Introduction: Macro-sized Diatom Box
"Untouchables" means going smaller, as well as infinitely larger, so I based my project on Diatoms, tiny organisms that populate our oceans, and can be found in soils. The living diatoms create the majority of oxygen for the planet. Their mineral-rich skeletons can be found anywhere by water, and land as fossils, but they are hardly seen.
More info:
https://westerndiatoms.colorado.edu/about/what_are... - Pretty cool and articulate article
http://tolweb.org/Diatoms/21810 - Small type, but don't be discouraged! Some great pix!
https://en.wikipedia.org/wiki/Diatom - Extensive, but not definitive
http://diatoms.myspecies.info/node/8 - Short read
https://blogs.scientificamerican.com/artful-amoeba... - Amusing moredetailed read
http://www.ucmp.berkeley.edu/chromista/bacillariop... - Very brief
The two shapes that intrigued me were the wheel-shaped ones, and the triangular boxy ones that reminded me of glass bricks, furnace blown glass or glass castings. The Untouchables Challenge got me moving to create a 3D model to be 3D printed or CNC'd.
In this Instructable, I will show the steps involved in creating the 3D model file - which I hope to print this week, but this will occur after the contest ends. I will update my post with the 3D printed object.
Step 1: CAD Software
I used SolidWorks, Student Edition with Photoview 360, V.2016, but you can use pretty much any other CAD software as long as you are familiar with the commands.
For the first part, I chose to make a base of the shape - circle or triangle. If I was to make this more like a triangular diatom, I would have used splines to allow a slight curve inward on all three sides. I will start modeling with the Diatom Wheel.
Step 2: Extrude Sides, Add Hub
Define the thickness of the sides. In Solidworks, I converted the outside edge to this sketch, and then offset and added another circle 0.10" from the converted circle. This will extrude upward to make the wheel's side.
Next I created a new sketch for the hub, defining the size of the outer circle, then offset that one with a smaller one.
Extrude that up.
Step 3: Rib and Circular Patterning
Each program defines ribs differently, and Solidworks doesn't make this terribly obvious. I used the Help feature for "rib" and the explanation and samples seemed clear until I tried it and it didn't work. After several tries, I hit on sketching a line from the hub inside ring to the outer edge of the entire form. This ensured me that the rib that will extrude will be touching and connected to both vertical rings. If I had drafted the rings, that would have been another option.
Step 4: Adjusting Ribs
aI noticed that the diatom's ribs aren't flat across, so I added an asymmetric bit to the top. I realized afterwards I could have done this right after making the first rib base, and then applied the circular patterning for the final rib shape.
Step 5: Minor Change to the Diatom's Wheel Shape
Adding a reference geometry of an axis so I could make a revolved cut of the side, I created a profile of the cutout shape I wanted onto a plane (front plane), and then revolved it along the axis. This is a simplified form of the Wheel Diatom.
This was a first time practice example to loosen up my diatom imitations.
Now onward to the more intricate Triangle Diatom.
Step 6: Triangle Diatom Box: Shape of Cover, Extrusion, Dome
My dimensions as shown. You can make your own. I extruded to 0.5" for the cover as I wanted the bottom box to be taller. To dome a surface, I had to have a thin extrude to use for the dome base.
In SolidWorks, the dome feature is found under Insert, Features, Dome.... click on the face to dome, input the height of the dome, the Continuous Dome is selected automatically for a smooth surface. When unchecked, the dome would be faceted if there are any straight sides. For circles, the choices are spherical or elliptical, giving a significantly different profile shape.
Step 7: Shell Cover, Start Making Holes!
After Shelling the underside of the cover, I used the Linear Patterns for many of the holes in the sketch mode, following the straight sides, and staggering the rows. Instead of making a go of it in one extrude cut, I chose to take several steps in order to control what I wanted to do with the overall pattern of the holes. That said, I did use the same sketch as a basis for the patterning. I also used the Circular Pattern for grouping of holes and put (3) sets in equal distance around 360 degrees. I could have set the amount of the arc for the patterning to any amount - like 90 degrees or 120 degrees.
For the large circle separating the corners from the inner holes, I created a Reference Plane to float above the domed surface. I sketched on this plane for the inner circle holes. I cut a 0.1" deep and wide band to demarcate the outer vs the inner holes. This made the doming a bit more prominent. Now for the inner circle of holes!
Step 8: Now for the Fibonacci Part ... Sort of - and the Finished Cover!
I did two versions of the holes for the center circle - one growing larger at it went into the center, the other going smaller. After looking at it, I felt the holes going larger seemed more mesmerizing.
I laid out several construction circles, growing wider apart from the outer circles. For the outermost circle, my holes started out small, then each successive circle going inward, the holes would increase slightly in size, and decrease in number. The final inner circle has only (3) large holes. To see my pattern easier, I hid the previous steps.
I think the end result came out pretty well. I then filleted the top surface and holes - which took forever with that many edges! Impossible to see the fillets in the rendered picture, and so I included a closeup with edges and rendering. I thought the outlined underside looked pretty cool, too.
Finally, I filleted the inside edge of the cover to fit with the bottom of the box.
Step 9: Box Bottom
I used the cover's outside edge and Converted it for the sketch for the box bottom. I extruded it 1.5", and then offset the outer edge 0.1" for a lip on the surface that will face the cover, and extruded cut that ledge.
I shelled the inside with the surface that would face the cover. With a fillet at the inside edge created from the ledge cut, I smoothed out the transition.
Then I flipped the box upside down to make some feet at the corners, using the offset to get some arcs, and adding small arcs at the ends to make one foot. I then used the Circular Pattern to make the other feet. Filleted the edges of the bottom (0.01") for a finished look, and the bottom is all done.
Step 10: Taaah - Daaah!
Voila! The 3D modeling part is finished! I rendered the top translucent teal, and the bottom shiny black plastic, though it's hard to tell.
The section cuts show the shell thickness, as well as the sides and feet. This diatom will definitely be a million times larger than actual!
I will update this Instructable after I've 3D printed or CNC'd the box! I can hardly WAIT to see it in real life!
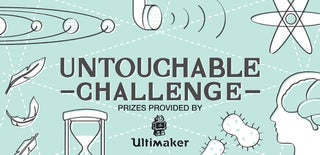
Runner Up in the
Untouchable Challenge
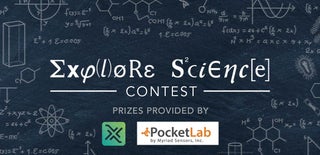
Participated in the
Explore Science Contest 2017