Introduction: Make a Knife From a Saw Blade Using Basic Tools
I wanted to try my hand at making a knife. I know the "right" way to do it, and that's my next project, but I wanted to see how I'd do using only cheap tools and cheap materials. So I got my Harbor Freight angle grinder and my HF files and some sandpaper and the blade that came with my (used) table saw and I got to work.
If you prefer video, you can check that out here: https://youtu.be/V91Btmi7oNU
Tools you will need:
- Angle Grinder (with cutoff wheels and flap disc)
- Files
- Bench vise
- Sandpaper of various grits
- Bench grinder (optional)
- Drill
- Saw suitable for cutting small pieces of wood
- Propane or MAPP torch
- Hacksaw (optional)
Materials:
- 10" table saw blade or other source of steel
- Bricks (preferably fire bricks, but regular red bricks work too)
- Small piece of hardwood (I used walnut)
- Brass rod
Step 1: Cutting the Saw Blade
Start by scribing a line across the saw blade and clamping it down securely. Using the angle grinder with a cutoff wheel, cut the blade along this line. Take care not to twist or push on the grinder, as cutoff wheels can explode if used improperly. Let the grinder do the work and don't force it. It'll get there.
PLEASE wear all necessary PPE/safety equipment when using an angle grinder. A face shield is recommended, but at least wear safety glasses.
Step 2: Shaping the Blank
I drew an outline of the blade on the metal using a sharpie, then made relief cuts with the grinder. Grinders aren't great at making curved cuts so this helps a lot.
I added a thumb relief with a half-round file because I liked how it felt. Use a file for fine detail unless you're very, very good with the grinder.
Once you have the blank shaped to your liking, it's time to start making the knifey part of the knife.
Step 3: Grinding the Bevel
Knife makers will tell you not to do this, and they're right. If you want a better quality knife, you should grind the bevel using a file and a jig to obtain the correct angle. I'm playing it fast and loose, so I used a flap disc and an angle grinder. This has the potential to overheat the steel and cause problems later on, so I would not recommend doing this with expensive tool steel or any knife you plan to sell. This is a first attempt for me and the steel was free, so we're doing it anyway.
Pay attention to how much material you're removing from each side. You want the sides to be even and the edge to be centered in the blank. Otherwise your knife is gonna look goofy. That's not the end of the world, but it's also not desirable.
Step 4: Heat Treating
Now we're going to get the steel super hot to harden it. To do this, we use a torch and some bricks to contain the heat. No fire bricks available? Regular bricks will do in a pinch. They just don't work quite as well. Be careful, because the inside will get ridiculously hot.
Bring the steel up to the temperature where it no longer attracts a magnet, then quench in oil. Used motor oil works (also stinks). Clean motor oil works. Vegetable oil works. Flaxseed oil works. Lots of oils work. Get some oil. Don't set your shop on fire.
At this point, a file should skate right off the steel. That's good, but we can't leave it like this. Go stick it in a 400-degree oven for something like 4 hours to temper the steel, then turn off the oven and let it come back to room temperature on its own.
After this, we're done playing with fire and we're going to avoid getting the steel too hot from now on. This means it's safe to add wood, so that's next.
Step 5: Adding a Handle (scales)
We're going to put a handle on this thing, and we're going to use wood. I used walnut because I had a scrap about the right size, but any hardwood will work fine.
Drill a couple of holes in the handle section of the knife. Try to keep them in line with one another and roughly parallel to the spine (back edge) of the blade or it'll look weird. Drill the holes the same size as your pins and remove the burrs with a countersink or just a small file.
Cut the scales to the rough size you need, then cut them in half. I used the bandsaw because I have one, but it's way overkill for this job. A hand saw will work just fine. Even one of those little flush-cut saws will work here.
You'll need pins. I used 1/8" brass rod and cut it with a dull hacksaw (dullness is optional). I then attached the handles with superglue (epoxy is also good), inserted the pins, and peened them over with a hammer.
Here comes the time-consuming part: shaping.
For rough shaping, I used the same angle grinder with the same flap disc. I did this because it will chew through walnut and brass without complaining, and I need to shorten the pins as I go. I then switched to the random orbit sander with 100-grit paper. A belt sander would also work if I had a belt sander, but I don't.
At some point it becomes easier to bring the work to the machine rather than bring the machine to the work. I inverted the sander and put it in the bench vise.
I switched to sandpaper and moved up through the grits. I went from 100 grit to 220, 400, 800, 1000, and 2000. By the end, the wood felt like glass.
Step 6: Polishing the Blade
I used spray glue to attach 800/1000/2000 grit paper to a scrap of wood and used it to polish the sides of the knife. You can just use sandpaper if you don't have spray glue. This removed the scratches from all of the previous work and left a really nice finish.
Step 7: Sharpening
Put an edge on the knife. Sharpening is too complex to cover here, but the basic idea is to start with a coarse stone and move up to a fine one until you have a nice edge on your knife. Bevel angle and whatnot is a very deep rabbit hole that I won't bother with here. Play with it and see what works. You're not going to hurt anything.
We're almost done.
Step 8: Optional: Final Polish
Sharpening can leave some icky stuff behind, so I used a cloth wheel on the bench grinder to polish up the blade one last time. This is completely optional, but makes the knife look really pretty.
Step 9: Finishing the Wood
I used beeswax and orange oil to finish the scales. It's simple and food-safe and doesn't stink.
Step 10: DONE!
Check it out! You just made a knife! Congratulations, you!
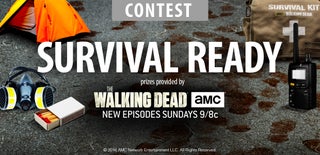
Runner Up in the
Survival Ready Contest