Introduction: Make a Benchtop Anvil
Here's how I made a small benchtop anvil for my workshop.
It was made out of a piece of small-gauge railroad track. Without the log base, the anvil weighs about 10 pounds. I plan to use it for pounding various bits of hot and cold metal, setting grommets, stamping leather, and basically any kind of light-duty pounding or flattening I may want to do.
While I'm showing the steps I took to make this and am sharing some general instruction, I admit I am very much a novice with any kind of metalwork. Therefore, constructive and informative feedback from knowledgeable metalworkers is highly encouraged, both for my sake and for anyone else that may read this instructable.
Thanks for checking this out!
Step 1: Acquire a Bit of Rail Track
To make an anvil like this you will need a small section of rail track.
The piece I used is small-gauge rail that is only 3.75 inches tall. I got a 9-inch long piece from a blacksmith that teaches classes where I live. He bought a pile of old rail at a scrap yard, and sells small pieces like this to his students so they can get started pounding metal at home.
It is not illegal to have a piece of railroad track . . . if it is acquired legally.
Obviously, you can't go pulling up railroad track unless you want want to get locked away for a long, long time.
At any given time, eBay has several listings for bits of scrap rail, both newish and vintage. There are usually finished railroad track anvils available too . . . so you could just simply buy one of those, or even just buy a cast iron hobby anvil or a steel bench block.
However, I prefer to spend a little more time, money, and effort to make my own things, as I thoroughly enjoy the making process.
So the first step is to ask around, search online as well as at your local scrap dealer, and legally acquire a bit of scrap rail.
Step 2: Tools, Etc.
I used an angle grinder for all of the cutting and shaping of the rail.
For removing large chunks of material, I used a 1mm cut-off wheel. I went through two of these.
For removing smaller amounts of material and general shaping, I used a 40-grit flap disc. I went through two of these as well.
For flattening the top of the rail anvil, I used a 40-grit corner/edge grinding and polishing disc. This disc is flat which helps make a decently flat surface by hand (this is covered in detail in step 4).
Other tools and materials used on the rail:
- Power drill with 3M Paint and Rust Stripper Brush
and a basic wire wheel
- Orbital sander with 100 - 220 grit sanding discs
- Wet/dry hand sandpaper in 320, 400, 800, 1000 grit
- Polish
- Wax
I sanded and polished my little anvil to a mirror finish just for fun. This was definitely not necessary as it immediately began to dull with use. But it was an interesting endeavor and I learned a lot by going through the finishing process.
Step 3: Flatten Top, Part One: Remove the Pits
The top surface of my rail had some pretty deep rust pitting.
Rails like this are typically slightly convex across the width as well, and I wanted my little anvil to be flat. However, for this first step we're only concerned with removing the rust pits and any other imperfections.
I began with a 40-grit flap disc on the grinder and carefully removed small amounts of material just until all the pits were gone.
The trick with this and the following step is to not go "hog-wild" and end up removing any more material than needed. There is no need to bear down and dig out troughs, which is the exact opposite of what is desired.
Always wear appropriate safety equipment: eye protection, hearing protection, lung protection.
Step 4: Flatten Top, Part Two: Hand-machining!
For this step I switched over to the flat grinding disc.
To flatten out the top of the rail and remove the little ripples from the last step (as well as any remaining convex-ness), you need to make smooth, full passes, with light and consistent pressure, keeping the grinding disc perfectly flat against the top of the rail.
If you move in a steady and consistent motion, you will eventually reveal a very flat and smooth surface. I would suggest trying to find a sweet spot of mechanically consistent rhythm with your body. Every pass needs to be a full pass from before one end of the rail all the way straight off the other. However, be mindful that you don't dip into or off of the ends, or you'll create unwanted slopes.
There's no need to bear down, as the weight of the tool is all that is needed and nothing more.
To gauge the correct speed of each pass, check the resulting swirl marks on the metal. Ideally you should see a fairly tight, machined-looking swirl pattern.
