Introduction: Make a Manly Mallet!
Tired of living in a world surrounded by cat memes, frappuccinos, and smart cars? Want to add back some of that long lost vim and vigor that our forefathers had??(curly train robber mustache not included).
Well you've come to the right place my friend! Now you'll be able to send those Monday morning TPS reports packing! Turn that salad into a big bowl of bacon!! And magically replace every awkward photo you've ever taken with a picture of Chuck Norris!.....Oh you can probably do some awesome woodworking joinery too. All of this and more can be accomplished with a mallet so manly it's rivaled only by the mighty hammer of Thor!
Now, enough talk...let's get down to business.
Step 1: Gather the Goods!
In the spirit of frugality, and mostly laziness, scrounge around for a few scraps of wood. Ideally you'll want 2 1x3's each measuring at least 20".
I happen to have some curly maple and a few pieces of mahogany.
The list of materials is pretty short:
MATERIALS:
2 20" 1x3 boards
wood glue
a heavy filler (lead shot, lead fishing wieghts, bb's, etc)...sand will work but is not as heavy
5 min epoxy
about 1 sq ft of leather
A note on the tools, there are many ways to accomplish the same results as I did with many different tools. I used mostly hand tools for this project but you can use whatever you're comfortable with and/or have available to you.
TOOLS:
rip/crosscut saws
chisels
marking gauge
awl
marking knife
pencil
drill
1 1/2" hole saw bit
clamps
draw knife
spokeshave
sand paper
Step 2: Prep the Rough Handle/head
Before you do anything first makes sure that the faces of your wood are flat! You may have make a couple passes with a hand plane or run it through the planer. Once your wood is nice and flat you can move onto making the handle and head.
Start by ripping the wood you've chosen for your handle right down the middle. You should end up with 2 20" long pieces measuring roughly 1 3/4" in width. Glue these up along their faces,clamp them up and let them sit overnight. This will be the blank you use for shaping/carving the handle.
While that's drying, you can get to work on the head of the mallet. You will need four pieces. Two of them will be 5 1/2" long. The other two will be 2 1/4" long with a 2 degree cut one end.
Before you cut the smaller pieces, you should drill a 1 1/2" hole through the middle. It's easier to handle them while they're still attached to a longer board.
Now, glue the two smaller pieces onto one of the 5 1/2" pieces. Line up the outside edges and make sure the angled sides are facing inward and slope AWAY FROM EACHOTHER! If this is done wrong, you'll have to re cut those pieces.
Step 3: Finish the Head and Start Carving!
Once the two smaller pieces are glued to the 5 1/2" piece, fill them with whatever heavy substance you can find. I had some extra shotgun shells lying around so I sacrificed them to fill the mallet. You can use lead fishing weights, sand, clay, etc...whatever you have or can find easily.
Fill the two voids as close to the top as you can with out going over. Then, pour a layer of epoxy on top to help solidify all the loose pieces. Finally, cap it off with the other 5 1/2" piece, clamp it up and put it aside.
Now it's time to muster up your inner Nick Offerman (or Ana White for the ladies) and get to carving that handle!
My tools of choice for this task are a drawknife and a sharp spokeshave. Personally, I don't think anything beats the feeling of carving and shaping wood one curly shaving at a time as the morning sun's rays creep into your shop and rake a warm glow over your bench....I'm sorry, what was i saying??...Any ways, you can use any tools you have at your disposal. If you don't mind the copious amounts of dust, a belt sander will make quick work of this process.
Regardless of the tools you use, the process is the same. Start by squaring/flattening all four sides of the blank. Then mark a line all the way around at 2 3/4" from one end. This will be the top shoulder of your handle where it meets the bottom of the head.
Now trace the shape you want for your handle on all four sides. On the bottom end of the handle draw an oval to show your final width. After all your lines are laid out, little by little start removing material making sure to stop periodically to check the feel and size of the handle. Trust your hands! If it feels comfortable go with it. Remember, your lines are only there as a guide, but the final shape will be dictated by how it feel in your hands.
When you reach a desirable shape, you have the option of leaving the rough tool marks on it, or sanding it smooth. This time around i decided to go for the clean smooth look. I started sanding with 80 grit, and worked my way up to 220 grit,
Step 4: Clean Up the Head and Fit the Handle
Once the head dries, you can square up the sides and the ends and clean off any glue. Then draw a line 1/2" from the edge on each face running down the length of the head. Connect those lines on the ends of the block. With a hand saw or table saw, cut the corners off and plane/sand them flat. this should leave you with an eight sided mallet head.
Now, measure the size of the smaller opening at the base of the mallet head. Add about 1/8" to that size and transfer those dimensions to the top of your handle. This will be the tenon that fits into the mallet. Carefully transfer the line from the top of the handle to the sides and cut them down to your shoulder line roughly 2 3/4" down.
After your tenon is cut, take your time and carefully pare it down until it fits snugly into the mallet. If done right, there should be no visible gaps at the base of the mallet and about 1/8" on either side of the tenon on the top opening of the mallet.
Step 5: Slice It Up and Wedge It Tight!
After your tenon has been fitted, divide the wider end of the tenon into thirds and mark two lines down the sides. About 1/4"-1/2" from the shoulder of the tenon drill a 1/8" hole through it on each line. This is to prevent the wood from splitting when you wedge it. Then, cut on those lines until you reach the holes.
Using some of the leftover wood from the head, cut some wedges about 2 1/2"-3" long at 2 degrees. This is roughly, 1/8" wide at the top over 3" long. Test the wedges to make sure they'll go in about 3/4" before they get really tight. Once you're satisfied with the fit, take it all apart, glue all four sides of the tenon and slide it into the mallet head. Then glue both sides of the wedges, get them started by hand, and then EVENLY hammer them in until the top opening in the mallet head is completely filled.
You can usually tell when the wedges bottom out when sound of hitting them in changes from a dull thud to a slightly higher pitched "ping".
Step 6: Finishing Touches
Almost done! While the glue is drying on the wedges, trace out the ends of the mallet head on some leather and cut out the pieces. Hold these on with tape, rub some glue on the ends, lay the leather down and using some wood blocks clamp it down.
By now the glue on the wedges should be tacking up and you can take the opportunity to cut the wedges and tenon flush.
After everything has dried, you can give the mallet a final sanding to knock down any sharp edges or tool marks, give a good coat of boiled linseed oil and voila! Your manly mallet is complete!!!
Now go and abolish unmanliness wherever it may abound!!...or just hang it on your tool wall and admire your handiwork.
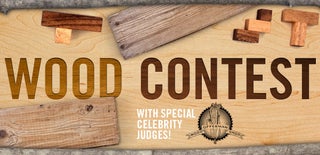
Participated in the
Wood Contest