wood in multiple layers of cyanoacrylate(superglue) to fill in the pores of the wood, and then sand down and buff to provide a shiney, transparent coating.
This I had a lot of trouble with, the method is simple enough; you apply about 2-5 coats of superglue with a brush, allowing them to dry fully each time, then lightly sand down the surface using a high-grit sand paper to remove any surface imperfections. You repeat this over and over until you have built up roughly 50 coats of superglue, you then sand down the finish using a multitude of high-grit sand papers starting from about 400 and working your way up to 1000+. Once you have a smooth finish, you use a clear wood wax and buff the handle to a high-shine glossy finish, the results are pretty impressive and it also gives a really quite durable surface.
That was the plan anyway...
All of the forums I read up about it on seems to leave out a few key details for this method though:
- First, don't breath on the drying superglue. Don't blow on the glue to try and speed up its drying time, don't even put your face near the glue, the moisture in your breath reacts with the curing glue and causes it to go foggy - which prevents you from getting the results you want from the superglue.
- Second, the weather and temperature affect the process just as much. If it is humid, like when I was trying to do it, it causes the glue to go foggy. If it is damp in your workshop, like mine was, it makes the glue go foggy. If it is too cold, then it prevents the glue from drying properly and it comes off really easily, the temperature will most likely also cause condense to appear on the metal tang and make the glue go foggy. If it is too hot, the glue dries too quickly and it comes off really easily. If there is ANY dust of any kind in the air, IT WILL find its way to the gluey handle and stick to it and you will need to sand the glue back and build it up again. Direct sunlight will also affect the curing process of the glue and most likely reduce its integrity.
- Third, you need to make sure you are using the right stuff. I did use the right stuff but there seems to be a lot of people out there that got the impression that they could use any glue and that it would work the same - wrong. You need to make sure you are using pure cyanoacrylate, or ethyl-2-cyanoacrylate, not impact adhesive or regular glue as these are rubbery when fully cured and not transparent. You also need to make sure it is the medium viscosity, or thin superglue, and not the thicker stuff as this takes a lot longer to dry and will prolong this step even further.
- Fourth, you will use a whole bunch of brushes, at least 10, for this process. Buy a pack of cheap painting brushes, the cheapest you can find, and make sure you have AT LEAST 10. You will go through them really quick and the glue will leave them useless - obviously you can spend ages using spirits or acetone to remove the glue from the brushes, but it really isn't worth the time.
- Fifth, you will use A LOT of glue. Buy the biggest pot of superglue you can find, I went through a 5g bottle of Loctite on one handle and didn't even get the desired finish. I bought 50g bottle of industrial stuff for next time though. I also recommended that you buy a curing accelerant to help speed this step up, simply carry out the steps as before but give a quick spray of accelerant after each application of glue and it will cure much faster. Try to buy an accelerant made by the same manufacturer as the superglue, this helps prevent any further complications.
- And finally, don't stand over, or put your face too near to the superglue. It is incredibly potent and the fumes make your eyes water and airways sting if you encounter them for too long. There are health warnings with superglue but you can read up on those in your own time if you really want to know the details, my advice would just be to not do this step in a cramped environment but use a well ventilated area if possible.
Okay, so now for what I did:
As I said, the above process didn't entirely work out for me because of the weather, so I ended up sanding down the glue to the point that it was only filling in the pores of the wood and nothing more, but the knife still ended up with a really nice sheen to it and a perfectly smooth finish. The Danish oil I had used previously was enough to stabilise the wood and make the handle solid so I didn't worry about the high-gloss glue finish in the end.
When I realised the glue had messed up I simply sanded the worst of it off using a 240 grit sand paper, then I sanded over this with a 320 and then 400 grit. Once the handle was even and the glue was completely flush with the surrounding wood, I sprayed the handle with WD40 and used some 600 grit wet and dry to get an even smoother finish. I finished the handle off by using more WD40 and a buffing wheel attachment on a dremel to simply polish the surface of the handle, then I wiped off the WD40 with a cotton rag and the handle was done.
I sharpened the blades edge using a regular kitchen knife sharpener and then refined the edge further using an oil stone. To use an oil stone you do need oil, soak the stone until it cannot absorb any more oil and then gently and swiftly drag the blade edge across it at an angle. This will take some time as it isn't really the stone itself that sharpens the blade but the oil/stone-grit mixture created from the process, and this takes a while to develop. As far as I know, the type of oil isn't too important - people use olive oil, WD40, unused motor oil, all sorts.
Check the blade edge every now and then until you are happy with the result and then just wipe off the remaining grit paste with a rag. Hand-buff both the handle and blade with the cotton rag and you are done!
The result wasn't too bad for my first attempt, though next time I will use some better suited steel such as 440c or 01 tool steel, and I will also heat treat the blade. I will most likely use either a pre-stabilised wood block next time, or I will stabilise the wood myself if I have time to build a pressure chamber.
Step 12: Post-project Notes.
1) I have stated above that the superglue finish didn't work out for me and that I finished the knife by sanding the handle down to the point that the glue had done nothing more than fill in the pores of the wood - this, I have recently found out, isn't accurate.
I have just started another instructable for a different knife design and have got to the stage of sanding the handle smooth after the Danish oil had completely cured; however, the finish after I had done this is not in any way similar to that found on this knife - there is a slight sheen to the wood and it is relatively smooth, but nowhere near the rock solid, smooth and shiney finish of this knife. So in summary, the superglue finish applied to this knife did work and it worked very well, I must of needed to simply apply a few more coats of glue and then buff the handle for a while longer to achieve the super high-gloss finish I was after. I will continue using the aforementioned method to finish my knife handles.
2) After finishing the knife I did manage to find out what the tree was that I used for wood - a twisted wych elm. And although the branch I used had started to rot slightly and consequently had large pores and a seemingly loose grain, wych elm wood is actually a very good wood to use for such a project:
'Elm wood is strong and durable with a tight-twisted grain, and is resistant to water. It has been used in decorative turning, and to make boats and boat parts, furniture, wheel hubs, wooden water pipes, floorboards and coffins.'
It is called a twisted elm because of the twisting fashion in which it grows and how this results in a dense, twisted grain in the wood. I am really glad I ended up using this wood as it has an interesting grain pattern, nice colour to it and has resulted in a hella-sturdy handle. It is also nice that my knife is made from a local tree rather than just some off-cut from a shop.
If you have any questions then do leave me a comment, but I do also recommend visiting such sites as: bladeforums.com, knifeforums.com, iforgeiron.com, knifenetwork.com, ukbladesforum.co.uk, and my personal favourite that I found to be most useful - britishblades.com. It is also worth checking out the instructables site because there are some really good tutorials on here with some really sound advice - I read through quite a few instructables prior to starting my knife. I have favourited some of the best tutorials if you need help finding the specific tutorials I am referring to.
Thanks for viewing!
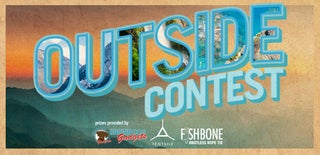
Participated in the
Outside Contest