Introduction: Ironman Welding Helmet Part 1.
I like to teach myself to do things. If you're like me, finding a cool theme for a project to help sharpen a skill is always fun. I've recently started making custom "hero-themed" helmets and other cosplay-like elements that have rather practical functions for everyday life. I make these for myself and for other people. If this Instructable were to be selected for the Epilog Challenge VI, the Tech Contest Sponsored by little bits,or the Hand tools only contest, I absolutely use any prizes won from these contests to get this business idea off the ground and scooting with a bit of swiftness. I'd like to have a few more pieces of equipment for this venture before I make the website live and officially open for business, So again, any or all of the prizes up for grabs between these three contests would be a great help. That's enough of the "pretty-please pick-me" for now :) , perhaps more of that later.
I wanted to get better at welding thin gauge sheet metal, as well as other related metal processes. This Instructable follows some of my progress on a welding helmet I am making. An Ironman welding helmet. A Welded Ironman Welding Helmet. If Tony Stark were poor, A real person, socially awkward, and kinda "meh" with his math skills, we'd be the same person he and I.
Before we get into the meat, bolts, and whatchamacallit's of this project, here's my fun disclaimer:
**Please be advised that at no place within this Instructable, nor any other I intend to publish will there be a step titled: "Hurt yourself, or break something, as a result of being careless or too ambitious". That being said, don't do it. At the very least, try your best to be careful. After all, it's hard to enjoy creating a handmade project, if your hands are missing. :)**
Let us Begin!
Step 1: Materials / Game Plan
The older I get, the more I learn just how wise it is to write things down. They say the world of grown-ups is nothing but paperwork. So I recommend getting in the habit of putting that pen/pencil to the paper and start pushing it around a bit.
Write out what you hope to learn from the project, and then write down your list of materials and take that list to the store and get this show on the road.
Project Objectives:
To gain a better understanding of the working/ structural characteristics of thin gauge sheet metal, as well as the proper techniques of using various hammers, grinders, tools to bend/ shape the metal pieces in the desired orientations.
Perhaps most important, make a super Sweet Steel Ironman helmet, that protects your pretty-face-bits from molten-weld spray.
Materials/ tools I used:
.16-22 gauge WELDABLE Steel.
I got most of what I needed out of a 2 foot square piece. Go to a legit metal shop whenever you can, It's cheaper per square foot and sometimes they have small scraps they don't mind giving away to young metal enthusiasts. Make sure it's not galvanized tho. The zinc coating will wreck you if you breathe in the fumes when the metal heats up. Zinc poisoning? No thanks. I'd rather get flicked in the nose while my hands are full. Don't get it? let someone flick you in the nose. No fun huh? Lesson learned.
Some of the pics you will see in this Instructable were used with Galvanized steel. It was tricky and ended up not being optimal for how strong I want this helmet to be. I'll talk more about why it didn't work later.
Ironman Pepakura templates
You can find them online, as well as multiple high-quality Instructables on this site of how to make a paper-pep helmet.
Permanent markers
for marking the steel.
Step 2: Street Cred
If you haven't made a paper-craft anything before. Go ahead and do that. If it's of the same thing you want to make out of metal, even better. In doing so, you will get a better understanding of what the pieces need to do once cut out of steel, as well as have a full size model of what it's going to look like while it's being constructed. Any tiny bend you have to make in paper, for the most part you are going to have to recreate in the steel, unless you get clever and use the thickness of the material/ filler metal in the similar way foam cosplay builders must modify their templates from the pep files. And of course, having a paper-craft version gives you some street cred/ entry into the world of doing paper-craft. There are some fun people to befriend in that part of the hobby world.
Remember, steel is just heavy, hard, and hot when working with it, so if it's not really what you are hoping to do, this step will help you scope out just how much time you want to put into something like this.
Step 3: Tools
A metal cutting bandsaw will be your best friend. The kind that is vertically mounted, and has a table top to slide the pieces around. I went through multiple other options for this first attempt. and unless you have access to a CNC metal cutting solution, or something fancy like a super awesome Epilog Laser machine (wink Wink), or any of the other fancy prizes, the bandsaw will be best and here's why:
Scroll saw-
Too fragile. Almost impossible to make the sharp turns needed for some of these pieces. Also, the reciprocating action of the blade will bind a lot which leads to broken blades, damaged work pieces, loud noises, and long hours starting over because you keep ruining your parts.
