Introduction: Leather Stitching Pony and Avoiding the Costanza Wallet
This entire build, and my interest in leather working all comes from my desire to never carry a Costanza Wallet. I can honestly say that this is my favorite leather-working tool and it has become the greatest "3rd hand" I own.
A little back story: April 18th, 2009 - I was visiting some friends in Oakland, CA and we went out for a day of walking the town. We stopped in a pop-up shop and at that moment, my life changed for the better. I found the perfect wallet. It was a bi-fold wallet with 2 simple compartments and a small piece of elastic that held the folds together. It was near impossible to fit more than 2 cards and a couple of bills in each compartment and for me, that was perfect. Fast forward a year or so and the wallet began to fail. The elastic was stretched to the point where it would no longer secure my belongings and the stitching was failing. Unfortunately, being a pop-up shop, I could not find the company who produced the wallet and therefore was forced to either move on to another style of wallet or learn to make my own wallets. (I chose the latter.)
I had been lucky enough to receive my grandfather's old leather tool kit many years before and decided the simplicity of the wallet was a perfect beginners project. After years of stitching leather together with the pieces between my knees, I upgraded to using some soft jaws on a small bench vice. This was fine except that I really had no room under the clamp jaws for excess material. After years of using the bench vice method, I began to start making my own leather pouches, bags, and tool rolls and thought, there must be something better than this inefficient bench vice. That's when I stumbled upon this Instructable by The Rambler and I decided I needed to make a dedicated leather camping device - So I did. I made a few small adjustments to The Rambler's Instructable but it was so simple and well-built that I used my prototype for years, abusing the hell out of it (notice the scorch marks) with each project.
I do not remember what I saw the other day but whatever it was, it instantly made me think of improvements I could make to my original leather stitching pony. This is not a new style as I found a few versions close to mine on Amazon after-the-fact, but I've made a few changes that bring in the best parts of my original design and these new concepts.
The original prototype version only had one adjustable arm, making for poor storage when not in use. The base was also fixed, not allowing for different angles or clamping configurations. The new version allows for adjustable positions and the ability to fold up completely for storage or transportation.
Step 1: Materials and Tools
Here is a list of the materials and tools I used to create and assemble my leather stitching pony.
Materials:
1 @ 1"x4"x6 foot long popular project board from a Big Box Store.
1 @ 4"x5" scrap 1/4" piece of plywood.
At least 12"x4" of leather to use as leather padding on the jaws.
1 @ Cam Clamp (I purchased a 2 pack at my local Rockler store)
1@ 5/16" T-Nut
1 @ 3" Hinge
2 @ 3/8"x5" Carriage Bolt (Trimmed to 4.5")
1 @ 3/8"x1 1/2" Hex Bolt
1 Handle Bolt (Found at Big Box Store in Lawn and Garden department. Often used for tightening handles on a push mower.)
Random Washers.
Tools: (I believe you could do most of this with non-power tools.)
Miter Saw
Drill Press
Disc Sander
5/16" and 3/8" Drill Bits
7/8" Paddle Bit
Socket Wrench with 1/2' socket
Clamps
Glue
5 Minute Epoxy
Spray Adhesive
Xacto Knife or other leather cutting tool
Painters Tape
Spray Sealer
Step 2: Prepping the Pieces of Wood
We will be working on 4 distinct pieces for our Stitching Pony. We will have the Base, a Pivot Block, a Stationary Stitching Arm, and an Adjustable Stitching Arm.
We will first rough cut our pieces of wood for assembly. You will need 3 pieces at 16 inches long (Base and both Stitching Arms) and 4 pieces at roughly 5 inches long (2 for the Stitching Arms and 2 for the Pivot Block). We will take 2 of the 5 inch pieces and put a 45 degree miter on one end of each. This will allow for clearance at the inside bottom of the Stitching Arms.
Measure in 1 3/4 inches from the sides and top of one of the remaining 5 inches pieces and use a compass to create a round end on one side of the piece. After these pieces are glued together, we will end up cutting and sanding that end to help form the Pivot Arm.
Step 3: Working on the Pivot Block
We will glue and clamp 2 of the 5 inches pieces together (pieces without mitered ends), sandwiching the 1/4 inch plywood between the pieces. Since we will be adding leather padding to the ends of the Stitching Arms, this 1/4 inch piece will serve as a spacer to allow our arms to run parallel when clamped together. Once the glue has dried, we will use a disc sander to smooth all of the edges of this piece of wood.
