Introduction: Harvesting Bark From Downed Trees for Baskets
Over the last few months I have been learning how to harvest inner bark from various types of trees that grow where I live (in upstate New York). I have some experience with basketry from store-bought basket reed, and have been doing research on using foraged material, but was a bit intimidated by the idea of harvesting from trees. The literature around harvesting inner bark is generally not the most approachable, and often assumes that you have land and can pick which types of trees to harvest at a particular age and in a particular time of year. I am interested in harvesting from trees that have fallen down or are taken down for alternate reasons, and harvesting bark for baskets would just be a byproduct. I could find almost no instruction on this type of harvesting, so I decided to just experiment with what was growing around me. I am happy to report that you can harvest material from found trees and turn it into beautiful baskets!
Why harvest from naturally downed trees?
If you don't own land (I do not) or work in landscaping (I do not) then taking down a tree might seem a little unapproachable as a means to get material. Harvesting bark from trees that have fallen down or been taken down for other reasons is an extremely low impact way to gather material. The tree is down already, and would otherwise just rot in place. Other flat basketry materials (like rattan, the most common source for commercial basketry) is grown in jungles, and is processed an imported (unless you live in one of these jungles).There are issues with how rattan is harvested commercially -- potentially negatively impacting the forests it is grown in. Harvesting inner bark where you live is a way to use a local, foraged material to make beautiful things from! (And the way that I am advocating, only using downed trees that would otherwise rot.)
What are the challenges of harvesting from downed trees?
One complication with downed trees is that you likely have to bring tools with you to a downed tree, so your tools will need to be portable enough to carry with you. Another is that the tree might not be in an ideal position or location to harvest from. And without these optimal conditions you won't be able to maximize absolutely all of the material there. (For instance, the under side of a log that is too heavy to move.) For me, the benefits of harvesting bark in this way still outweigh the down sides. I have casually been harvesting when I happen upon a good looking downed tree for the last two months. I have enough splints in reserve to make 3-4 medium-sized baskets. Maybe it wouldn't be a practical method if you want to make a living off of selling baskets, but if you just want to learn and make some as a hobby, I recommend it!
Not all trees will work, but many will
Many trees have a usable layer of inner bark, but some are much more desirable than others. I have found the literature on this subject to be fairly incomplete, so I started experimenting with what I found around me. I have harvested and woven with inner bark from striped maple, eastern hemlock and white ash. Ash is well known for being an excellent basketry material. The striped maple (which I had never heard of anyone using before just trying it) might be my favorite!
What can you use inner bark for?
The outer bark of trees (what most of us usually think of as the bark) will often be scaly, flaky or wrinkly. But just beneath that outer skin is a layer of cambium, or inner bark. The inner bark has totally different properties than the rest of the tree in terms of a material. Under the right conditions, it can peel off of the interior heartwood pretty easily (though this depends on many different factors.) Once peeled away, these strips of inner bark are incredibly flexible almost like leather. When they are fully dried and cured, they become firm again almost as strong as the wood itself. Traditionally, inner bark can be woven into beautiful baskets, but I also think it is an incredible material that has dozens of potential uses!
What are splints and splintwork baskets?
Different types of basketry are differentiated by the shape and firmness of the materials used. Some use round materials, or flexible grass-like materials and some use a wide, flat material. Most basketry instructions will use the word "reed" because that is the product that you can buy. But splints, or thin strips of flexible wood can be used to make just about anything that you could make from flat commercial reed. Having used both, I far prefer splints! As a material, splints are incredible. It is much more flexible than commercial reed of a similar size but just as strong or stronger once cured. It is a really pleasant texture to touch and it even has a lovely sweet woody smell. If you want to see some examples of traditional splintwork baskets, just google something like "Appalachian splint basket". You will find beautiful and inspiring creations (most antiques) made from trees! Some splints are made from splitting the heartwood of logs down to thin, flexible splints. I haven't experimented with that yet, and will just be talking about harvesting inner bark in this tutorial.
Step 1: Tools You Will Need
Harvesting inner bark doesn't take too many specialized tools. And neither does weaving baskets with splints! With just a few common hand tools, you can take on a basketry project made with found material.
Drawknife
This is the one specialized tool that I would recommend if you want to harvest inner bark. The first experiment that I tried with harvesting, I peeled away the outer bark with a knife, which was very tedious. A drawknife makes it much easier to remove outer bark from a tree. I recommend keeping your drawknife sharp (your bark removal will go much more smoothly!)
Hand Saw
Not totally necessary, but I usually throw a lightweight hand saw in my pack, it can be nice to cut away branches and make it easier to access your work area.
Razor Knife
You will want a very sharp, thin blade to cut the inner bark strips. I prefer the snap-off blade type so you can always have a sharp edge.
Sharp, Sturdy Knife
Sometimes you might need a little more weight behind your cuts than you can get with the razor knife, so I like to carry a standard pocket knife with me.
