Introduction: How to Make an Entire Drone/Multirotor and Camera Gimbal Using Laser Cut Parts
the photo you see was taken from my first ever copter which i built in 2 hours, what i had not mentioned was my first copter used a laser cut frame i designed and produced whilst in school.
This difference between this post and my other about building multirotors is this is mainly to do with designing a custom frame, however i thought rather than post links to the next tutorial, i would include it both for posterity and ease of use to those reading through and learning.
I currently pay to use my college laser cutter, unfortunately i have finished my course so i will not have the regular access i once had, part of the reason for submitting this instructable is in the hope i win the epilog challenge and can open a mini business selling my designs or at the very least open a world of possibility in design for me, not having to tiptoe around my college time table.
i hope you like my video intro
This difference between this post and my other about building multirotors is this is mainly to do with designing a custom frame, however i thought rather than post links to the next tutorial, i would include it both for posterity and ease of use to those reading through and learning.
I currently pay to use my college laser cutter, unfortunately i have finished my course so i will not have the regular access i once had, part of the reason for submitting this instructable is in the hope i win the epilog challenge and can open a mini business selling my designs or at the very least open a world of possibility in design for me, not having to tiptoe around my college time table.
i hope you like my video intro
Step 1: New Designs
So as of 12th of july i made new frames for a new copter, but i decided i would push the limits of 2d designing a 3d model and camw up with some innovative designs,
I was in contact with a company that studies copter and found interesting design features that increased efficiency and stability.
Anging the motos on a 10 degree tilt increases stability significantly, Raising the motors above cg can make the copter more stable and mounting the motors under the frame rather than on top gave a 9% power and efficiency increase in flight due to no turbulence on the frame.
So i had that in mind for one frame, my other frame i wanted to be compact, so i could easily take it places without using up too much space.
So i wanted a folding frame but the conventional frame where the arms all fold down was a big issue, the joints had to be large to withstand the force they would be under and i would need 8 joins that add weight and unreliability,
So i came up with an entirely new frame that as far as i can see has never been made before. :)
I was in contact with a company that studies copter and found interesting design features that increased efficiency and stability.
Anging the motos on a 10 degree tilt increases stability significantly, Raising the motors above cg can make the copter more stable and mounting the motors under the frame rather than on top gave a 9% power and efficiency increase in flight due to no turbulence on the frame.
So i had that in mind for one frame, my other frame i wanted to be compact, so i could easily take it places without using up too much space.
So i wanted a folding frame but the conventional frame where the arms all fold down was a big issue, the joints had to be large to withstand the force they would be under and i would need 8 joins that add weight and unreliability,
So i came up with an entirely new frame that as far as i can see has never been made before. :)
Step 2: Designing the Laser Cut Frame
NEXT STEP, Photos of all the frames.
This step : design
When designing anything, you need a rough idea of how you want it to turn out, I usually have an idea in my mind but for some i recommend sketching and possibly taking measurements to figure out how you want the final model to look.
In this case, i took inspiration from the basic design of quadcopters, a simple x, but i felt that was too bland and so took parts from various frame designs and fashioned it into my frame.
I wanted something unique, that stood out not simply because of the material it was made from, but because of its design
In this case i wanted a dome to house the electronics and i wanted a unique looking set of arms that werent simply to hold the motors apart.
So i came up with this design.
(image 1)
I had made it to be relatively lightweight by removing large amounts of material (the helix design which is lots of squares cut out), but still needed it to be strong so i made a honeycomb design that was the many little squares cut out.
This halved the weight of the model, but it also hugely increase the cutting time, which i has to pay for , the longer the time to cut, the higher the price tag.
Which meant i had to compromise, so for larger parts i cut large pieces out.
so i had a few things that needed to be factored into the design to make it a viable frame.
Airflow (the props had some of their thrust lost when blowing onto the arms, so i had to make them thin or i ha to allow air flow)
Length (the props lose efficiency when close to other props, so i needed the arms to be long but not ridiculous)
weight (the copter loses flight time with weight, so i had to make it as light as possible)
Time Cost (because i pay for time used on the cutter, i had to make the design relatively simple)
Material strength (i could not design outside of the materials strengths, it could not be ultra thin as it could snap, or oscilate causing bad flight performance)
With the above factored in, The design can go ahead.
the trick is to design part by part, rather than design it all in one go, in this case, i designed the sides of the arms before i designed the top/bottom or plates, the arm was designed to be two x the length of the propellor i would use, this ensures the props would not be too close to each other or the board.