Jigsaw-
Similar problems to the scroll saw, only it's more able to take the corners and curves in the material. Another big drawback to the jigsaw is that it's designed to move through the material, instead of moving the material over a stationary cutting device. Why does this matter? Because you will be making very small parts, and with a handheld jigsaw, you have to look past the tool to follow the line. Plus, as you cut through the thin metal, friction from the blade generates heat that sits in the material which will make your metal softer the longer you cut and can cause your material to distort if you do not plan ahead. I will talk more about this in the Tips and Tricks step.
Bench mounted jigsaw-
Nice try. I bought one of these too thinking it would be a nice blend of scroll saw, and jig saw. Nope. For our purposes, this tool doesn't cut the mustard either. It is a step in the right direction because it's designed to move the material over the blade, but that reciprocating motion doesn't translate as clean into curves in steel as it does in wood/ softer materials.
Metal cutting bandsaw is the way to go. The blade always goes in the same direction, and the nicer ones have a speed control which will help with blade-life as well accuracy of your cut. I do not own a dedicated Metal cutting bandsaw. I have a portable bandsaw, which I fashioned into a vertical metal cutting bandsaw. It works pretty good, but it has some drawbacks. The 1inch thick blade doesn't do sharp curves very well. I have to do a lot of back cuts and cutting around to allow for the horrible turning radius. It's doable, but I can think of a dozen other things I would have rather done with all the extra time spent working around this limitation. The portable bandsaw, also doesn't have a very deep cutting area. A lot of the pieces I hoped to keep one piece, I had to get clever with where to zip them in half. It ultimately led to inaccurate pieces and areas where the templates do not match up so cleanly in the final helmet, and another work around has to be found.
You're also going to need to have an angle grinder with cutoff discs, as well as flap discs of various grit counts. Flap discs are amazing. You will learn to love them. Pancakes are amazing, so too is pizza.
I went to the local Harbor-freight and picked up a set of auto-body repair hammers. These are neat and are excellent for working with the steel used in this project.
A Teardrop hammer will be needed for shaping the pieces, as well as a sandbag/ shot bag. I didn't have a sand bag I was willing to sacrifice to the blunders of hot/ sharp steel, so I made one from a canvas tool pouch found in the electrical department at the big box hardware store. The Blue one... Lowes. Fill it with sand, and BOOM, pretty good shaping bag to go with the teardrop/ auto body hammers.
It would be wise to have some small strong magnets and other hand tools/ squares and what-not that most people wanting to give this a shot will already have on hand.
You are also going to need a welder, and some welding skills. Yep. Indeed.
Step 4: Transfer Templates to Steel Plate
It's pretty simple on this step. Take the pep-pieces and lay them out on the steel. You have to be clever how you lay them out, in order to make the best use of space on the material. Also, keep in mind that putting too many small pieces together will make it harder to cut them out. This goes back to the metal getting hotter the more you cuts you make all at once. It's also easier to manage if you can cut out smaller chunks of pieces from this big plate. It is unlikely you will cut all of this out in one go. Especially if you use a set up like I did with the Porta-band style cutting apparatus. I took this photo in 2011 when I started this project. I've had other things going on, as well as a few 'plot-twists' in life which haven't aided the effort to bring the quickness for this project, but it can really be a buzz kill when you start and see just how long it can take without the right tools. How to remedy this? Persistence. For when skills and fortune fall short of your goals, persistence will get you there. Keep going!
Step 5: Form Your Pieces
Start hitting that hammer on that steel. Crank some AC/DC or Black Sabbath and pretend you're held captive in a cave. I started this project in the winter up in the mountains, so It was easy to smack things with the hammer, because it got the blood flowing and warmed me finger-bits. Depending on how you strike the sheet metal and tool you use, you can curve the steel, as well as contour, and thin the material. Imagine you are pushing your finger through plastic sandwich-wrap. It's doing the same thing..sorta-kinda. When you think you have the piece curved in the right way, mock it up to the paper one you already built. If it is, great!, If not, keep going. All though there is a limit to how many times you can bend the metal back and fourth before it fatigues and breaks,so be careful. No big deal if it breaks tho, this is about learning!
