Introduction: Make It Access Bridge Build -- WORKING PROTOTYPE
Hi my name is Catelynn Reed I will be a senior next fall at Buffalo High School in Minnesota. I would like to go to school to learn a trade after I graduate high school. Maybe an electrician, welder or construction.
My grandparents made a drainage ditch last summer to solve a water drainage problem in front of their garage. The problem is that the ditch makes it awkward and dangerous for them to access the back of the garage and backyard from the house. Since this was an actual need for them I felt it would apply to this contest. I had to keep it simple, since I would actually build the bridge. My goal was to make it strong and convenient; to be functional but attractive.
My grandparents already had all the tools I needed to build the bridge. My dad had most of the supplies that were salvaged from other projects. We did have to buy the concrete and some wood for the planter.
--Working Prototypes are functioning versions for testing purposes. This one is smaller than most bridges you will see. This a small trench. The longest side of the bridge is about 10 feet. If this were for a park or golf course going over a creek, the materials would be much bigger, much heavier. Like I-beams and pillar supports that go much deeper into the ground and would be much wider. I am sure the concrete would need to be cut to allow for controlled cracking. It will work for my grandparents. We shall see over the years how it holds up and what I would do differently. if I was involved in a commercial bridge building project I would already have some basic knowledge of things that work and things that don't.
Supplies
Most of the supplies were salvaged from other projects.
4 heavy angle iron pieces, 4 inch sewer pipe, rebar, chicken wire, 2.5 sheets of plywood, 4 2x4s, screws, 55 bags of concrete, railing, 1 decking board, 2 2x10 green treated boards, 1 2x8 green treated board, flagstone. Annual flowers and solar lights.
Tools
chop saw/ miter saw, welder, circular saw, drill/screw gun, cement mixer, Shovel, trowels, rubber mallet.
Step 1: Tinkering the Design
Tinkercad was useful for making draft ideas for this project.
I started with some simple ideas and then changed them to better fit the area I needed to cover.
The bridge is slightly v shaped with a handrail, some flagstone ramps and a planter for display plants.
Tinkercad was a good visual guide for me and helped me think through the steps to build the bridge. Some of the materials changed a little from the drawing as I had to use what was available.
Step 2: Laying Out and Building the Supports
I used the main metal support beams to locate where I wanted the supports. I dug the holes and cut sewer pipe to use as concrete forms.
Step 3: Building the Form for the Concrete
Once the pipes were cut and in place. I layed together 2x4s over them and screwed and braced them together. I had help to flip it over and then I cut plywood and screwed it to the back of the 2x4s. I then filled the sewer pipes with concrete. I Placed the plywood form on top of the supports and drilled holes where the pipe supports were located under the plywood. I cut short pieces of pipe and inserted them through the holes and into the wet cement. This would attach and hold the angle iron and wood form to the supports.
Step 4: Add Metal Support to the Bridge
Before I can pour the concrete form it has to be strenghtened with rebar and mesh wire. The wire holds the concrete together when it eventually cracks. I have been told that all concrete will eventually crack. So the metal holds the concrete in place over a long period of time.
I used and arc welder to weld the rebar to the heavy angle iron to lock it all together. It was fun!!!
Step 5: Pouring the Concrete
My dad helped me pour and spread the concrete. It took 35 bags to fill the form. By the end of the day I was really tired. The next day the concrete was totally set. But it is best not to walk on it for a few days since it is still building its strength.
Step 6: Adding the Railing and Cement Curb
The railing needed an additional pvc pipe form and poured cement on the ends. I welded the center post to the angle iron and used blocks and boards to hold it straight while the concrete was poured.
I then built a wood form for the concrete curb and poured it. The outer green treated deck board is where the planter is attached.
Step 7: Building and Attaching the Planter Box
Now for a little decoration for visual interest. i used 2 2x10 and 1 2x8 green treated lumber to build the planter box. Notches were cut into the back and bottom to fit the supports. The notches also serve as drainage for water within the box. I then attached it to the green treated deck board with screws.
Step 8: Adding the Flagstone Approach and Trench Access Steps
The approach had uneven ground. So I used flagstone with support concrete underneath to make the approach the same level. I left space for dirt around each stone so grass can eventually grow between them.
i used a 2x4 as a guide to find the angle for the two levels to line up. I dry fit the stones first so I had a rough idea how they might fit together.
The flagstone needs to be tamped down with a rubber mallet to make good contact with the concrete.
Step 9: The Finished Bridge
I added some bling. Planted annuals for color and I added solar lights.
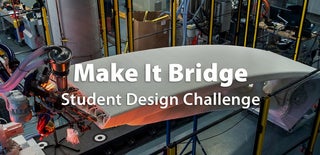
Second Prize in the
Make It Bridge