(It was at this point that I thought the 5 inch tall pivot block was a bit much and I ended up cutting it down to a height of 4 inches.
Since all of the edges are flush and have been sanded, we will take this opportunity to draw lines on the bottom of the Pivot Block, connecting the opposing corners to find center. The hole we are about to make will house a T-Nut that allows the base to screw to the Pivot Block. After finding center on the bottom of the block, we will use the 7/8 inch paddle bit to drill a shallow recess which will hold the top of the T-Nut under the surface of the wood block. We then will follow our paddle bit with a 5/16 inch drill bit to hollow out the remaining hole so the the T-Nut will fit fully inside the block. (It is a good idea to allow some extra depth with this hole for any extra bolt length you may have when attaching the base to the Pivot Block.) You can now add the T-Nut to this hole. I suggest adding a little 5 minute epoxy between the T-Nut and Pivot Block to ensure the T-Nut remains fully secured.
We will then take our Pivot Block to the miter saw and remove excess stock, bringing us closer to our circular line. Once cut, we can take our block to the disc sander and remove the remaining stock right to our line, leaving us a circular top.
We can use the drill press and a 3/8 inch drill bit to punch a hole through the Pivot Block at our center compass mark. This hole will allow us to pass a bolt through the Stitching Arms and Pivot Block, locking the two together.
Step 4: Working on the Stitching Arms
We will glue and clamp the long pieces of the stitching arms to each of the mitered 5 inch pieces of wood. Place the mitered end facing the bottom inside of each arm. Once the glue is dry, take the edges of your joined pieces and run them across the disc sander to smooth the edges of your Stitching Arms.
Once sanded, mark a 45 degree angle on the outside top of each of the Stitching Arms. This will give you easier access to your work once it is clamped into your Stitching Pony. You will notice that I left a 1/4 inch flat on the inside top of each Stitching Arm. I like to think this gives you a little extra strength at the top of your Stitching Arm when working with your pieces and allows for a more gradual rounding to the leather padding pieces when installed. While I think this cut would be made better on a table saw, I do not have access to a table saw in my garage workshop so I opted to clamp the Stitching Arm securely to my miter saw and make the cut. After cutting these miters, I took the piece back to the disc sander to smooth the edges of my previous cut.
(The images may show a few steps out of order but follow what I say and not what I've shown.)
Take one of your Stitching Arms and make a mark 4 inches from the bottom of the Stitching Arm. Using your miter saw, make a cut through the arm at this point. This cut will eventually be joined by the hinge, allowing you to open and close one of your Stitching Arms. You'll see that I sanded a small bevel on the outside of that previous cut so the pin of the hinge will sit flat on the Stitching Arms. Clamp your two recently cut pieces together tightly and layout your hinge and holes positions so you can drill them out. You can now assemble the Adjustable Stitching Arm.
I do not have pictures of what I am about to do next but my explanation should make sense. Seeing as you removed some material from your Adjustable Stitching Arm when cutting it in half, you will need to align both your Adjustable and Stationary Arms at the top and cut the Stationary Arm down to the same length as your assembled Adjustable Stitching Arm. Once cut, mark the bottom of each Stitching Arm 1 3/4 inches from the sides and 1 3/4 inches from the bottom, creating a center mark at the bottom of each Stitching Arm. Using a 3/8 inch drill bit at the drill press, drill out these holes on each of the Stitching Arms. Then make a 45 degree miter on each of the bottom corners of the Stitching Arm, 3/4 of an inch from the edges (You can see these cuts in the above images.). This will give the Stitching Arms enough room to pivot on the bolt and Pivot Arm without hitting the Base.
You will then measure up 8 inches from the bottom of each arm and 1 3/4 inches from each side, mark and drill another 3/8 inch hole for the cam clamp. This will allow you to open and close your Stitching Arms, securing your pieces for work.
Step 5: Working on the Base
The Base is likely the easiest piece to work on but you will need to make a few key measurements. On the bottom side of your Base, mark 1 3/4 inch from each side and 1 3/4 inch from each end. You will also make a mark 8 inches from each end and 1 3/4 inch from the sides to create a spot for a center hole. These hole positions allow you to move the Stitching Arms to the ends for a more compact storage solution and also hold the Stitching Arms in the center of the Base for clamping to a work table or placing between your legs when working from a chair.
