Introduction: Laser Cut Stormsword
Before we begin, I want to let you know that this build was a prototype, and some of the methods and techniques I used resulted in some unforeseen consequences. I will be including those steps as well so that you won't repeat my happy accidents unless you just want to.
Things you'll need:
Laser cutter with 700x500mm work bed or larger
Drill press or hand drill
Forstner bits
Rotary tool with engraving bit
Adobe Illustrator/CorelDraw/similar
Some experience using the aforementioned
1/4" plywood. I think I used oak plywood from Lowes in a 2x4 foot sheet.
1/4" acrylic sheet
1 button cell powered mini LED string lights (Joann's, floral/wedding section)
Aluminum foil
Liquid super glue (I used Loctite)
12x #6 1.25" brass machine screws
11x #6 .75" brass machine screws
23x #6 brass nuts
Sandpaper, 400-600 grit
Wood sealant
Metallic spray paint
Square of soft leather large enough to wrap the sword grip
3 snap sets and setter
Optional: Acetone (nail polish remover) and alcohol ink dyes (Tim Holtz section, Hobby Lobby)
Step 1: Laser Prep
For these builds you have to think in terms of layers building a 3 dimensional object. The pommel and crossguard are the thickest parts and will have 5 layers of wood. The handle will house the battery pack for the lights and be 3 layers thick, and the acrylic will be sandwiched between the spine.
Firstly, I set my canvas in Illustrator to the size of my laser bed. This ensures my design will be to scale and not overflow the bed or the cutting material.
In Illustrator, my black lines are set to stroke, not fill, with a stroke weight of 1 point. Red lines for the runes are set to stroke with a weight of .25 point. I am using the CMYK color palette, although some laser cutter software requires the use of RGB and will not import the design otherwise.
If you're making your own design, the easiest way to have all layers line up properly is to copy and paste the base pattern and then delete the lines out that you don't need. When making the blade, you can use the sword spine similarly to make sure the screw holes line up. If your pattern is a symmetrical design like mine, you can design one half of the pattern, then copy, paste, and invert it, then line it up to the other half.
My laser uses vector lines for cut lines. I can make the lines different colors and they will have editable cut properties in my laser software. For this build, I set black lines for complete cut through and red for partial cut through.
I find I get better cuts if I set my laser for a higher cut speed with multiple passes. This helps minimize charring to the wood and the possibility of fire. In RDWorks (my laser software) I can set multiple passes by importing the file multiple times. In this case I imported the design 4 times for 4 passes. My laser is 50 watts so I set my cut speed to 9mm/sec at full power for the black lines, and 200mm/sec at full power for the red lines (rune engravings). Some pieces did not cut all the way through even with this, so in retrospect, I might have done better with 5 passes at 10mm/sec and full power.
MISTAKE DURING THIS STEP: The lightning design on the blade was done by importing a black and white lightning strike jpeg and superimposing it over the blade in RDWorks. I don't recommend this, as the image became pixelated and just looked generally bad on the acrylic. I went back over it with an engraving bit in my dremel to smooth things out.
Step 2: Wood Prep
At this point both my wooden parts and acrylic blade were cut out and ready for prep.
I sanded the edges of the wood pieces to get rid of most of the carbon and smooth the edges a bit. If you're wanting to round out the edges, it's important to only round off the outermost, outward facing edges so you don't have weird gaps in your layers.
Then I applied a sealer to all outward facing pieces and every edge on every piece. The sealer pictured in actually gloss top coat for leather. It seemed to work ok. I needed something I could use indoors that would dry quickly, and this fit the bill. the purpose was to fill some of the wood grain in so it's not so apparent after the metallic paint is applied.
After that, a couple layers of metallic spray paint, being careful to cover the edges well. Yes, that's my patio table. It's wonderful for this sort of work, and I can always paint it black again after, lol.
Then I used my drill press and Forstner bits to cut recessed holes for my screws and nuts. Forstner bits are made specifically to give a flat bottomed recessed hole without cutting all the way through your material. I eyeballed the depth of these cuts, but in retrospect I might have done better to set my depth to 1/8 inches on my drill press for a more uniform appearance. These cuts are necessary because your screws won't be long enough to get purchase on the respective nuts and hold your piece together.
MISTAKE: I should have only made these cuts on the nut side of the piece, not on both sides. my finished piece has screw shafts sticking out all along the back now, which can get caught on stuff or scratch stuff unintentionally. Future iterations will only have the countersink cuts on the nut side.
Step 3: Blade Prep
Here is where much experimentation and lamentation took place. I wanted to frost the edges of the blade a bit, and I had read that acetone would do this. Brushing it on seemed to have no effect, so I made an impromptu bath and set the blade on its edge in the acetone. It didn't really fog the blade like I had expected, but it did produce a rather cool looking series of cracks all down the edge (see closeup). Which was great until i picked it up and had part of it snap off in my hand. Some of the other cracked areas had peeled away from the body of the blade as well. I won't be doing that again. Some fine grit sandpaper will cloud the blade just fine without compromising its structural integrity.
My waifu used some of her alcohol ink to make the blue cloud pattern on the blade.
After that had dried, I went over the lightning etching with my rotary tool and engraved it better and smoothed it out. This helped it catch the light much better.
Step 4: Lighting and Partial Assembly
Unfortunately I didn't take a picture of the process of actually setting the lights in the channel of the blade, but honestly it's a very simple process. You just jam the string of lights in so they all fit and are relatively evenly spaced. If you don't plan on removing them, you can glue them in the blade channel.
It's important to note that the power switch needs to be facing down and out of the pommel to reach it. The wire also face down and out, so you have to route it around the side of the battery pack and into the channel in the handle. It's a tight fit but it will fit.
I did notice upon an initial assembly of the pieces that the lights weren't glowing very brightly, so I had the idea of using some aluminum foil on the inside back of each spine as reflectors. This was a very good idea. I glued the aluminum foil in place and trimmed the excess.
This part is optional, but it will keep your whole piece from falling apart when it comes time to change the batteries: If you look at the 3rd picture you will see what is essentially the battery cover portion of the handle above the rest of the piece. I put some screws in to keep the alignment true, then dabbed a couple drops of glue between the layers of the crossguard and pommel and pressed them together until they set. I did the same thing with the rest of the piece - glued the outer layer of the cross guard and pommel to the next layer under it, and then glued the battery housing pieces in side the handle.
As a matter of personal preference, you can also glue the blade to the spine on this side if you don't plan on needing to take it out in the future.
After this, I threaded all my screws and nuts together. the .75 inch screws go into the blade spine and the 1.25 inch screws go through the crossguard and pommel.
Step 5: Handle Wrap
The best way to do this is to use a tailor's tape measure and wrap it around the handle. Take that measurement and add roughly a half to 3/4 inch. Then measure the length of the grip. Cut out the leather, punch 3 holes. and set your snaps.
MISTAKE: Uhhh, make sure the snap tops and bottoms are oriented properly before setting them. The snap bottoms should have their business ends facing out of the grain (outward) side of the leather, and the tops should have their business ends facing out of the flesh (inner) side of the leather. Double check this, because they are exceedingly difficult to remove once set. Your piece will look like the second photo in this step if correct.
Alternatively, one might try using lacing instead of snaps. I used snaps for easy access to the battery housing.
Step 6: LOOT AND PILLAGE
If everything has gone according to plan, you may now go forth and conquer!
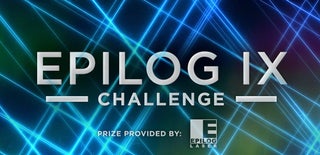
Participated in the
Epilog Challenge 9