Introduction: How to Make a Wooden Legend of Zelda Master Sword
Here is how I used a stainless steel replica I bought from ReplicaDungeon of the Legend of Zelda: Twilight Princess Master Sword as a guide to make the same sword from wood and PVC and acrylic. Since I am a member of the Makers Local 256 hackerspace I had access to an entire woodworking shop as well as a 40 watt laser cutter to cut shapes from acrylic sheets. You could do the same thing with a knife only it will take a bit more time. You also can substitute the acrylic for something like foamboard if you don't want the translucent jewel appearance and just use a knife to cut the shapes from that.
One of the main reasons I set out on this adventure was because DragonCon made me peace bond my metal sword so I couldn't pose with it in pictures. I thought with a plastic looking wooden sword they wouldn't have any issues.
One of the main reasons I set out on this adventure was because DragonCon made me peace bond my metal sword so I couldn't pose with it in pictures. I thought with a plastic looking wooden sword they wouldn't have any issues.
Step 1: Materials
40 inch x 6 inch plank of pine. (I recommend you use MDF instead of real wood. Sanding and cutting will be 100x easier).
2 sheets of 1/8 inch thick 6 inch square craft plywood.
1 10 inch long piece of 1 inch PVC pipe.
2 3.5 inch square end pieces of a 2x4.
1 10 inch square sheet of 1/8 inch clear acrylic.
Tennis racket grip tape.
Blue painters tape.
Wood Glue.
Super Glue.
Wood Putty.
Spray paint primer.
Gold spray paint.
Translucent red (tail light) spray paint.
Blue spray paint.
Flat black spray paint.
Silver spray paint.
Spot glazing putty. http://goo.gl/LqScKA
2 sheets of 1/8 inch thick 6 inch square craft plywood.
1 10 inch long piece of 1 inch PVC pipe.
2 3.5 inch square end pieces of a 2x4.
1 10 inch square sheet of 1/8 inch clear acrylic.
Tennis racket grip tape.
Blue painters tape.
Wood Glue.
Super Glue.
Wood Putty.
Spray paint primer.
Gold spray paint.
Translucent red (tail light) spray paint.
Blue spray paint.
Flat black spray paint.
Silver spray paint.
Spot glazing putty. http://goo.gl/LqScKA
Step 2: Cut Out the Blade
I first had to get the blade down to 1 cm thick. I used a 1/2 HP planer to shave the plank of pine down to 1 cm.
I already had a metal version of the sword from ReplicaDungeon so I laid the sword on top of the plank of pine and used a red sharpie to trace the outside of the blade.
I then used a jigsaw and scrollsaw to cut out the blade close to the line but not right one the line. Keep the trimmed off pieces to use to fill in the wings in the next step.
Then I used a belt sander held by a table vice as a table sander to sand the wood down to the line I traced to make it very accurate.
I had to use a sanding bit on a dremel (I know! A hackerspace has a LOT of tools!) to sand down the hard to reach places.
I already had a metal version of the sword from ReplicaDungeon so I laid the sword on top of the plank of pine and used a red sharpie to trace the outside of the blade.
I then used a jigsaw and scrollsaw to cut out the blade close to the line but not right one the line. Keep the trimmed off pieces to use to fill in the wings in the next step.
Then I used a belt sander held by a table vice as a table sander to sand the wood down to the line I traced to make it very accurate.
I had to use a sanding bit on a dremel (I know! A hackerspace has a LOT of tools!) to sand down the hard to reach places.
Step 3: Cut Out the Wings
I took a picture of the wing area of the sword then measured the width of the wingspan tip to tip and loaded the picture up in GIMP software. I resized the image so that it matched the real life size and printed it out. Then I cut it out and laid it on the plywood boards and traced it.
Then I cut those out with the scroll saw. I then laid the new plywood wings on the blade where they go and sandwiched two pieces of the scrap pine plank. I then traced the edges of the wings on to the scrap pieces and cut those out so they will fill in the spaces where it was wider than the plank was. You can skip this step if your plank is wide enough for both wings.
I then used wood glue to glue all these pieces in place and held it together with small wood clamps and let the glue dry.
Then I cut those out with the scroll saw. I then laid the new plywood wings on the blade where they go and sandwiched two pieces of the scrap pine plank. I then traced the edges of the wings on to the scrap pieces and cut those out so they will fill in the spaces where it was wider than the plank was. You can skip this step if your plank is wide enough for both wings.
I then used wood glue to glue all these pieces in place and held it together with small wood clamps and let the glue dry.
