Introduction: Infill Block Plane
For a long time I was playing with the thought of building a small one hand block plane. As I now have some time over, I decided to finally build it.
All I needed was some scrap wood, a steel plate for the sole, a knurled screw, a thin steel plate for the lever cap and for sure a plane iron.
Material:
- Steel plate 6mm
- Steel plate 3mm
- Threaded pin M4
- Knurled Scrw nut M4
- Brass pin
- Scrap Wood (oak and cherry/plum)
- Plane Iron (32mm width)
5 minutes epoxy or comparable glue
- spray lacquer
I paid around 17€ (~19$) for the plane iron (12€), the steel plate, threaded pin and knurled screw and the brass pin (5€ all together). All the other material I had laying around.
Tools needed:
- wood saw (japanese pull saw)
- miter saw
- belt sander, sandpaper and granite stone
- drill press and metal drillbits
- thin files and rasps
- M4 thread cutter
- square and ruler
- marking gauge (for wood and metal) and caliper gauge
- hand plane
Step 1: Flattening the Steel Plate for the Sole
In the first step flatten the sole plate. I did that with a small hand belt sander and a file. It doesn’t have to be perfectly flat because it will not be sole. It will be the upper side where the wood is glued on. One edge of the steel plate has to be straightened as a reference edge.
I attached the sole with double sided tape to a piece of scrap wood to be able to grab it and hold it onto the belt sander. Check for straightness regularly.
Step 2: Making the Side Pieces
I had a thin piece of oak lying around. It was a cut off from an old project. I resawed the piece into two thinner pieces and flattened them with a plane.
Now draw the shape of the plane onto the outer pieces. Use double sided tape to stick both side pieces together to perfectly match both sides. Remove most of the wood with the saw and shape it with a rasp and sandpaper.
Step 3: Opening the Plane Mouth
Lay the plane iron and the resawed pieces on the sole plate and measure the width of the sole.
Before opening the plane mouth, cut the sole plate to the final width with a metal hand saw.
With a marking gauge, mark the width of the plane iron to the sole plate. The bed angle of the plate is 20°. Scribe a line onto the sole plate where to drill the holes for the mouth opening. Try to drill them with an angle of 20° into the sole plate, as shown in the picture. Fully open the mouth of the plane with a file. Remove as much material as possible with a drill bit to minimize time filing away the material.
To achieve the bed angle, cut a piece of scrap wood with a 20° angle on the miter saw and attach it to the sole plate with double sided tape. This piece of wood should act as a guide for filing the mouth.
Step 4: Making the Infill Pieces
I had a piece of cherry or plum wood – I’m not sure what it really is – laying around in my shop. It had approximately the width, that I needed. Plane the pieces to the thickness you need with a hand plane. Sketch the shape of the front infill piece to the wood and remove the waste material with the saw and shape it with a rasp and sandpaper, as before on the side pieces.
Afterwards set your miter saw to 20° and cut the plane iron bed. As the piece was very small I attached it to a piece of scrap wood with hot glue to allow a safe cut.
Sand every piece to get rid of all saw marks and continuously checked for squareness of the sides and that the bed is completely flat.
Step 5: Glue Up
With all wooden pieces prepared, you can start gluing it up. I used 5 minutes Epoxy and a lot of clamps to keep everything in place while the glue dried. Epoxy can be removed easily if it’s not yet fully dried, but a bit jellylike. Make sure that the wooden bed is in straight projection to the bed you filed into the sole plate.
Step 6: Filing and Sanding
When the plane is fully assembled now, go on to sanding the sides, so that the sole plate is flush with the side pieces and there is no excess material on the front and the back. I started with 60 grid and went up to 120 grid on the belt sander
Step 7: Making a Lever Cap
Draw the outline of the lever cap onto a thin (3-4mm thick) piece of steel plate. Cut it out with a common metal saw or whatever you have laying around. Flatten one of the short edges of the lever cap with a file or sandpaper to make sure, there will be no gap between the plane blade and the lever cap. This is very important. If there is a gap between the plane iron and the lever cap, chips can be caught in this gap and jamming the mouth. I additionally polished the lever cap for optics.
Drill a hole into the lever cap near the back edge of the lever cap and cut a thread in it. This thread has to fit to the knurled screw.
Step 8: Drilling the Hole for the Brass Pin and Gluing It In
As an end support for the lever cap drill a hole into the side pieces of the plane. Make sure, that there is enough space for the lever cap to fit in, but not too much space, that you can’t tighten the lever cap.
Polish the brass pin with sandpaper and polishing paste.
Now glue the brass pin into the drilled hole. I again used 5 Minutes epoxy for that task.
I only had a threaded pin and a knurled screw nut. So I had to glue the threaded pin into the internal thread of the nut. For this I used Loctite.
Step 9: Flattening the Sole
As one of the last steps we get to flattening the sole. I again used a belt sander for rough flattening and metal sand paper on a granite stone for the final finish. Take your time for this, because a plane with a bowed sole isn’t worth a lot. Mark the sole of the plane with a permanent marker and grind afterwards. Like this you can easily see, where there is too much material. Check with a ruler for flatness and with a square for squareness every now and again.
Step 10: Closing the Mouth That Only a Thin Opening Remains
Due to the method with opening the mouth of the plane using drillbits and files, the mouth is quite big. This can cause issues when you want to cut along the grain of the wood, as it tends to break out.
In the picture I illustrated why it is necessary to have a thin mouth opening. The blue dashed line is the actual cutting depth. If the wood breaks out, the plane leaves gaps in the surface below the cutting depth, marked as red area. As shown in the picture, reducing the plane mouth width is reducing the depth of tear-out.
Insert the plane iron and let it stick out a few millimeters as shown in the picture. Then cut a piece of wood to size and insert it into the mouth. Glue it in with 5 minutes epoxy and again flatten the sole, as some of the wood might stick out.
Step 11: Finish It With Spray Lacquer
In the very end, give it two or three coats of shiny transparent spray lacquer. Make sure to not spray too much lacquer to the wood at once as it might run down the vertical sides and cause ugly drops.
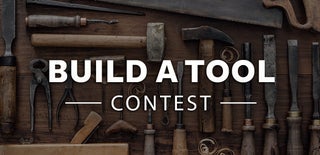
Runner Up in the
Build a Tool Contest