Introduction: Inexpensive Home Metal Casting
This process will show you how to build a cheap but effective foundry for melting aluminum, bronze, brass, or similar metals. The foundry uses parts that can be easily sourced and runs on ordinary wood. Caution is required when building and operating this foundry, as parts can heat up to 2000 degrees Fahrenheit or greater during melts. Proper safety gear is a must.
Of course, different setups work for different people. This design is inherently modifiable, and you should feel free to swap parts and experiment with whatever suits you best until you find a setup that works for you.
Supplies
55 gallon oil drum
16 gallon oil drum
Plasma cutter, hole saw, or similar hole-making tool
Thick steel tube, at least 2.5" in diameter
Duct fan
Thick steel pipe, 1" in diameter, thick angle steel, or similar steel pieces
Clay-graphite crucible
Wood for fuel
Loose dirt for insulation
Extension cord
Step 1: Prepare Oil Drums
Once you've acquired the supplies, the first step is to alter the oil drums. Carefully clean and rinse both drums with soap and warm water until they're free of oil and contaminants.
Firstly, remove the tops of both drums. Some oil drums have easy-open lids, others require you to cut the top off. If using a plasma cutter, be sure to clean the area thoroughly and remove paint. Cut the drums approximately 1" from the top and file down any sharp edges. Save the lid to the 55-gallon drum; it can be used as a lid during casting.
Once the tops are removed, you then need to cut holes for the blower tube. Find your thick 2.5" steel tube and trace a circular outline approximately 6-8" from the bottom of the large oil drum; cut this circle out.
Cut the same circle out of the small oil drum approximately 2-3" from the bottom. The small drum should sit inside the large drum and have 4-6" of space between the bottoms of the drums when the two holes are aligned.
Now, you'll need to add supports for the crucible. In the picture, you can see inside the foundry and view the way I made my supports. Find your crucible and make a horizontal mark in the small oil drum approximately halfway from the bottom of the drum; depending on your crucible, higher or lower may be necessary. Trial and error will tell you for sure. Find two thick-walled steel pipes, two thick angle steel pieces, or any thick steel that will work to support the crucible and will not block air from rising up the drum. Cut holes in the drum at your horizontal mark (through both sides of the drum) and insert your supports so that they are parallel and level; they should be resting on the walls of the drum. Test these supports with the crucible and some weights to ensure they will be strong enough. Remember, thin steel will burn through at high temperatures, so only thick steel works for these supports.
At this point, the drums are ready for assembly.
Step 2: Assemble the Foundry
Firstly, set the large oil drum where you intend for it to stay permanently; it will be extremely heavy and difficult to move later. Add enough dirt into the drum so that the small oil drum sits concentrically inside with the blower tube holes aligned and level. Insert the crucible supports into the small drum, and lower the small drum into the large one. Once the small drum is in place, slide the blower tube through both holes into the small drum and fill the space between the two drums with dirt, all the way to the top of the small drum.
Do not remove the blower tube from this point onward: if you do, the dirt will pour through the blower tube holes and you'll have to redo this step.
You may need to add a concrete block or similar object to support the blower tube on the outside of the foundry so that it doesn't shift during a melt.
At this point, you can test fit the fan. I used a simple duct fan inside a wooden box, but any fan that moves a large amount of air would work. A hairdryer may be too small, but you can always try it and find out. I have also found that old microwave fans work extremely well; these may require more wiring than duct fans.
Your finished foundry will likely look different from the one in the picture; it doesn't need to be exactly the same. Whatever system you find works is the one you should use.
Step 3: Cast!
Now you have a finished foundry that you've made for very little money. You should feel free to modify your setup and use parts that work for you.
As for fuel, I find that wood scraps get hot enough to melt aluminum with ease. If your temperatures are too low, try finding a beefier fan to move more air. Check the foundry regularly during a melt to make sure the foundry is still operating properly.
Since the small steel drum is so thin and exposed to so much heat, it will likely burn through after a couple pours. You could either replace the drum regularly or find some sheet steel (ideally stainless) to use as an interior liner to protect the small drum.
If you intend to melt bronze, wood may not work for you. I found that inserting a propane line into the blower tube from the outside, then allowing a small amount of propane to flow into the combustion chamber to supercharge the wood allows for higher temperatures than wood alone. Use caution if you choose to add propane; moving the cylinder too close to the foundry may result in an explosion.
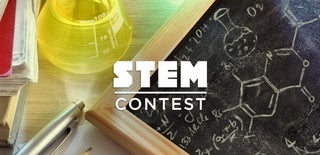
Participated in the
STEM Contest