Tape Measure or Ruler
Not totally necessary, but if you want to mark widths of strips you are cutting, or get the size of a tree, it can be useful to have along.
Dull Butter Knife (or something similar)
Sometimes I like to pry off the strips of inner bark. It is very important to have a dull, sturdy blade for this. You don't want to be cutting into the splints!
A Bag or Basket
Last thing, make sure to bring a bag or basket to carry out any splints that you harvest!
Step 2: Find a Tree Suitable to Harvest Bark From
I am ONLY advocating using bark from trees that are already downed. Never harvest inner bark from a live tree! If you are taking down trees as part of managing land, you can definitely use those for baskets too-- I have written this tutorial with a "use what is around you" mentality.
Look for downed trees that have the following qualities:
- The right size probably about 4-10" diameter. Smaller trees will have inner bark that is too thin to harvest. Larger trees will often be more gnarled and harder to both remove the outer bark from and to get uniform strips of bark.
- A smooth, round trunk without lots of branches and knots.
- Easily accesible. On safe, level ground where you will be able to work with them.
- Are newly downed (not rotten). Freshly downed trees will have light-colored inner bark, when it starts to rot the bark will turn a darker brown.
- Are a desirable species for weaving. Not all species are good for weaving, I wish I had a definitive list of species that work for weaving! What I know, I have learned from research and some from just trying what I have found where I live.
Test Bark for Workability
To test and see if you have found a tree that is going to have usable inner bark: cut a little shaving off of the outer bark and take a look at the inner bark. Is it dark and fibrous? It has already started to rot, and won't work for weaving. Is it springy, juicy and light colored? Great, sounds like it's worth investigating! Shave off the bark from a little larger area-- big enough to remove a strip of bark a few inches long and half an inch wide. If you are unsure of the species, or whether it will be good for weaving, take the strip with you and see what it is like when it dries. Take pictures of the tree to help identify it, if you don't know the species (make sure to include bark, branches and any leaves to help you identify the tree!) If your test strip is flexible and isn't extremely brittle when dried, you can likely use inner bark from this tree for weaving!
Species Known to Be Good For Weaving:
- white ash - I have used bark from white ash (including outer bark from a young tree)
- black ash - There isn't a ton of black ash that grows where I live, but it is a species well known for its bark. I would love to try using it someday!
- striped maple - This is the species that I have found most commonly down in the forest where I live, I haven't read anything about using this species of maple, and very little about maple at all, but when I tried the bark, it is fantastic! I haven't experimented with other species of maple, but I think it would
- hemlock- One book that I read suggested hemlock inner bark was a nice material. I found a downed hemlock and did weave a small basket from the bark. I'm not sure I would harvest it again-- the texture of the inner bark I harvested is a bit fuzzy and needs to be sanded before being woven. I also found the dried bark to be a bit brittle (thought the finished basket does feel nice and strong.)
- oak - I haven't come across any oak in a condition to harvest, but it is another material classically used for basketry. I also don't have information about specific species of oak-- but if there are downed oaks in your area, they might be worth investigating!
Step 3: Remove Outer Bark
Prepare a work area. Remove any small branches that are hanging in your way, and move any debris on the ground that you might trip on. If it s possible to safely move the tree, prop the tree or branch up to make it easier to work with.
Remove outer bark with drawknife. Using as little pressure as you can, gently shave away the outer bark. You really want to remove as little material as possible, but get the harder scaly outer bark off. Work slowly and with light pressure. You don't have to remove bark from the entire log all at once, but you will want to remove enough to cut a few strips off from. You can always come back and work with the drawknife some more.
Step 4: Cut the First Strip
Plan out where you will locate your cut for your first strip to get a nice, long length (looking at branches, knots and other things that would get in the way of a nice strip of bark) You will need some long, thick strips for basket rims and handles, so it is helpful to have lengths several feet long. Six feet would be great. Anything much shorter than 18" won't be terribly useful. Use a razor knife to make one slice down the length of the tree where you want your first strip to be. Cut firmly into the inner bark, trying to get all the way to the heartwood (you will feel more resistance once you get to the heartwood.)
Decide how wide you want this strip to be (I find 1 1/2" to be a convenient width to harvest) and slice a parallel line that distance from the first one. If the bark comes off easily, it is okay to harvest wider strips. If it is very difficult to remove, you can do narrower ones. Basically, it is less work to cut larger strips. Ifthe bark isn't peeling off easily, it will be harder to get a wider strip to come off all in one piece. So figuring out the width is something you will probably want to do by feel and adjust based on the condition of the particular tree.
Now that you have outlined the sides of the first strip, cut across the grain at the top of the strip all the way down to the heartwood. It might take a little finessing, and sometimes I will shave off a little bark, just to get a clean look at the area I want the strip to start. Now it is time to start prying the strip off the tree. In the best case scenario, the strip will just peel right off. Often you will need to pry and convince the bark to separate. This is another step where you will have to go by feel, and use different techniques based on the condition of the tree.
