Introduction: MAKING WAVES
I have seen many interesting versions of this wave generating machine and decided to make one of my own. The first one I saw appeared here: https://imgur.com/gallery/CHklf.
My first thought was how entertaining it would be to make a CNC project out of it. Wanting to provide better cam mechanism visibility, I contoured the center plate and gave the side supports some openings as well. Knowing I would get tired cranking it, I took it a step further by adding an electric drive system. I left the crank in place, in case of power failure. By shaping the cams differently, the wave motion can be significantly altered. I elected to stay with round cams.
I set about modeling all the parts in SolidWorks ®. Then created the step files required for generating the G-code. Documentation for all the machined parts can downloaded below in the forms of step files, dxf files, and pdf files.
Because of the motor addition, some soldering is required.
Most all the parts were cut out using my 3040 router/engraver. Parts were held in place either by double sided tape or my home-made router vise. Careful indexing is required for the Drive Box as there are pockets on both sides of the part.
Because of the soft nature of wood, be careful not to over tighten screws during the assembly processes.
Supplies
Glue_ similar to Elmer’s wood glue or Titebond
Super Glue
Fine and coarse sand paper
Steel Wool #0000
Paste wax
Soldering iron and solder
Clear Wood finishing spray
Step 1: Materials
Baltic Birch
1 piece 9 ½ x 7 ¼ x ½ inches for the Guide Plates
1 piece 7 ¼ x 7 ¼ x ½ inches for the Base
1 piece 6 ½ x 6 ½ inches for the Rings
1 piece 4 ½ x 5 ½ inches for the Feet
1 piece 6 ¾ x 5 ½ inches for the Gears and Motor Supports
Oak
1 piece 2 x 18 x ¼ inches for the Side Bars and Crank
1 piece 2 x 6 ½ x ¾ inches for the Drive Box
1 piece 2 ½ x 7 ¾ x ¼ inches for the cams
MDF
1 piece 7 x 7 x ¼ for the Rim
Dowels
1 piece hardwood 3/16 diameter x 9 inches long for cam shaft
22 pieces bamboo skewers .116 diameter x 5 1/8 inches long for lifters
12 pieces hardwood 1/8 inches diameter x 7/8 inches long for cage gear
Brass Tubing
1 piece 5/32 OD x 1/8 ID x 2 ¼ inches long
Screws
4 PHPD 4-40 x 5/16 inches long
10 PHPD 4-40 x ½ inches long
12 PHPD 6-32 x ¾ inches long
1 PHPD 6-32 x 1 inch long
2 M1.6 -.35 x 5mm long
Motor
1 Micro Gear head 90 rpm, 12 vdc motor (https://www.servocity.com/90-rpm-micro-gear-motor)
Misc
1 miniature double pole three position, on/off/on toggle switch
1 Battery Connector for 9 volt battery with 10 inch leads if possible
1 Battery, 9 volt
1 aluminum ¼ inch OD standoff ¾ inches long for crank handle
2 nylon or wood spacers 3/16 inch ID x .16 inches long
Step 2: Making the Parts
My System (dust pick-up removed)
Step 3: Cutting the Cams
This was performed in two operations. First, the index marks were cut using a 10 degree engraving bit. Then after a tool change the holes were machined as pockets and then the profiles were cut.
Step 4: Cutting the Guide Plates
Step 5: Cutting the Feet (Cam Followers)
After the drilling operation, I made a tool change to cut the profiles. For the thinner parts I used a 10 degree tapered engraving bit to cut out the part profiles. I get nice smooth cuts this way. I program for several passes advancing the depth less than 1 mm each pass until the cut is clear through.
After cutting out all the parts, sand the edges as needed to remove rough edges and sharp corners. This is a good time to tap the six 4-40 screw holes in the top guide plate.
The outer circumference of the cams should be very smooth to the touch.
Step 6: Assembling the Cams
When assembling the cams, I started with a dry fit to check out the tolerance stack-up of all the parts. It is important to verify that the centers of the cams line up with the centers of the holes in the guide blocks. Paper shims may be placed between cams if the material too thin. If material is too thick, sanding the sides of the cams may be required. Also, the thickness of the glue application can be a factor. Build slowly and check often. Be sure the 3/16 inch dowel is long enough to protrude 1 ½ inches past the outermost cams, they will be trimmed at final assembly. Also try to use the straightest piece of dowel you have.
