Introduction: Kiln Dry Lumber at Home
Kiln drying your own wood at home can be a great way to sustainably harvest the materials around you, and dry it fast enough to build furniture with. If furniture is made with wood that is too wet, it will continue to dry and crack, possibly ruining the piece. This instructable takes you through the process of raw wood in the spring, to dry lumber in the fall. You can do this with any kind of wood.
Step 1: Mill Up Your Wood
Once you've gotten the wood, local sawyers are plentiful in most areas, and many will bring their portable sawmill to you for a very reasonable rate. I pay $100 an hour here, and a good sawyer can do a lot in an hour. Worth their weight in gold, these hardworking folks are a woodworkers dream come true, and they often have a stock of amazing, local woods for sale.
You can also choose to mill it yourself with a chainsaw, which I partially do sometimes depending on the log. If you choose to do this, read up, and follow all the safety precautions of those tools. And like anything in woodworking, protect your eyes, ears and lungs.
Step 2: Wood & Moisture
Step 3: Air Drying
Start off by air drying your wood for a few months to shed the first bit of water naturally, maybe a loss of eight to ten percent. Stack the wood up with plenty of spacers, or stickers, to allow for good airflow, and I like to put a piece of plastic on the ground under the wood to keep the humidity from the ground from effecting the lumber. I bind the wood with tie downs to minimize cracking and twisting, and I build a temporary plastic roof to keep off the rain. Place it in a location with good prevailing winds, it makes a big difference.
Step 4: Build the Kiln
The fan circulates the air to even out the drying. I designed mine to pull air from below, then blow the air down a plastic tube to the other end. This way I know there's no stagnant air or dampness trapped in the kiln. This one is 20 feet, or 6 meters, long. The dehumidifier is also trapped inside the kiln and is set to maximum. This model has a hose that runs out of the kiln and fills a bucket.
The kiln is built around the stacked and bound lumber over a light wooden frame that carries the plastic. All seams need to be sealed with vapour barrier tape to hold the moisture in. I cut a few small access holes to control the dehumidifier and to test the woods moisture content in various places. Tape up these holes after you use them. The wood remained in the kiln for about 4 months and reached an average of 8 percent. This is mostly 2" thick arbutus, also called madrone.
Step 5: Using the Wood
Step 6: Making Furniture
Thanks for taking the time to read through this instructable, now get out there and save some logs!
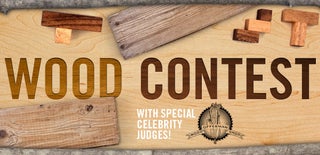
Runner Up in the
Wood Contest