Step 6: Start Tacking Into Place
When you have the pieces shaped the right way, Start burning that Steel! Start with the welder heat and wire speed as slow and cold as possible. I recommend using a MIG welder. it's a lot cleaner than Flux core wire welding. When you find a good speed and heat that doesn't burnout too bad in this small gauge, start spreading out your tacking to get the basic shape of the helmet. I built this helmet primarily as one piece, and only lightly tacked on the parts I plan to go back and hinge/motorize. This will keep the proportions/ symmetry in check, and it helps morale of the project, because by this point you have spent a lot of time hoping to see a steel Ironman face looking back at you. Make it so.
Step 7: Tack in the Smaller Bits...
I broke this build into stages, because I realized fast that the size and shape of the welder and the helmet make it difficult to get inside the dome and poke around. So I dropped the top "vent" in as a separate piece. There are some tricky very small pieces in this build that will easily pool up and melt away as you tack together. SLOW SMALL TACKS is key. Welding a long constant bead isn't optimal in the world of MIG welding thin material. you will learn to see the heat flow in the material as you get deeper into this project. Once you have the basic shape of everything tacked up, just fill in the rest of the seams and get to flap-disc-ing that mambo-jambo.
Step 8: Tips and Tricks
There are pros and cons when welding vertically. Depending on what you are trying to achieve, you will learn fast the importance of modifying your angle of attack.
Bottom to top vertical welding:
In my experience,a universal constant reveals itself: heat rises. If you are welding this thin material, from bottom to top, the heat build up will cause your welds at higher-altitude to be hotter and deeper, risking a blow-through of your material. It can also distort what's going on up above as the heat collects on the upper-most point of your piece.
If you go top to bottom as you weld, you have a more consistent welding parameters with regards to ambient temperature. What does this mean? It means it's easier to go into auto pilot and save time with your welding going top to bottom because the added metal from your previous weld serves as a heat sink to help pull the heat away from your next weld point. The extra metal also helps to dissipate the heat better and fights against distortion due to uneven heating of the steel.
Color of the steel as you weld:
Steel speaks to you as you use heat to manipulate it's properties/ orientations as you fabricate. When mild steel gets heated to the point of melting, it has distinct colors for each of the following phases: cold-ish, real-hot, blacksmith-hits-with-hammer-red, and just-about-to-run-down-your-leg-on-fire-hot. As you weld, the time between these separate stages are very small, but once you learn to identify these stages, you will get closer to being one with the metal ways, young grasshopper.
Cutting on the bandsaw:
Use a cutting oil on the steel occasionally as you cut. It helps cut down on blade-wear, as well as noise, and undue heat generated in this stage of the game. But it also smudges your permanent marker so, try to be neat and tidy as you apply.
Cut the pieces into smaller chunks. It's easier to hold on to a cluster of 3 pieces as you cut them out instead of the entire plate for hours on end.
Keep in mind that as you cut, the metal gets softer due to heat. This, plus the downward constant direction of the blade can pull your pieces into the saw and jam the tool, injure your person, and/or distort your piece. Just as with the welding heat tricks, the heat can be pushed around as you cut too. start at the narrow pointy-bits and cut into the wider parts of your pieces. This will give the piece more support as you finish your cut. It's safer. Cleaner. More gooder-er.
Welding Galvanized steel
I tried this and it is tricky, dangerous, and not the best quality weld. An important life lesson that can be learned from welding is that the strength of any bond lies within the prep-work. To make the galvanized steel weld cleanly, you have to remove the zinc plating from the weld area so it does not compromise the weld. With material as small as this, by the time you have removed the zinc mechanically (with a grinder/ flap disc) there is too much base metal removed and becomes even trickier to weld. All this plus the fact that zinc in the lungs, is just bad-news-bears.
The burned zinc does make an interesting cob web-like flame residue around where it was burned away during welding tho. That's a good way to know if you're welding galvanized material. If you are, stop. Go eat a cheese burger while you are out buying the proper weldable steel.
