Introduction: KAUDA Robotic Arm
- KAUDA is a printable and DIY robotic arm developed with the aim of creating a robot that could cover the functions you want at a low cost, without losing quality and efficiency.
- Developed by a maker for makers, for those who want to work on it, apply changes, study new functions and therefore have fun with it.
- KAUDA is intended primarily for students, teachers, schools and universities, in order to be able to work with simple and intuitive robots, easy to make, assemble and program.
- In a short time you can have a simple, intuitive and fun product on your desk, teaching post or work station.
Attachments
Supplies
OFFICIAL WEBSITE:https://www.diy-tech.it/
MY BLOG: twitter.com/GiovanniLerda
ON THE SITE YOU WILL FIND A NEW VERSION OF THE ROBOT AND NEW OPTIONALS !
Contacts & social:
Step 1: List of Materials
3D Printed Parts:
- Base [QTTY. 1]
- Base door [QTTY. 2]
- Internal GW [QTTY. 1]
- Base ring [QTTY. 1]
- Axis 1 [QTTY. 1]
- Axis 2 [QTTY. 1]
- GW Axis 2 [QTTY. 2]
- GW Base [QTTY. 1]
- GW Axis 1 [QTTY. 3]
- Axis 3 [QTTY. 1]
- GW Axis 4 [QTTY. 1]
- Axis 4 [QTTY. 1]
- Rot dwn Axis 4 [QTTY. 1]
- Rot up Axis 4 [QTTY. 1]
- Axis 5 [QTTY. 1]
- GR Pz1 [QTTY. 3]
- GR Pz2 [QTTY. 6]
- GR Pz3 [QTTY. 6]
- GR Pz4 [QTTY. 3]
- GR Pz5 [QTTY. 1]
- GR Pz6 [QTTY. 3]
3D Printed Parts (optional):
- Axis 1 Dec1 [QTTY. 2]
- Axis 1 Dec2 [QTTY. 1]
- Axis 1 Dec3 [QTTY. 1]
- Axis 3 Dec1 [QTTY. 1]
- Axis 3 Dec2 [QTTY. 1]
- Axis 3 Dec3 [QTTY. 1]
- Axis 3 Dec4 [QTTY. 1]
- Axis 4 Dec [QTTY. 1]
Hardware Parts:
- Steel rod Ø8 x 80 [QTTY. 2]
- Steel balls Ø8 [QTTY. 40]
- Steel Rod 3 mm [QTTY. 18]
- Round aluminum tube Ø 35 x 90 [QTTY. 1]
- Round aluminum tube Ø 40 x 110 [QTTY. 1]
- Steel rod Ø8 x 15 [QTTY. 1]
- M3 nut
- M3 x 12 SHCS screw
- M3 x 20 SHCS screw
- M3 x 12 SHCS screw
- Bearings Ø22 x 7 mm [QTTY. 5]
Electronics:
- Nema 17 Stepper-M [QTTY. 4]
- G16 - 8 Pin [QTTY. 2]
- G20 - 12 Pin [QTTY. 1]
- DC 6V Extended Gear Motor with Shaft [QTTY. 1]
- Nema 17 Cables [QTTY. 4]
- MG996R Servo-M [QTTY. 2]
✅ OFFICIAL WEBSITE: https://www.diy-tech.it/
🌐 MY BLOG:twitter.com/GiovanniLerda
----------------------------------------------------------------------------------------------
ON THE SITE YOU WILL FIND A NEW VERSION OF THE ROBOT AND NEW OPTIONALS !
Attachments
Step 2: Robot Structure
✅ OFFICIAL WEBSITE: https://www.diy-tech.it
🌐 MY BLOG:twitter.com/GiovanniLerda
----------------------------------------------------------------------------------------------
ON THE SITE YOU WILL FIND A NEW VERSION OF THE ROBOT AND NEW OPTIONALS !
Step 3: Base
- Insert the gear wheel (“GW Base”) on the shaft of the Nema-17 stepper motor.
- Insert the stepper motor in the space provided inside the Base (“Base”), anchoring it with 2 M3x20 screw
- Insert the 8 mm diameter balls (“Steel Balls”) inside the appropriate cavity, for a total of 40 balls. It’s recommended to lubricate the balls to decrease friction.
- Insert the 8 M3 nuts inside the inner ring (“Internal GW”).
- Rest the inner ring with the 8 M3 nuts inserted inside it on the balls, so that the cavity matches the position of the balls.
- Insert the 8 M3 nuts inside the Base (“Base”).
