Introduction: Impossible Spiral Pen Blanks
The traditional way to make a spiral pen blank is to glue strips of multiple colors of wood together, cut them perpendicularly into thin slices, and glue them back them back together again while rotating each slice at a constant angle relative to the previous slice. This technique is well known to pen makers and an example of the process can be found here.
The downside to this technique is that each slice has to rotate relative to the others, so they have to always be perpendicular to the length of the pen. With my new laser-cut technique however, it is possible to create an angled spiral.
This Instructable is intended to explain the process for creating impossible spiral blanks and is not an explanation of pen turning in general. I assume that you already know how to turn a pen and have the requisite tools and supplies for pen turning.
Supplies
- 1/8" or 3mm thick hardwoods of contrasting colors. Ocooch and Cherokee are two good suppliers.
- Pen kits of your choice. Single tube pens work better with the spiral and my favorite is the Jr. Zen.
- 1/8" or 3mm dowels
- Thin super glue
- Gap filling super glue
- Super glue accelerator (not absolutely necessary, but it can be helpful)
- 5 minute epoxy
- Epoxy colorant (not absolutely necessary, but highly recommended)
- Dental wax sheets
- Other common pen-turning supplies such as sandpaper and your preferred finish.
- A sacrificial sheet of HDPE
- Disposable plastic gloves if you don't like super glue on your fingers
- Blue shop towels or paper towels
- Wood spatulas or toothpicks
- Q-tips
- Fine steel wool
- Sanding Sealer (not absolutely necessary, but helps prevent color bleed between dark and light colored woods)
- Multiple grits of sandpaper and micromesh pads
Tools:
Step 1: From an Idea to a Design Via Fusion 360
Since it isn't possible to rotate angled slices, I decided to keep all of the rectangular slices aligned and have the wooden pieces within the slices rotate instead. The elliptical holes within the slices allow them to slide onto a dowel at an angle which results in the finished blank being approximately square despite being made from rectangular slices. This solution gives the angled spiral solution that I was looking for and as a bonus, makes it much easier to maintain the proper rotational angle for each slice simply by aligning the long edges of the slices against a flat surface before gluing. This gives a square-ish blank with exact rotational angles whereas the conventional spiral technique yields a cumbersome spiky blank with rotational angles as exact as you are able to do by hand. Assembling the blanks from individual laser cut pieces also allows much more creative freedom in the patterns of spiral possible.
Step 2: Spiral Design Animations
In order of appearance, the embedded videos are:
Four-Color Standard Spiral
Two-Color Standard Spiral
3/4 Spiral
3/4 Thin Spiral
Four-Color Return Standard Spiral
3/4 Return Spiral
3/4 Thin Return Spiral
Step 3: Select Your Files and Cut Your Pieces
- Choose which pen kit you want to make and look up the diameter of the bushings. If you like to turn pens with a straight profile from bushing to bushing, the diameter of the pen will be about the same as that of the bushings. If you like to turn a convex profile, try to estimate what the diameter of the pen at its thickest point will be. The files come in four sizes that refer to the thickest diameter of the finished pen, so if your pen is going to be thinner than 10.5 mm and thicker than 7 mm, use the 7-10.5 mm file. If your pen will be between 10.5 and 12.5 mm thick, use the 7-12.5 mm file. If you want to turn a very thick pen, use the 7-14.5 mm file or the 7-16.5 mm file. Always use the smallest possible size so as not to waste wood. The width of a blank created by the 7-10.5 mm file is actually 21 mm, so it is possible to make a thicker pen with it. The reason I don't recommend this is that the male and female parts of the puzzle pieces are meant to be removed as waste material once the blank is glued together. If you make a pen with a larger diameter than what the file is designed for, the male and female puzzle parts will not be entirely removed during the turning process and will be visible in the finished pen. See photos 1-3 for an example of what this flaw looks like, and photo 4 for the desired pattern.
- In addition to multiple sizes, the files come in two styles. The standard spiral is formed from four equally sized puzzle pieces and there is also a 3/4 version that uses two unequal pieces, the larger of which is three times the size of the smaller. I recommend starting with the standard spiral and it is the one that I will explain in depth in the following sections. See photos 5 and 6 for examples of the two types of spiral.