I tried to make the design as unified as possible which meant as few joints as possible thus as few weaknesses as possible.
so now i had to make it 3d, which meant in between the two side plates i had to put somthing that spaced them.
I could have printed out lots of side plates and stuck them together, but it would have used huge amounts of material and would have been heavy, instead i used spacer plates that slotter in with finger joints.
There were just slightly wider than the motor mounts and were 3mm thick, one thing to note when designing how they fit together is make sure you know the thickness of the material you are using.
In this case i used 3mm MDF so the finger joints were 10mm long and 3mm wide.
I tried to make the spacers as long as possible to make assembly easier and reduce cutting time .
I also had to make the plate the motor would mount onto.
I used dedicated spacers for this and used two samwidged together for extra strength.
at the time i did not know where the motor mount holes would be, so i cut generic equally spaced holes.
I now had to make the holes in the side plate that the spacers would fit into, so i made a line of boxes 100mm ling, 3mm tll and spaced 5mm apart like the fingers on the spacer plates, i then took the template and placed it on top of the side plate in the position needed..
It was very simple to do and the end result was a clean design.
i did make sure that the holes where the spacer plate slid into, would not compromise other parts of the frame making it weaker.
, i now had he arm designed, but i need to think how i would fit 4 of them together, so i h to make two plates that would clamp to the bottom and top of the arms, to hold them in place securely, this was ver simple, i measured the space i had available on the top arm and make a square that was double the size.
I then put two "fingers" that poked out of the arm that would slot into the top plate.
, i then had to put holes in the top plate that would allow those fingers to slot in, as you can see in the photo i did just that but i forgot the arm was actually in 3d and at the time only put in one set of holes for each arm.
So i had to correct this which was simple. i just copied the holes and spaced them the correct distance apart..
Now that i had a top plate, i decided i would simply cut out two and stick one to the bottom in the same manner.
I now had to design the holes for fitting the flight controller, this was difficult as again i did not have the measurements of controller at the time, so i made a generic design that would supports lots of mounting points.
I also put in lots of holes for any extra wiring that would need to be slotted through.
I now had to think about the dome, it would be too weak on its own, so i made a simple spacer that all the arms slotted into and make it far stronger.
the frame was now finished.
when i later cut it out and tried it, i found i had not completely thought out all the design, it was still a bit too heavy, the motor mount plate was a bit too weak and the dome needed strengthening.
So i took these ideas and proceeded to design many different frames, somewhere for fun and some were for practicality, you will see them all in the photos.
As you can see i have had a lot of fun designing the different frames, i have tried all sorts of designs, some for strength, some for practicality some for looks, some for nostalgia.
I have also included the image where i designed the frame and the image where i space it for the laser cutter bed.
Step 3: Building the Frame
This is a very short step, I will explain about building the frame.
so when you design more complex frames, you may find assemble form lots of parts a ta confusing, this is why i like to lay the parts out in order of how they will be assembled, as 2d representation of the 3d final product effectively.
When it comes to attaching the parts together i would recommend wood glue or hot glue, because they are both not to messy, dry quickly and if needs be can be pulled apart to replace broken parts if necessary.
there is not much to assemble so i will simply show you photos of the final frames i made.
so when you design more complex frames, you may find assemble form lots of parts a ta confusing, this is why i like to lay the parts out in order of how they will be assembled, as 2d representation of the 3d final product effectively.
When it comes to attaching the parts together i would recommend wood glue or hot glue, because they are both not to messy, dry quickly and if needs be can be pulled apart to replace broken parts if necessary.
there is not much to assemble so i will simply show you photos of the final frames i made.
Step 4: Laser Cut Camera Gimbal
A few months on, i am looking to get into photography and aerial filming, but when searching for camera gimbals, i could only find very expensive gambles that can only hold a go pro and even more expensive gambles that can only just hold a dslr, this frustrated me , why should these laser cut gimbels be so expensive when they aren't even very good.