- Anchor the outer ring (“Base ring”) to the base with 8 M3 x 20 screws, making sure that once fixed, the inner ring (“Internal GW”) rotates according to the correct movement.
✅ OFFICIAL WEBSITE: https://www.diy-tech.it
On the official website you will find the complete manual for assembling the Robot.
🌐 MY BLOG:twitter.com/GiovanniLerda
----------------------------------------------------------------------------------------------
ON THE SITE YOU WILL FIND A NEW VERSION OF THE ROBOT AND NEW OPTIONALS !
Step 4: Axis 1
- Insert the gear wheel (“GW Axis 1”) on the shaft of the Nema-17 stepper motor. Perform the operation on two stepper.
- Insert the two bearings (“Bearing”) in the appropriate cavities of axis 1 (“Axis 1”).
- Insert the 2 stepper motor in the space provided inside the Axis 1 (“Axis1”), anchoring it with 4 M3x12 screws.
- Fix the 8 M3 x 20 screws to join axis 1 (“Axis1”) with the inner ring (“Internal GW”), matching the holes as shown in the figure. So as to allow the fixing of the screws with the nuts previously installed in the inner ring.
- Fix the decorative components on axis 1 (“Axis1”) as shown, taking care not to damage any other component.
✅ OFFICIAL WEBSITE: https://www.diy-tech.it
On the official website you will find the complete manual for assembling the Robot.
🌐 MY BLOG:twitter.com/GiovanniLerda
----------------------------------------------------------------------------------------------
ON THE SITE YOU WILL FIND A NEW VERSION OF THE ROBOT AND NEW OPTIONALS !
Step 5: Axis 2
- Fix the two half-toothed wheels (“GW Axis 2”) with plastic glue. Insert the Ø40 x 110 mm tube(“Round aluminum tube Ø 40 x 110”) into the cavity of axis 2 (“Axis2”), fixing it if necessary with screws M3 x 12.
- Join axis 2 (“Axis2”) and axis 1 (“Axis1”) with the relative components already installed by using an Ø8 mm tube (“Steel rod Ø8 x 80”) which allows movement of axis 2 on axis 1.
✅ OFFICIAL WEBSITE: https://www.diy-tech.it
On the official website you will find the complete manual for assembling the Robot.
🌐 MY BLOG:twitter.com/GiovanniLerda
----------------------------------------------------------------------------------------------
ON THE SITE YOU WILL FIND A NEW VERSION OF THE ROBOT AND NEW OPTIONALS !
Step 6: Axis 3
- Fix axis 3 (“Axis3”) in the correct position on the 40mm tube, inserting if necessary M3 screws in the appropriate cavities.
- Insert the bearings (“Bearing”) in the appropriate cavities as shown in the figure.
- Insert the gear wheel (“GW Axis 1”) on the shaft of the Nema-17 stepper motor. Insert the motor in the dedicated cavity on the right side of axis 3(“Axis3”), fixing it with 2 M3 x 12 screws.
- Fix the decorative components on axis 3 (“Axis3”) as shown, taking care not to damage any other component.
✅ OFFICIAL WEBSITE: https://www.diy-tech.it
On the official website you will find the complete manual for assembling the Robot.
🌐 MY BLOG:twitter.com/GiovanniLerda
----------------------------------------------------------------------------------------------
ON THE SITE YOU WILL FIND A NEW VERSION OF THE ROBOT AND NEW OPTIONALS !
Step 7: Axis 4
- Insert the servo motor (“MG996R Servo-M”) inside the cavity in axis 4, fixing it with 4 M3 x 12 screws. It is important to pass the motor cables through the cavity inside the component.
- Fix the half-toothed wheel (“GW Axis 4”) with plastic glue.
- Join axis 4 (“Axis4”) and axis 3 (“Axis3”) with the relative components already installed by using an Ø8 mm tube (“Steel rod Ø8 x 80”) which allows movement of axis 4 on axis 3.
- Fix the component (“Rot dwn Axis 4”) on the servo motor using the appropriate screw supplied with the motor, screwing it on the motor shaft fixing the component. Insert the Ø35 x 90 mm tube(“Round aluminum tube Ø 35 x 90”) into the cavity of the component (“Rot dwn Axis 4”) fixing it if necessary with screws M3 x 12.
✅ OFFICIAL WEBSITE: https://www.diy-tech.it
On the official website you will find the complete manual for assembling the Robot.
