Introduction: Improving a MakerBot Clone (Wanhao Duplicator 4S)
My first 3D printer was a Prusa I3 that I built from a kit at the beginning of last year. It got a lot of use but ultimately I wanted something that would be able to print ABS easily, would be more rigid and therefore more accurate than the Prusa I3, and maybe even a little quieter. Oh yeah, and was closer to 500 pounds than 1000!
What I ended up with was the Wanhao Duplicator 4S, a MakerBot Clone, similar to the CTC, Flashforge, and a bunch of others. I have been happy with it but with my background having been a RepRap printer I could not help but implement some improvements!
This instructable walks through each of the improvements that I have implemented to date:
- Catches to secure front door closed
- Catch to secure front door open
- Corner stops to secure hood
- Hair spray director for PLA prints
- Directed cooling for nozzles
- Binder clip free build platform (glass or FR-4)
- Enhanced interior lighting
- On demand ventilation for PLA prints
All of these models, save for directed cooling which is not my design, are available on here on Thingiverse.
Step 1: Catches to Secure Front Door Closes
Not exactly opening with rocket science here! Yes, this is a trivial design but with two of these, one on each side, the door of my printer stays snuggly closed. The dimensions of this piece are probably printer specific as it took me a couple of tries to get them just right.
Step 2: Catch to Secure Front Door Open
This design is a little more sophisticated! It is one of the first things that I have done that is a single piece with articulation. There are a couple of one layer tabs that help keep the axle pinned to the build platform on one of the two models in the download file as I found them to be helpful. Some printers may be able to do without them.
Step 3: Corner Stops to Secure Hood
The hood on my printer would occasionally walk around (pushed by the filament feed tubes) so I whipped up this thing. Two of them mounted on opposite corners keeps the hood nicely in place.
Step 4: Hair Spray Director
I did this design when I was thinking that I would also be printing PLA. The box is cut to size from one in which a reel of filament was delivered. It fits reasonably tightly onto the build platform to minimize the amount of hair spray going everywhere.
Step 5: Directed Cooling for Nozzles
I really wish that I had the 3D modeling skills to do a design like this one. It looks great, prints nicely, and works well to boot. Here is the Thingiverse link to this fan duct. I was not able to print this initially as my printer struggled with the layer thicknesses, bridging, and general detail until I had a fan duct installed. So I needed a fan duct to print a fan duct.
The designer of the above fan duct recommended this design as a temporary solution that would enable printing of the final solution. Unfortunately the fans on my printer did not seem to like the temperatures this arrangement inflicted on them and they died before I was able to print the ultimate fan duct. I suspect that my fans were defective as the temperatures were high but well within their supposed operating range.
In any case I turned to 3D Hubs and found a local printer that was able to print the one that is shown above on my printer. I was then able to print the gray one that is serving now as a backup to the one on the printer. I know that not everyone believes that active cooling is needed but I am a fan (pun intended). The improvement in detail rendering and the higher tolerances that active cooling enables makes it an essential improvement.
One caveat. The older mother boards shipped with Wanhao printers did not have support for active cooling built into the board. The printer that I was shipped did. Unfortunately I killed that mother board and the one that I bought as a replacement does NOT have active cooling installed. I have added a manual switch but this is not the road forward. I am not sure what the state of other MakerBot clones is but if you are thinking of buying one make sure it is wired for active cooling.
The above images show a board with, and one without, support for cooling.
Step 6: Binder Clip Free Build Platform (for Glass or FR-4)
There are a number of advantages to using glass as the build plate on a 3D Printer. Not having to worry about retaping and not having to buy expensive wide rolls of tape (or worry about tape lines on your print) are why I choose to use glass, or more recently FR-4, on my build platforms. A major downside of using glass or FR-4, however, is the loss of build space that can result from having the build plate secured with the traditional binder clips. It is never a good thing to hear the noise your printer makes when the nozzle catches on one of those damn clips! This instructable presents a way of securing glass or FR-4 without using a binder clip there-by preserving as much build space as possible...and...avoiding having a nozzle drag across a binder clip!
There is a whole Instructable on this topic so I will say no more here.
Step 7: Enhanced Interior Lighting
Might be a little like a disco but it is brighter in there. What you are looking at is a strip of LEDs stuck just under the top rim of the printer. I may have to go back and re-apply them however as the heat inside the case might be hindering adherence. Not sure if this improvement is a do over.
The next step plus one describes power provision for these lights.
Step 8: On Demand Ventilation for PLA Printing
ABS may love the enclosed printer but PLA does not! This improvement fixes that as it is a printed replacement for one of the windows in my printer with inserts for two 12V fans (60mm 12V Internal Tower Desktop Computer CPU Case Cooling Cooler Silent Fan 6CM). There is a switch on the outside and when not in use the cover can be used to seal them from stray air flow into the case. All this and I have pretty much decided to stick with ABS on this printer! This is nice for a quick cool down of the build area to help de-adhere ABS prints so I am keeping it installed.
The next step discusses power for the fans.
Step 9: Added 12V Power Feed for Extra Cooling and Lighting
The previous two enhancements needed 12V power and the supply from the printer is 24V. There were spare outputs on the power supply so I took one of them and connected it to a variable step down regulator. Out comes 12V that I divided into two circuits, each with a switch, for the lights on one, and the fans on the other.
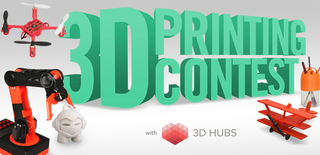
Participated in the
3D Printing Contest