Start from the center and work out. I machined an index mark on each cam to help with the angular alignment. Sheet 3 of the documentation shows how mine turned out. Angular spacing is not too critical but the index marks help ensure that each cam pair are timed the same.
Apply 2 or 3 small dabs of glue on the smaller of the two mating parts to help limit the application. Push the pieces together near the angle position targeted. Then twist cam into final position. I did not apply glue to the dowel.
Step 7: Cage Gear Assembly
When assembling the cage gear, I cut the dowels slightly longer than required. All pins were glued into one side plate protruding slightly to the far side. The second side plate was then glued in place slightly below the dowel tops. When dried, both sides were sanded to make the dowels flush with the plates being careful not to sand through the veneer.
With exceptions, a clear finish can now be put on the remaining wood parts, cam assembly and cage gear assembly, followed by a very light rubbing with #0000 steel wool and paste wax. A light buffing with a soft cloth should leave a nice sheen.
Exceptions: Do not coat feet, bamboo lifters and bottoms of rings (hole side), because more gluing required.
Step 8: Drive Assembly
With a center punch, make a small indentation about ¼ inch from one end of the Brass tubing drive shaft. Because the shaft will have tendency to collapse, it is advised to grind or file a small flat (similar to the motor shaft) on a 1/8 diameter rod to temporarily slip inside the tubing to prevent this. Do not go too deep as the tubing indentation must slip over the flat on the motor shaft.
Start by attaching the motor to drive side motor support with the two M1.6 screws. Use caution, if the screws are too long, they may interfere with one of the gear plates.
Install the switch and tighten in place with mounting nut refer to sheet 2 of the documentation. The battery connector I used had wire long enough to wire the project. Cut and connect wires per the wiring diagram.
Be sure to route the wires through the motor support before soldering.
Step 9: Main Frame
From the milling process, the cutouts in the plates where the Sidebars mount have rounded corners. Use a file or other preferred means to create sharp corners so the sidebars can seat correctly.
Fit the Sidebars into position on the three plates. Hold in place with tape or clamps. Then with a #35 or 7/64 inch drill bit, drill a pilot hole through the sidebar holes and into the plates at least 7/8 inches deep. Separate the pieces and tap the holes 6-32 to the bottom of each hole.
Secure the Sidebars in place with six 6-32 x 3/4 inch screws to verify fit.
Step 10: Ring Assembly
Reassemble the two guide plates, base and sidebars using twelve 6-32 screws screws. Place two scraps of 1/8 inch Baltic Birch on the top guide plate alongside the hole pattern.
Starting with the inner most ring, place a lifter through both guide plates and apply a bit of glue on the end and place the inner ring in place engaging the two parts. Repeat with a second lifter. Allow the ring to rest on the scrap pieces and verify that the lifters are fully engaged with the ring.
Step 11:
Repeat this process until all rings are in place. Allow a few hours for the glue to dry.
Step 12: Install the Cams
Carefully, remove all the rings. Remove the screws from one side of frame and remove sidebar.Place the two nylon spacers on the cam shaft and set in place under the lower guide plate. Replace the side bar and screws.
Step 13: Rim and Crank
Install the Rim and Crank
Note: It was my choice to just use a friction fit for the Crank to Shaft. A bit of tape wrapped around the shaft provided a good tight friction fit. With a Q-tip, apply a light coat of paste wax on the outer diameter of the cams using the Crank to rotate them.
Step 14: Re-install the Rings
Install the rings back into place. At this point the rings and lifters should follow the cams as you rotate the Crank.
This has worked well enough for me at this stage without gluing the feet in place. With the feet glued on, complete disassembly cannot be performed.
Step 15: Install the Drive Assembly
The Drive assembly can now installed. Place the Drive assembly on the Base plate such that it is centrally located from side to side. The gears should be fully engaged but not binding. Mark the locations of the four corner holes, then remove the Drive assembly.
Remove the Base plate and drill four .089 diameter holes 3/8 inch deep and tap the holes 4-40. Re-install the Base plate and secure the Drive assembly in place with four 4/40 x ½ inch long screws. For the last step, glue the Drop to a skewer. By trial and error, cut the length of the skewer to achieve the desired action with the rings when riding on the center cam.
Actuate the switch and enjoy. Thanks for looking.
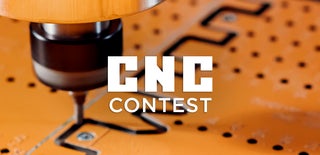
Participated in the
CNC Contest