SO i brought it upon myself to desin a strong nd practical gimble that is very inexpencive and that is exactly what i did!
This design take 45 minutes to cut and works out costing £2 in material and £20 in time cost
So here it is
I am very proud of the gimbal, it is very cleanly designed and very strong
Here is it working.
SO i brought it upon myself to desin a strong nd practical gimble that is very inexpencive and that is exactly what i did!
This design take 45 minutes to cut and works out costing £2 in material and £20 in time cost
So here it is
I am very proud of the gimbal, it is very cleanly designed and very strong
Here is it working.
Step 5: The Multirotor
the photo you see was taken from my first ever copter which i built in 2 hours.
Price range can vary drastically, if you use this tutorial to build an quadcopter, your price range will be rouphly $290 without gps and telemetry however if you chose an octocopter you will be looking at upwards of $700
If you choose to buy a much cheaper flight controller board such as the kk2 from hobbyking.com you ill knock $70 off the price but sacrifice gps, telemetry battery voltage etc.
By Jared Reabow
Now before people plinky plonk on their keyboards "This is an Octocopter why is the title not Octocopter!!!!!" Understand you could build a Quadcopter - Hexacopter or quadcopter using this tutorial using identical parts , Even the Octocopter frame can be easily used for the 3 configurations by simply not fitting some arms :)
Also if you wish to use my instructable for profit making, just messege me and i will be more than happy to change the licence after chat :)
So lets get to it !!!!
I have made videos on doing everything but will also type out the relevant info.
But firstly the things you will need to build your own multirotor (note if it says 8x somthing, simply remove however many for the type of copter you are building, so a hex would be 6x)
Note that EVERYTHING you need can be bought from hobbyking.com simply search for the items described below
All required parts are listed below and are to be bought on hobbyking.com
2cm or smaller rubber bands
3mm wire
Hot glue gun and hot glue
Soldering Iron
Allen key set!!!!!
hobbking x930 frame
1 x 7a UBEC
8 x 30Amp esc's any make or brand, just make sure they are 30Amp not 25 with 30burst.
30 bullet connector pairs 2.5mill or higher.
20pais of xt60 battery cnnectors
6 meters of silicone wire- 3 meters red - 3 meters black 26swg which is 3mm thick or more.
solder- preferred leaded.
8 x 12x4.7 props 4 clockwise 4 counter clockwise (order spares!)
8 x 850/750/700 kv outrunner motors bell type
lots of various sized shrink tubing.
sandpaper
(Radio)
Turnigy 9xr
Frysky Jr module with telemetry RX
2 x frsky voltmeters (note i am referring to small meters that are less than $5 each they have a red and black wire coming off each end with a servo plug on one end)
Male to male servo plugs x 18
Male to female extension leads (any length) x 10
stickyback velcro
4x 2200MAH 3s battery or any 2 battery combination that totals at least 8000MAH
(these should be bought from rctimer.com , they are available at hobbking but do not include some of the extras.
APM 2.5 flight controller board
MAvlink for telemetry (not required)
Ublox GPS
YOu may have to source this elsewhere ( buy some 2cm wide clothing elastic at least 2 meters
The videos will be posted in step 2, step 3 and later will be text based.
Price range can vary drastically, if you use this tutorial to build an quadcopter, your price range will be rouphly $290 without gps and telemetry however if you chose an octocopter you will be looking at upwards of $700
If you choose to buy a much cheaper flight controller board such as the kk2 from hobbyking.com you ill knock $70 off the price but sacrifice gps, telemetry battery voltage etc.
By Jared Reabow
Now before people plinky plonk on their keyboards "This is an Octocopter why is the title not Octocopter!!!!!" Understand you could build a Quadcopter - Hexacopter or quadcopter using this tutorial using identical parts , Even the Octocopter frame can be easily used for the 3 configurations by simply not fitting some arms :)
Also if you wish to use my instructable for profit making, just messege me and i will be more than happy to change the licence after chat :)
So lets get to it !!!!
I have made videos on doing everything but will also type out the relevant info.
