Introduction: Jumo Inspired Wood Desk Lamp
This desk lamp is inspired from the Jumo "Bolide" folding lamp originally made in bakelite. It was designed in the 40's.
A re-edition of this lamp can be seen on the New Jumo site. My version is inspired from this design but is not intended to be a replica. I made it from lime tree (tilia wood) for the base and shade with a "Shou Sugi Ban (Yakisugi)" (Japanese burned wood technique) for a nice deep black finish.
The arms are made from steel and some walnut wood.
Step 1: Tools and Materials
Materials:
- lime tree wood (I used a block of 12x12x30cm for the head and one block of 8x8x60cm for the base). I used lime tree wood because it has a very nice aspect when charred, it is fairly easy to work with and ...cheap.
- walnut wood (very little, just for the lower arm)
- steel 4mm thick I found at the scrap dealer
- 20cm of 30x20mm rectangle steel tube for the arm attachment to the base and shade
- 5mmx40mm screws and locknut
- bulb socket: I used a G9 type of socket, available in Europe as it can handle various type of small low consumption LED bulb
- Led bulb (I use led to have a low wattage and make sure the lamp is not going to heat the wood shade)
- wall socket, switch and wire
- epoxy glue
- common wood glue (PVA)
- linseed oil
Tools:
- angle grinder with cutting grinding and sanding disks
- router with straight and round bit
- planner (I have one so I used it but you can probably manage to use a router)
- lathe and gouge
- band saw
- circular saw
- chisel
- gas torch or weed burner
Step 2: Drawings
I made some hand drawings that I used to cut the various pieces.
They are full scale drawing and I used them to cut templates of the various parts (either to draw the pieces on the raw material or verify the shape when I was turning or carving.
Step 3: Arms - Steel Part
Making those arms (a pair for the lower arm and a pair for the upper arm) is quite simple although time consuming:
- draw the shape on the steel bar
- cut with an angle grinder
- grind to the final shape (I hold both of them in a bench vise while grinding to have the exact same shape)
- drill 5mm holes for the articulation
- sand (2 passes, 2 different grit)
- polish and buff
I added a picture with tools I used to go from raw steel bar up to the finished arm.
Step 4: Arms - Walnut Add On
Once cut and sanded to the desired size, I turned some little pins to hold the wood in place on the arm.
The pins are cut off once glued with the walnut.
Step 5: Arms - Base Attachement and Socket Holder
The base and shade attachment are cut form the 30x20mm rectangle steel tube (see drawings).
For the socket holder, 4 holes are made, 2 for the wires, 2 for the holding screws.
The socket holder is a turned piece of wood to hold the wire connection in a safe place.
Step 6: Arms Assembly - Leather Washer
We are still missing a few parts for the folding arms: a small walnut spacer to hide the screw and keep the arms away (see picture). Mine is 12 mm wide, but it will depend on your arm thickness.
Two more small pieces of walnut are drilled and are used as guide for the cable. They are cut to the width of the arm and inserted between the arm. No glue, pressure is enough to hold them in place.
Once we have all parts, the assembly is pretty straightforward.
For each articulation the screw and locknut will apply enough pressure to hold everything in place...but we want the arms to fold.
The magic piece here is a leather washer. With a leather washer between all steel parts of the articulations, we have a smooth folding.
The leather washer can be replaced by an equivalent plumbing washer but the result is not as smooth.
I made washers from the leather of my dead Birkenstock...drill, cut and finish on the lathe.
Step 7: Shade
The head of the lamp is made from a block of wood that I opened first, carve (in order to have the interior ready) glue back as a block and turn it to final shape.
the overall process I followed is:
- cut in two parts (the head is bigger than half of the bock. I kept 8cm out of a 12 cm block)
- draw the desired shape
- clamp and use a router to have a clean cut against the inside line. I did it free hand with small steps, going deeper and deeper
- carve the remaining/inaccessible wood with chisels
- use a paper template to verify how deep you have to go
- sand
- I also roughly carved the opposite block in order to keep the block balanced as much as possible to avoid trouble on the lathe due to an unbalanced piece.
- before gluing, measure the start and end of your head to know exactly how close you can go when removing wood.
- the two blocks are glued back together and I used a sheet of paper between the two: it will be strong enough to turn but it will allow an easy separation once the egg is turned.
- turn to shape (use paper template to verify)
- open the egg....
Step 8: Base
I did not have a block big enough to cut the base so it is done in two blocks.
the overall process is (you can follow the pictures too):
- draw the head contour, the inner contour and the lower end contour on the base
- cut the inner part with a band saw
- shape with a router
- cut (as top and bottom are not parallel)
- glue
- a little pass on the planner
- cut outside with band saw
- carve and sand to final shape
- drill a hole on the lower back end of the base for the power cord
- et voila!
Step 9: Yakisugi - Shou Sugi Ban Finish
This nice deep dark finish is performed in three steps:
- burn the surface
- Yakisugi finish is not unique and will depend on how much you burn. I should try before applying to you final project...
- For lime tree I observed that when the wood start to burn by itself it is burn far enough. The wood should be uniformly black.
- brush with a brass brush
- the wood is now brushed (no sanding), follow the wood grain.
- The wood will loose its black color (at least it is the case for lime tree) and turn dark brown. Do not worry, the next step will bring back the nice black.
- apply linseed oil
- and let is dry for a couple of hours.
- surprisingly, once dried, the surface will be stable and will not leave any char on your hands when you touch it.
Step 10: Final Assembly
Arms to base and head attachment
The arms connectors are screwed in the base and the shade. In order to have a perfect fit when the lamp is folded I used a router to have a flat surface (the shade is rounded inside and it would be challenging to attach the arm connector). The top connector is screwed to a small wood insert and this piece of wood is glued with epoxy (which does not requires pressure) on the head of the lamp when in folded position. Please see the quick drawing I did for a better explanation. This way we have a perfect position when closed and the head can still be disassembled from the arm (using the screws).
Power cord and on/off switch
A power cord with on/off switch is inserted trough the hole on the back of the base and connected to the arm cable. This connection will be bellow the lower end of the arm, I used Wago lever type of connectors which are easy to use and offer good protection.
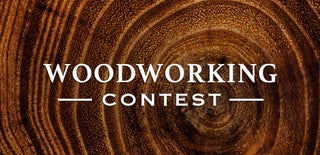
Second Prize in the
Woodworking Contest