🌐 MY BLOG: twitter.com/GiovanniLerda
----------------------------------------------------------------------------------------------
ON THE SITE YOU WILL FIND A NEW VERSION OF THE ROBOT AND NEW OPTIONALS !
Step 8: Axis 5
- Install axis 5 on the component (“Rot up Axis 4”). Insert the bearing (“Bearing”) in the cavity plus the Ø8 x 15 mm (“Steel rod Ø8 x 15”) rod and from the opposite side of it insert the servo motor (“MG996R Servo-M”) in the right direction, fixing it with 4 screws M3 x 12.
- Secure the servo motor with the screw supplied with it.
- Fix the DC motor (“DC 6V Extended Gear Motor with Shaft”) on axis 5.
- Fix axis 5 (“Axis5”) in the correct position on the 35mm tube, inserting if necessary M3 screws in the appropriate cavities.
- Fix the decorative component on the component (“Rot up Axis 4”) as shown, taking care not to damage any other component.
✅ OFFICIAL WEBSITE: https://www.diy-tech.it
On the official website you will find the complete manual for assembling the Robot.
🌐 MY BLOG: twitter.com/GiovanniLerda
----------------------------------------------------------------------------------------------
ON THE SITE YOU WILL FIND A NEW VERSION OF THE ROBOT AND NEW OPTIONALS !
Step 9: Gripper
- Fix the brackets (“GR Pz1”) on axis 5 with the M3x 10 screws as in the picture.
- Insert an M3 nut inside the sliding bracket (“GR Pz5”).
- Insert the piece on the DC motor shaft (“DC 6V Extended Gear Motor with Shaft”) as shown in the correct position and with the M3 nut facing upwards.
- Assemble the remaining parts of the gripper (“GR Pz2 - GR Pz3 - GR Pz4”) as shown in the figure using the special cylinders (“Steel Rod 3 mm”) which allow the parts to slide between them.
- Install the last 6 mm rods (“Steel Rod 3 mm”) to connect the PZ3 with the PZ5 using the PZ6 (“GR Pz6”) as shown in the figure.
✅ OFFICIAL WEBSITE: https://www.diy-tech.it
On the official website you will find the complete manual for assembling the Robot.
🌐 MY BLOG:twitter.com/GiovanniLerda
----------------------------------------------------------------------------------------------
ON THE SITE YOU WILL FIND A NEW VERSION OF THE ROBOT AND NEW OPTIONALS !
Step 10: Cables Management
In many components it is possible to find holes and cavities useful for the passage of motor cables, therefore the use is recommended.
✅ OFFICIAL WEBSITE: https://www.diy-tech.it
On the official website you will find the complete manual for assembling the Robot.
🌐 MY BLOG:twitter.com/GiovanniLerda
----------------------------------------------------------------------------------------------
ON THE SITE YOU WILL FIND A NEW VERSION OF THE ROBOT AND NEW OPTIONALS !
Step 11: Connectors
It is recommended to use the G16 -8 PIN and G20 - 12 PIN connectors to connect the motors in a simple and fast way to the microcontroller, so as to be able to make the robot free from the weight and encumbrance of any case containing the control circuits and drivers.
- Connect the component (“Base door”) on Base with the M3x 10 screws as in the picture. Insert the connectors as shown in the picture.
Note:
It is necessary to solder the motor cables to the ends of the connectors.
✅ OFFICIAL WEBSITE: https://www.diy-tech.it
On the official website you will find the complete manual for assembling the Robot.
🌐 MY BLOG:twitter.com/GiovanniLerda
----------------------------------------------------------------------------------------------
ON THE SITE YOU WILL FIND A NEW VERSION OF THE ROBOT AND NEW OPTIONALS !
Step 12: Images & Info
For more information see the official website: https://www.diy-techn.it Otherwise contact me via email at: lerdagiovanni@hotmail.com
On the site you will find the STL files to proceed with the printing of the components and other information about the product, including the Software part and the electronics of the Robot.
YT Video: https://www.youtube.com/watch?v=Lrvtf4m6fgc&t=99s
Note:
If you can't find the STL files for printing, contact me by mail!
If you are interested in purchasing the product already assembled and ready to use, contact me.
I Wish you a Good Job!
✅ OFFICIAL WEBSITE:https://www.diy-tech.it
🌐 MY BLOG:twitter.com/GiovanniLerda
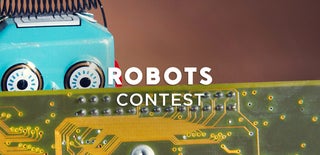
Participated in the
Robots Contest