Introduction: Iron Man Stool
This instructable is all about making a stool. When I started making I want all my things to look beautiful. This build was looking me very ordinary so to increase the beauty I decided to build the custom top of this stool. I am a huge fan of Iron man and his spark and I want to introduce this thing into my project. I thought this was definitely a great project to give honour to the creator of that character. Initially I wanted to make his new spark but then I change the plan and go with the old version of iron man. If I made this completely out of wood I would definitely going to include some other superheroes also. Hopefully, you learn something new from this build and use that in your own projects. If you like this build then make sure to leave your feedback. I use two different material for this build but you can definitely make entirely out of wood and made arc reactors, other parts of the iron man suit. May be in future I introduce mark 2 of iron man stool and that will definitely going to be whole new level. The awesome thing about this build is that in the night the whole build alive and boggles your mind. You can carve the piece with the CNC with much accuracy but it didn't mean that you can't do it with hand. If you use templates then there is no doubt that you are capable of doing some magic tricks with the resin and glow in dark pigments.
Step 1: Material Used
Following is the list of material used in this build.
1. 1” X 2” stainless steel pipes
2. 1” X 1” stainless steel pipes
3. 1¹½” X 1½” stainless steel pipe
4. ¾” wide and ¼” thick steel bar
5. Pickling agent
6. Epoxy resin
7. Glow in dark pigment powder
8. End cap
9. Buffing compound
Tools and Safety Used:-
1. Chop saw
2. Angle Grinder
3. Flap disk
4. Scotch Brite wheel
5. Buffing wheel
6. Welding Helmet
7. Leather Glove
8. Apron
9. Safety Goggles.
10. welding Set
11. SS304 Welding Electrode
Step 2: Material Cutting
To cut the material I always go with a chop saw. It always does the job much faster than using regular grinder because of its reach. But I know everyone doesn't have a chop saw for their own so for the desired length you need to make a mark and then made a perimeter around the material so that once you reached the maximum cutting capacity of your blade that reference line helps to stay nice and straight.
Step 3: Deburring
Once the cutting process completed I do the deburring work. There is a small disadvantage of the cutoff wheel is that it always created sharp burrs because it grinds the material and then removes it. On the other hand, if you use carbide wheel it cuts the material by revolution. If you use stick welding then I recommend you not to chamfer the edges because of it thin down the material surface and that leads to blowhole which is extremely difficult to fix. If you are using thick mild steel pipes then it would be good to do the chamfer.
Step 4: Welding
After doing the cleanup now the pieces are ready to be welded. Always make sure to have a flat surface so that the end result will be nice and flat. Then everything is all about tack weld and then make a full weld. The welding starts from that top frame which is made out of 1” X 2”. First I clamped the pieces and tack weld and recheck the squareness of the pieces because when you made a tack due to the sudden heat and its cooling it always changes the squareness, so make sure to check the squareness after every tack. Once the frame made full welds are made. Then I grind down the welds beads because I have to weld the legs and for that, the surface needs to be flat. Then I place the legs to its position, first made a tack weld and then recheck with the speed square. Align it perfectly and then made tack weld to remaining three sides. Repeat the same thing for remaining legs. After that, I tack weld the stretcher pieces and then made a complete weld. Now the basic shape of the stool rises. For welding on stainless steel, I always prefer the stitch welding technique to avoid blowholes.
Step 5: Stool Top.
For the stool top I decided to make something unique and then this idea came in my mind and another thing is that I wanted to make this table look awesome in the night as well. So I decided to use glow in dark pigment powder. I was thinking about using a CNC but then I thought why not to make this with the handheld router because everyone was not equipped with those tools in their garage shop. So I made a print out of the iron man and then stick it onto the wood. The wood I am using already cut down to the required dimensions. So it fits in nice and snug. Then I cut that template and stick it onto the wood and remove the material of that shape. After that, I filled it with resin with some glow in dark pigment powder. The design looks way to simpler so I decided to sprinkle powder randomly onto the resin once it gets some thick consistency so that the Colors will not settle down to the bottom. Once the resin cure I found that I definitely have to do some detailing work so that the figure can be easily understood. Then I sand down the entire surface making it smooth and then stick the template onto it. Then with 10° V bit, I carved the boundary area by taking my time and filled that with different colours of pigment powder. I also marked my stamp onto it. And then pour the resin to cover the entire surface and those powder which are filled in those carved sections. Once the resin cures I straighten the edges with a guide and flush trim router bit so that it can fit inside that stool top.
Step 6: Welding the Backing for the Stool Top
For providing more strength to the top I decided to weld down some strips under that wooden piece and for that, I am taking the reference from the top I made. I fix that inside the stool top frame and make it flush to the surface. There is small bow inside that stool top but clamping did the job done. Then I place the strips and weld it with the main stool. The strips have a hole drilled inside that so that the board can be fixed from the bottom with some screws.
Step 7: Decorative
The bottom of the stools seems to be empty so I cut down some 1” X1” square pipe and made L shape out of them then I welded them to the main frame at each corner. Always make sure to start from a small tack weld to that it anything goes wrong you can easily sort out your problem.
Step 8: Cleanup
Once the basic shape finished the cleaning process can be started. I start from a 30 grit ceramic stone wheel. People usually say that you have no need to use aggressive grit onto stainless steel and I agree with them but if you are careful enough then you can remove the beads to much higher rate just by using the curvature of the wheel and knock off the bigger bumps on the welded surface. Then follow it with 120 grit. Then I switch to Scotch Brite wheel and after that, the buffing work is done. I decided to leave the corner without doing any grinding but to remove the blackening I use pickling agent to remove that oxidation and burn marks around the welds. That solution is a huge time saver. The thing you have to do is apply and then wipe it off with a rag.
Step 9: Admire Your Work
The final thing to do is install the end caps to save your floor from scratch and admire your work and to boost up your moral switch off the lights and let the magic happens and once it's done it will definitely blow your mind.
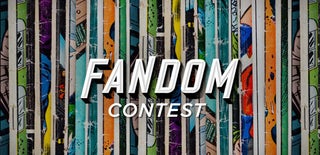
Runner Up in the
Fandom Contest