Introduction: Industrial Bookshelf Cabinet
Industrial bookshelf cabinet
For some time we were looking for an industrial bookshelf/cabinet made from metal and wood for our living room. Because we couldn't find a cupboard that we really liked, we started making it ourselves. Because it was going to be a closet of metal and wood, we also had to weld it and I hadn't done that before, luckily my dad could help me with tips and tricks.
Below you'll find an overview of the materials, tools, and steps I took to build this the project, during the project I made some pictures in the different stages of this project.
Supplies
Tools:
- Welding machine
- Angle Grinder
- Miter saw
- Circular saw
- Jigsaw
- Sander/paper
- Welding magnets
- Spirit level
- Tape measure
- Corner iron
- Wood drill
- Metal drill
- Countersink
- Steel brush
- Chisel
Material:
- Rectangular metal tube:
2x 60x40 2mm 2000 mm
2x 60x40 2mm 2350 mm
2x 60x40 2mm 480 mm
- Angle Profile metal:
14x 40x40 2mm 50mm
- Wooden shelves:
4x 32x400mm 460 mm
2x 32x400mm 2300 mm
1x 32x400mm 1300 mm
2x 32x400mm 2630 mm
- Sanding paper 80, 120 and 160 grid
- Corner iron
- Screws 30mm
- Decking screws
- Wood stain
- Wood glue
- Transparent Metal paint
- Anti metal splash spray
Step 1: Step 1 Ask the Old Men and Make a Design/Plan
To get this project off to a good start, I thought it would be wise to ask my father to help. Not only because it's fun to do something like this together but mainly because I haven't welded before and he used to work as a welder and later as a cad-designer.
Of course I could have asked my dad to weld the frame together, but I wanted to learn how to weld and since this is for our own home, this was the perfect moment. So he taught me the basics and then I spent the necessary time laying welds on a piece of waste metal.
After some time I felt comfortable enough to start welding this cabinet, the welds are certainly not perfect yet but I'm still learning. My father was kind enough to make a CAD model of the design I wanted to build. This made the process much more efficient and easier because I knew immediately what I needed, in what dimensions and I had some kind of (construction) plan. A summary of the materials was already mentioned in the previous topic, however, the list we created in the CAD program included also the angle cuts I made so i decided to include it.
Step 2: Step 2 Getting the Materials and Preparing Them.
With the parts list, I bought all the wood for the shelves and the rectangular metal tubes for the frames, luckily the shop where I bought it had a metal saw so they could cut the metal directly into the right lengths and angles I needed.
The ends of the frame are sawn at an angle of 45 degrees and are also welded in this way. Where the upper and lower frame are welded together I have chosen for a right angle connection.
I also needed brackets to attach the shelves too, for this, I cutted 14 brackets from a 3x3 angle profile with an angle grinder. In each bracket, I drilled two holes which I countersank so the screws would be flush with the brackets.
I chose the wood very carefully because I had to glue two pieces together that you want to be so straight and flat, luckily the DIY store had a lot of them in stock.
Step 3: Step 3 Welding and Grinding
Everything was ready now we could really start, first I sanded all the ends of the tubular tubes short so the right angles are easy to weld then we put the bottom frame on a flat surface. When all was well I welded the lower frame together with tag welding on one of the ends where the upright frame will be, I made a piece of wood to size and put it temporarily in between so I was sure it would stay square under the frame. Then we welded the standing frame on the left side and the middle stand on the right side to the bottom frame. When everything turned out to be at right angles, I welded it completely. When it was finished we measured where the brackets for the shelves had to be and welded them in place.
Since we were welding outside in the open air with a MIG/MAG welding machine I used flux-core welding wire, this means you get slag and metal splashes. Although I'm not a professional welder I wanted to keep the welds in sight so I removed the slag with a steel brush and the metal spatter with a chisel luckily I used an anti spray so the amount of metal spatter was not that bad.
at the bottom of the frame, we have grinded away the welds, this part is not in sight after all and it prevents scratches on the floor and makes sure the frame stands stable.
Step 4: Step 4 Woodworking
The frame for the cabinet is now ready so I could start with the woodwork, first I sawed the wood in coarse lengths with the miter saw and then I glued two pieces together into a single plank and of course the side panels that had to be glued.
As you can see on the pictures, the cabinet has four side panels, two of which are around the metal central post, one on top of the post and the other on the left and the right side of the central post. The top panel has been cut to size with a jigsaw, the other sides, and the shelves have been cut to the exact width with a circular saw because my miter saw couldn't cut the required length in one go.
After sawing everything to the length I carefully removed all the glue residue with a chisel and sanded everything with 80 grid, 120 grid and finished with a 160 gird.
After sanding it was time for the first test assembly, I wanted to make sure everything fitted for the pickling and the final assembly, everything fitted perfectly as you can see on the pictures, I used glue clamps and some pieces of wood to hold everything.
Step 5: Step 5 Painting and Staining
After removing all the wood from the frame, I pulled the frame in the garden, cleaned it with ammonia so I could then finish it with a transparent metal lacquer to keep the metal color and to be protected against corrosion. I applied two coats, to make sure that everything would be well protected.
When the lacquering was finished it was time to stain the shelves, for this I had already tried different types of stain on waste wood and my wife and I chose the most beautiful one for this project, the choice fell on a light oak stain applied in two layers. I applied the stain with a cotton plug and polished it well, after letting the first layer dry for 30 minutes I applied the second layer.
Step 6: Step 6 Assembly
As everything was ready now, it was high time for the final assembly, because of the weight and size I did the assembly in the living room where the cabinet will be.
First of all I put the cabinet together just like I did with the test stand and fixed it with glue clamps etc. so I could align everything properly and make everything even. Then I screwed the shelves to the brackets that were welded to the frame. The side panels are wood-on-wood joints that I pre-drilled and then I used Spax deck screws with a Torx head.
These screws contain milling ribs under the head so it is no longer necessary to countersink the head of the screw. In addition, the milling ribs ensure that the wood has room to work. This also reduces the chance of cracks, the most important thing is that the screw heads are so small that the screw holes are also as small as possible. These screw holes can, of course, be eliminated, but I have chosen not to do this.
Step 7: End Result
Both I and my wife are very happy with the end result and even more fun is that we regularly get compliments about the cabinet. Hopefully, you found this a nice project to read and maybe to make yourself.
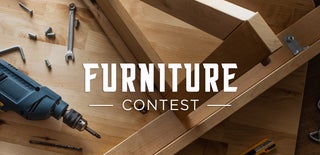
Runner Up in the
Furniture Contest