But firstly the things you will need to build your own multirotor (note if it says 8x somthing, simply remove however many for the type of copter you are building, so a hex would be 6x)
Note that EVERYTHING you need can be bought from hobbyking.com simply search for the items described below
All required parts are listed below and are to be bought on hobbyking.com
2cm or smaller rubber bands
3mm wire
Hot glue gun and hot glue
Soldering Iron
Allen key set!!!!!
hobbking x930 frame
1 x 7a UBEC
8 x 30Amp esc's any make or brand, just make sure they are 30Amp not 25 with 30burst.
30 bullet connector pairs 2.5mill or higher.
20pais of xt60 battery cnnectors
6 meters of silicone wire- 3 meters red - 3 meters black 26swg which is 3mm thick or more.
solder- preferred leaded.
8 x 12x4.7 props 4 clockwise 4 counter clockwise (order spares!)
8 x 850/750/700 kv outrunner motors bell type
lots of various sized shrink tubing.
sandpaper
(Radio)
Turnigy 9xr
Frysky Jr module with telemetry RX
2 x frsky voltmeters (note i am referring to small meters that are less than $5 each they have a red and black wire coming off each end with a servo plug on one end)
Male to male servo plugs x 18
Male to female extension leads (any length) x 10
stickyback velcro
4x 2200MAH 3s battery or any 2 battery combination that totals at least 8000MAH
(these should be bought from rctimer.com , they are available at hobbking but do not include some of the extras.
APM 2.5 flight controller board
MAvlink for telemetry (not required)
Ublox GPS
YOu may have to source this elsewhere ( buy some 2cm wide clothing elastic at least 2 meters
The videos will be posted in step 2, step 3 and later will be text based.
Step 6: Videos
Please follow each video successively and do so before you buy and build the copter to make sure you are up to the task,
By Jared Reabow
By Jared Reabow
Step 7: Parts
By Jared Reabow
So once you have bought everything, the very first thing you should do is wait for it to arrive :)
once it has arrived check you have everything as building then finding you forgot something will be annoying.
Once the above is done, take out the frame and assemble it!.
You assemble the frame first because all the electronics are attached according to the frame.
As i said in the video DO not use the included motor mounts, they cause far to much vibration, rather mount the motors directly to the aluminum arms using the two screws provided which offer more than enough strength.
The frame arms have two holes in either end, when you get the two center plates, the plate with a star design cut into it is the top plate and the thicker plate is the bottom plate.
Firstly you will notice on each corner on both plates there are two slots, they are for the slot in landing gear, you must take the sandpaper and sand those holes to be much wider and longer, use one of the legs to test the holes and make sure you sand enough.
Now you have done this sanding, you should proceed to build the frame, start by screwing he top and bottom plates onto a single arm and tightening, This holds everything in place, continue screwing in the other arms making sure the two red arms are attached on the broad side of the rectangular shaped plates. (see first image)
Now that the arms are secured you have a choice, assemble the landing gear and put to the side to fit later, or assemble and fit.
You may wish to leave the gear off as it mkes setting up and securing the electronics far easier.
Your choice :)
Next step.
So once you have bought everything, the very first thing you should do is wait for it to arrive :)
once it has arrived check you have everything as building then finding you forgot something will be annoying.
Once the above is done, take out the frame and assemble it!.
You assemble the frame first because all the electronics are attached according to the frame.
As i said in the video DO not use the included motor mounts, they cause far to much vibration, rather mount the motors directly to the aluminum arms using the two screws provided which offer more than enough strength.
The frame arms have two holes in either end, when you get the two center plates, the plate with a star design cut into it is the top plate and the thicker plate is the bottom plate.
Firstly you will notice on each corner on both plates there are two slots, they are for the slot in landing gear, you must take the sandpaper and sand those holes to be much wider and longer, use one of the legs to test the holes and make sure you sand enough.
Now you have done this sanding, you should proceed to build the frame, start by screwing he top and bottom plates onto a single arm and tightening, This holds everything in place, continue screwing in the other arms making sure the two red arms are attached on the broad side of the rectangular shaped plates. (see first image)
Now that the arms are secured you have a choice, assemble the landing gear and put to the side to fit later, or assemble and fit.
You may wish to leave the gear off as it mkes setting up and securing the electronics far easier.
Your choice :)
Next step.
