Introduction: Led Bulb
This is a led bulb that i made from a broken CFL bulb and some Leds that i had laying around.
I already made 2 led bulbs. The one on the left is 1 watt and the one on the right is the 3 watt which im showing you now.
These bulbs are for 120v mains.
(RISK OF ELECTROCUTION. MAKE THIS BULB, IF YOU KNOW WHAT YOU ARE DOING! )
Do not touch the output when open or closed circuit, it is still referenced to MAINS!
IF U GET ELECTROCUTED OR HARMED MAKING THIS, I AM NOT LIABLE, DO IT AT YOUR OWN RISK!
Step 1: Parts Needed.
1) 1-dead or new CFL bulb
2)4-470k ohm resistors
3) 1-120ohm resistor(may be in the CFL bulb)
4) one 200-400nf capacitor(will be in the CFL bulb)
5) 2-330nf capacitor (i used it because, the current output wasnt enough)
6) Any polarized capacitor from the CFL light bulb for DC smoothing ( You should use a 100-200uf capacitor)
7) 4-diodes (from the CFL bulb)
8) perf board
9) copper PCB board
10)5050 led chips( i had them laying around, but u can you use any leds but you have to change the total capacitance of the group of capacitors to limit more or less current) use this website to calculate the resistance from the capacitor value--------http://www.66pacific.com/calculators/xc_calc.asp
And use this website to calculate the the current that it will limit, use the middle calculator----http://www.digikey.ca/en/resources/conversion-calc...\
(Also if you want to use these bulbs for 240v, use the calcuators above to find the appropriate non-polarized capacitors needed)
Step 2: Taking Apart the CFL Bulb
First i used a hacksaw to saw around the plastic casing( the top seam of the plastic base), opening up and out the important electronic components. (be very careful when sawing it apart, trying not to crack the cfl glass bulb which has mercury in it)
I soldered out 4 diodes, the polarized capacitors, and non polarized capacitors.
Step 3: Creating the Led Driver Board
Start cutting out a larger piece of perf board that fits inside of the CFL housing and start creating and soldering in resistors, capacitors, diodes, in the circuit above which look like this.
The diodes should be wired in the orientation above.
The non polarized capacitors should be all wired in parallel to get the correct total capacitance of 1uF, but capacitance can be larger for larger Leds.
Step 4: Making the Led Board
I used 5050 led chips, so they are surface mounted so i needed a PCB board, but i couldn't etch the copper board with any chemicals, since i didn't have any chemicals, nor the tools to make the board.
So i etched the board using the DIY way, by creating the board by drawing the board out with marker (my Leds are all wired in series), then covering the parts i wanted in aluminum tape. Then creating an etching solution of 1 part vinegar and 1 part hydrogen peroxide. I let the board sit in the solution for 12 hours, overnight.
After 12 hours it looked like this and i cleaned off the aluminum pieces and the etching solution and i was left with a cup of blue liquid and cleanly etched circuit board.
(you can wire as many Leds in series as long that the total voltage of the Leds isn't more than the supplied mains voltage of 170v (after rectification, 120v before).
Step 5: Nearly Done!
After the driver board was finished, i soldered it to the CFL edison screw base and sealed the board in the base with hot glue with 2 wire pertruding from the case.
Then after the tiring work soldering in the 5050 chips, i was finalling able to put in all together and testing it out.
(near finished soldering of the LEDs above)
Step 6: Finished!
Since everything worked, i glued the led board on the the lamp base, with a piece of cardboard separating the CFL base from the Led board.
And now it puts out 3 watts of light which is enough to light my kitchen table brightly.
Don't touch the face of the led board when the light is on, or you can get a used,clean and translucent plastic container to cover the led board and diffuse the light, preventing electrocution.
RISK OF ELECTROCUTION IF YOU DON'T PUT A COVER OVER THE LED BOARD!
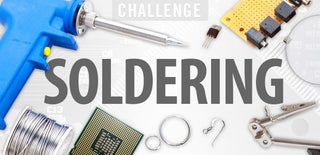
Participated in the
Soldering Challenge