Introduction: Japanese Woodblock Printing
This project started out as a open-ended school assignment where I was invited to make or do anything relating to Modern World History. I landed on Japanese woodblock printing because I thought it was an interesting blend of art and woodworking. This goes to say that I am no expert in this field, but I did do a lot of research and learn a great deal from my experimentation.
I documented my whole process in a video, so if that is your preferred method of viewing information, then click the link above!
If not, please read on...
Step 1: Design and Transfer
I started out by creating the design for the final print.
I drew up a butterfly design that was similar to one I had seen online, and I scanned it into Photoshop to add some Japanese characters. I basically searched for cliche words that had aesthetically pleasing characters and dropped them in. If I got them right they should say “love” “joy” and “happiness.”
Since the woodblock is essentially a stamp, the pattern has to be transferred and carved backwards, so I flipped the entire design horizontally in Photoshop before printing it. I had set the dimensions of the Photoshop canvas to the dimensions of the block of wood that I had, so I was able to simply print the pattern to it’s actual size.
I secured a 4x8x1 inch block of cherry from a friend’s scrap pile and set to work transferring the design. To do this I covered the back of my printed pattern completely in black chalk, taped it to my block, and traced over all of the outlines of the pattern with a ballpoint pen. By tracing all the lines firmly, a chalk pattern was left on the actual wood when the paper was removed.
I then went over the entire design with a fine Sharpie on the actually wood. After a couple hand cramps, I finally had a woodblock prepared for carving.
Step 2: CARVING
Carving was a very experimental and time-consuming process. I first experimented with a set of smaller chisels on a shaky table using only the force of my hands. After plenty of struggling there, I eventually took the project outside, clamped it down, sharpened some larger chisels, and started using a small hammer for the extra force. This process was much smarter and helped move the carving along much quicker.
Carving quickly revealed itself to be very time-consuming and hard on the hands. I made a lot of mistakes at first. I chipped off parts of the design by accident and even sliced the tip of my finger a bit. Turns out both these issues were easily solvable with Superglue.
Since only raised areas will transfer ink when paper is laid over the blank, you essentially need to carve away everything but the design. The general technique is to make angled cuts outlining the pattern, use gouges or sometimes large chisels to clear out the excess areas, and then use flat chisels to come up to the outline. My video demonstrates these techniques in more detail.
The carving process probably took 8 or 9 hours, but time flies when you’re having fun. The trickiest bit was carving the curved designs on the butterfly. I couldn’t afford to cut straight down along the outlines since the small pieces needed all the support they could get, so I ended up using a small sharp chisel to cut in at an angle and then meet it from the other side. This worked very well and the shallow V-cuts were enough to keep ink off the paper.
I used a wire brush to clean up small areas as I went, and in the end I used a gouge to make uniform cuts into all the waste areas. This made the whole block look more professional and clean. I also left some waste areas raised, since they were far enough away from the design that they wouldn't accidentally get inked.
I should mention that cherry is the ideal wood to use for carving. Cherry is pretty hard and has a very tight grain, this makes small, intricate designs such as this one possible. If you do not have access to any cherry, try to find a wood with similar qualities.
Also, my block was an inch thick. This turned out to be completely unnecessary, and you could get away with anything down to half an inch thick.
Now, on to the paper...
Step 3: Prepping the Paper
Japanese printers are very particular about their paper, and I even found recipes online for making my own perfect printing paper. However, contrary to the traditional path, I simply used a variety of craft papers that I thought looked absorbent, including some water-color paper. I cut these materials into pieces the size of my block.
The paper has to be moist in order to soak in the ink, so after cutting, I laid each sheet in between damp newspaper in a plastic shoebox and added some pressure. The correct dampness of the paper was tricky to figure out, and you will have to play with your set-up to see what level of dampness works best to get a good print.
Step 4: Printing... Finally
There are two main parts to the actual printing process: inking the block, and rubbing the paper onto the block. Both of these operations required tools that I did not have, so I improvised.
To ink the blank I used a small foam brush to dab ink across the surface. A roller would have done this quickly and evenly. With my method it was hard to get a coat of ink across the whole design before some of it would get soaked into the wood, creating an uneven final print.
Once the ink was on, I quickly laid a damp sheet of paper on top of the design and rubbed it in thoroughly using a selection of materials including leather, card stock, a wooden spoon, and my hands. Real printers use a tool called a barren to get good, even coverage and pressure. With my method I had to do a lot of experimentation and many trials to get a good print.
After many prints I also figured out the right level of dampness to aim for with the paper.
In the end, some of the prints stuck to the block, some absorbed too little, some absorbed too much, and some shifted during the process. But, after many trials I finally had about four prints that I was proud of.
Each of these spent a little time wrapped in newspaper underneath an SAT book to try to flatten them as they dried. Even so, none of them ended up being completely flat. I would imagine that better flattening techniques and proper printing paper would have solved this problem.
Step 5: Final Thoughts
This project was very difficult and experimental, but it was pretty cool. I had a lot of slip-ups and issues during the process, but I think with better tools and more time those all would have gone away.
At first I felt a little weird writing about my "experience" with an art-form that has been studied and perfected for centuries. But I just had to recognize that this project was merely a fun exploration into a traditional medium. At the very least this project got me several nice prints, lots of carving practice, and a 100% on my history assignment.
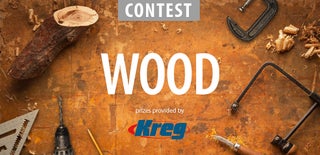
Participated in the
Wood Contest 2016