Introduction: Lasercut Crane W. Automatic Hydraulics
Welcome to our instructable.
We will show you how to build your own hydraulic crane and how to make it automatic.
We supply you with the original 3D-files (for SolidWorks), to give you as much freedom as possible, when it comes to the design.
Step 1: Stuff You'll Need
For the hydraulic crane without automation, you will need the following items/materials (the automation will be covered in step 8):
Tools/machines:
- 1 Laser cutter
- 1 scissor
- 1 hand drill
- 1 drill (matching the thickness of the string or cable tie)
- 1 glue gun (or similar, as long as it is fast drying and relatively strong)
Materials:
- 1 sheet of MDF 600x600x6mm
- 1 syringe, (no needle) 12ml
- 1 syringe, (no needle) 20ml
- 1 piece of 6mm rubber/soft plastic tube, (or whatever fits your syringe), approx. length 200mm
- 1 piece of string or a cable tie (for attaching the syringe to the boom)
Step 2: Cut Your Parts
If your lasercutter understands Illustrator-files, our file has partnumbers, that you should make sure will be engraved and not cut, unless, of course, you want them to.
If your lasercutter does not understand ai-files, you have to use the original 3D-files to convert the patterns to whatever program you are using.
Attachments
Step 3: Assembling the Bottom With the Pedestal
These parts are used to fixate each other. You start by aligning the rectangular holes of the two bottom parts (G1-G2), with eachother, with G2 on top. Then you push the pedestal parts through the holes, as shown in the first picture. Then you simply push G1 into place, so that the outer contours of the parts are aligned.
Next, you mount the feet (F-series) on the bottom. You do this by pushing the feet through the holes of the G-parts and twisting them, while the axis of the feet are in the center of the rectangular holes, as shown.
Step 4: Placing the Cylinder Platform
The cylinder platform (part B), is placed by using the same method that you used with the feet. You push it in and twist it in the circular hole, making sure that the small hole in part B is facing into the crane.
Step 5: Assembling the Beam
To assemble the beam, you align the parts (D-series) and push and twist the E-part through the key-hole, as you did with the feet.
Step 6: Assembling the Beam With the Pedestal
You use the two small C-series parts as the axis of rotation, for the beam.
You just assemble them so they make up a cross and then push it through the cross-shaped hole in the pedestal, through the circular hole in the beam and into the other cross-shaped hole in the other pedestal part, aligning it with the sides of the pedestal.
If you want to, you can use glue to fixate the C-part, however this will make it hard to disassemble.
Step 7: Making the Hydraulics
To make the hydraulics, you put the hose through the hole in the B-part and glue the hose firmly to the syringes, with the smaller syringe to be used for the actual lifting of the beam. You won't be able to put the hose through the B-part later, so this is extremely important.
When this is done, you remove the piston from the small syringe, drill a hole in it, as you can see in the picture, and fill the hose and larger syringe with water, making sure that there is no air in the system, before you put the piston back into the small syringe.
Now simply strap the piston on the smaller syringe on to the beam and you are good to go.
Step 8: Adding the Automation
When we were struggling to make the automation function, we started out with a smaller motor (12VDC) that just didn't deliver enough torque. This meant that we needed either more power or bigger gears. We didn't have bigger gears, but we did have a "slightly" bigger motor.
To control the speed of the motor, we needed some rather powerful resistors that we didn't have. Therefore we used a couple of H4 headlights.
To control the rotation, we used a 2-way-switch.
To transmit the power from the motor to the syringe, we used a linear gear from LEGO.
The power supply is a simple 18V, 1.1Ah battery from a hand drill.
For the actual construction, we just used what we could find, which in this case is a 6 mm HPV sheet, for the base and some pieces of 10 mm acrylic sheet to adjust the spacing between the syring and the motor. The parts are just boltet on, except for the syringe, which is glued into place.
The parts available to you, will most likely have different dimensions and therefore you will need a different setup.
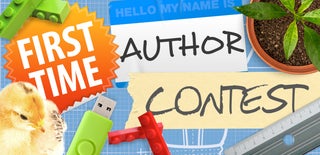
Participated in the
First Time Author Contest