Introduction: LED Torchiere
I wanted to convert my energy wasting incandescent torchieres to LED but there isn't an LED bulb powerful enough to get even close to the amount of light I was used to. So I built an adapter to let me use 4 LED bulbs at once without affecting the appearance of the torchiere at all. Now I use 150W less energy every time I turn it on.
In my home we have three very nice torchiere floor lamps. They are rated up to 250W each and I have 200W incandescent lamps (bulbs) in each of them. Two of the torchieres are in our living room and are the major source of light in that room. I wanted to switch over to LEDs, but I'm not aware of any screw-in LED equivalent for a 200W incandescent bulb.
Soooooooooo..... I decided to see if I could retrofit the Torchiere to take four LED lamps (Four 60W equivalents). The LED lamps use 12.5 watts each so my fix uses 50W and produces as much light as the 200W incandescent I'm replacing.
Materials:
4 - Philips AmbientLED LED light bulbs
4 - ceramic light sockets (optional in my case)
Screw-in Socket Adapter (Socket to receptacle)
Add-on Plug, polarized
1/8 inch thick sheet acrylic plastic (recommend polycarbonate)
18 inches of electrical cord
Solder
Liquid Tape
silicone caulk
epoxy glue
Electrical Tape
Tools:
Hand and machine tools necessary to shape the acrylic/polycarbonate sheet
Wire strippers
Soldering Gun (140W or greater)
screwdriver if the Add on Plug body takes one
CAUTION - This is an electrical project utilizing hazardous household (mains) voltage and current. Making a mistake can result in property damage, personal harm or even death. You need to be familiar with electricity and its hazards. If you are not knowledgeable and comfortable with this project do not attempt it. You take full responsibility for the project you build. I may be taking risks that are acceptable to me, but may not be acceptable for you or your circumstances. Build at your own risk. If you do not understand or have questions consult a professional electrician. Sorry for the disclaimer, but if you burn something down or kill yourself it's your own fault.
P.S. If you find the Instructables I post interesting please click the "Follow" button above. Thanks!
Step 1: LED Lamp (bulb)
Both the AmbientLED and L-Prize lamps are the funny looking bulbs that look orange when not energized. The plastic lenses have phosphor in them that gives the lens the orange color. The bulb uses BLUE LEDs behind the lens so that when the blue light strikes the phosphor in the plastic the phosphor glows white. This apparently has some efficiency advantages and helps with consistent light color. 'Regular' white LEDs are also blue LEDs but have the phosphor applied directly to the LED die (silicon) but Philips separates them for this bulb. I popped open one of the orange plastic lenses and you can see the blue LEDs inside.
These LED bulbs are very bright and virtually match the color of a 60W incandescent. They are also estimated to last 25,000 hours, or 22.8 years at 3 hours per day, per the box. See my side by side comparison of a 60W incandescent to the 12.5W LED in my torchieres. However, 60W is not enough so on with the build....
Step 2: Assess Your Space
You will have to see if you can fit a socket as well as determine the layout and orientation of the bulbs. And how to mount them in the product you are retrofitting. I didn't think it was too hazardous to omit the sockets because all the materials around the screw bases of the bulbs are either glass, ceramic or plastic (probably phenolic). It's still a good idea to electrically insulate the bottoms of the bulbs to keep the electrical contacts from being exposed. And it also keeps them insulated if the glassware should ever break.
Step 3: Build the Frame
I had to determine how to fasten the frame down. I chose to mount it to the existing center socket by capturing it between the socket and an adapter that screws into the socket. I made a central hole in the frame large enough to just allow the threads of the socket adapter to slide through and screw into the existing torchiere socket. This lets me easily remove the retrofit.
The four holes for the bulbs are located as far from the central hole as possible and equally spaced around it. I also added two small holes to allow threading the power wires from my plug down to the underside of the frame to make the electrical connections to the bulbs.
The LED bulbs still generate a fair amount of heat so make sure they have ventilation. The LED bulbs should not be installed in a closed space and should last longer if installed with the screw base at the bottom to keep the LEDs at the top for maximum cooling. You should also be concerned about exceeding the temperature of the frame material, which is why I now recommend polycarbonate since it has a higher working temperature. If there is any doubt you should measure the temperature on the frame and compare it to the manufacturer's specifications for the material.
Step 4: Add the LED Bulbs
Any portion of the bulbs' screw base that will be located above the acrylic frame should have electrical tape applied to prevent anyone from contacting it. The bulbs are inserted through the holes in the frame and oriented so that one of the 3 bulb lenses faces away from center to give the best light distribution. One end of the electrical cord is split part way to provide two separate conductors and each end passed through the hole in the frame to get it to the bulb base contacts.
Solder the wires to the bulb metal base contacts. Use a high wattage soldering gun (>140W) as it takes a lot of heat to solder to a screw base. The center bulb contact is soldered to the wire that goes to the narrow plug blade (hot, line). The outer screw bases are soldered to the other wire that goes to the wide plug blade (neutral). Check that your solder connections are secure. It is easy to get a cold solder joint that will pop off with a tug or bump.
The wires are connected to the polarized plug making sure the correct wire is connected to the correct blade as noted above.
After the wiring is done test the assembly to make sure the bulbs light. If you have exposed electrical contacts make sure that they are not going to contact anything electrically conductive, yourself or another person.
If the bulbs light you can install the frame in the Torchiere and position the bulbs to their final orientation. I had to angle mine slightly outward to keep them from touching each other and to allow room for the socket-to-receptacle adapter and plug. After you find the optimum position you can secure the bulbs into the frame with silicone caulk or epoxy glue or both, depending on how permanent you want them mounted to the frame.
After the mounting adhesives have cured use Liquid Tape to coat any remaining exposed electrical parts to electrically insulate them. (My photos do not show this step). There should not be any exposed live electrical parts. After the Liquid Tape has dried you are ready to install the retrofit kit.
Step 5: Install Retrofit
Enjoy!
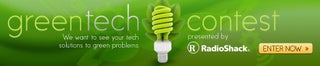
Participated in the
Green Tech Contest
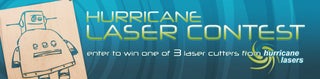
Participated in the
Hurricane Lasers Contest
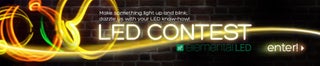
Participated in the
LED Contest with Elemental LED
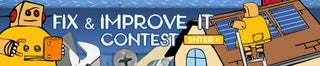
Participated in the
Fix & Improve It Contest