- Decide how many slices to include in your blank. This will depend on the thickness of wood that you are using, (nominally 1/8" or 3mm), the length of your pen kit's tube, and personal preference. It would look ugly to cut into the spiral to square it with the end of the tube, so instead you will make the entire spiral shorter than the length of the tube and fill the rest of the space with two additional pieces of wood which I will refer to as end caps from now on. See photo 7 for a diagram. I have found that 18 slices works well for the 80 mm long tube of a Jr. Zen. A full rotation takes 12 slices, so 18 slices allows for 1.5 rotations while still leaving room for end caps.
- The standard spiral uses 6 unique shapes that come in 3 pairs. The 3/4 spiral uses the 6 shapes of the standard spiral and an additional 6 unique pieces that are 3 times the size of the standard spiral pieces that they pair with. In each style, the pairs are marked with either a square, circle, or a triangle. Pieces within a pair are distinguished by the presence or absence of a line over the square, circle, or triangle. See photo 8 for a diagram. The standard spiral uses 6 slices for each 0.5 rotation and each slice uses 4 pieces, so each 0.5 rotation uses 24 pieces. There are 6 unique pieces, so for each 0.5 rotation in your pen, you will have to cut 1 of each of the 6 unique pieces from each of 4 different sheets of contrasting wood for a four-color spiral. See photo 9. Or use 2 of each unique piece from each of two contrasting boards for a two-color spiral. See photo 10. As an example, for a Jr. Zen I could make a four-color 1.5 rotation spiral with purpleheart, hickory, walnut, and yellowheart by cutting 3 of each of the 6 unique pieces from each of the 4 boards for a total of 72 pieces. For a two color 1.5 rotation spiral with maple and cedar, I could cut 6 of each of the 6 unique pieces from each of the 2 boards for the same total of 72 pieces. The 3/4 uses 1 of each of the 6 standard spiral unique pieces and 1 of each of the 6 3/4 spiral unique pieces for each full rotation. This math is complicated! You can calculate the number of pieces needed, or you can do what I actually do, which is cut as many sets of the 6 unique pieces out of a given sheet of wood as I can and then save the extras for additional pens. Write down how many sets of the 6 pieces you decide to cut, but don't actually do it yet.
- Before cutting, select the boards that you will use. It is extremely important that the boards have the exact same thickness. Measure them with calipers and select boards that are all within 0.1-0.2 mm in thickness of each other. If you can't find boards that are that close in size, you can use boards that differ by up to 1 mm in thickness, but it will require time consuming additional sanding and gluing steps.
- Hopefully you have the kerf on your laser dialed in. Test it by cutting a pair of interlocking pieces from one of your boards, such as the pieces marked square and underlined square. The black lines in the file should be cut and the red lines should be vector engraved. The files come in SVG, Ai, and DXF formats. When importing DXF files, ensure that the units are set to mm. After cutting, try to fit the two pieces together. If they fit too loosely, increase your kerf compensation. If they fit too tightly, decrease it. Ideally the pieces will be easy to press together, but will be tight enough that the whole slice stays together if you pick it up by just one of its constituent pieces.
- Once you have your kerf dialed in, cut out all of the pieces that you calculated you would need in step 4, or just cut many sets of each of the 6 unique pieces from many sheets of wood so that you can mix and match for several pen blanks. I highly recommend using nesting software to automatically align the pieces in an efficient way. Once cut, I like to keep my pieces in plastic bags with labels for the species of wood and the size of the pieces, (7-10.5 mm, 7-12.5 mm, etc). See photo 11.
Attachments
7-10.5 mm Standard Spiral 6 Shapes.ai
7-10.5 mm Standard Spiral 6 Shapes.dxf
7-10.5 mm Standard Spiral 6 Shapes.svg
7-10.5 mm 3-quarter Spiral 6 Shapes.ai
7-10.5 mm 3-quarter Spiral 6 Shapes.dxf
7-10.5 mm 3-quarter Spiral 6 Shapes.svg
7-12.5 mm Standard Spiral 6 Shapes.ai
7-12.5 mm Standard Spiral 6 Shapes.dxf
7-12.5 mm Standard Spiral 6 Shapes.svg
7-12.5 mm 3-quarter Spiral 6 Shapes.ai
7-12.5 mm 3-quarter Spiral 6 Shapes.dxf
7-12.5 mm 3-quarter Spiral 6 Shapes.svg
7-14.5 mm Standard Spiral 6 Shapes.ai
7-14.5 mm Standard Spiral 6 Shapes.dxf
7-14.5 mm Standard Spiral 6 Shapes.svg
7-14.5 mm 3-quarter Spiral 6 Shapes.ai
7-14.5 mm 3-quarter Spiral 6 Shapes.dxf
7-14.5 mm 3-quarter Spiral 6 Shapes.svg
7-16.5 mm Standard Spiral 6 Shapes.ai
7-16.5 mm Standard Spiral 6 Shapes.dxf
7-16.5 mm Standard Spiral 6 Shapes.svg
7-16.5 mm 3-quarter Spiral 6 Shapes.ai
7-16.5 mm 3-quarter Spiral 6 Shapes.dxf
7-16.5 mm 3-quarter Spiral 6 Shapes.svg
Step 4: Assemble Your Slices (4-Color Standard Spiral)
These instructions will be for a four-color standard spiral, but the process for other designs is very similar. The pattern for the pieces is easy to remember if you enjoyed the TV show Squid Game. The order is square, triangle, and then circle. Each shape matches with its underlined counterpart, such as squares with underlined squares.
