Introduction: Kids Learning Tower / Work Desk for ~ 30$.
I am submitting this as part of the Tables and Chairscontest. If you found it helpful, or just think its cool. Please vote for me. https://www.instructables.com/contest/tablesdesks20...
I was recently asked to build a "learning tower". For those who don't know what it is, its a step stool of sorts that allows a Toddler (or small child) to safely engage with activities on a counter or table. Its a great way for them to get involved in cooking and similar tasks. After extensive research I couldn't quite find anything that really spoke to me. So I decided to design my own.
The criteria I was working from were as follows:
- takes up as little room as possible
- can slide under a table or counter
- be a efficient use of materials.
- Aesthetically pleasing & functional
During the design process I realized that if it could be multi-functional, so much the better.
- Be able to convert from a learning tower to a table.
Bellow is my journey of discovery that eventually led to my Learning Tower / Work Desk.
(This is my first Instructable. If I missed any steps you would like to see, please let me know and I will do the best I can.)
Step 1: Collect Your Materials and Tools
In full disclosure, I have a bunch of tools collected over the last 6 years. I also had half a sheet of 7 ply 3/4" plywood that heavily dictated a lot of my dimensions and decisions. That being said, I designed it in such a way that you could use different sheet goods and have similar success. Also, though I used power tools, it should be pretty easy to build with simple hand tools.
Necessary Materials (to build what I built)
- 48"x32" (1/3) Sheet of Plywood or similar ( I used 7ply 3/4") $39.99/3=$13.33
- 5'-0"x1/2" EMT Conduit. $1.25
- 5/8"x48" Hardwood Dowel. $1.77
- 1/4" Dowels (28 come with the 1/4" doweling kit, see bellow) $3.99
- Set of Hinges, I chose 2 1/2"x 1 9/16" Middle Hinges. $3.96
- Wood Glue. I chose to use Gorilla glue after some research. $4.97
Total: $29.27
This is the bare minimum cost if you don't consider the rest of the plywood sheet as cost or you can share it with someone else. Your millage may vary.
Optional Materials
- Countertop Laminate. 5$ from Habitat for Humanity Resale
- Laminate contact cement or similar. $12.97 (I had some, but most people would have to buy it)
- Non-toxic wood finish. I choose bees wax / orange oil. $7.99
- Latch. to keep it from hinging when in Tower mode. The one I used originally broke, so I don't have a recommendation.
Because I'm a perfectionist I really wanted to dress it up. My total cost was 55.23$. Which is still a lot cheaper & useful than the commercial ones I saw online. That is if you don't include my labor, of course.
Necessary Tools
- Saw for cutting wood. ( I used a combination of table saw, circular saw & jig saw)
- Saw for cutting metal. ( I used a angle grinder, but a hack saw or band saw would have worked just as well)
- Drill
- 3/4" drill bit, 5/8" drill bit
- 1/4" dowel kit (Harbor Freight)
- Sand Paper always good when your working with wood.
Optional Tools
- Clamps. I put these as optional.. because I don't think you absolutely need them, but I don't think my project would have come out as good without them. I used bar clamps, but I have heard that ratchet straps can do the same thing.
- J-Roller. Its just a hard plastic roller used to make sure the laminate glue gets a nice tight bond.
- Router with flush trim, round-over & straight bit. I placed the router in optional tools because its not necessary to finish this project, but it was a amazingly helpful during this project.
- Belt Sander. Nice when your cuts don't come out quite as smooth as you would like.
Attachments
Step 2: Plywood Dimensions & Components.
The First step is to rip the lumber down to the component size. If you have access to a printer that will print 24" wide the attached PDF has full size drawings in it of the 4 most complex components. If not the first picture above provides the dimensions. Some might ask "why does everything say EQ.(Equal)" . The reason why is that it is important that all of the pieces come out approx the same size. The height of the TOP SIDES & BOTTOM SIDES is especially important because when folded down in table form it has to be equal to sit flat to the floor. If I just divided say the 48" width by 4 it would not account for the width of the cut. The result would be 3 pieces that are 16" and one piece that would be 16 - the width of the saw blade x 3 cuts. I have included the cut order, which if followed should provide approx. equal components.
