Introduction: LCD 3D Printer
UPDATE: THIS PROJECT IS NOT FUNCTIONAL. If anyone has any tips to help make it functional, your help is greatly appreciated.
I am a fifteen year old who took an interest in 3D printing about two years ago. I tried and failed to build a fused deposition modeling 3D printer. There were too many moving parts that I had issues with. So, I began exploring simpler, less complex printers. I came across the "Olo" smartphone 3D printer which uses your LCD screen on your phone to cure resin. I thought this was a great idea, so I decided to scale it up with a monitor. I am entering this instructable into the 3D printing contest because I really want to better understand how FDM printing works and how I can make my previous one better by getting a commercial printer. I hope you will vote for my instruct able based on its merit. I would also appreciate constructive criticism because I am always looking for ways to get better.
Thanks!
Carter
Step 1: Bill of Materials
Item- Makerbeam 300mm
Quantity- 14
Link- https://www.amazon.com/MakerBeam-300mm-beam-black-...
Item- Makerbeam Corner Cube
Quantity- 8
Link- https://www.amazon.com/MakerBeam-Corner-Cube-Black...
Item- Makerbeam Bearings
Quantity- 4
Link- https://www.amazon.com/MakerBeam-Bearings-bolts-se...
Item- Makerbeam M3 Bolts
Quantity- 100 (I did not count, but it is better to be safe)
Link- https://www.amazon.com/MakerBeam-bolts-wing-type-h...
Item- Makerbeam Right Angle Bracket
Quantity- 6
Link- https://www.amazon.com/Makerbeam-Openbeam-Right-An...
Item- Stepper Motor
Quantity- 1
Link- https://www.amazon.com/Stepper-Motor-Bipolar-64oz-...
Item- 8mm Lead screw w/ Nut
Quantity- 1
Link- https://www.amazon.com/Drillpro-400mm-Lead-Screw-P...
Item- Miscellaneous M3 Screws and Nuts
Quantity- N/A
Link- N/A
Item- RAMPS 1.4 w/ Arduino
Quantity- 1
Link- https://www.amazon.com/OSOYOO-Printer-Controller-S...
Item- LCD Square Monitor
Quantity- 1
Link- https://www.amazon.com/E172FPb-Inch-Flat-Panel-Mon...
Item- 12x12 Inch Clear Glass
Quantity- 1
Link- N/A
Item- Purple Acrylic Sheet
Quantity- 4
Link- https://www.amazon.com/12-violet-Acrylic-Plexiglas...
Item- Craft Wood 1/16 Inch Thick
Quantity- N/A
Link- N/A
Item- Aluminum Angle Iron
Quantity- N/A
Link- N/A
Item- Expanded PVC Sheet 12x12
Quantity- 1
Step 2: Build the Makerbeam Cube
Get the four Makerbeam corner cubes, the screws that come with them, and the Makerbeam. Attach all 12 pieces to the corner cubes to form a cube. This cube will be the "chassis" of the 3D printer.
Step 3: The Z-Axis
Next, you will build the z-axis.
- Get two pieces of Makerbeam and place a Makerbeam screw on the bottom of each one.
- Get six right angle brackets, and three screws and nuts for each bracket.
- Place the two pieces Makerbeam in one side of the cube and tighten them.
- Do this by twisting the beam in place.
- Then, put the right angle brackets on the beams like the picture.
Step 4: Motor Mount
The motor mount is a very difficult piece.
- First get two M3 screws that are at least an inch and a half, and file them so they do not turn, but fit into the Makerbeam's groove.
- Then, remove to screws on the same side of the motor. You will not need these.
- Place a nut on the M3 screws.
- Screw in the M3 screws to the top of the motor so that there is a inch gap between the head and top of the motor.
- Unscrew the beam of the cube that has the z-axis attached. Do not remove the beam.
- Move the beam so you can slide in the motor. Place the motor so the shaft is in the middle of the z-axis.
- Tighten the nuts of the screws so that the motor does not move.
- Place the motor coupler and shaft onto the motor.
Step 5: Z Axis Bearings
- Cut 2 piece of the craft wood so it is roughly 2 inches by 3 inches.
- Take one drill two M3 sized holes that are vertically aligned towards the edge.
- Then, place a M3 screw into each hole, along with a nut, washer, bearing, and nut.
- Hold this up to the z-axis and mark two more holes so that the z- carriage is tight around the beams.
