Introduction: Laser-cut Pinwheels
So the makerspace I run for the City of Auburn, WA is open for the 4th of July as a part of a huge celebration in the park next door, and I needed a fast and inexpensive kids' project that would show off the laser. I love laser-cutting paper, and I thought what's more festive for the 4th than making pinwheels? The cost of these is probably less than $.25/per, depending on what materials you use. My own files are included below!
Step 1: Materials
Laser cutter
Cardstock/crafting paper, basically anything heavier than printer paper (any size, just scale the template accordingly)
A thumbtack, seed beads + hammer
1/8" baltic birch (at least 1.5 x 12", scraps work well)
This is a recipe for what I found works; see the end of this tutorial for discussion on what DIDN'T work from the suggestions I found online.
Step 2: Design
The design for a pinwheel is very straightforward. The only things you might want to consider are your choice of colors for paper, beads, and pins. Paper will ideally be colored on both sides, so the white doesn't show. Also keep in mind that the smoke will stain whatever side of the paper you lay face down, so if one side is darker than the other, it's better to put that one face down.
For the handles, I customized them with a graphic promoting our 4th of July event, so it's a nice keepsake. Other customization could be adding specific peoples' names, drawing candy-stripes, adding a celebratory pattern, etc.
Baltic birch takes very well to being painted or colored with sharpies, so your audience can customize them in that way (or you can pre-paint them whatever colors you like). You can also have folks color on the sheets before laser-cutting them--making pinwheels can actually be a fun way to repurpose old drawings, magazine covers, that sort of thing.
This template can also be used to quickly make decorations like garlands and such; if that's your plan, then I recommend using a brass brad instead of a pin to hold it together. In that instance, you would resize the teeny holes drawn on my template to a 1/8" (.125") diameter. You can also resize this template, but make sure that you don't resize the pin holes as well; those will have to be rearranged.
Step 3: Cut!
My laser is a 50 Watt Epilog Helix. I cut using a speed of 100 and power of 30, 500 frequency top cut the paper.
I cut the handles with a speed of 25 and a power of 100.
The purpose of this instructable is not to cover laser-cutting basics, but I will say things to keep in mind when cutting paper:
1. lower power and more passes is better; if you have thicker paper that doesn't cut in one pass consider either pulling it out (if it's perforated but just stuck in a few places) or running it again. If you raise the power, you'll create more smoke, which will stain your paper.
2. the air assist on the Epilog can make your paper flutter and either mess with the focus or, worst case, get caught up in the x-axis assembly and start to burn. Watch it closely, consider using weights where you can, and/or use the side clamps on the machine. You CAN turn the air assist off, but I don't recommend it, since paper is highly flammable.
3. it's not practical to cut more than 2 pieces of lightweight cardstock, one on top of the other, simultaneously, because even if you power the laser up the only way you can reach the bottom of the stack is by charring the top. You're better off running more batches.
4. for an 18x24" bed, I arrange 4 pieces of 8.5x11" paper (or 4 stacks of 2, for a total of 8) at the 4 corners of the cutting bed. This gives me the maximum cuts per batch, while also allowing my files to have good margins, no paper overlap (which can lead to underpowered cuts), and more predictable alignment (so I don't accidentally cut outside the bounds of a piece of paper).
Step 4: Assemble
Your pieces should now be as follows:
1 laser-cut baltic birch handle
1 laser-cut spacer
1 glass seed bead
1 thumbtack
1 laser-cut paper template
The only tool you will need is a hammer. You can also use a wood clamp that you ratchet shut to fasten your pieces, since the 'pilot holes' have already been lasered into your pieces.
First, assemble the wheel. Hold your paper template burnt side up and grab one corner with a hole cut through it. Fold the corner towards the middle without creasing the paper. Stick the thumbtack in from the clean side, to the burnt side.
Grab the next corner with a hole poked in it, fold it towards the middle, align the hole with the pin the same way, sticking the pin from the clean, to the burnt side.
Attach the next two corners in the same way, so 4 corners are folded towards the middle and their opposite corners are sticking outwards.
Stick the pin through the hole in the center of the square of paper. On the backside, thread the seed bead onto the pin. This is necessary to give the fins some space from the handle to move freely.
Line the pin up with the hole in the tip of the handle, and push it firmly.
Set the spacer directly underneath the tip of the handle on a flat surface and give it a couple of good whacks with the hammer. The sound will change when it's all the way in.
The pin should not be sticking out the back; if it is, twist the push pin to pull it back out again to give it some freedom of movement. Adjust more if the wheel doesn't spin freely when blown on, at this point!
Step 5: How to Explain the Laser to an Audience
Here's a quick tip for explaining the laser to kids (or adults): Analogies!
-the laser uses UV light, which is just like what gives us sunburns from sunlight, but we're burning the paper/wood/whatever instead.
-the x-axis assembly has a little magnifying glass, which focuses the laser just like we can use a magnifying glass in the sunlight to fry ants on the sidewalk.
-the air assist blows out the flames just as soon as we can start them, just like you blow out your birthday candles.
-just like a magnifying glass won't burn if it's too far away OR too close, the auto-focus keeps the laser at just the right distance.
I usually explain this while the kids are all hypnotized by watching the laser cut :) Even if they don't learn much, maybe it will stick in their brain a little!
Step 6: Process, or the Mistakes Along the Way!
I honestly thought this would be a fun, hour-long project. How hard could it be??? Well friends, the internet led me astray.
First of all, don't trust anything that says you can use brass brads. That's fine for decorative pinwheels, but they won't spin! There's too much friction with the edges of the brads and the paper. I included the design I made in case you're looking for something more decorative.
Second, don't use a straw for a handle! It doesn't hold the metal of the pin, especially with heavier paper, which has enough rebound to it to send the pin and bead soaring across the room! Which is a great way to lose an eye.
Third, dowels are for chumps. You have to cut them to length AND sand off splinters, they're ROUND so the pin glances off them when you strike it OR you have to pre-drill them...which is all to say, I have a laser, so no.
A few other experimental failures:
-printer paper cuts fine, but is too flimsy--it tears, bends, flops, and gets caught on the handle.
-I found a template for decorate pinwheels where each individual fin is cut and then added together...again, fine for decoration but lacks functionality.
-Also, I tried to laser-cut a little spacer to use instead of a seed bead (because, again, I HAVE A LASER, why would I use a bead if I can avoid it???), but it had too much friction--it spaces well, but the glass beads also allow it to spin more freely.
-Finally, I found a recommendation for using a section of pipe cleaner instead of a pin for the center, which again is fine for a mostly decorative pinwheel instead of a functional toy, but I can't imagine that it would spin freely just by blowing with that much friction after my experience.
All in all, it took me over 3 hours of experimentation as a pretty decent designer, working from one of the SIMPLEST POSSIBLE INVENTIONS, to make this sucker. Hope you have fun with it!
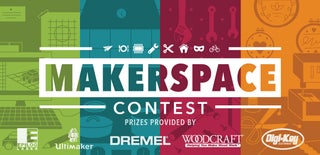
Participated in the
Makerspace Contest 2017