PRO TIP: Once the components are cut out its a good idea to check to make sure they are all the same height. Unless you are better at cutting things than I am you will find that there might be some slight variation. This is where a belt sander comes in handy. I was able to "true up" everything which probably saved me a lot of headaches.
Once we have the rough shapes cut out its time to cut them into their final shapes. For the holes in the TOP SIDES I used a 1-1/2" hole saw to get my top and bottom radius, then used a jig saw to cut out the wood in-between. These holes are to give children something to grab on to, to both help them in moving it around, but to also provide them a hand hold for getting in and out. They can be optional, but I would recommend them. All other cuts I used the Jig Saw for. Again. It is your choice to include them, but most I found really improves the Towers functionality.
Now that everything is cut to your liking its time to drill some holes. You will need both the TOP SIDES & BOTTOM SIDES. You will need to decide which sides will be the insides, and which the outsides. The reason is we are going to drill a stepped hole to accept our EMT support rods. Starting from the inside drill a 3/4" hole about 1/4" deep. Finish the hole all the way through with a 5/8" hole. the 3/4" section is for the EMT. The 5/8" section if for the 5/8" dowel. Construction of the EMT support rods is outlined in the next step if you are curious what I am talking about.
Optional: Use a router , or Sandpaper to ease the edges of the plywood. Cut plywood is sharp and the rounder the edge the less injury it will cause if someone falls into it. I used a round over bit and took care off all the edges that needed it. Be careful not to round over any edges where two pieces of plywood are going to come together. TOP SIDES -to- TOP BOTTOM, BOTTOM SIDES -to- DESK TOP, BOTTOM SIDES -to- SEAT/STEP. Should all be left square.
Step 3: Building the Support Bars.
The support bars are pretty simple. Cut the 5'-0" EMT into (4) equal 15" sections. Cut the 48" dowel into (8) equal 6" sections. Using some sort of blunt object, hammer the dowels into the EMT. I used a dead blow hammer, but a regular hammer and a piece of wood, would work just as well. You want to hammer in the dowel until there is about 1" of dowel left exposed. We only need 1/2", but we will cut off the remainder after it is assembled.
In the pictures I show 5 support bars. After testing I found the extra bar actually made it less functional so I removed it. If you look at the final assembly you can see that it only has 4 bars.
Step 4: Assembly
Now that we have all of the components ready, it is time to assemble everything. I chose to use dowels to hold everything together. Mostly because I didn't want any exposed fasteners. Feel free to fasten it together what ever method you feel is going to work best for you. I used 5 dowels to hold the sides and tops together. In retrospect, I should have only used 4 since the dowel kit only comes with 4 dowel center transfer punches.
If you choose to use dowels you will want to start with measuring in from the edge of the plywood by half its thickness. If you are using 3/4" plywood, it would be 3/8". using the provided collar and drill bit, drill equal spaced holes 1/2" deep along the line. Put the transfer punches in the holes you just drilled. Here is the tricky part. Line the sides up with edge of the plywood & transfer the dowel locations into the edge of a side component (see the second picture if this sounds confusing). Repeat for the other side. Then repeat for the other components.
NOTEBecause we now have right and left sides, it is important to make sure that they don't get mixed up. If they get mixed up the 3/4" DIA. recess for the EMT will be on the wrong side.
Now it is time to do a dry fit to make sure everything fits the way it is supposed to (hammer may be necessary to massage things into place). If everything went the way it is supposed to it is time to glue everything up. I chose to use Gorilla Glue for its expanding properties, this may be overkill and regular wood glue may suffice. Put glue in the dowels and in the glue joints. Also glue the support bar dowels into their holes. I wasn't to worried about squeeze out because I knew I would be sanding and finishing it. If I build another one I will probably tape off the EMT. It sticks to it a lot better than I expected. Once everything is glued up it is time to clamp everything together.