Some of the face plates in this instructable were made with galvanized steel, it was terrible. The right stuff welds soo much better. so I 86'd the galvanized ones. Being a person born in '86, I'm not sure how I feel about that saying.....
Step 9: Final Thoughts Before Part 2
I decided to play around with flame hardening and oil quenching to see what kind of finishes it would give to the piece. I'm a real fan of function over fashion so, instead of painting something to look like rust, I usually just let it rust. When the rust looks cool, I spray some clear-coat enamel on that bad boy and get back to being awesome.
I took one of the faceplate attempts and heated it up until it was cherry red and then doused it in used motor oil/ radiator fluid in a jug from my Jeep. Let me tell you, that is not the proper way to "blue" a metal-anything. It was kinda cool tho. I knew what was going to happen beforehand, so I prepared the kill zone with as much "outdoors" and "away from people" as I could. Once the red-hot faceplate was doused with the cold junk oil, it instantly burst into flames, and was very smoky. An awesome party trick, but still dangerous, since most people these days live in places where actions like this are frowned upon. Especially in close proximity to vinyl siding, dogs, neighbors, fire departments, and environmental activists. But hey, what doesn't make you deader, makes you better.
In the followup to this instructable, I will go over the remaining need-to-be addressed topics for a welding helmet such as :
Optical filters and mounting of the safety lenses inside the faceplate
Motors and pivot assemblies that can handle the added weight of the metal pieces
Airflow/ quality inside the helmet for comfort, and safety reasons
How / what to use to trigger the mechanics in the helmet
Inner frame/ support for comfort as well as safety for the wearer
Bluetooth audio-bits for awesome tunes while working and fancy pants integration of technology
There is also a chance I will completely redo the order of operations of this build. If it ends up being faster and more accurate way to go, I will add another Instructable to compensate.
Thanks for reading, I hope this inspires you guys-gals to go out and make something you want, as cool as you want, instead of just settling for lame alternatives of what 's already available in retail stores. Now I have to get cranking on my 3d printing, little bits, laser engraver, and other related handtools knowledge, in the event you wonderful-face-awesome-people-types vote for this instructable to win some of that awesome gear.
Oh, and check out my new digs. The site isn't too fancy yet tho, so you won't see much when you click this way. Perhaps soon. I spend too much time in the shop making stuff and not enough time on the computer clicking stuff. www.pepsteel.com
And yes, a fully functional (to some extent), all metal suit is in the works....
Step 10: Additional Resources/ Updates Until Part 2
Since, work is picking up a bit in my grown up life, It might take just a tad longer until part 2 than I realized. So, I've added a step to help make this 'ible better and to better assist those of you out there on the interwebs to try this yourself without having to thumb through the internet looking for the best pep files to cut from steel.
9/17/2014
After much searching online and reading I came across the model work of Sharkhead7854. It had the best detail and proportions of all the ones I came across. also, the unfold work by Dubean 33 within the pep file, helped keep the tiny intricate cuts to a minimum. Well done you two. Thanks for making this file available to the interwebs.
Attachments
Step 11: Another Updated Before the Big One Starts Rolling Out.
Hey guys
I'm sure you all thought I was yet another "fall-away before the follow-up" type of internet people. Honestly for a while there, I almost was. To spare you on all the whimpy-details I will say this: if ever in life your friends, fortune, or skills cause you to fall short of your goals, persistence will get you there. Just keep going. When everything is on fire, move forward, never backwards. As we all get older we realize just how life can put a bit of a twist in your path to where you want to go. When they lack the courage to go with you, be brave enough to go alone.
Now, as you can see from the video, I have the laser machine and can get back to slapping these monsters together and sending them out to the world. There is also a whole HUGE load of new tech and gadgets to trickle out the pipeline too. Thanks again for your kind words, and your patience, Now it's time to get CRACKING!!!
-Barringer.
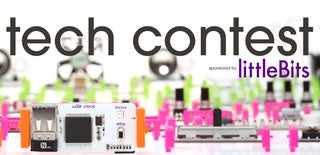
Participated in the
Tech Contest
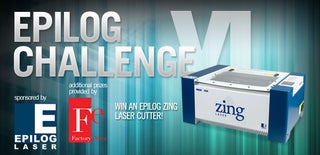
Participated in the
Epilog Challenge VI