- Set out the four colors of wood that you are going to use in the order that you want them to appear in the spiral. Starting clockwise from the top left I am using purpleheart, hickory, walnut, and yellowheart. See photo 1.
- Find a square marked piece from your top left color, in my case it was purpleheart. See photo 2.
- Find an underlined square marked piece from your second pile, in my case hickory, and press it onto the square marked piece from the previous step. See photos 3-4. If the pieces are difficult to press together, try pressing them in place with a flat piece of scrap acrylic or plywood.
- Find a square marked piece from the third pile and press it onto the underlined square marked piece from the previous step. See photo 5.
- Find an underlined square marked piece from the fourth and final pile and press it between the two square marked pieces as shown in photo 6.
- Find a triangle marked piece from the first pile and set it to the right of the completed first slice. See photo 7.
- Repeat steps 3-5 for the triangle marked pieces rather than squares so that you have a finished triangle marked slice. See photo 8.
- Repeat steps 2-5 for the circle-marked pieces. See photo 9.
- For the fourth slice, start with an underlined square marked piece from the first pile in the top right position. Continue the pattern clockwise for the rest of the slice. See photo 10.
- For the fifth slice, start with an underlined triangle marked piece from the first pile in the top right position. Continue the pattern for the rest of the slice. See photo 11.
- For the sixth slice, start with an underlined circle marked piece from the first pile. Continue the pattern for the rest of the slice. See photo 12. The first half rotation is now complete.
- Each piece of the second half rotation is identical to the first, with the exception that after each slice is finished, it needs to be rotated 180 degrees. See photo 13. The first slice is a 180 degree rotation of the seventh slice.
- Follow the pattern to complete the rest of the second half rotation. See photo 14.
- Complete as many rows as necessary. All odd rows are identical. All even rows are identical. See photo 15. I am doing 1.5 rotations, so I only need 3 rows of slices.
Step 5: Sanding and Gluing Slices
If you used sheets of wood with nearly identical thicknesses within .2 mm and your slices are tight enough to hold themselves together, skip this entire section. If your pieces have identical thicknesses, but are too loose to hold together, only do the first step, gluing.
- Move your slices to the HDPE sheet without messing up their order or orientation. HDPE is resistant to super glue, but if you use too much super glue it will still stick. Put a small drop of thin super glue at each of the 4 seams in each slice.
- Pick up each slice one at a time and sand it on a piece of 150 grit sandpaper until each piece within the slice is the same thickness. The slice should be completely flat on both sides. Be careful not to accidentally sand one end of the slice thinner than the other. You don't want the slice to become a wedge shape.
Step 6: Thread Slices on a Dowel
- Watch the instructional animation embedded above at least once before continuing.
- Take out a 1/8in/3mm dowel. See photo 1.
- Look at the numbered slices in photo 2. Slide the slices one at a time onto the dowel as shown in the photo. Be careful not to mess up the pattern. Every slice should be put on in the exact same orientation as the others.
- Continue adding pieces until they are all on the dowel. See photo 3. The diagonal pattern should be clearly visible. If it looks like you made a mistake, you may have to take the slices back off and try again in order to be sure of the order and orientation.
- The holes in the slices are ellipses in order to allow them to stack at an angle. Without messing up the orientation of the slices, angle them on the dowel. Take the tube for your kit and place it next to your angled threaded dowel. See photo 4. Make sure that the tube is longer than the stack of slices so that there will be room for the end caps to be added in the next section.