Step 4: Bevel the Blade Edges
While the wings were drying I measured how far in the bevel goes from the edge of the blade inward. I then drew a line on the blade at that same distance all around the edges. I then measured 2 mm in on the very edge of the blade (where it's "sharp") from both sides and drew those two lines all the way around. I then used a sanding drum on the dremel to sand down the blade so that it made a straight edge from the inner line to the edge line on both sides all the way around. I made sure to leave the blade flat around the little wider spot near the wings where the triforce symbol goes.
Step 5: Make the Donut and Handle
Again I got lucky with having access to the makerspace and used the wood lathe to turn a square end piece of a 2x4 into a cylinder.
I then used that cut out of the paper wings I printed to match the curve of the donut dome.
I made sure the dome stopped about 8 mm from the bottom edge to leave a level section all the way around for decorative triforce symbols.
I then used a 1 inch drill bit on our drill press (I know!) to drill a hole in the middle for the PVC pipe handle to fit through.
I had to trim down the part of the blade that fits in the inner diameter of the PVC pipe handle making sure it is a tight fit.
I then slid the donut on then slid the PVC pipe on. I then put gobs of wood glue all around both sides of the dount, in the donut hole, and down in the PVC pipe handle.
I then used that cut out of the paper wings I printed to match the curve of the donut dome.
I made sure the dome stopped about 8 mm from the bottom edge to leave a level section all the way around for decorative triforce symbols.
I then used a 1 inch drill bit on our drill press (I know!) to drill a hole in the middle for the PVC pipe handle to fit through.
I had to trim down the part of the blade that fits in the inner diameter of the PVC pipe handle making sure it is a tight fit.
I then slid the donut on then slid the PVC pipe on. I then put gobs of wood glue all around both sides of the dount, in the donut hole, and down in the PVC pipe handle.
Step 6: Make Decorations
I then made the decorative end of the handle from the other 2x4 end piece on the lathe by turning it down to a 1.5 inch cylinder then putting the beveled edges on it with a table sander while turning it manually in my hand.
I then used a 1 inch woodboring drill bit on the drill press to put a 2 mm hole in the end of this handle piece so it could sit over the PVC pipe end and have a place for the glue to grab. I then stuck it on and wood glued it like crazy.
I then used a sanding drum on the dremel to sand out the notch at the top of the wing plywood pieces. I then held the dremel at a 45 degree angle so I could cut out "V" grooves in the wings to give the look of separation and a nice 3D effect.
I went ahead and sanded down the edges of the wing sandwich so they were rounder and smoother.
I then used a 1 inch woodboring drill bit on the drill press to put a 2 mm hole in the end of this handle piece so it could sit over the PVC pipe end and have a place for the glue to grab. I then stuck it on and wood glued it like crazy.
I then used a sanding drum on the dremel to sand out the notch at the top of the wing plywood pieces. I then held the dremel at a 45 degree angle so I could cut out "V" grooves in the wings to give the look of separation and a nice 3D effect.
I went ahead and sanded down the edges of the wing sandwich so they were rounder and smoother.
Step 7: Time for the Putty!
I wanted the sword to look like it was made of plastic and or metal if I could. Or at least avoid it looking obviously like wood. So to cover up the wood grain and knots I smothered all the wood pieces with wood putty. To make it easier to spread so it could fill in the tiny grains and knots I kept a tub of water nearby and dipped my hands in it and spread it with my soaking wet hands. After the wood putty dried overnight I sanded it smooth. I used a palm sander (I know!) to get this done within an hour or so. Once I thought it was plenty smooth I gave it coat of grey primer spray paint. After primer dries it makes it easy to see where the imperfections are. I then circled these bad places with a sharpie and filled those places in with spot gazing putty. After that dried (sometimes for a few hours sometimes overnight) I sanded it smooth again. I hit it with another coat of primer to check for more bad places. I had to repeat the primer, glaze putty, sand, primer steps twice until I was happy. It was also getting close to DragonCon 2012 so I had to hurry. I gave it one final coat of primer and let that dry.
Step 8: Painting Is the Easy Part
Next I began to practice how I would put the grip tape on the handle. So I used an extra piece of PVC pipe to figure out the best way to put the tape on. I laid a length of the grip tap along the table and used an exacto knife to cut it in half so it wasn't so wide. I then laid it out on some cardboard outside and spray painted the white tape the same blue as the wings and handle end would be. I would practice wrapping the tape while the paint dried from these steps.
