Introduction: Joule Thief Torch With Casing
In this project you will learn about how to build a Joule Thief circuit and the appropriate casing for the circuit. This is a relatively easy circuit for beginners and intermediates.
A Joule thief follows a very simple concept, which is also similar to its name. It extracts or "steals" joules (energy) out of low-voltage systems. E.g. Most non-functional batteries actually have about 20%-30% of juice still in them. However their voltage is too low, and it is not able to power anything. The Joule thief circuit can actually harvest this low-voltage energy from batteries (or any source) and power a standard 5mm LED light quite brightly. The output is not limited to a LED.
This is a very easy, practical, and useful circuit to have in your house. If you can't find a working battery that you need urgently, or you want to make complete use of the batteries you buy, this would be perfect for you.
Finally, this Instructables will also showcase a 3D printed casing for the Joule thief. However, if you do not have a 3D printer then you can check out my Laser cut acrylic box or design a casing yourself. Even just a plastic box would be satisfactory. I would not recommend leaving the circuit without a casing.
Step 1: Supplies and Tools
Supplies:
1. Perf board
2. AA battery holder (can be for 2 batteries or 1)
3. Ferrite toroid (with two coils over it)
4. Tactile latch switch
5. 5mm LED (any colour)
6. 5mm LED bezel + nut
7. NPN transistor (I used C1815)
8. 3mm Nuts x4
9. 3mm Bolts x2
10. Wires
Tools:
1. Soldering wire and iron
2. Wire-cutter pliers
3. Multimeter (if you don't have one you can make one DIY. Check out my Arduino powered multimeter)
4. Desoldering pump (optional)
5. Needle-nose pliers
6. Pencil/pen/marker
7. Superglue
Step 2: Circuit Schematic and How It Works
Here is a very that very nicely explains how a joule thief works:
CREDIT TO ELECTRONICGURU FOR IMAGES
Step 3: Securing Battery Holder to Board
1. Using a black marker, I marked where the holes in the battery holder were on the PCB.
2. I used the wire cutter pliers to make the holes in the perf board. Soon enough it was big enough for the 3mm bolt. If you have a handheld or electric drill this process is a lot easier. It is important to test if the holes are big enough for your bolt.
3. I added an extra set of nuts between the perf board and battery holder to stop the bolt from protruding out of the other end so much.
4. The two remaining screws were used to secure battery holder onto the perf board.
Step 4: Understanding C1815 Transistor
Some transistors have different schematics and pinouts. Therefore, just as clarification, I wanted to state which pins of the transistor are base/collector/emitter
Moving from left to right with the flat side facing you, the pins are base, collector, and emitter in that order. This is exactly as what is shown in the diagram.
Step 5: Preparing Ferrite Toroid
I got the ferrite toroid from a broken RC car circuit
1. Taking thin enamelled copper wire I wound the coil around the ring-shaped ferritetoroid 7 times. See picture
2. The wire was cut after 7 coils with length to spare for soldering and connections. The second coil started in the same place where the first coil was started. Following the shape of the first coil, the second coil also was pulled out after 7 winds and cut with excess.
3. To differentiate between the coils coil 1 had much longer legs than coil 2.
4. Since my ferrite toroid was very small, I used a very thin copper coil wire. Most likely 26 SWG. If your toroid is bigger then you can use bigger and even normal wires
5. After this, you would have 4 different wire ends. 2 for coil 1 and 2 for coil 2. These 4 can also be written as 2 for the starting side and 2 for the end side.
6. To simplify remembering the coils, I gave the following names to the coil ends. S1, S2, E1, E2. The S and E stand for start side and end side. 1 and 2 stand for the coil number.
7. S2 and E1 are winded together to make a total of 3 legs. Remaining are S1, E2, and winded leg.
Step 6: Preparing LED
1. LED Bezel attached. LED slides into the white plug. White plug fits into the metal bezel.
2. Soldering leads onto LED legs. Make sure to know whichleg is the anode and cathode.
Step 7: Soldering Tactile Switch and Connections
1. Battery positive wire connected to latch switch
2. Winded part of ferrite toroid coil connected to otherterminal of the same latch switch.
3. E2 (end side-coil 2) is connected to a 1K resistor (Brown-Black-Red).
4. S1 (start side - coil 1) is connected to transistor's collector pin.
Step 8: Soldering Transistor and Connections
1. 1K Ohm resistor connected to transistor's base pin.
2. S1 connected to transistor's collector pin.
Step 9: Soldering on the LED
1. LED's anode connects to transistor's collector.
2. LED's cathode connects to transistor's emitter.
Step 10: Housing 3D Model
1. I used Fusion360 to design the housing for the circuit.
2. A .step and .gcode file have both been attached below. If you want to alter the housing download the .step file and use a 3D modelling software to edit it.
3. If you want to go straight into 3D printing the model, you can download the .gcode file and upload it to your printer. The print time is approximately 14 hours. Rough dimensions of the model are 150mm x 80mm x 100mm.
4. I used Ultimaker Cura as the slicer and Ender 3 as the 3D printer.
Details about the housing:
1. The design is trying to replicate the shape of a keyboard mouse. Easy fit for your hand. Ergonomical
2. There is a back panel secured using rubber bands. The rubber bands fit into the grooves holding both pieces tightly, while still making it easy to remove and access the circuitry inside.
3. There are 2holes for the LED bezel as well as the latch switch.
Step 11: 3D Printing
1. I used Ultimaker Cura as the slicer and Ender 3 as the 3D printer.
2. File was uploaded to the 3D printer. The temperature presets were 200 degrees C for the nozzle and 50 degrees C for the bed.
3. The print took about 13.5 hours. Using pliers I removed the model off the platform and picked off the supports.
4. The hole for the latch switch was a bit small, so I sanded it using a thin file.
Step 12: Attaching Button and LED Bezel to Model
1. The latch switch and LED+bezel had to be desoldered and removed from the perf board so that they can be secured to the housing.
2. The latch switch was soldered to a small piece of perf board and leads were attached to the relevant pins. This makes it easier to secure the switch in the hole.
3. The LED bezel was put through the round hole at the front of the model. A nut was added to the other side and tightened using pliers.
Step 13: Finishing Circuit Again
1. The latch switch's leads were soldered in back into the main circuit.
2. Superglue was put between the model's inner surface and the small piece of perf board to hold the switch in place.
3. The LED's leads were also soldered back into the circuit.
Step 14: Attaching Back Panel
1. I made small rubber bands using a couple of larger ones.
2. The back panel was placed onto the model's base, and the rubbers bands were wrapped into the grooves.
Step 15: Final Images and Testing
Step 16: Video
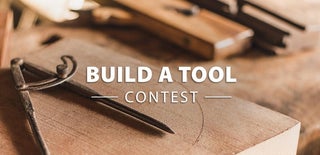
Participated in the
Build a Tool Contest