Step 8:
By Jared Reabow
Take to now that the frame is built, you will want to set up and secure the APM to the frame.
Start by heating your hot glue gun and soldering iron.
Take the 4 nylon screws included and secure the large female to male scew to each corner of the frame with its bolts.
Look at the main image to give an idea of what i described,
You should not solder on the pins to the board, take reference from my video on how to solder.
You shouls solder the 90degree bent pins to the front of the board and back of the board, you do not need to slder any other pins, so keep the extras safe.
Once the nylon screws are secured, you should work on the mounts to hold the elastic.
You should create 4 mounts using the wire and make sure they are taller than the nylon screws so that when attached to the flight controller, it is suspended above the plate..
place the flight controller on the center of the board with the white arrow pointing to the red arms.
now space the wire mounts about 2cm away from each corner and hook the rubber band into the leg, Hot glue them in place with the legs facing inwards. and stretch the bands over each nylon leg of the board.
It should either be suspended just above the frame or lightly touching.
IF it is to close to the board you can either raise the stands or try to slide the rubber band to the bottom of the nylon screws.
Another option would be buy some clothing elastic , roll small parts up and glue below each leg.
Now that the board is positioned and secured, it is time to install the gps and Mavlink
As i stated in the video, the APM comes with two cables, one for the gps and one for the MAVink
Simply remove the white plug to servo plug from the gps and mavlink and keep safe.
now fit the plugs to the mavlink and gps, The small white plugs go the the modules and the larger plugs to the board.
make sure the red wire goes to vdd on the module (at this point i recommend you watch my setup apm video)
Take the elastic or alternative if you could not get any (2cm wide strips of paper)
and roll them up to a thickness of about 2cm then secure with tape.
With your hot glue gun , Glue the gps pad into one of the furthest corners of the board.
Now that it is glued in place, take some tape and stick it to the bottom of the gps so that when it is glue in place, it does not damage the components should you want to remove it.
once the tape is in place, put some hot glue on the top of the pad, let it coll for about 10 seconds then push the gps onto the pad and hold in place for about 5 seconds.
Now the gps is secured you can plug it into the board, the plug is on the front rite and it facing directly up.
It is up to you where you secure the MAVlink, but try to position it in a corner.
Now that the system is secured, it is time to fit the receiver.
You can place it where you like, but i recommend taking some wire and constructing a small frame to sit over the APM, look at image 2.
Once you have the frame build, hot glue it in place, making sue it does not touch the APM.
On this frame you will place the receiver and tape the bar to it so should you need to remove it later you do not have messy hot glue.
you must now get the male to male servo plugs, you are likely to have bought either the one pin plug of the 3 pin plugs with a red white and black wire.
look atthe side of the reciever, you will see 3 symbols, a negative a positive and an Ohm ( Ω )
Plug one end of a servo plug into each of the ohm pins, if you have the 3 wire version then simply plug one into each 3 pins making sure the white wire goes to the ohm pin.
See the 3rd image for help.
If you have single plug servo leads then connect 8 to the ohm pins , one to the positive and one to the negative.
With the rx now wired you need to connect the wires to the flight controller
with the board flat, the top pins are the signal pins , if you look on the bottom the pins should be labeled 1 to 8 and and the same for the receiver, simply plug them in in order and remember to plug the two power leads in correctly, the center pins are positive and the bottom pins are negative.
Your receiver should now be wired in.
You should refer to the video on setting up the apm with missio nplanner, please also download and install the following
Make sure you download and install the following on your computer
http://ardupilot.com/downloads/http://ardupilot.com/downloads/
this is the driver for the telemetry pick the rite version for your computer
http://www.ftdichip.com/Drivers/D2XX.htm
Take to now that the frame is built, you will want to set up and secure the APM to the frame.
Start by heating your hot glue gun and soldering iron.
Take the 4 nylon screws included and secure the large female to male scew to each corner of the frame with its bolts.
Look at the main image to give an idea of what i described,
You should not solder on the pins to the board, take reference from my video on how to solder.
You shouls solder the 90degree bent pins to the front of the board and back of the board, you do not need to slder any other pins, so keep the extras safe.
Once the nylon screws are secured, you should work on the mounts to hold the elastic.
