Introduction: Laser Cut Hawaiian Quilt
Hawaiian applique quilts are beautiful but very labour intensive. You start by thinking of a design, usually inspired by nature (e.g. palm trees, pineapple or breadfruit), cut out your design on a piece of paper folded into quarters, then open it up and trace the design onto fabric, and then cut it out by hand. You then applique it by hand to a solid fabric backing, turning the raw edge under and doing a close applique stitch.
I have never had the time or patience to make a Hawaiian applique quilt myself until just recently, when I figured out how to use a laser cutter to do the cutting, and use fusible web to replace hand stitching.
Few quilt designs are so perfectly suited to laser cutting as these Hawaiian applique quilts, which feature intricate designs and require precise cutting. After I experimented with my first laser cut applique, I realized that the laser cut was SO precise, that I could use both the part which was cut away, as well as the initial applique cut out, to make an interesting quilt, with both “positive” and “negative” images.
This technique is “no waste” – all of the fabric is used in the quilt. I love that this method saves both time and fabric, leaving more time to focus on design and colour choices. Super cool!
Step 1: Gather Tools and Supplies
For this project you will need:
- 5" squares of cotton fabric for the appliques, in a solid or mostly solid single colour
- 7" squares of cotton fabric for the background squares
- Quilt batting
- Cotton fabric for the quilt backing
- thread
The amount of fabric you need will depend on how big you want your wall hanging to be.
You will also need the following tools:
- rotary cutter and mat
- acrylic ruler
- pins
- scissors
- sewing machine
- access to a laser cutter
Step 2: Choose Fabric, Add Fusible Backing and Cut Into Squares
I used 5" squares of mostly solid fabric in 5 different colours, and lightly ironed them to Wonder Under, a paper backed fusible web, holding the iron down for 3 or 4 seconds on cotton setting. Do not fuse for too long at this stage or it will be hard to remove the paper backing from the fusible web. There are other brands of paper backed fusible web which would also work but I've had the best results with Wonder Under.
Step 3: Laser Cut the Applique Pieces
I took the fusible backed cotton pieces to my local makerspace, imported designs from the internet into Corel Draw (google "hawaiian applique designs" to find images) and laser cut the pieces on an Epilog laser cutter, using vector only, with settings at Speed 50, Power 20 and Frequency 50. The fusible backed fabric was .018" thick. The cut out patterns were sized to be 4" wide and were cut out of 5" squares.
Step 4: Remove Paper Backing From Applique Pieces
The hardest part is removing the paper from the back of your fused piece to expose the glue.
Cut a slit with a pin on the back of the Wonder Under paper and CAREULLY peel off the paper backing before fusing to the background fabric. With intricate designs and small pieces, you must be very careful not to rip off or damage any of the fabric when you are removing the Wonder Under paper.
Step 5: Iron Pieces Onto Background Fabric Squares
- Once the paper is removed, position the applique piece in the centre of your background fabric, then iron with a hot iron for 10 - 15 seconds to fuse it in place. A clear ruler can help you to position the applique exactly in the centre of your square.
- I used 7" squares of a white "tone on tone" fabric as the background fabric.
- The photos above show the piece that was cut out from the laser cutter, as well as the background "leftover" piece showing the cutout. I used both parts, fusing each to a white background square, but rotated the cut out piece 45 degrees, so it sits "on point", rather than having the same orientation as the background square.
Step 6: Arrange Squares on Design Wall or Floor
I started out with 7 different colours, but reduced it down to 5 after I laid the squares out on a "design wall". A design wall is a piece of flannel nailed to the wall - cotton fabric sticks to flannel, enabling you to easily rearrange the squares. You can use a flannel sheet, flannel fabric, or purchase a commercial design wall. If you don't have a design wall, lay the squares on the floor or on a bed, and keep rearranging them until you are happy with the design. A design wall is a great way to "audition" your design before sewing the squares together.
I took photos of several different combinations and arrangements so I could compare the different designs and decide which arrangement I liked best before doing any sewing.
