Introduction: Magician's Card Table
My son has been performing magic as Jet Veridis for a little over a year now. Last Christmas, when he had only been performing for a couple of months, I made him a portable padded surface he could carry around to practice and perform on.
In the past year that little surface has gone everywhere, including many street shows and other venues. It works well, but it is kind of small. This year I decided to make him a larger surface that would really let him spread the cards dramatically and give his show a more polished look. It's not as portable as the smaller surface, but when performing for a crowd, it sure works out much better.
This is not a how-to so much as a record of what I did.
I had a couple of missteps along the way, and the result is far from perfect. It IS, however, a great improvement from the earlier surface and it works well for him. I did not wait for Christmas this time, as he had a party and a street fair to perform at in early December.
I'll probably end up making a nicer version in a year or so. Until then....
Step 1: The Table and Materials
To start, we found a black 6' folding table at Wal Mart. Black and green is the jet Veridis theme (jet black, "veridis" from the Latin for green, "viridis")
Since we were not going to cover the finished project with a tablecloth, we wanted a black table for the parts that would remain uncovered.
I needed some molding from the local Lowes hardware store, some 1/2 furniture foam, some green suede-looking cloth, and some PVC.
The fabric was perfect because it "grabbed' the cards just right, allowing them to be spread or slide easily, without sliding all over the place. Essentially, the cards go where you tell them to and stay put.
I also needed the tools, glue, and hardware to put them together, of course.
Step 2: The Legs
Jet performed maybe two street fairs with a regular table. It was just too low. We got some bed risers and they put the surface at a comfortable height. We will be keeping the risers, as they are easily portable. We also cut some 1 1/2" PVC leg covers/ risers that are much more stable and easier for one person to use. They don't collapse though.
If we had found a black table with a crossbar close to the bottom of the legs, we could have made the PVC shorter. Maybe next time I will find another table with the right kind of legs and, if necessary, paint it black.
Cutting the PVC was no problem, and they are stable and simple to slide around if we need to move it.
It also provided a more comfortable work height for the rest of the project.
Step 3: Measuring Out the Working Surface
Jet wanted the surface to be right in the middle of the table (of course he did!). He likes when people can gather on all sides and see equally well. So, I used the foam to measure out where the working surface would be and how big it could get.
I cut the foam so we would have a break in the middle and set it aside.
Step 4: Measuring, Cutting and Gluing the Border
Measurements in hand, we went to Lowe's to choose the molding.
To make this basic frame, I borrowed/stole from THIS INSTRUCTABLE about making a frame from molding. I thank irisgottlieb for posting it, but do not blame her for the end result.
I cut all the pieces to size with the chop saw. One concern I had was that I actually needed to cut the frame in half. This turned out to be no problem at all with the clamps I used.
I did glue the pieces before clamping them together. I bought four clamps from a little hardware store closer to my house because they are much cheaper than Lowe's. I won't tell you the name, but there is a harbor involved. Two of the four were all but impossible to turn the screws on. The other two turned easily, but only one of the four held the pieces square. I used a steel carpenter's square to test that.
I ended up using shims in the clamps to hold the wood at a true 90 degree angle as measure by my steel square. Moral of the story? Just buy good stuff.
In the end, I got all the pieces glued.
Step 5: Testing the Layout
With the molding and foam cut, I added the fabric and tested the overall layout. I laid the foam on the table, then the fabric, and finally the glued frame.
It all looked OK, so I started making it permanent.
Step 6: Gluing the Foam
This is pretty straightforward. I taped off the parts of the table that should not be sticky and sprayed the glue on.
Once it got tacky, I just carefully pressed the foam into place. I have glued foam to stuff before, and the only time I have had a problem us if I sprayed directly on the foam. The solvents eat it.
Spray first, then adhere.
Step 7: Stain the Frame
Nothing much to this. I had a couple of stains left over from making haunted house props. I just mixed them (same brand/type of stain) so I'd have enough.
Then I laid the wood on some coroplast harvested after elections were over and stained it.
Step 8: Affixing Fabric
Now everything was ready for final assembly.
I had some issues here.
To do the fabric, I folded the table to a 90 degree angle. This gave me access to the center break, which I would need to cover with fabric.
My method for affixing the cloth seemed straightforward. I cut the fabric in two and spray glued the back of one piece. Once it was tacky, my son and I laid it down on the foam, careful to make sure it stuck without air pockets.
The first trouble came at that break in the center. Try as we might, we could not get the foam to stay perfectly flat. One part or another always compressed more than the rest. I tried laying a flat piece of wood on the top of the edge and pressing slightly, but I still got uneven spots.
I'd love to tell you I figured it out, but in the end, I just went with "close enough". I did both halves in this way.
Side note: I realized afterwards that cutting the fabric made it easier to apply, but was not 100% necessary. I could have folded the table completely in half and glued the fabric up one side, across the gap, and down the other side. This would have worked fine. Because I would have glued the fabric down, it would not have popped up in the center when the table was laid flat.
Step 9: Affixing the Frame
The frame presented its own problems. My original intent was to screw it to the table from the bottom. The first problem with that was the underside of the table was not flat. It was like an egg carton.
That would mean precisely measuring holes so they would all come through either the depressed or raised part of the underside. Or using different sized screws.
Gluing did not seem viable. I have spilled every kind of glue and epoxy I own on this kind of table. While it doesn't always come away cleanly, this plastic simply does not stick well with any thing I have ever used. Gluing fabric to it is one thing, wood is quite another.
Measuring and pre-drilling seemed the way to go, so I pre drilled some holes in the table. When I tested the screws, they split the wood. It just seemed too hard to pre-drill all the wood perfectly through the table without drilling all the way through (it's pretty narrow and thin, and I'm not a woodcrafter). I decided to drill holes through the top of the frame and fill them in.
So I laid the wood where I wanted it, clamped it in place, and drilled. I used a countersink bit to countersink the screws and I puttied them over after.
When the putty dried I sanded and stained it too.
That is easily the least satisfying part of the project. I never wanted to have any visible holes in the frame, and now there are, stain or no stain.
Step 10: Field Testing
My wife made a skirt for the table, which we simply attach with velcro. Nothing elaborate- just a long piece of cloth and a long piece of velcro.
With everything as good as I could get it, we took it to a local street fair and tested the table under actual performance conditions.
It seemed to perform just fine!
I'll add some staples to the fabric that goes down into the center break, as that seems like a weak spot. Also, My wife made a cover for the whole table, as between the suede type surface and the velcro, the thing is a debris magnet!
What's important is that Jet likes it, and it made the performance easier and better. Some regulars even commented on the new table, so that's nice.
Maybe one of these days we'll get video of him using this table in action and I can post it. It will probably end up on his YouTube channel in any case.
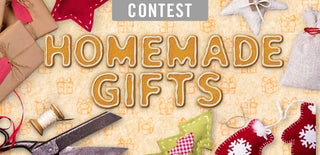
Participated in the
Homemade Gifts Contest 2015
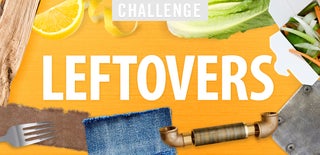
Participated in the
Leftovers Challenge
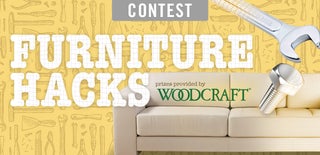
Participated in the
Furniture Hacks Contest