Introduction: Lighting Up the Radial Arm Saw
While trying to better organize my shop, I decided to make a new table for the radial arm saw I got cheap. It's far more powerful than my portable tablesaw, so it has become a necessary thing to have it in good operating condition.
While checking all the adjustments carefully, I realized that there was a ridiculous shadow cast by the arm, and that it made marks and measurements hard to see. I looked through my scraps and found this old aluminum angle. Grabbed some leftover LED strip, a power supply, and got to planning. A few hours later, This is the result. A saw that I can see under! It's tempting now to add line lasers to each lamp so there is a visual barrier on the tabletop.
One massive benefit is the lights are self adjusting.. You rotate the arm, The lights go too. No more moving lights around just because I want to cut a compound angle.
Please vote for me in the lighting contest! Not going to lie... A laser cutter would be amazing to have!
Step 1: Gather Your Stuff.
It's 1 AM, I'll try not to miss anything.
1:Brackets. Mine are shopmade, but commercially available brackets will do well.
2: Drill bit and tap. I used a 10-24 NF with a 5/32 drill bit. Use what suits you.
3:Matching screws/bolts.
4: 12 volt LED strip.
5: 2 Pieces of aluminum Angle the length you like. In this case 9 3/4 inches didn't interfere with anything.
6:Soldering iron, solder, and flux.
7: Glue of some kind. I do not trust the adhesive on the LED strips.
8: Heat shrink.
9: 2 strand wire of the appropriate length.
10: Conduit of some kind to run the wire in and make everything look neat. I used PET tubing and a Vacuum "T"
11: a plan.
12: Thread locker of some kind. I chose removable, since I may wish to remove/modify these down the road.
Step 2: Mark, Drill, Tap, Repeat.
Mark your hole centers carefully. You'll only get one shot to make this look good, so you really need to plan carefully.
Drill the holes. 5/32 gives me about 62% thread depth. A smaller size would be better since the aluminum might be soft. However, I'm a machinist, and confidence in my abilities made me comfortable with 62%. When drilling freehand, short bursts of drilling yield better, more consistent results. be careful that there is no wiring in the way inside the casting!
Tap the holes. Freehand tapping can be hard to get right. If you are not confident, then use a block of wood with a hole the same size as the tap drilled through it on the drill press. screw the tap through the wood and into the casting, and you should get a nice straight hole with good threads.
Mount the brackets. A little thread locker will prevent the screws from vibrating loose.
Step 3: Prep the Lights.
Strip the coating from the LED pads and prepare them with flux and a blob of solder.
Solder wires in place
Heat shrink over the wires being careful not to cover any of the LEDs
Rubber cement is my glue of choice, I coated the back of the lights, AND the aluminum angle. In hindsight, It didn't hold that well because I neglected to clean the angle.
Feed wire through the PET (Or whatever your conduit choice is) and heashrink it in place.
Join your wires and solder the junction to a longer wire to connect to your power supply.
Solder to power supply after being certain your polarity is correct.
Step 4: Installation.
Mount your aluminum angle onto your pre-mounted brackets. I used 1/4-20 bolts and nuts to hold mine. With a bit of threadlocker of course.
Run a bead of hot glue along each edge and around each end of the LED strip. Assuring it will not move. (Clean your aluminum! )
Feed wires into "T" and glue PET tubing in place on top of the saw arm.
Hot glue "T" fitting in place.
Hot glue PET tubing in a few more places and route along top to point you think won't interfere with anything. If you haven't done so already, Solder the power supply on and heatshrink the connections.
Step 5: You're Done!
This project took me a couple of hours.
I made a plan and stuck to it. The result is pleasing, and very useful.
There are no shadows where the blade will be, and there's more light on the measurements on the arm.
I like the PET tubing and am happy I went with it. But corrugated tubing, and wire sleeving would also look nice.
I could very easily run the wires through the casting, and might do that. For now, I want to get the saw back in operation and get back to woodworking.
Yes. I know that radial arm saws are dangerous. I am aware of the "recall". I don't have the money to buy a nice, big, tablesaw, so I have to accept the risk and use my brain while using this saw. that means proper adjustments, and being aware of my hands in relation to the blade at all times.
Thank you for viewing! Please vote for me in the lighting contest!!!
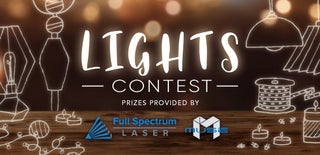
Participated in the
Lights Contest 2017