Introduction: Live Edge Cedar Industrial Computer Desk
I have always been fascinated by live edge (bark or natural edge on one or more sides) slab tables. My wife found an “L” shaped live edge cedar desk for sale on Facebook. The individual on purchases the slabs, adds IKEA table legs and finishes the top of the desk.
I liked the desk, but there were just a few things that I wanted to change…how the two pieces were joined, the design of the legs, and the finish. Ok, I just wanted the wood.
The person that built the desk had taken one slab of wood, cut it in the middle, reversed the two ends (wider root and branch ends) and joined them with two 45 degree angle cuts. This made the desk area at the joint larger, but with none of the interesting features (the crack and the grain) that flowed through from one side to the other.
Step 1: Re-configuring the Desk
One of the existing 45 degree angles was cut so that it was straight and the other angle (root end) was reformed with an ogee curve. Since the slab was too thick for any of my saws a reciprocating saw was used to make the ogee curve cut. This required a lot of work with the sander. The 90 degree joint was then recut so that the crack and grain lined up. The two slabs were joined using two Tite Joint Fasteners from Rockler. Don't bother buying the spade drill bit sold for drilling the hole. The bit is designed to center the bit in the template, but doesn't cut very well. Just use a spade or forstner bit and be careful when you center it.
Step 2: Preparing the Surface
The thickness of the desktop wasn’t consistent and I didn’t like the yellow color of the finish, so I took it to a local shop where they ran it through their giant planner and made the thickness a consistent 2.5 inches (cost less than $20). I sanded the top of the desk with several different grits of sandpaper - starting with 100 grit, 120 grit, 180 grit, and ending up with 220 grit. I experimented with several different types of finishes and settled on polyurethane because it maintained the color of the wood better than anything else. I like the satin finish rather than high gloss. Three coats were applied with a 220 grit sanding applied between each coat. I left the bark on the edges of the wood and applied the polyurethane using a spray can so that it would penetrate the cracks and crevasses.
Shortly after the slab was brought home small boring bugs started to come out of the bark. They left interesting holes and trails in the bark, but weren't too welcome in the house. I took the slabs out to the shed and set off two bug bombs. Problem solved.
Step 3: Designing the Legs
I wanted something a little bit more industrial for the legs, so I used ¾ inch black pipe. Since the desk is 13 to 15 inches wide the legs were designed with angled supports so that there would be more clearance for legs under the desk. Use of the pipe provided the opportunity to integrate electrical boxes into the frame for electrical outlets and LED power supply for the lamp and shelf lighting.
Most of the pipe was purchased online (Zoro, Ebay) and some at the local hardware store (Home Depot). Online was cheaper and they had a better selection in increments of ½ inch. Ebay was used for the one three-way fitting for the lamp.
I tried to calculate the length needed for the angles to make them even, but after assembly I had to make some adjustments with the short pipes connected to the foot flange. Felt was added to the bottom of the foot flanges so they would not scratch the floor.
Note: I found that I needed one odd length pipe and went to Home Depot to have it cut. They said that they couldn’t cut short pieces of pipe. I suggested that they use a union fitting on two pieces of pipe to make it long enough to fit in the machine. That worked and they thanked me for that idea.
Here are the design drawings for the legs. The height of the desk is 31 ½ inches. For clarification 1) the first leg is the back leg where the electrical cord enters, 2) the middle leg is at the 90 degree angle and where the lamp attaches, 3) the right leg holds up the end that has the ogee curve. Adjustments are easy to make as there are so many joints. They don’t have to be completely tight since everything is tied together and screwed into the wood. The pipes between the legs would depend on the
Two 16 inch pipes were used on the front to connect the junction box to each leg and two 18 inch pipes were used on the side.
Step 4: Electrifying the Desk
There are two junction boxes in the leg framework. Because of all the angles created by the “Tee”s the legs had to be disassembled and the wire threaded through as everything was put back together. The junction box in the front is a double back-to-back box that holds the LED power supply on one side and an outlet and switch on the other. The switch energizes the LED power supply for the lamp and shelf lighting. One of the outlets also has USB power outlets. The other junction box under the keyboard shelf has two outlets. Each junction box required 3/4 to 1/2 inch reducers on both sides of the box.
Step 5: Desk Lighting
Next an LED lamp was designed for the top of the desk. Using a grinder, slots were cut in two 12 inch pieces of ¾ inch pipe and mounted above the middle leg. Bolts through the desktop join the leg and lamp together. Initially a straight pipe coming up from the desk was used. The three-way fitting, made in China, was not square and this caused one arm of the lamp to dip lower than the other. Adding two 45 degree fittings allowed adjustments to be made to level the arms. A three-way switch (on-off-on) allows control of the lamp and the shelf lights (lamp or lamp and shelf). LED strips were hot glued to strips of wood that were cut to fit inside the tube to keep the LED strips from hanging outside the grooves. The shelf lights are LED strips hot glued in grooves routed on the bottom side of the desk.
Step 6: Framework for Keyboard Shelf and Monitor Stand
After the leg frame was built, outlets wired, and desktop mounted I realized that the desk wasn’t wide enough to accommodate a keyboard and monitor. So a ½ inch black pipe framework was designed that would support a keyboard shelf and monitor. The pipe framework was attached to the bottom of the desktop and keyboard shelf. Had I thought of this in the beginning I would have integrated this framework into the leg frame.
All the pipe was rubbed down with mineral spirits to remove the rust inhibiting oil and sprayed with satin finish polyurethane. No galvanized pipe was used.
Attachments
Step 7: Adding the Keyboard and Storage Shelves
Besides the keyboard shelf another shelf for additional storage was added. The shelves were made from live edge boards purchased at Rockler. To accommodate the legs running through the shelf holes were drilled using forstner bits. A cord and power supply storage area with hinged access was integrated into the back of the keyboard shelf. The backs of the shelves and the shelf extension for the cords were attached using pocket hole screws (Kreg jig).
Step 8: Final Outcome
Some length was lost when the desk was reconfigured, but the addition of the keyboard shelf and monitor stand made up for the loss. Next steps - create pencil holder, drink coaster, and more...
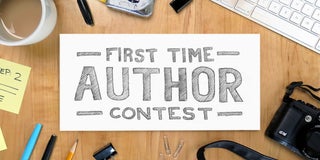
Participated in the
First Time Author Contest