- Copy the holes on the second piece of craft wood and attach it to the carriage. Use a nut to tighten it.
- Next, get a piece of angle iron and attach it to one side of the craft wood.
- After that, drill holes that match the lead screw nut, so you can attach it.
- Attach the lead screw nut.
Step 6: Resin Tank
- Get the clear square of glass and use caulk to attach it the the bottom of the printer.
- You cannot use plastic because it has UV blocking qualities.
- Then, attach the purple plastic squares to the all the sides of the printer except the one with the z-axis and its opposite.
- For the side opposite the z-axis, use a hinge to attach it, so it can be opened.
- Cut the remaining plastic square so you have a strip three centimeters tall.
- Attach this strip to the bottom of the side with thee z-axis.
- Do not put any resin in the tank yet.
Step 7: Print Platform
- Get two pieces of Makerbeam.
- Screw them on to the top screws of the z-carriage.
- Get your expanded pvc. You may need to cut it to an 11x11 so it easily fits.
- Drill 2 holes bout 1.5 mm deep into the pvc.
- Get a piece of wood about six inches and drill two holes that correspond to the ones on the platform.
- Attach them.
- Get a 3 inch piece of wood and drill 2 holes that correspond with the width of the maker beam, and another one to attach it to the previous piece of wood.
- Get two maker beam screws and slide the platform onto the maker beam. Make sure it is tight.
- Then use two right angle brackets to attach the ends of the maker beam.
- Optional: I attached a piece of glass to the bottom of the pvc. I did this to ensure a smooth print surface.
Step 8: Legs
- Cut four pieces of wood six inches.
- Attach them to each corner of the bottom of the printer.
Step 9: Attaching the Monitor
- Place the monitor on the bottom of the printer.
- You may need to sand the legs so it fits.
- Hot glue the edges of the monitor in place. You can also use books to place underneath the monitor if you are worried.
- I turned the printer upside down so it was easier.
Step 10: Attaching the Electronics
- Plug the z-axis motor into the RAMPS 1.4. It should be plugged into the port farthest toward the right, the one with two plugs.
- The RAMPS needs a power supply.
- Plug the monitor into the computer.
Step 11: Software
Download the appropriate firmware onto the RAMPS 1.4.
I used Creation Workshop to control my printer. It can be found at the following link https://github.com/area515/Creation-Workshop-Host.
You should also download Repetier-Host so you can configure the steps per millimeter for the z-axis easily.
Step 12: Configuring the Z Axis
Open Repeater Host.
- Plug RAMPS 1.4 into the computer and attach the power supply. Connect the board, you may have to change the baud rate or port number.
- On the right side there is a panel with "Object Placement", "Slicer", "G-Code", and "Print Panel". Click on "Print Panel".
- There should be a spot to type in G-Code.
- Type in "M92 Z100" and press enter. This will set the steps per millimeter to 100. Then type "M500" to save the configuration.
- Then tell it to move 10mm.
- Measure the distance actually moved.
- Plug the numbers into the following formula: (10/millimeters moved) x 100
- Then type "M92 Z(number found)"
- Type M500 to save the configuration.
- The more you do this, the more accurate your printer will become. If you do this more than once, instead of using 100, use the number found the previous time.
Step 13: Configuring Creation Workshop and Printing
This step may be easier if you remove the platform or move it so you can easily see the monitor's screen.
Measure the height and width of the screen. You will need this later.
Make sure the display setting is on extended screen.
Open Creation Workshop. Locate the Machine Config tab.
Input the height and width into the axis length in the x and y spots. Select "DISPLAY 2".
Go to the Machine Control tab and press "show" in the projector section.
Measure one square to confirm it is one square centimeter. If it is not, adjust the x and y values to fix this.
Fill the resin tank with resin.
Upload a SVG file.
Change the cure time to about 12 seconds. However, be prepared to raise this value significantly due to the low levels of UV light that the monitor emits.
Print the SVG.
I have not had a chance to test this because I have not been at home for the past week and a half.
Step 14: Software Alternative- ProjectLayer
I tried using Creation Workshop, but it only communicated with the monitor. It did not talk to the RAMPS board. So, I looked online for alternatives. I found a program called ProjectLayer, which is a modification of :.
It is listed at http://garyhodgson.com/reprap/projectlayer/
Configuring-
In the extracted files, open the one entitled "Pronterface". I suggest making a shortcut to your desktop for this program.