PRO TIP I guess I'm not a pro, since I didn't think of this. The support bars will crush into the plywood when clamping. The result is my top and bottom ended up being slightly narrower than the sides attached to the plywood with dowels. I would recommend using some scrap cut to the inside dimension as a brace between the support bars.
I let mine dry overnight. If you are in more of a rush just find out what the curing time of the glue you are using is. When everything is dry, cut the support bar dowels flush with the plywood sides.
Step 5: More Assembly. Adding the Hinges.
Caution: If you plan on adding laminate you need to subtract the thickness of the laminate from the measurement you use to recess the hinges.
This is the last step if you are going for a bare bones desk. It is maybe the most important one since its really just a desk and a side table without the hinges. Take whatever hinge you are going to use and look at it. You will discover that it doesn't actually sit flat when closed. If opened up so that both leafs are parallel you will see that there is a slight gap. This is important, because if the hinges were just mounted to the face of the desk the would sit apart at what I consider a significant angle. To prevent this we need to recess the hinges into the face of the desk.
Align the top and bottom together in their down position (A clamp helps keep them tight). Place both hinges on the top, barrel up, centered on the seem. trace their outline.
How you Cut the recess is up to you. I have used a router and a straight bit. Quick and dirty. A utility knife and a chisel would do a good job as well. The most important part is making sure they are deep enough. The holes should be half the width of the hinge, when folded so both leaves are parallel. I think I ended up with 3/16" as my measurement.
Once you have the recesses cut, screw them in place & test to see if it closes tight. You may need to remove more material if there is still a gap.
!!CONGRATULATIONS!!You just finished building you very own learning tower / work desk.
Step 6: Finishing Touches. Adding Laminate and Staining.
This is a completely optional step. At this point you should have a functional piece of furniture. But if you want to really wow your friends its time to turn it into something that looks professional.
Adding laminate is super easy. First thing you are going to want to do is cut a couple pieces about 1" larger the the finished size of your desk tops. If you can, use a factory edge for the edge used for the seem. Next you are going to want to cut a small notch in both pieces where the barrel of the hinge will poke up through the laminate.
Once the fit is acceptable. It is time to apply the glue. Using a low nap roller, or brush. put a thin coat of glue on both the desk top and the back side of the laminate. If you have never used contact adhesive before you may think its time to glue them together. That would be a mistake. You have to wait until the adhesive has dried until it is tacky before you can put them together. Once they are ready. Starting at the seam, gently lay each piece of laminate on the side it goes to. Hopefully you it is in the right place. If it needs adjusted, just pull it up and try again. Once they are positioned where you would like, push down on them (I used a j-roller) to make sure the glue is adhering properly. Let it dry. It actually cures out pretty quick, it usually gives cure times on the back of the glue you are using.
Once the glue has had time to cure it is time to trim the laminate to fit. I used a router with a flush trim bit... but I understand not everyone has one. You could use a sander, or a file to bring the edges down flush with the sides of the tops, its just time consuming.. I know, I've done it. One they are flush with the sides, it is a good idea to "ease" the edges of the laminate because they can be sharp. Using a file, go along the edges at a 45* angle and add a slight bevel.
The final step is staining to protect the wood. Since this is going to a child I decided to use a natural, non-toxic oil finish. Its not the most durable finish but it is the safest option.
!!CONGRATULATIONS!!
You are really finished this time. If my instructions are clear & you followed them accurately, then you should have a piece of furniture that will last for years. And hopefully will enjoy.
Step 7: Closing Thoughts.
After testing it for several weeks I have found that it is both pleasing and functional. A 2 year old has no problems raising and lowering it as needed. When in its tower arrangement it is slides easily under the counter for storage. It will hold my 210lbs at the very edge of the desk with ease, so its durability is outstanding.
If I was to do it over again, the only change I think I would make is to use a higher quality plywood & have the parts cut by a CNC machine. The whole time I was building it I felt like I was chasing my inability to get a perfect cut.
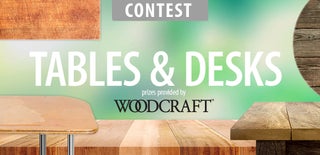
Third Prize in the
Tables and Desks Contest 2016