- Place the threaded dowel over a sheet of HDPE and make sure that it is properly aligned and angled by pressing the flat sides of the blank against the HDPE sheet. Lift the blank off the sheet without disturbing the slice and saturate it with thin super glue. Try to keep the slices tight against each other while gluing. See photo 5. This is a great time to use plastic gloves. Make sure the blank is completely saturated by pouring thin super glue on all four sides and down the center along the dowel. When the blank is finally saturated, wipe the excess glue off with a blue shop towel and allow the glue inside the blank to cure for at least 15 minutes.
Step 7: Add End Caps
- Use your flush cutting saw to trim the dowel from the ends of your blank. See photos 1-2.
- Sand both ends of the blank smooth, but be careful to sand the entire surface evenly to avoid making the last slice thinner on one side. I like to do this by hand sanding flat against my belt sander while it is off. See photos 3-5.
- Measure or look up the length of the tube for your kit and measure the length of the angled slices portion of the blank. Make sure you measure the angled slices in the manner shown in photos 7-8. If you measure incorrectly the end caps will be the wrong size. Study the diagram in photo 8. The profile of each end cap will be a trapezoid with the shorter side length equal to ((tube length + 4 mm) - angled slice length)/2. The 4 mm is padding so that there is 2 mm of excess wood left on each end of the blank to square off later.
- Now you have the length of the short side of your end cap. In order to make the cuts, you need to measure the angle of the angled slices. Alternatively you can just set the jig using the angled slices directly as shown in photo 9. This makes much more intuitive sense to me and makes it less likely that I will get confused.
- Find a pen blank sized piece of wood to use for your end caps and check that the end is square. If it isn't, square it. Then draw/mark a line x mm from the end of the piece where x is the length that you calculated in step 3 and in the diagram in photo 8.
- See photo 11. With the jig set at the angle of the angled slices, align the mark on the end cap wood to the edge of the sawblade. Make sure that the other end of the trapezoid will be longer than the marked end. If it isn't, then you probably used the complement of the angle that you actually want. Once everything is set up properly, cut the end cap.
- Set aside the end cap. Now take the angled end of the wood you just cut the end cap from. Mark/draw a line x mm from the shorter end of the piece where x is the length that you calculated in step 3. See photos 12-13.
- Set the jig to 90 degrees and cut the second end cap off of the piece of wood at the line that you marked in the previous step. See photo 14.
- Place the two end caps next to each other and check that they are identical or nearly so. See photo 15. If one is larger than the other, either recut another one or sand the larger one down until they are the same size. Lightly sand the angled sides of the end caps so that they will have a clean glue seam. I like to do this on my belt sander while it is off. See photo 16. I recommend not using end caps full of cracks like mine. I really wanted to use this ebony so I had to spend a lot of time filling in cracks with super glue.
- Lay out the two end caps and the angled slices as shown in photo 17 in order to confirm that the assembled blank is longer than the tube.
- Use gap filling super glue to glue the end caps onto the angled slices, one cap at a time. Spray the cap with accelerant after pressing it into place. See photos 18-20.
Step 8: Tube, Square, and Trim the Blank
- Scuff the brass tube that comes with your kit with sandpaper if it doesn't come already scuffed. See photo 1.
- Drill through the blank with your lathe or drill press. It's critical that the hole is as close to centered and straight through as possible or else the spiral pattern will be disrupted in the finished pen. Drill slowly and back out to clear chips often. See photo 2.
- Use a tube cleaning brush to clean sawdust from the inside of the hole in the blank. See photo 3. Push the tube through the blank and out the other side to make sure that it fits.
- Press each end of the tube into a dental wax sheet to plug the holes and prevent epoxy from getting inside the tube. See photos 4-5.
- Squeeze a few drops of the epoxy onto a disposable surface and then add one drop of black epoxy colorant. Mix thoroughly with a wood spatula or toothpick. See photos 6-8. The colorant will help hide the brass of the tube if there are gaps in your slices.
- Place the blank in front of you and use the wood spatula/toothpick to lightly coat the inside of the blank with epoxy. Do the same for the tube. See photos 9-10.
- Push the tube into the blank while twisting it side to side. This will ensure that the epoxy spreads throughout the entire inside surface of the blank. Excess epoxy will get squeezed out, so use a blue shop towel to wipe it away. Then use Q-tips to clean as much excess epoxy from the ends of the blank as possible. See photo 11. Once the ends of the tube are visible within the blank, make sure that the tube is perfectly centered within the blank. Make adjustments if necessary.
- Allow the epoxy to cure for at least 12 hours before continuing to the next step.