Step 7: Sew Squares Together and Add Border
- Once you find an arrangement of squares that you like, sew the squares together with a 1/4" seam.
- Iron all seams open.
- You can decide how large you want your quilted wall hanging to be. I used 5 squares across and 8 squares down for a total of 40 squares. Once the squares were sewn together, the wall hanging was 33" X 52".
- I decided to add a narrow 1 1/2" border on all sides, made from the same white fabric as the background fabric. The border gives the applique designs a bit more room to breathe at the edges.
Step 8: Baste the Quilt Top to Batting and Backing Pieces
Cut backing and backing fabric about 2" larger than the quilt top on all sides.
I used a fusible batting (Hobbs Heirloom Fusible Cotton Batting) so I could fuse the quilt top to the batting and the backing, simply by ironing all 3 layers together. Other methods of basting the 3 layers together include using safety pins, using an adhesive spray, and hand basting.
Put the quilt backing (I used a plain white cotton fabric for the back) on the floor or on a large table, then put the batting on top, and finally put the quilt top over top of both layers.
Smooth the layers and put in a few pins to hold it together, then iron on both sides, to fuse both the quilt top and the quilt back to the fusible batting in the middle.
Step 9: Quilt Your Layers Together
The quilt stitch is what connects the quilt top, batting and backing together, by going through all 3 layers.
To keep the fabric from getting caught in the machine or creating drag, roll the quilt to expose only the area you will be quilting (see first photo above).
I used an even feed foot (also called a walking foot) and a stitch which creates a wavy line to quilt through all 3 layers, quilting long lines from one edge to the other, and then from the top to the bottom of the quilt, positioning the wavy line over the seams between the squares. If you don't have this "wavy line" stitch, you can do it manually, or use a straight stitch to stitch "in the ditch" of the seam. I chose to do the minimal amount of quilting possible - just enough to hold it all together. I didn't want to do more quilting as I thought it would just be a distraction from the strong graphic design of the applique pieces. There are many different ways this could be quilted, including using a free motion quilting technique - the choice is yours.
The last photo shows the quilt, with batting and backing securely attached by the lines of quilting going across and down the quilt.
Step 10: Add Binding and Hanging Sleeve
- Sew close to the edge of your quilt (approximately 1/4" from the edge) to hold the layers securely together, then trim the quilt (i.e. cut off any excess batting and backing fabric, so the quilt batting and backing are the same size as the quilt top).
- Cut a 5" strip of fabric, about 1" shorter than the width of your quilt, for a hanging sleeve. Fold and iron it in half lengthwise, and sew the raw edge of this sleeve to the raw edge at the top of your quilt, on the back.
- Cut 2 1/4" wide strips for the binding and sew these strips together to make a strip long enough to go around the entire perimeter of your quilt. Cutting the ends of the strips at a 45 degree angle and joining them this way (see photos and comments in photos) will reduce the lump that might otherwise form where the strips are joined together.
- Fold the binding strip in half lengthwise and iron. The folded edge creates a neat finish.
- Sew the raw edge of the binding strip to the raw edge of the front of the quilt, pinning or clipping first, and folding at the corners to create mitred corners. See photos. I find Wonder clips very useful to hold the binding to the quilt but use pins if you don't have clips.
- Fold the binding over to the back, and sew the binding to the back of the quilt by hand, taking care to make the mitred corners neat. Detailed instructions for making and attaching binding in this way can be found at https://www.craftsy.com/blog/2014/09/how-to-bind-q...
Step 11: Display and Enjoy!
Insert a rod (a dowel, a curtain rod, or a piece of wood will work) into the hanging sleeve and hang up your quilt.
The second photo shows a headboard which I made using the same technique, but using larger squares and a simple red and white colour scheme.
I look forward to seeing the creations you can make using this technique!
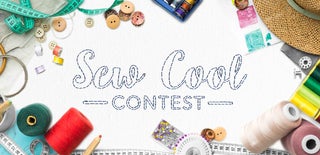
Participated in the
Sew Cool Contest