Step 5: Begin Horn
I wanted my benchtop anvil to have a horn that would allow for shaping basic curves.
I laid out the shape I wanted, and used a 1mm cut-off wheel on the grinder to slice off wedge shapes as shown. Don't be fooled though, this took about 20 minutes for each side!
Step 6: Make It Anvily
I then removed a section under the horn using the cut-off wheel.
The size of this notch is dictated by the reach of the grinder. I made two cuts from each side of the rail and even so, full cuts weren't able to be completed.
However, the still-connected area was small enough that I was able to break out the pie-shaped piece with a swift hammer blow (see last photo).
Step 7: Refine Horn, Etc.
To refine the shape of the horn and the cutout below it, I switched back to a 40-grit flap disc.
I carefully laid out guidelines with a marker on the horn to indicate areas to be removed. These were ground away in sections making uniform passes similarly to how the top was done in step 4.
The cutout below the horn was shaped until I was happy with it as well.
Step 8: Remove Rust
Using a wire wheel on a power drill I removed all of the rust. This could be done in a number of ways, but I went for quickness with the wire wheel.
Step 9: Power Sanding
To begin the process of finishing the shiny surfaces, I first used an abrasive Scotch-Brite disc in a power drill. This removed all of the marks left by the grinding discs.
I then switched to an orbital sander, sanding all the shiny surfaces with the following grits: 100, 150, 220.
Just like when sanding wood projects, the goal is to remove all the marks from the previous grit. When all you see are the new marks from the current grit, it's time to move up to the next one.
For the hard-to-reach cutout under the horn, I used a rotary tool with tiny sanding discs in similar grits. This worked great, although it was a little tedious; I went through probably 10 discs in each grit I used.
A note on orbital sander discs:I started this step using pretty typical aluminum oxide sandpaper discs on my orbital sander (which I've been quite happy with for all of my wood projects), but they wore out almost immediately on metal. Perhaps a rookie mistake. But then I switched to Diablo brand discs which are made with a "ceramic blend" . . . and the difference was amazing. The discs lasted much longer and were distinctly more effective.
Step 10: Wet Sanding
After the shiny surfaces were all dry sanded up to 320, I switched to wet sanding by hand using grits 400, 800, and then 1000.
Things started to look pretty nice at this point!
Step 11: Polish and Wax
I didn't have any fancy polishing compounds on hand, so I just used what I had: Mother's Mag & Aluminum Polish. It seemed to work fine though, since the polish turned black as you rubbed it in.
Following a series of rub-downs and buff-offs with polish, I did the same thing with Johnson's Paste Wax.
Step 12: Notches for Bolts
In order to be able to bolt the anvil down, I ground out notches on each side of the bottom plate.
This was done using an angle grinder with a 3mm grinding disc, by simply grinding away three disc-widths about 1/4" deep into the base for each notch.
Step 13: The Anvil Stump
I used a chainsaw to cut a small section from an old log.
I then used a router and a leveling jig to make the ends flat and parallel to one another. The process I used is covered in detail in another instructable I wrote: How to make log ends perfectly flat and parallel
Step 14: Add a Base Plate and Finish
A small base plate was made from a piece of scrap plywood which was screwed to the bottom of the log.
The log and base plate were finished with boiled linseed oil by simply rubbing it on liberally with a rag, letting it soak for a few minutes, and then wiping off the excess.
Step 15: Add Handles
I added two handles made from an old leather belt.
The leather pieces were fastened in place with 2 inch long 5/16" diameter lag screws, screwed into drilled holes.
Step 16: Fasten Anvil
The anvil was fastened to the top of the log with the same size lag screws as were used for the handles.
These screws were fastened into 3/16" holes that were made at an angle to match the profile of the anvil's base (see last photo).
Step 17: Done!
This was a fun project and I learned a lot along the way.
Thanks for taking a look!
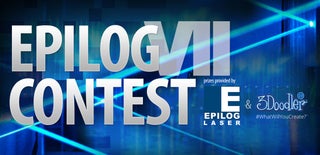
Participated in the
Epilog Contest VII