- Remove the dental wax from the blank and use the tube cleaning brush to clean the inside of the tube. See photos 12-13.
- Square the ends of your blank until the tube is flush with the end of the blank. I like to use a disk sander for this, but if you don't have one you can use a barrel trimmer instead. See photos 14-15.
- As I discussed earlier, the slices are much larger than the finished diameter of the pen because of the male and female puzzle parts that need to be removed. The end grain in the angled slices will make turning the blank difficult, so I highly recommend trimming the diameter of the pen as much as possible before turning. I use a custom table saw jig for this, but Penn State Industries also sells a rounding jig that will work. See photos 16-18. The offcuts can be used for other projects such as inlay in the lid of a pen box. You can see the disruption of the spiral pattern in the offcuts that is caused by the male and female parts of the puzzle pieces. After trimming, the blank should be an octagon that is close to the desired final diameter of the pen.
- Inspect the blank for gaps and cracks. Depending on the size of the void, fill them with thin or gap filling super glue and then spray accelerant. See photo 19.
- Your blank is ready to turn!
Step 9: Tips When Turning
- Before I use any tools, I turn the blank on the lathe with 80 grit sandpaper until the blank is fully round. This will help prevent a tool from catching one of the corners and tearing out the end grain.
- Use high RPMs and sharp tools to help prevent tear out. Stop the lathe frequently to check for and repair tear out or cracks.
- Dust from dark woods like ebony can get into the end grain of of lighter colored woods like maple and discolor them. There are several ways to minimize this. Start by using a sanding sealer after turning and before sanding. You can also try sanding the darker woods separately from the rest of the blank as much as possible and by using fine steel wool as your last sanding step. The steel wool removes some of the discoloration.
- I like to finish my pens with EEE cream and 3 coats of Aussie Oil, but these blanks should be compatible with any finishing method.
Step 10: Four-Color Standard Spiral
This Zen Jr was made with ebony end caps and walnut, yellowheart, purpleheart, and hickory in the slices. This is the pen that I took photos of at each step of the process. For the following sections, the process is nearly identical for all steps other than the pattern of the puzzle pieces. For that reason I will include photos of the un-assembled slices and the finished pen, but I will not include detailed instructions.
Step 11: Two-Color Standard Spiral
This Snap Cap Rollerball (Tiny Giant) was made with ebony end caps and maple and cedar slices.
This pattern is assembled in the exact same manner as the four-color standard spiral.
Step 12: Four-Color Return Standard Spiral
This Zen Jr was made with canary wood and bloodwood end caps and purpleheart, padauk, wenge, and afromosia slices.
- For this pattern you need to choose an odd number of slices ahead of time. I wanted 15, so I assembled the first 8 in a single row with the same pattern as the standard spiral--square, triangle, circle, underlined square, etc. The second row simply duplicates the first 7 slices of the top row. See photo 1.
- The order that the slices go onto the dowel is different than the standard spiral, so pay close attention to the numbering in photo 2. Essentially, the pattern proceeds clockwise for the first 8 slices, then goes counter clockwise for the next 7 so that the first and final slices are the same. That is why it is called a return spiral and requires an odd number of slices.
Step 13: 3/4 Spiral
This Zen Jr was made with ebony end caps and purpleheart and yellowheart slices.
Assemble the pieces according to the pattern and numbering in photos 1-2. This spiral requires the 6 unique pieces from each style, standard and 3/4.
Step 14: 3/4 Thin Spiral
This Zen Jr was made with ebony end caps and purpleheart and maple slices.
Assemble the pieces according to the pattern and numbering in photos 1-2. This spiral is similar to the 3/4 spiral with the only difference being that the colors of wood alternate with each slice. This gives an interesting pattern in the final pen in which 2 thin spirals wrap around each other and even appear to go backwards in places.
Step 15: 3/4 Thin Return Spiral
This Zen Jr was made with ebony end caps and purpleheart and maple slices.
This pattern is a straightforward combination of the return and 3/4 spirals. Follow the pattern and numbering of photos 1-2.
Step 16: Go Out and Make Your Own!
Please post a photo in the comments if you make any impossible spiral pens. There are plenty of patterns that I haven't tried out yet, so I would love to see what you come up with!
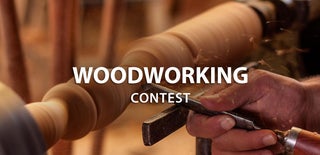
First Prize in the
Woodworking Contest