I used Inkscape software to load up an image of the triforce logo on the blade and traced it with my mouse into vector art. I then loaded up the vector art in the laser cutter and cut it out of 1/8 clear acrylic. I then sanded down the spot on the fat part of the blade a bit so the super glue would have a spot to grab. I also sanded the back of the acrylic carefully so I didn't break it. Then I put a drop or two of super glue on the triforce piece and put it on the blade. I did the same for the other side of the blade.
I hit the blade and triforce with another coat of primer and let that dry. I then went ahead and painted the blade first. I gave it a nice coat of the more metallic silver paint so it would look more like metal.
I let that dry overnight. Then I used painters tape to cover up the blade in the little notch by tearing it into small pieces to fit in all the little spots. I then taped sheets of paper around the blade and middle of the handle so I could paint the wings and the handle end piece blue. After that dried I taped up everything but the handle grip and painted it flat black.
Every time I waited for the paint to dry I practiced wrapping the grip tape around my practice handle. That paid off in the next step.
I used Inkscape software to load up an image of the triforce logo on the blade and traced it with my mouse into vector art. I then loaded up the vector art in the laser cutter and cut it out of 1/8 clear acrylic. I then sanded down the spot on the fat part of the blade a bit so the super glue would have a spot to grab. I also sanded the back of the acrylic carefully so I didn't break it. Then I put a drop or two of super glue on the triforce piece and put it on the blade. I did the same for the other side of the blade.
I hit the blade and triforce with another coat of primer and let that dry. I then went ahead and painted the blade first. I gave it a nice coat of the more metallic silver paint so it would look more like metal.
I let that dry overnight. Then I used painters tape to cover up the blade in the little notch by tearing it into small pieces to fit in all the little spots. I then taped sheets of paper around the blade and middle of the handle so I could paint the wings and the handle end piece blue. After that dried I taped up everything but the handle grip and painted it flat black.
Every time I waited for the paint to dry I practiced wrapping the grip tape around my practice handle. That paid off in the next step.
Step 9: Finishing Touches and Decorations
I figured out where the grip tape would overlap at an "X" shape and marked it with a pencil. I then super glued the first part of the tape near the donut and let that dry. I then put a drop on the first "X" spot and wrapped the tape around to that spot. I then repeated that all the way down and around the bottom of the handle one lap then back up. This time making sure to overlap at each "X" spot and putting another dot of glue on the tape there. I cut off the excess where it met back up with the top and glued it down.
I then did another image trace in Inkscape of the decorative jewel area of the sword and loaded that up in the laser cutter. I cut those out of the same acrylic as the triforce. To make the jewel I just cut out the diamond shape three times, reducing the size of the diamond by 10% each time. I put a tiny drop of super glue between each diamond and stacked it up. I made another set of "decorations" for the other side of the sword.
I found out the hard way that if you just put these tiny pieces on cardboard and try to spray paint them they will go flying! So I had to double over some painters tape to stick them to the cardboard so I could paint them gold. I did the same tape trick with the diamonds and painted them translucent red.
I then traced the decorations onto the wing area where they would go with an exacto knife into the paint. Then I used the knife to scratch up the paint to give the super glue a path down to the wood and glued the pieces on.
Once all these pieces were glued in place I was done! I was then able to pose with this sword at DragonCon without having to peace bond it.
Let me know if you are going to try to make this sword. It would be great to know I inspired someone else to make one. This was the first thing I've ever made from wood and the first prop I've ever attempted. I think it came out pretty good!
I then did another image trace in Inkscape of the decorative jewel area of the sword and loaded that up in the laser cutter. I cut those out of the same acrylic as the triforce. To make the jewel I just cut out the diamond shape three times, reducing the size of the diamond by 10% each time. I put a tiny drop of super glue between each diamond and stacked it up. I made another set of "decorations" for the other side of the sword.
I found out the hard way that if you just put these tiny pieces on cardboard and try to spray paint them they will go flying! So I had to double over some painters tape to stick them to the cardboard so I could paint them gold. I did the same tape trick with the diamonds and painted them translucent red.
I then traced the decorations onto the wing area where they would go with an exacto knife into the paint. Then I used the knife to scratch up the paint to give the super glue a path down to the wood and glued the pieces on.
Once all these pieces were glued in place I was done! I was then able to pose with this sword at DragonCon without having to peace bond it.
Let me know if you are going to try to make this sword. It would be great to know I inspired someone else to make one. This was the first thing I've ever made from wood and the first prop I've ever attempted. I think it came out pretty good!
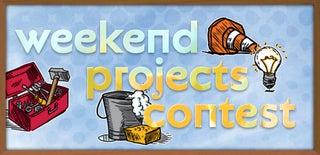
Participated in the
Weekend Projects Contest