You should create 4 mounts using the wire and make sure they are taller than the nylon screws so that when attached to the flight controller, it is suspended above the plate..
place the flight controller on the center of the board with the white arrow pointing to the red arms.
now space the wire mounts about 2cm away from each corner and hook the rubber band into the leg, Hot glue them in place with the legs facing inwards. and stretch the bands over each nylon leg of the board.
It should either be suspended just above the frame or lightly touching.
IF it is to close to the board you can either raise the stands or try to slide the rubber band to the bottom of the nylon screws.
Another option would be buy some clothing elastic , roll small parts up and glue below each leg.
Now that the board is positioned and secured, it is time to install the gps and Mavlink
As i stated in the video, the APM comes with two cables, one for the gps and one for the MAVink
Simply remove the white plug to servo plug from the gps and mavlink and keep safe.
now fit the plugs to the mavlink and gps, The small white plugs go the the modules and the larger plugs to the board.
make sure the red wire goes to vdd on the module (at this point i recommend you watch my setup apm video)
Take the elastic or alternative if you could not get any (2cm wide strips of paper)
and roll them up to a thickness of about 2cm then secure with tape.
With your hot glue gun , Glue the gps pad into one of the furthest corners of the board.
Now that it is glued in place, take some tape and stick it to the bottom of the gps so that when it is glue in place, it does not damage the components should you want to remove it.
once the tape is in place, put some hot glue on the top of the pad, let it coll for about 10 seconds then push the gps onto the pad and hold in place for about 5 seconds.
Now the gps is secured you can plug it into the board, the plug is on the front rite and it facing directly up.
It is up to you where you secure the MAVlink, but try to position it in a corner.
Now that the system is secured, it is time to fit the receiver.
You can place it where you like, but i recommend taking some wire and constructing a small frame to sit over the APM, look at image 2.
Once you have the frame build, hot glue it in place, making sue it does not touch the APM.
On this frame you will place the receiver and tape the bar to it so should you need to remove it later you do not have messy hot glue.
you must now get the male to male servo plugs, you are likely to have bought either the one pin plug of the 3 pin plugs with a red white and black wire.
look atthe side of the reciever, you will see 3 symbols, a negative a positive and an Ohm ( Ω )
Plug one end of a servo plug into each of the ohm pins, if you have the 3 wire version then simply plug one into each 3 pins making sure the white wire goes to the ohm pin.
See the 3rd image for help.
If you have single plug servo leads then connect 8 to the ohm pins , one to the positive and one to the negative.
With the rx now wired you need to connect the wires to the flight controller
with the board flat, the top pins are the signal pins , if you look on the bottom the pins should be labeled 1 to 8 and and the same for the receiver, simply plug them in in order and remember to plug the two power leads in correctly, the center pins are positive and the bottom pins are negative.
Your receiver should now be wired in.
You should refer to the video on setting up the apm with missio nplanner, please also download and install the following
Make sure you download and install the following on your computer
http://ardupilot.com/downloads/http://ardupilot.com/downloads/
this is the driver for the telemetry pick the rite version for your computer
http://www.ftdichip.com/Drivers/D2XX.htm
Step 9: Setup
By Jared Reabow
You need to first mount the motors to the frame, mount them to the aluminium arms, and remove the motor mount extentions if you had them installed.
Once the motors are all mounted you will need to plug in the ESC's (speed controller) to the board so you know how much work room you have, i recommend routing the servo plugs in between each arm and up through the center hole to the input pins.
ALWAYS REMEMBER TO SLIDE ON SOME SHRINK TUBING FOR EACH IRE TO COVER THE SOLDER JOINTS.
see the first image for where to plug each esc.
now that the escs are wires secure them in place n the rm with tape as hot glue will melt.
make sure there is slack in the servo wire.
With them now mounted, it is time to solder the esc's to the motors, you will need to cut length of silicone wire for each motor, i chose red wire for the front 4 and black for the back 4, but remember to solder one esc first so you can test its rotation by plugging it directly into the receiver and throttling up. and make sure it rotates the correct direction, if it does not, switch two of the 3 wires.
Take note of this as each motor will alternate between crossed wires and non crossed.