Connect to your RAMPS. You may have to change the port or baud rate to connect. Connect to the RAMPS before plugging it into the power supply.
It will give you an error alerting you that it is in "Dry Run Mode". Disregard this because it does not affect this type of printer.
Go to file in Pronterface and click on "Projector". This will open "ProjectLayer".
Move the "ProjectLayer Display" onto the monitor.
Click the "Fullscreen" and "Calibrate" boxes in the control window.
Adjust the number of pixels ( "X(px)" and "Y(px)") so that the grid fills up the whole screen.
Next, change the "ProjectedX (mm)" value so that each square is a square centimeter.
Change the "Direction" to "Bottom Up" and the "Blank (s)" to 2.5.
I choose bottom up because generally the bottom has the largest surface, therefore the more stuff to stick to the platform.
Choose the layer setting of your choice. Make sure you write down this number because it will be needed later.
Change the "Exposure (s)" value to 15. You may need to raise this due to the low levels the monitor emits. It is basically how long the resin takes to cure.
Printing-
Make sure you have the newest version of "Slicer" on your computer. The new one is the best at creating "SVG" files.
Open Slicer and press "ctrl g" this will prompt you to choose a file.
Choose the file you want to print. I recommend a small cube first. It is a simple print and you will have what it looks like with shrinkage taken into account, that way you can adjust the scale in ProjectLayer.
After you open the file it will prompt you to choose a location for the SVG. I choose my desktop because it is easily accessible.
Go back to the ProjectLayer control panel and select load.
Select the SVG file you just created.
Click on the "First Layer" box and change the offset so you can position your print.
If you look in the info section it will tell you the amount of layers the print has. I divided this number by the total height of the print and got my layer height. I did this because I forgot the value I used in Slic3r.
Press "Present" to start the print.
Optional: Use the "First Layer" command to ensure you get the print to adhere to the platform. The value "-1" has the first layer displayed infinitely. You can change the value so how many second longer you want it to be there. This is to be done manually, because pressing "Present" will not take into account the extra time.
Step 15: Replacing the Backlight (Optional, But Recommended)
I had trouble curing the resin with the LCD screen. So, asnzqwack suggested, I have replaced the original backlight with a UV backlight. In order to make sure the resin was cured by the light, I used the inverter and plugged it into the power supply for the printer. It cured the resin in a matter of seconds.
When you test this, make sure not to get any resin on you. The curing process is exothermic and will burn you. It is also like super glue and is very difficult to get off once it is cured.
First, remove the back of the monitor. This will allow you to get to the old backlight.
Step 16: Choosing the Right Resin
LCDs block almost all UV light. So, a visible light resin needs to be chosen.
It is possible to use some UV resins.
First, you need to change the RGB scale so it is only blue/violet. They have the lowest wavelength, some of which falls on the scale of some UV resins
You will need to use the buttons on your display to do this.
You should also use the Windows Monitor calibration and set maximum brightness, blue, and contrast for best results.
In order to use the UV resin, first you need to open a print with a large bottom. I used a cube. Turn on the first layer view and remember where the print is.
Turn off the first layer view.
Put 10 drops in the tank on top of where the print is.
Time how long it takes for the resin to harden. Use this as your exposure time. Expect very large values and keep it in seconds.
I am going to test this resin soon, it has one of the highest wavelengths (blue) I have seen. http://bucktownpolymers.com/zve200-v470.html
Step 17: Final Remarks
Next time I would like to create an easier way for the platform to be removed. I would also like to make it more level.
I used an old plastic page divider for two sides of my printer because I could not get the glass cut small enough to print.
I have just started to update the intractable. I am still waiting for the resin I ordered. I will update it more as soon as possible. This way, I will have results and will be able to form better conclusions about the project. I do apologize that I was not able to finish it, and resorted to posting an unfinished work to meet the contest deadline.
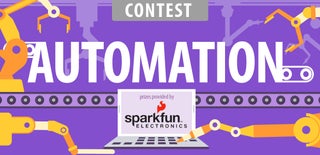
Participated in the
Automation Contest 2016
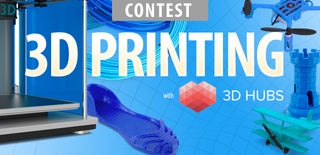
Participated in the
3D Printing Contest 2016