You'll want to take the 7/8 inch paddle bit and drill a hole deep enough in each of these locations so the hex bolt you use to attach the Pivot Block to the Base will sit below the surface of the Base. In my case, this ended up being a little over 3/8 inch deep, accounting for the hex head and a washer. Then with a back board under your Base, use a 3/8 inch drill bit on the drill press to finish the holes all of the way through the Base.
Using your 1 1/2 inch Hex Bolt with a washer, you can attach the Base to the T-Nut in the Pivot Arm to make sure everything lines up.
Step 6: Putting Finish on Your Leather Stitching Pony
Give all surfaces and edges a light sanding to break the edges and smooth out the wood before sealing. I was going to put a heavy duty finish on the pieces but opted for a few quick coats of Rust-oleum Clear Finish. This allowed for a quicker drying time and I already had some on hand.
The first thing we will want to do is remove all of the hardware from your pieces. This includes any bolts and the hinge. You'll want to cut a small tape circle to place over the hole of the T-Nut at the bottom of the Pivot Arm and place some painters tape over the top and inside areas of the Stitching Arms where we will be adding our leather padding. This will make sure we do not accidentally place sealer on the surface we plan to hit with spray adhesive later.
If you have painters blocks, I suggest placing all of your pieces on those and hitting each surface with a few coats of spray sealer. The more the merrier but I think I stopped after the 3rd coat dried.
Step 7: Adding Leather Padding to Your Stitching Arms
After your finish dries, remove the tape and tape your edges again so you are protecting your recent finish, exposing the areas you will want to attach the leather padding. You will also want to clean and prep the back of your leather scraps, cutting them a little larger than the size of your Stitching Arm pads. We will come back and trim this with an Xacto knife later.
Add a coat of spray adhesive to the back of your leather padding and to the exposed wood of your Stitching Arms, giving the piece 5 minutes to tack up. (I've always heard you will get a better bond if you add a second coat of spray adhesive but I seemed to get an acceptable bond doing only one layer of adhesive on both parts.
After the 5 minutes have elapsed, carefully take your Stitching Arms and place them down to the leather, wrapping around the edges and leaving some exposed leather on all sides. Then use an Xacto knife or other cutting tool to trim the edges of the leather flush to your Stitching Arms.
Step 8: Assembling Your Leather Stitching Pony and Some Final Thoughts.
Everything should be done and you are ready to assemble your Leather Stitching Pony - YAY! Run the 1 1/2 inch Hex Bolt and a washer though the bottom of the Base and into the Pivot Block. The Pivot Block can be rotated in any direction and placed in any hole, giving you adjustability over the previous fixed prototype version. This nut can be tightened with a 1/2 inch socket wrench.
You can now place and tighten your hinge screws, connecting the pieces of your Adjustable Stitching Arm. Using one of the 4 1/2 inch carriage bolts, a washer and your Handle Bolt, attach your Stitching Arms to the outside of the Pivot Block, tightening the Handle Bolt until the arm is at the angle that best suits your needs.
Using the other 4 1/2 inch carriage bolt, a few washers, and your cam clamp, place the assembly between the arms of your clamp. The cam clamp allows you to quickly loosen or tighten your Stitching Arms, pivoting the Adjustable Stitching Arm at the hinge.
Final Thoughts
It's already 100 times better than the previous version. There are still a few problematic areas that some clever engineering could solve. Mainly, when working on a large runs of leather stitching, the excess thread can get wrapped around the cam clamp or handle bolt. Basically, anything that sticks out from the side can cause issue if you are not careful. I've been working so much with my previous version that utilized the cam clamp that avoiding these catch-points comes naturally to me. Just be aware before you go making hard pulls on your thread. You'll also see that I had some decorative tacks on the leather padding in the prototype version. I thought I might need them for extra support of the leather but they ended up just catching thread as I was sewing. I feel the spray adhesive will hold well enough without the tacks.
That's about it and I hope you've enjoyed this Instructable. If you have any questions, please feel free to ask and I'll be happy to clear anything up or take some more precise measurements. Heck, I'll probably be designing version 3.0 at that point.
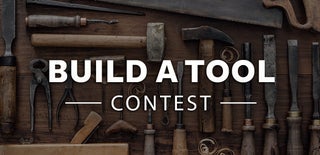
Participated in the
Build a Tool Contest