Each arm is likely to take about 20 minutes,
now that they are soldered you can start wiring in the power system, this is up to you on how you wire it in but i recommend tht you route the two power wires to the bottom of the frame , solder male bullet connectors on the red wires, female on the black wires.
Now get two xt60 female connectors and solder on the silicon wire about 2cm long (split the end of the wire in half to share between the two connectors, once this is done divide the other end of the wire up equally between the 8 opposite gender bullet connectors and solder them in place, then slide over some shrink tubing.
remember on the xt60, the negative pin is the top one with the triangular slot and the positive in the flat bottom one.
You will power 4 esc's on each side using these adapters you made.
Your power system is now built as on hobbking almost all batteries come with xt60 connectors.
You will need at this point to attach the landing gear if you have not.
Once attached you will take the Velcro and create battery straps, there are parralel slots in the legs to slide in velcrow which you will glue in plce with the hot glue.
you should also place some Velcro on the battery and on the legs to help secure them in place.
now you can strap in the batteries. however at this point, do not connect them.
You need to follow my video guide on setting up thefrsky radio if you have not set it up yet.
If you have not done so already, you must watch my video on setting up the apm for mission planner as it is very important.
once this is done you can plug in the batteries and test everything is working as it should.
Next step.
You need to first mount the motors to the frame, mount them to the aluminium arms, and remove the motor mount extentions if you had them installed.
Once the motors are all mounted you will need to plug in the ESC's (speed controller) to the board so you know how much work room you have, i recommend routing the servo plugs in between each arm and up through the center hole to the input pins.
ALWAYS REMEMBER TO SLIDE ON SOME SHRINK TUBING FOR EACH IRE TO COVER THE SOLDER JOINTS.
see the first image for where to plug each esc.
now that the escs are wires secure them in place n the rm with tape as hot glue will melt.
make sure there is slack in the servo wire.
With them now mounted, it is time to solder the esc's to the motors, you will need to cut length of silicone wire for each motor, i chose red wire for the front 4 and black for the back 4, but remember to solder one esc first so you can test its rotation by plugging it directly into the receiver and throttling up. and make sure it rotates the correct direction, if it does not, switch two of the 3 wires.
Take note of this as each motor will alternate between crossed wires and non crossed.
Each arm is likely to take about 20 minutes,
now that they are soldered you can start wiring in the power system, this is up to you on how you wire it in but i recommend tht you route the two power wires to the bottom of the frame , solder male bullet connectors on the red wires, female on the black wires.
Now get two xt60 female connectors and solder on the silicon wire about 2cm long (split the end of the wire in half to share between the two connectors, once this is done divide the other end of the wire up equally between the 8 opposite gender bullet connectors and solder them in place, then slide over some shrink tubing.
remember on the xt60, the negative pin is the top one with the triangular slot and the positive in the flat bottom one.
You will power 4 esc's on each side using these adapters you made.
Your power system is now built as on hobbking almost all batteries come with xt60 connectors.
You will need at this point to attach the landing gear if you have not.
Once attached you will take the Velcro and create battery straps, there are parralel slots in the legs to slide in velcrow which you will glue in plce with the hot glue.
you should also place some Velcro on the battery and on the legs to help secure them in place.
now you can strap in the batteries. however at this point, do not connect them.
You need to follow my video guide on setting up thefrsky radio if you have not set it up yet.
If you have not done so already, you must watch my video on setting up the apm for mission planner as it is very important.
once this is done you can plug in the batteries and test everything is working as it should.
Next step.
Step 10:
By Jared Reabow
standard parameters, them Now that everything is wired as it should be and set up from you following my tutorial video you can test the copter.
You must before you do anything make sure that pids are set correctly by doing the following:
Plug in the flight controller board to your computer and connect it to missionplanner.
once connected go to the configuration tab by clicking on it, then on the rite it will say standards params, click on that and wait.
on the left again a tab named arducopter config will appear, click on it and wait.
A to the rite a bbunch of value will appear, look for the one that says rate roll
next to the letter p will be numbers, edit them to say 0.0800
then for the I edit it to ay 0.0700
at the bottom you will see a button that says rite parameters, click this and you are done.
