Introduction: Make It Extreme's Plasma Cutter Notcher
A very essential tool for every manufacturer who uses tubes to his constructions is the notchers. The notchers are very useful as they are used to remove a piece of the tube in order to fit precisely on another tube without leaving any gap between them and so that their welding to be accurate. Generally, notchers are essential tools and particularly, in constructions like a buggy, exhaust, fields of a mini football and in anything that requires the use of tubes and the procedure of welding.
Step 1: Square Tube
There are various kinds of notcher at the market and each and every one has its own advantages and disadvantages. In particular, our construction uses the plasma cutter as a cutting tool. To start with, we first made a frame made of a square tube of 30 x 30 x 2mm on which we placed a tube with slots to pass a bearing through the two edges. Then, through the bearing we passed a perforated shaft, which at its back side a pulley was placed and it was connected on the motor with a strap.
Step 2: Motor - Flange
Initially, we used a motor taken by car wipers but then we preferred an AC motor having the potential of moving both on the right and on the left. The motor was connected with a potentiometer to regulate the speed of its rotation and with a switch that chooses the rotational direction as well as the activation of the motor. Therefore, by activating the motor the perforated shaft rotates on the direction that we want and at the speed that we wish. After we had achieved our goal and this function, we put an aluminum flange lined with linear bearing at the front side of the perforated shaft. The linear bearing is used for ensuring a forward and backward move in our machine.
Step 3: Basis
Moreover, using these bearings, we managed to make a basis for the plasma cutter. At the back side of the basis, there is a bearing that follows a guiding ring to achieve a particular move according to the guiding ring. In specific, our system is known as a ‘pantograph’. At the front side of our machine, it was made a basis that a clamp was placed for the tubes. In this way, the plasma cutter is spinning around the tube following the orders of the pantograph and removing the material that should be removed.
It should be noted that without the pantograph, our machine cuts in a straight line and if it is needed to cut in an angle, the inclination for cutting is chosen according to the direction of clamp’s rotation.
Step 4: Done
In conclusion, our construction’s advantages are multiple. For example, it is mobile and light, it can cut tubes of a large diameter compared to other kinds of machines that are not capable of that. Also, it can cut straight angles and various shapes according to the guiding ring of the pantograph. More importantly, its major advantage is its cost as it is much less comparing to other machines like CNC that are also capable for the same thing. Additionally, its potentials are not just restricted to these as it is also capable to cut round flanges and many other things using different clamps and different basis for the plasma cutter.
Step 5: Video
Closing, it is hard to describe this construction in words so there are precise designs at the make it extreme patreon for any of you who is interested to make it by himself.
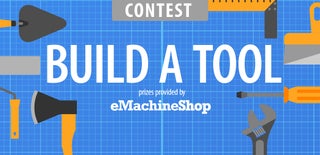
Participated in the
Build a Tool Contest 2017