My favorite technique is to use a dull butter knife to pry up the strip. (I find it is easier to not damage the bark strip when using a prying instrument without sharp edges.) If the strip starts to separate, with some fibers clinging to the heartwood, take a sharp knife and cut and scrape those fibers off, so you will get back to the original profile of the strip. (If you just continue pulling, you might tear the strip in two).
Ash is famously resistant to giving up it's bark. The traditional method is to bang the heck out of the bark with a rubber mallet. This breaks up the fibers and helps the bark to release. I have tested banging on other types of bark, and have found that most often it damages the strips of inner bark, and so is counter productive. But depending on the species, this is another technique to try!
Step 5: Cut As Many Strips As You Can
Cut away all the strips you can. Repeat the same process you used to peel up the first strip to cut as many strips as you can from the workable area of the log. Remember to look at the length of the strip and plan ahead where you want your cuts to go. (Sometimes you can get a longer strip by slightly angling your cut to avoid a branch or knot.).
Pack your strips to bring home. Carefully set strips aside and pack them up to take home. You can coil them, but take care that they don't kink when you bend them.
Step 6: Trim/Clean and Store Splints
There isn't any rule that you have to trim your splints right away, but I like to do it the same day I harvest them. If you trim them while they are still fresh and flexible, it is easy to store them in tidy coils, which will easily fit into a pot to soak when you are ready to weave.
Cut splints into uniform widths. I like to trim and store splints at home (though you certainly could do this step in the field if you want.) Use sturdy scissors to cut the bark strips into uniform widths. Don't worry if they don't look like they were made by a machine-- I think a little variation gives your basket character! I like to cut into around three widths something around 3/4"(good for ribs & spokes), 3/8" (good for weavers) and 1"(good for handles and rims). When in doubt, leave the strips wider-- you can always cut them down later! I also save thin strips of bark (1/8") for lashing/wrapping. Short pieces, (less than 8") get thrown away or turned into kindling.
Split very thick strips into two thinner ones. If you are lucky enough that you harvested thick inner bark, and it is thicker than you want to use, you can split the bark into two thinner strips. (Remember that you will want some thick pieces to use for rims and handles! And you can always split them later.) If you have decided to separate a piece into thinner strips, begin by cutting the strip where you want it to separate. Gently pull the two apart, holding one strip in each hand. Slowly and carefully pull the strip into two. When one side starts to get thicker, pull the thicker side down at a more dramatic angle, this will thin it out a little. It takes some practice, but you can learn to feel how the fibers are moving and get a technique for separating strips into thinner pieces.
Wind strips into coils and store. The general wisdom in basketry is to let your harvested materials dry out completely, and then rehydrate before weaving. This gives the material a chance to shrink and change shape before you weave with it, and will give you a tighter weave. The good news is that splints dry very quickly (within a few days) and a quick 30 minute soak in warm water will have them supple and ready to work with. As far as I know, splints will keep indefinitely! You want to make sure they have good air circulation when they are drying out.
Step 7: Soak & Weave Splint Baskets (or Other Sculptures)
I am not going to cover weaving instructions in this tutorial (that is its own subject which deserves a tutorial of its own. Maybe my next project!) For now, I will go over the preparation of the material and you can use splints to make a basket pattern designed for commercial flat reed.
How many splints to you need for your weaving project? If you are new to making baskets, I would recommend gathering more splints than you think you need. You always lose some length cutting the ends off, and almost all of the surface basket will have at least two splints overlapping. So if you are gauging visually, making a basket will take much more material than you might think. The good news is if you run out of material, you can always pause and pick it up later when you gather more (though running out of material is very annoying!) I have a rough gauge of how much material I need to use for a project, but it is hard to translate that into a rule of thumb. The best advise I can give is start with a small project first, and always accumulate more raw material than you think you need for your project!
Prepare splints for weaving. Place the splints in a container of hot water (not boiling, just hot straight from the tap is fine). Thicker splints will take longer to hydrate and become pliable. The splints that I have made have been ready to use in about 15 minutes of soaking. Test to see if they are ready by bending a piece at the end. It should not crack or splinter when bent. As you are working (depending on how involved your weaving is) your splints might start to dry out. Just use a spray bottle to keep the pieces hydrated and pliable while you are working. Inner bark splints are very easy to work with! You can bend them, cut them with scissors, punch holes in them and use leather rivets to connect them together! I
Finishing. After your project is done, you want to let it dry fully. At this point, you can treat it with any finishing coat that you would use on other wood work! (Stain, dye, oil.) I like to make functional baskets that will see everyday use, so I usually treat them with linseed oil to make them resistant to staining. Adding finishing treatments is totally optional and a matter of taste.
I hope you have enjoyed reading about this process, and would love to hear about it if you give it a try!
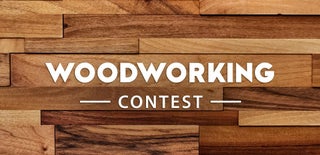
Judges Prize in the
Woodworking Contest