Now you can connect the battery power making sure no propellers are attached.
put throttle to minimum and slide the yaw to the rite, you should see the blue nd red led start blinking quickly, the red led will then turn on solidly.
You now are arms, slowly lift the throttle until the motors move. (if you cannot get it to arm then email me at Jared_reabow@hotmail.com)
now that they are spinning move the aileron stick to the left, all the rite motors should speed up.
Move the elevator stick forwards and the rear motors should speed up.
now when you yaw to the left, all the motors pinning clockwise should speed up.
If this works correctly you are nearly ready to fly, if it does not, it means you have not wired up something correctly, go back and check.
now you need to check the stabilization is working correctly, throttle up the motors again (arm it first) and tilt it forwards, the front motor should speed up, tilt it left and the left motors should speed up, yaw it rite and the clockwise motors should speed up.
If this works then you are READY TO FLY!!!!
First things first, start on grass nd do not hover above 2 meters until you are confident which could take 20 flights.
also make sure it hovers steadily, if it does not you will have to take it back to your computer, connect it, either with the mavlink or usb and go to the config tab, then arducopter level, then click the calibrate accelerometers.
Now it should fly level, you cn test it, if it does ok you ccan move to setting up the PIDS.
Whe outside and powered disarm the copter if it is armed, then hold the yaw to the rite as if to arm but keep holding until a yellow light next to the blue light turns on.
Then take it up and hover it as still as possible, it should calibrate itself.
And thats it,
thanks for using my guide.
standard parameters, them Now that everything is wired as it should be and set up from you following my tutorial video you can test the copter.
You must before you do anything make sure that pids are set correctly by doing the following:
Plug in the flight controller board to your computer and connect it to missionplanner.
once connected go to the configuration tab by clicking on it, then on the rite it will say standards params, click on that and wait.
on the left again a tab named arducopter config will appear, click on it and wait.
A to the rite a bbunch of value will appear, look for the one that says rate roll
next to the letter p will be numbers, edit them to say 0.0800
then for the I edit it to ay 0.0700
at the bottom you will see a button that says rite parameters, click this and you are done.
Now you can connect the battery power making sure no propellers are attached.
put throttle to minimum and slide the yaw to the rite, you should see the blue nd red led start blinking quickly, the red led will then turn on solidly.
You now are arms, slowly lift the throttle until the motors move. (if you cannot get it to arm then email me at Jared_reabow@hotmail.com)
now that they are spinning move the aileron stick to the left, all the rite motors should speed up.
Move the elevator stick forwards and the rear motors should speed up.
now when you yaw to the left, all the motors pinning clockwise should speed up.
If this works correctly you are nearly ready to fly, if it does not, it means you have not wired up something correctly, go back and check.
now you need to check the stabilization is working correctly, throttle up the motors again (arm it first) and tilt it forwards, the front motor should speed up, tilt it left and the left motors should speed up, yaw it rite and the clockwise motors should speed up.
If this works then you are READY TO FLY!!!!
First things first, start on grass nd do not hover above 2 meters until you are confident which could take 20 flights.
also make sure it hovers steadily, if it does not you will have to take it back to your computer, connect it, either with the mavlink or usb and go to the config tab, then arducopter level, then click the calibrate accelerometers.
Now it should fly level, you cn test it, if it does ok you ccan move to setting up the PIDS.
Whe outside and powered disarm the copter if it is armed, then hold the yaw to the rite as if to arm but keep holding until a yellow light next to the blue light turns on.
Then take it up and hover it as still as possible, it should calibrate itself.
And thats it,
thanks for using my guide.
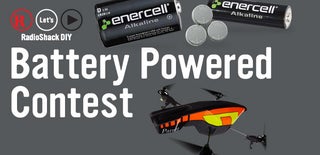
Finalist in the
Battery Powered Contest
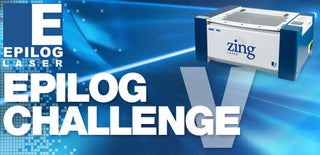
Runner Up in the
Epilog Challenge V
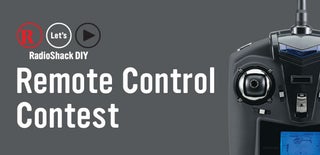
Finalist in the
Remote Control Contest